Vacuum Freeze-drying Archaeological Artifacts – Canadian Conservation Institute (CCI) Notes 4/2
(PDF Version, 158 KB)
CCI Note 4/2 is part of CCI Notes Series 4 (Archaeological and Field Conservation)
Caution:
This Note discusses actions that will physically affect the object, and/or procedures that involve the use of chemicals. Exercise caution, and seek qualified assistance if in doubt.
Introduction
Freeze-drying is a useful technique for drying organic archaeological artifacts, recovering water-damaged archival and library materials, and preparing museum specimens of plants and animals. This Note will introduce the freeze-drying process, discuss the major components of freeze-dryers, and describe ways to monitor the progress of drying.
The Freeze-drying Process
Freeze-drying removes moisture from frozen material by sublimation (i.e. the ice in the material is converted directly to vapour; it does not melt to water and then evaporate). This process is generally carried out in a freeze-dryer, and the rate of drying is governed by both temperature and pressure. For this reason freeze-dryers usually allow for temperature, pressure, or both to be controlled.
Freeze-drying is valuable as a conservation procedure because it does not result in as much shrinkage, distortion, and collapse as can occur when wet objects are air-dried. Lowering the temperature of the material to well below 0 °C throughout the process reduces the risk of drying damage even more. However, as the temperature falls the vapour pressure of ice decreases (Table 1), which reduces the tendency for ice to sublime and therefore slows the freeze-drying process.
CRCTemperature (°C) | Vapour pressure (Pa) |
---|---|
0 |
611,15 |
−5 |
401,76 |
−10 |
259,90 |
−15 |
165,30 |
−20 |
103,26 |
−25 |
63,29 |
−30 |
38,01 |
Vacuum freeze-drying circumvents this problem by using a vacuum pump to remove the air and water vapour from the system, thereby reducing the air pressure in the chamber. As the chamber pressure approaches the vapour pressure of the ice, sublimation increases and drying begins. The rate of drying is directly dependent on the extent to which the pressure in the system is below the vapour pressure of the ice, and will speed up as the chamber pressure continues to fall. However, if the chamber pressure becomes too low there will be no heat transferred to the object by convection, the temperature of the object will fall, and drying will cease.
As the freeze-drying process continues, the water vapour that sublimes from the object forms ice on the cold surfaces of the condenser. This trapped ice must be removed periodically during the freeze-drying run by defrosting the condenser.
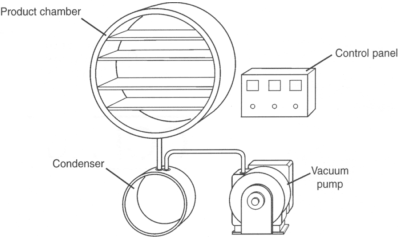
Major Components
Freeze-dryers that are suitable for conservation purposes can be purchased commercially. Commercial freeze-dryers range in size from small bench-top units to large installations with chambers that can hold several cubic metres of material. A typical vacuum freeze-dryer has four principal components: a vacuum pump, a refrigerated product chamber, a condenser, and a control system. The size and capacity of each affects the others, e.g. the size of the product chamber determines the capacity of the vacuum pump (which must be able to evacuate the chamber in a reasonable amount of time — usually less than an hour), and the size of the chamber and the temperature required both influence the size of the refrigeration compressor. The suggested requirements for each of the systems are outlined below.
The vacuum pump
Vacuum pumps remove air and water vapour from the product chamber. Their most important feature is therefore the degree of vacuum they can create. This is especially important at colder temperatures where the vapour pressure of ice decreases. Also important is the pumping capacity (the number of litres of air and water vapour that the pump can move per minute), which controls how fast the system can be evacuated.
Modern direct-drive rotary-vane vacuum pumps are preferable to older-style piston pumps because the modern pumps are more tolerant of water. This reduces the need to exhaust the moisture that collects in the oil of the pump, and is a major advantage when large quantities of water must be extracted from frozen material. (Exhausting this moisture requires opening a gas ballast valve on the top of the pump, which increases the operating temperature of the pump and therefore slows down the drying process.)
The refrigerated product chamber
Refrigerated product chambers contain the material being dried, and their size determines the size of the object that can be treated. Small chambers are less expensive than large chambers, both to purchase and maintain. If oversized material must be dried, small chambers can be extended in length with a well insulated addition.
Chambers are cooled by mechanical refrigeration systems. It is important to know what type of refrigerant the system uses, especially when purchasing used equipment. Many traditional refrigerants have been banned and are no longer in production.
The best product chambers are made of stainless steel, which is rust-free, simple to clean, and easy to disinfect after drying mouldy material. Some less expensive freeze-dryers use coated or painted steel, but these are likely to rust as they get older.
Some freeze-dryers have heated shelves in the refrigerated product chambers. These are often used in the food industry but are not generally recommended for use with cultural material.
The condenser
Condensers trap the water vapour that sublimes from frozen objects as they dry. Two types are available: a chamber cooled with a mechanical refrigeration system, or one cooled with methanol/Dry Ice or liquid nitrogen. Although the latter approach reduces equipment costs, it requires daily monitoring and maintenance which results in higher operational costs. Condensers that cool with a mechanical refrigeration system are therefore the better choice.
Condensers should be made of stainless steel, and constructed to provide maximum surface area for ice formation. They may be designed with a matrix of tubing for the refrigerant inside the drum or with insulated tubing carrying the refrigerant attached to the outside of the drum. However, because it is easier to remove the ice plug if the tubing is outside the drum, this is the preferred design.
The control systems
Vacuum pumps and refrigeration systems for both the product chamber and the condenser have individual controllers and display. Vacuum pumps have an on/off switch and a gauge to indicate the pressure in the product chamber. Some systems also have a device to control the pressure or a method to switch between several different pressure sensors.
Refrigeration systems for condensers have an on/off switch and a gauge to display the temperature. In most freeze-dryers these systems cannot be controlled; they always attain the coldest temperature possible. Some units have a defrost feature to speed the removal of ice from the chamber.
Refrigeration units for product chambers have an on/off switch and a temperature display. In nearly all cases these systems allow adjustment of the temperature. This is important because different applications have different temperature requirements, e.g. archaeological artifacts that have been soaked in a polyethylene glycol solution must be dried at a colder temperature than water-damaged archival records or books.
Other possible control or measurement systems include alarms, temperature sensors, or weighing devices. It is also possible to have all of the control systems combined into a single computer system.
Monitoring the Progress of Drying
The progress of drying can be monitored by (starting with the most common method):
- weighing the object
- determining the temperature of the object
- measuring changes in pressure in the product chamber
Each method has advantages and disadvantages. The last two allow monitoring without losing the vacuum in the chamber and slowing down the drying process, but the first is easier to do and does not require the insertion of a probe into the object.
Weighing the object
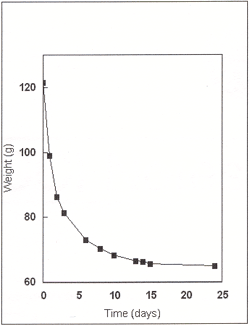
Determining the temperature of the object
The internal temperature of a wet object being freeze-dried is lower than the surface temperature. This difference decreases toward zero as the object dries. The progress of drying can therefore be tracked by measuring the surface and internal temperatures of the object. This technique is most often employed when using a freeze-dryer with heated shelves. It is rarely used with cultural material because of potential damage to the object from overheating and from inserting the temperature probe. However, it is sometimes applied to large pieces such as ships' timbers.
Measuring the changes in pressure
The moisture that sublimes from objects being dried changes the pressure in the product chamber. Pressure changes can therefore be used to indicate the state of dryness. This technique requires a valve to isolate the product chamber from the vacuum pump, and an accurate device to measure the pressure (because changes are often very small as complete drying is approached). The leak rate of the empty system must first be determined by closing the valve and recording the rate of repressurization in the product chamber while it is isolated. This process is then repeated at intervals throughout the drying run. As moisture sublimes from the object being dried, the pressure sensor registers the increasing water vapour and the rate of repressurization of the chamber. Until drying is completed, the rate of repressurization of the chamber containing the product will be greater than the rate of the empty chamber. When the rates of repressurization are equal, the material is considered to be dry.
Conclusion
The vacuum freeze-dryer is a very useful piece of equipment for preserving cultural material, either during recovery from a disaster or as part of a normal conservation process. For those who do not have their own equipment, the Canadian Conservation Institute can provide freeze-drying services.
Bibliography
Lide, D.R., ed. CRC Handbook of Chemistry and Physics, 79th edition. Boca Raton, Boston, London, New York, Washington, DC: CRC Press, –, p. 6-7.
by Clifford Cook
Originally published
Revised
Copies are also available in French.
Texte également publié en version française.
©Minister of Public Works and Government Services, Canada,
Cat. Nº NM 95-57/4-2-2007E
ISSN 0714-6221
Page details
- Date modified: