Silica Gel: Passive Control of Relative Humidity – Technical Bulletin 33
Jean Tétreault and Paul Bégin
CCI Technical Bulletins
Technical Bulletins are published at intervals by the Canadian Conservation Institute (CCI) in Ottawa as a means of disseminating information on current techniques and principles of conservation of use to curators and conservators of Canada's cultural objects as well as collection care professionals worldwide. The authors welcome comments.
Abstract
The purpose of this Technical Bulletin is to explain the need to control the relative humidity (RH) in a museum environment. Fluctuating RH can damage organic materials, while other objects, such as those made of metal, require a low RH set point to ensure optimal preservation. Controlling RH can be done in a passive way by using a moisture sorbent, the most common type being silica gel, in an enclosure, such as a display case. This bulletin provides an equation, based on assessments of the buffering capacity of common commercial products, to help determine the quantity of sorbent required. It also includes examples of how the equation can be used in various scenarios and proposes methods for conditioning moisture sorbents.
Authors
Jean Tétreault studied at the University of Montréal where he received a Master's degree in Analytical Chemistry in 1989. That same year he joined CCI, where he currently works as a conservation scientist in the Preservation Services Division. His main research interests focus on pollutants, products used for display and storage, paper degradation and passive environmental controls in collections. Results of his research have been published in various peer-reviewed journals. He has given more than 100 seminars in Canada and Western Europe on preventive conservation issues such as lighting, environmental guidelines, and exhibit and storage materials. Jean is the author of the book Airborne Pollutants in Museums, Galleries, and Archives: Risk Assessment, Control Strategies, and Preservation Management, published by CCI in 2003. Since 1998, he has also been a board member of the Indoor Air Pollution Working Group, which holds conferences every two years.
Paul Bégin graduated from Laurentian University in 1986 with a B.Sc. in Chemistry and then joined E.B. Eddy Forest Products Ltd. to work in research and development. In 1988, he moved to the National Archives of Canada, where his work as a paper conservation chemist focused mainly on paper stability, including studies on deacidification, accelerated aging and paper permanence. In 1993, his position was transferred to CCI. Paul was involved in a joint study with the Pulp and Paper Research Institute of Canada that examined the effect of lignin on paper permanence, which resulted in the development of a Canadian permanent paper standard. He was also involved in another cooperative research project organized by the American Society for Testing and Materials' Institute for Standards Research (ASTM/ISR) that resulted in the development of accelerated aging test methods for paper. He currently works in the Conservation Science Division of CCI, where he continues to study paper stability and conservation issues.
Disclaimer: The information provided here is based on the current understanding of the issues presented. The guidelines given in this Technical Bulletin will not necessarily provide complete protection in all situations or protection against every possible adverse effect caused by incorrect RH and incorrect temperature in museum contexts.
Table of contents
- List of abbreviations and symbols
- Introduction
- What is relative humidity?
- Why control the relative humidity?
- How can incorrect relative humidity be controlled?
- Passive use of sorbents in enclosures
- Scenarios
- How to condition sorbent
- Measurements
- Suppliers
- Appendix 1. Determination of the specific moisture reservoir
- Appendix 2. Equilibrium moisture content
- Bibliography
List of abbreviations and symbols
Abbreviations
- AIC
- American Institute for Conservation of Historic and Artistic Works
- CCI
- Canadian Conservation Institute
- EMC
- equilibrium moisture content
- HS
- humid sorbent
- HVAC
- heating, ventilation and air conditioning
- ICOM-CC
- International Council of Museums – Committee for Conservation
- RH
- relative humidity
Symbols
- °C
- degree Celsius
- AH
- absolute humidity
- cm
- centimetre
- g
- gram
- H2O
- water
- kg
- kilogram
- m
- metre
- M
- specific moisture reservoir
- MH
- specific moisture reservoir with hysteresis adjusted
- mL
- millilitre
- N
- leakage rate
- T
- temperature
Introduction
This Bulletin concerns the use of moisture sorbents, which include silica gels and desiccants, to maintain a stable level of RH or to maintain a specific RH level inside enclosures such as display cases, storage cabinets and containers as well as transportation cases. The specific levels of RH required are generally defined by the organization which owns the heritage object. Different types of moisture sorbents exist on the market, but few are targeted for the heritage preservation field. This Bulletin summarizes an impartial evaluation of the moisture buffering performance of commercially available sorbents. By consulting the performance results, heritage preservation professionals can determine the quantity of sorbents needed to maintain the correct RH for their objects, depending on the enclosure design and environmental conditions present. Different methods for conditioning the moisture sorbents prior to their use in an enclosure are also provided. The more technical aspects of this document, such as the equations and data tables, are included to ensure the correct use of sorbents for optimal RH control.
What is relative humidity?
Relative humidity is a common measure of the humidity in a specified environment (outside, in a room or in a display case). Technically, RH is the ratio of the amount of water vapour in the air to the maximum amount of water which the air can hold at a given temperature, expressed as a percentage. RH can also be defined as the ratio of the actual water vapour pressure to the saturation vapour pressure.
Why control the relative humidity?
The humidity in the ambient environment has an influence on the preservation of many types of objects. If the humidity is too high, the rate of degradation of papers and photographic dyes due to hydrolysis increases, the risk of corrosion of metals is higher and mould growth may occur. On the other hand, if the humidity is too low, metallic objects will be well preserved but many organic objects such as paintings, wooden furniture and leather-covered books can lose some flexibility and can crack due to stress-caused dimensional changes.
In addition to the risks caused by extremely humid or dry environments, there are problems related to large fluctuations in RH. The moisture of organic objects tends to be in equilibrium with the humidity in the surrounding environment. During RH fluctuations, the moisture in organic objects adjusts to the humidity changes in the air by absorbing or desorbing water vapour. These cycles cause small dimensional changes in the objects which can result in crack formation or propagation.
RH fluctuations also affect objects impregnated with salt, such as some archaeological metals and ceramics. Each type of salt has a critical RH level where it changes state between a solid and a liquid. Above the critical RH, one type of salt is liquid and mobile and can react with other substances. Below the critical RH, the same salt returns to its solid form where it has a larger volume than when in its liquid state, and this can cause localized stresses in the object.
For all these reasons, it is important to avoid dry, damp and extreme RH fluctuations in the surrounding environment of vulnerable objects. More general information on incorrect RH can be found on the CCI webpage Agent of deterioration: incorrect relative humidity.
How can incorrect relative humidity be controlled?
When there is a need to adjust the RH to a specific level (set point) in a room, active systems such as commercial humidifiers and dehumidifiers are commonly used in small institutions. RH control inside newer and larger buildings tends to rely on the central heating, ventilation and air conditioning (HVAC) system. Exhibiting or storing objects in humidity-controlled enclosures is worth considering if controlling RH in the room is not sustainable, or if the RH requirement for certain objects is different from what is required for the rest of the collection in the room.
At the enclosure level, RH can be controlled either by an active or passive system. An active system is where the RH of one or many enclosures is mechanically controlled remotely and delivered with a series of pipes. Some mechanical RH control modules are small enough to fit inside the enclosure. The passive way to control RH in enclosures is to use a moisture sorbent without any system to force air movement.
Passive use of sorbents in enclosures
Typically, silica gel beads, designed as buffering materials, are employed as the moisture sorbent in passive systems. This type of sorbent is sometimes referred to as "type A" or "regular density gel." Bentonite clay (also called montmorillonite clay) and zeolite have also been used as desiccants. Many porous materials such as wood and textiles can act as moisture buffers. In fact, many organic materials in a collection can play that role. That is why the moisture sorbent in the enclosure must be more efficient at buffering water vapour than the object itself and why the sorbent should be well spread out to provide a greater buffering surface.
In the past, moisture sorbents often did not fulfill the expectations of users for a variety of reasons. First, recommendations were rather rigid, offering a fixed amount of sorbent per volume, independent of the other parameters that could influence RH control. Second, either the high amount of sorbent recommended by some professionals in the field discouraged their use or the low amount recommended by some distributors resulted in insufficient performance. Third, the design of a display case and its airtightness were two important parameters that were underestimated when determining the amount of moisture sorbent needed.
The subsequent sections introduce concepts and methods required for estimating the quantity of sorbent needed in specific contexts, followed by scenarios that show typical uses of sorbents in passive modes.
Absolute humidity
RH can be defined in another way by considering the absolute humidity (AH). AH is the weight of water vapour in a given volume of air, expressed in grams per cubic metre (g/m3). The quantity of water in the air is not always at maximum level (saturation). It can vary from dry to saturation. The measurement of AH cannot, by itself, determine if the air in an enclosure is close to saturation. The measurement of temperature is also needed since the maximum amount of water vapour in the air depends on the temperature. The warmer the air, the more water vapour an enclosure can hold without condensation. The atmospheric pressure also influences saturation, but for simplification it is considered as constant. Therefore, the RH can be defined as the ratio, expressed as a percentage, of AH measured to AH at saturation at the current temperature. For example, in an enclosure at 21°C, the maximum amount of water vapour that can be held in a cubic metre is 18.3 g. This is the saturation point; any excess water vapour will simply condense. In this case, the RH is 100%. If, at the same temperature, the amount of water vapour is reduced to 9.15 g, the RH will be reduced to 50% (100 x 9.15 / 18.3 = 50%).
Equilibrium moisture content
An important concept used to understand the performance of a sorbent is the equilibrium moisture content (EMC). When equilibrium is reached, the same amount of water is adsorbed as desorbed. In this Bulletin, the EMC is defined as the weight of water in a material expressed as a percentage of its dry weight (100 x g H2O per g dry sorbent weight). As with any hygroscopic material, the moisture in the sorbent is greatly influenced by the temperature and the RH in the surroundings. There is a specific relationship between the EMC of each type of sorbent and the RH in the air at a given temperature. This relationship is called the EMC/RH isotherm. At a fixed temperature, as the RH increases, the EMC will also increase as shown in Figure 1. If the temperature changes, the EMC/RH isotherm relationship will also change.
Minimizing the RH fluctuation by using a sorbent, also known as buffering, is the desired outcome. In practice, as water vapour infiltrates or exfiltrates from an enclosure, the sorbent will minimize the change in RH by absorbing or desorbing the water. Consequently, in the presence of an adequate amount of efficient sorbent, little variation in the RH will be observed in the enclosure.
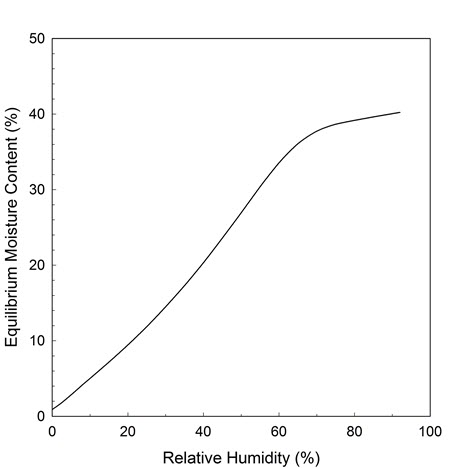
© Government of Canada, Canadian Conservation Institute. CCI 128941-0008
Figure 1. EMC/RH isotherm curve of a sorbent sample at 20°C.
Specific moisture reservoir
Sorbents can be compared by looking at their respective specific moisture reservoir values. This value is defined as "M," and it is the amount of water (in grams) that is gained or lost by 1 kg of dry sorbent for each 1% change in RH. The value of M varies depending on the RH range studied and on whether the sorbent is adsorbing or desorbing. In some cases, the difference in the adsorption and desorption curves is quite significant. Sorbents tend to buffer the increase of RH better than its decrease. This is referred to as hysteresis. A hysteresis-corrected M value, referred to here as MH (Weintraub 2002), can be derived using the EMC on the adsorption curve at the high end of the RH range and the EMC on the desorption curve at the low end of the RH range, as shown in Figure 2. MH should be used when there is a need for reducing the up and down fluctuations of RH around a set point. If the interest focuses on only one direction, such as keeping the RH low (dry) or keeping the RH in the enclosure higher than in the room, the consideration of hysteresis is not relevant.
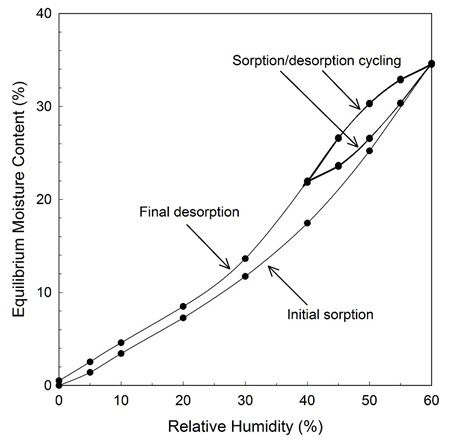
© Government of Canada, Canadian Conservation Institute. CCI 128941-0002
Figure 2. EMC/RH isotherm curves of a sorbent sample with four sorption–desorption cycles between 40% and 60% RH at 20°C.
Three typical RH ranges found in conservation are:
- RH stabilized around 50%
- RH kept low (dry)
- RH kept higher (more humid) than the average ambient condition
Table 1 shows M and MH values for moisture sorbents commonly used for these three scenarios. It illustrates that some sorbents perform better than others depending on the desired conditions. The final selection of a sorbent will depend on the M in the RH range of interest as well as on the price of the sorbents, shipping costs and the space available for the sorbent in the enclosure.
The M and MH values in Table 1 were obtained from testing done at 20°C, but those values remain almost unchanged over the 15–25°C range. With an increase of 5°C, the M and MH values only decrease by about 3%, which is less than or equal to the precision of the method used to determine them. Rapid changes of more than 5°C in the enclosure may cause too large a disruption in the EMC. This may happen when the enclosure is close to a source of heat or cold or if direct sunlight illuminates the inside. The RH level in the enclosure may then fluctuate in an undesired range.
The advantage of this comparison table is that the same protocol (described in Appendix 1) is used to compare the moisture sorbents' performance for all three scenarios listed above.
Moisture sorbent | MH 50 ± 10% RH around 50% |
M 20 → 30% Keep RH low |
M 60 → 50% Keep RH high |
---|---|---|---|
RHapid Gel | 6.11 ± 2.16 | 4.48 ± 0.42 | 4.38 ± 1.40 |
PROSorb | 5.42 ± 1.32 | 4.37 ± 0.10 | 4.25 ± 0.38 |
Art-Sorb | 4.04 ± 0.80 | 2.84 ± 0.47 | 4.18 ± 0.49 |
Regular silica gel (clear, type A) | 1.93 ± 0.44 | 5.48 ± 0.40 | 1.47 ± 0.16 |
Orange silica gel | 1.16 ± 0.26 | 4.92 ± 0.59 | 0.94 ± 0.14 |
Bentonite clay (Desi Pak) | 1.19 ± 0.07 | 2.25 ± 0.03 | 1.11 ± 0.02 |
Molecular sieves 4A (zeolite) | 0.33 ± 0.02 | 0.47 ± 0.04 | 0.31 ± 0.01 |
* Moisture sorbents evaluated for this Bulletin were obtained during the period 2013–2015. New batches of these sorbents are not guaranteed to have the same performance. See Appendix 1 for methodologies.
Amount of sorbent needed
The actual amount of sorbent required to control the RH in an enclosure depends on more than just the specific moisture reservoir of the gel. Many variables are involved, as shown in Equation 1 (Tétreault 2003). As a safety factor, adding an extra amount of sorbent (such as 30%) is suggested.
CCI created a moisture sorbent calculator as an Excel workbook. Users may enter data into the workbook, and the results will be calculated automatically as per equation 1 below.
Equation 1:
Where
Q = recommended quantity of dry sorbents (kg)a
Ceq = concentration of water vapour at equilibrium (g/m3)b
D = decimal difference between the RH outside the enclosure and the targeted RH inside (no unit)c
V = net volume of air in the enclosure (m3)
N = air exchange rate (1/day)d
t = minimum number of days the targeted RH range must be maintained (days)e
MH = specific moisture reservoir of sorbent, including the effect of hysteresis (g/kg for a 1% RH change)
F = targeted range of RH fluctuation (%)f
Notes:
- For sorbents available in sheet format, the density of the sorbent (g/m2) in the sheet must be known to determine how many sheets are required. Since Q is the quantity of dry sorbents required, it will need to be conditioned to the targeted RH (consult How to condition sorbent).
The equilibrium concentration of water vapour (AH at saturation; 100% RH) will vary depending on the temperature (T in °C), e.g. 17.3 g/m3 at 20°C; 18.3 g/m3 at 21°C; 20.0 g/m3 at 22.5°C. Concentrations at other temperatures can be obtained with this equation:
Equation 2:
Ceq = 7.36 e(T/19.96) - 2.75
- For example, if the average minimum (and/or maximum) RH in the air surrounding the enclosure is 30% and the targeted inside RH is 50%, the difference is 20%, thus D = 0.20 (Figure 3).
- The leakage rate, ideally, based on water vapour. If a precise measure of the airtightness of the enclosure is not available, a value of one air exchange per day is commonly used to represent a typical, moderately sealed display case.
- The time period from mild (such as the annual average RH) to extreme conditions and back to mild. For example, the time is about 183 days to go from mild conditions where the RH could be close to the annual average value (or close to the set point of 50% RH) to dry winter conditions and back to mild conditions again (Figure 3).
- For example, if the maximum allowable RH fluctuation is ± 5%, then F = 10% (Figure 3).
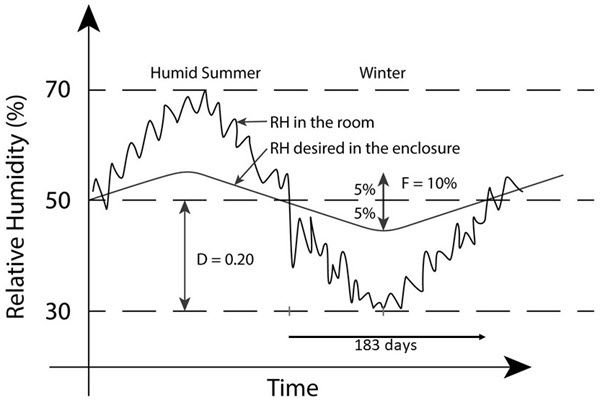
© Government of Canada, Canadian Conservation Institute. CCI 128941-0006
Figure 3. Schematic of a hygrograph showing some parameters from Equation 1.
Leakage rate
Having an enclosure with a low water vapour leakage rate is the best way to minimize the effect of the external climate and to reduce the amount of sorbent needed. However, the leakage rate (N) is a parameter that is hard to determine. As a reference, it is often mentioned that a typical display case has an air exchange rate of one per day (Padfield 1966). The rate of one per day can be achieved for display cases when there are no gaps visible between the glazes and the structure joints are sealed with glues or sealants. Some refer to the "paper or credit card insert test," where an air exchange rate of one or below is achieved when it is not possible to insert a sheet of paper or a credit card in any spacing (tiny gap) between components of the case.
In terms of permeability of water vapour, glass is a better glaze since acrylic (Plexiglas) is slightly permeable. A well-designed glass and metal display case can easily reach an air exchange rate as low as 0.3 per day. For a display case, it is important to consider that the air exchange between the area where the object is located and the area where the sorbent is located must be higher than the air exchange between the interior and exterior of the enclosure. For example, the display case should be as airtight as possible; gaps inside the display case should be discrete but big enough to allow sufficient air movement between the top of the case where the object is displayed and the bottom part of the case where the sorbent is installed, as shown in Figure 4. For large display cases, especially tall cases, it is sometimes better to use forced ventilation to ensure well-mixed air in the enclosure.
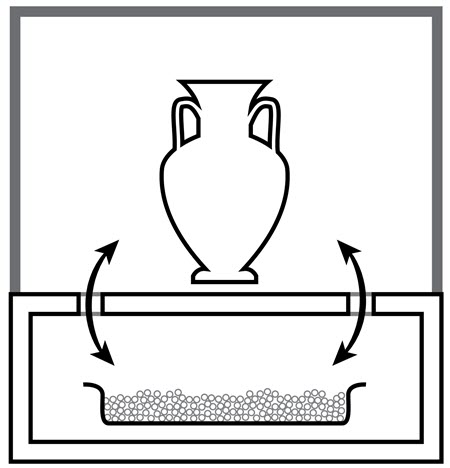
© Government of Canada, Canadian Conservation Institute. CCI 128941-0003
Figure 4. Cross-section of a display case showing the sorbent in the lower part of the case and an object in the top part. The gap between the two parts should allow sufficient air movement for optimal control of the RH by the sorbent.
Techniques exist for detecting leakage or for measuring the leakage rate (Calver et al. 2005). Leakage rate values determined with a tracer gas, such as CO2 and N2O, will need to be converted to an equivalent leakage rate for water vapour (Brimblecombe and Ramer 1983). Water vapour permeability data of glazes and some advice on the design of display cases can be found in Airborne Pollutants in Museums, Galleries, and Archives: Risk Assessment, Control Strategies, and Preservation Management.
Monitoring
When there are unknowns in the different parameters involved in the estimation of the amount of sorbent needed, RH monitoring with reliable instrumentation is highly recommended. Non-calibrated and unstable instruments can cause major errors in the measurement and control of RH. It is quite common to observe a shift of 5% in the RH value with a hygrometer. The most reliable and affordable instrument to measure the RH is a psychrometer, which comprises both a wet and dry thermometer. The psychrometer can be used to measure the RH and to validate the measurement of any hygrometer.
Scenarios
Some scenarios have been selected to show how to use Equation 1. Parameters used are set at the following initial conditions:
Ceq = 17.3 g/m3 of water vapour at equilibrium at 20°C; the annual average RH is 50%
D = 0.20 for difference between the RH outside and the targeted RH inside the enclosure (high 70% or low 30% compared to 50% RH: 0.70 - 0.50 = 0.20)
V = 1 m3 net volume of air in the enclosure
N = 1 air exchange rate (1/day)
MH = 3 g/kg for a 1% RH change
F = 20% for the targeted range of RH fluctuation of ± 10%
Keeping the relative humidity fluctuations minimal
Keeping small RH fluctuations in an enclosure for the full year is probably the most sustainable use of a sorbent for organic objects simply because there is no need for maintenance. However, monitoring of the RH in the enclosure is important to ensure that the target range of fluctuation is maintained, particularly during extreme climate conditions such as humid periods in the summer or dry periods during the winter. These climates can affect the conditions in the room, which consequently can affect the RH in the controlled enclosures.
The cycle of a mild-dry and mild-humid season spans approximately 183 days (six months). This period should be enough to provide a good RH control year-round. With the initial conditions defined above, an enclosure having a leakage rate of one air exchange rate per day in a room having an RH fluctuation of ±20% will need 10.6 kg/m3 of dry sorbent if a maximum internal RH fluctuation of ±10% is required. This 10.6 kg of dry sorbent will need to be conditioned at 50% RH (consult sections Measurements and How to condition sorbent).
Q = (Ceq D V N t) / (MH F) = (17.3 x 0.20 x 1x 1 x 183) / (3 x 20) = 10.6 kg
If the leakage rate (N) is reduced by one half or if the MH is two times more efficient, only 5.3 kg of dry sorbent will be needed (plus conditioning adjustment).
Keeping the environment drier than the ambient level
The preservation of metal objects and objects contaminated by salt will be greatly improved if they are kept in a dry environment. Consider the example of silver trophies in a display case, which will be better protected in a dry environment. The RH in the room is relatively stable at 50%, and the trophies should be kept dry within the range of 20% to 30% RH. The initial RH in the display case is 20%. When it reaches 30%, the sorbent needs to be changed. The replacement of the sorbent should be done only once a year. In this scenario, D = 0.30 (50% - 20%), F = 20% (F represents the RH range of ± 10% allowed, even though the focus here is on + 10%) and t = 365 days.
Q = (17.3 x 0.30 x 1x 1 x 365) / (3 x 20) = 31.6 kg
A quantity of 31.6 kg of dry sorbent is a significant amount for a 1 m3 enclosure. If the airtightness could be improved by a factor of 3 (N = 1/3 day), only 10.5 kg would be needed (plus conditioning adjustment).
For the preservation of paper against acid-catalyzed hydrolysis, it is best to avoid periods of high RH. If the room maintains an RH below 50% nine months a year, and the RH tends to go up to 65% during the summer, the following scenario could be used. To limit the rise in RH in the display case to 50%, a set point could be determined at 45% with an allowed increase in RH of 5% for three months. In this scenario, D = 0.20 (65% - 45%), F = 10% (similarly to the example above, an increase of 5% is allowed) and t = 90 days.
Q = (17.3 x 0.20 x 1x 1 x 90) / (3 x 10) = 10.4 kg
In the scenario above, it is highly possible that the sorbent would not have to be replaced because if the RH in the room goes as high as 65% in the summer, it most likely will go drier than 45% during the winter. Consequently, at the beginning of the humid period, the sorbent would be equilibrated at 45% or slightly below and then it would be ready to control the RH during the coming humid period.
Keeping an environment drier in the display case than in the room is typically a manageable option for a temporary exhibition or for transportation. For example, when only inorganic objects in the same enclosure need to be kept dry temporarily, an easy solution is to use dry sorbent (0–5% RH) and replace it when the RH reaches the maximum allowed value. However, for permanent use, it can be too time-consuming to recondition the sorbent and there is a risk of incorrect RH if there is a lack of monitoring.
Keeping the environment more humid than the ambient level
In this scenario, the average annual RH of the room is at 40% and an RH of 50% ± 5% is required for a very fragile organic object for a maximum of 90 days. Here, D = 0.10 (50% - 40%), F = 10% (F represents the RH range of ± 5% allowed, even though the focus here is on - 5%) and t = 90 days.
Q = (17.3 x 0.10 x 1x 1 x 90) / (3 x 10) = 5.2 kg
Before the beginning of the dry period, the sorbent should be equilibrated somewhere in the range of 50–55% RH. Regular monitoring is recommended.
How to condition sorbent
Conditioning the sorbent means adjusting its moisture content to a desired RH level. This will allow the optimization of its buffering capacity. Remember that the quantity (Q) provided by using Equation 1 is based on dry sorbent and an adjustment needs to be made to determine the amount of conditioned sorbent (consult the section on Measurements). If the sorbent received or available in your facility is not conditioned to the desired level, some work will be required. There are different methods for adjusting the EMC of a sorbent to a desired level (Lafontaine 1984; U.S. National Park Service 1999 and Weintraub 2002). Drying and humidifying the sorbent and measuring the RH generated by the sorbent are the three key aspects of conditioning sorbent to a specific RH. Ordering pre-conditioned sorbent is a good option if the objective is only to minimize short-term RH fluctuations without the need for periodic regeneration.
Drying the sorbent
Drying the sorbent at 115°C overnight is often recommended if the sorbent contains some RH indicator colourants (blue or orange). Art-Sorb cannot be heated in an oven above 65°C, otherwise some of the beads break into small fragments. The other sorbents can be dried at higher temperatures (up to 200°C) for shorter time periods, but small debris may be generated. Some moisture sorbents can be dried by using a microwave oven, but this must be confirmed by the manufacturer or distributor.
Humidifying the sorbent
The nature of the sorbent used will dictate how it should be humidified. Many warnings are found in the literature about never adding liquid water directly to silica gel. With the exception of Art-Sorb, all silica gels tested with drops of water crack extensively, leaving small fragments of beads. When sprayed with water mist, Art-Sorb and PROSorb are not damaged while the other sorbents are affected but to a lesser extent. A slow absorption of water vapour is the safest method.
Increasing the moisture content of the sorbent with water vapour can be done with a commercial RH-controlled chamber or with a small chamber containing an open container of saltwater solution that generates a specific RH at equilibrium as shown in Figure 5. For example, a saturated aqueous solution of magnesium nitrate [Mg(NO3)2 ∙ 6H2O] will generate an RH of 54%. Unfortunately, the salt used to make this type of solution is expensive.
A list of salts with the respective RHs they generate can be found in Greenspan (1977). Avoid magnesium dichloride hexahydrate (MgCl2 ∙ 6H2O [34% RH]) since it can release chlorine. Sodium chloride (NaCl) will generate an RH of 75% and will not release chlorine. Unfortunately, it is not always possible to get exactly the RH wanted with salt solutions. For example, you can get 54% but not 50% RH.
To prepare the saltwater solution in a pan, simply add water to the salt and stir often. Also, make sure the salt remains wet by leaving a few millimetres of water above the salt surface.
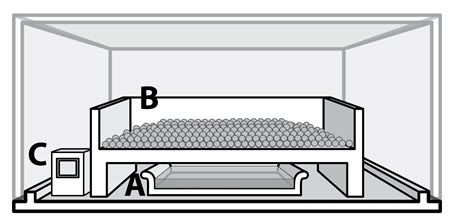
© Government of Canada, Canadian Conservation Institute. CCI 128941-0004
Figure 5. Example of a small conditioning chamber.
There are many ways to build a small conditioning chamber. The conditioning chamber must be airtight and transparent to read data on the hygrometer monitor unless the RH value can be read remotely. The conditioning chamber in Figure 5 has a base made of plywood, painted with an acrylic (latex) paint. On top is an acrylic glazing panel. On the base, there is a pan containing a saline solution (A). Above the pan, there is a little tray where the sorbent is evenly dispersed (B). There is enough space around the tray to allow good air movement between the saline solution and the sorbent. A hygrometer inside the chamber monitors the RH (C).
To humidify a sorbent to a high humidity level such as 75%, place water instead of a salt solution in the pan for a few days to speed up the process. Then, when the desired moisture level has been attained, remove the water and use the proper saline solution.
Measurements
The verification of the RH or the proper EMC (% g/g dry weight) is an important step to ensure that the sorbent is at the required moisture level. Verifying dry sorbents is usually not as critical, but humid sorbents should be quantified either by RH or weight measurements.
Measuring the relative humidity generated by the sorbent
A hygrometer can be used inside the conditioning chamber (mechanical or with a saltwater solution) to give an idea of the RH, but it cannot confirm if the sorbent has reached the desired moisture level. Since the RH measured reflects the RH generated by the salt solution more than the sorbent, the RH measurement must be done outside of the chamber. An easy and fast way to see if the RH level of the sorbent is equilibrated to the desired level is to place about 25 mL or 20 g of sorbent and a small reliable hygrometer in a small well-sealed container (plastic or glass) as shown in Figure 6. The sensor of the hygrometer should not touch the gel. Periodically read the RH level on the hygrometer until the RH stabilizes. RH equilibrium should be reached after two to six hours, depending on the specific moisture reservoir, the free air volume in the container and the difference between the RH in the room and the RH generated by the sorbent.
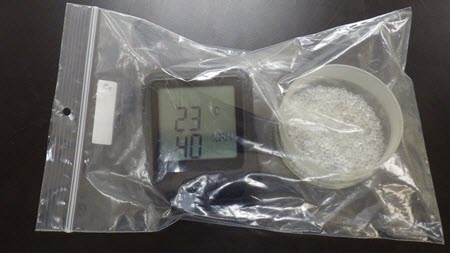
© Government of Canada, Canadian Conservation Institute. CCI 128941-0005
Figure 6. A compact hygrometer and 20 g of sorbent in a 24 cm x 16 cm zipper-type polyethylene bag. After a few hours, the monitor shows a stable RH of 40%.
Measuring the sorbent's weight
The amount of water that a sorbent needs to reach equilibrium at a specific RH is determined with the help of its respective EMC/RH isotherm. If the EMC is available from the distributor or from the literature (consult Appendix 2), look for the EMC corresponding to the RH you want and determine how much water is needed. Weigh the dry sorbent and introduce the quantity of water required using the most suitable approach (drops, spray or vapour; consult the section on Humidifying the sorbent) until the desired weight is reached.
Example: Conditioning the silica gel to equilibrium moisture content at 50% RH.
According to Appendix 2, 27.07% water (EMC % g/g dry weight) is needed in regular silica gel to be in equilibrium at 50% RH. If you start with 1000 g of dry silica gel, introduce water until the weight of the humid sorbent reaches 1270.7g (1000 x 1.2707).
Another way to determine if the desired EMC is reached is to monitor the weight change of the sorbent during conditioning in the conditioning chamber. Measure the sorbent weight every two to three days until it stops changing. The scale used should have enough sensitivity to detect a weight variation in the sorbent of 0.1% or less.
An easy method for adjusting the sorbent moisture level by adding dry or humid sorbent
Adjusting the sorbent to the desired moisture level can be time consuming. The process can be sped up if, in addition to the batch of sorbent that needs to be adjusted, a dry sorbent (close to 0% RH) and a humid sorbent of the same type (75% RH made with NaCl) are already available. A dry or humid sorbent will be added to the main batch of sorbent to equilibrate it to a specific RH based on the following equations.
If the sorbent available is equilibrated at an RH below the target level, a humid sorbent (HS) needs to be added according to Equation 3.
Equation 3:
Example: If the sorbent should be conditioned to reach an equilibrium of 50% RH, and 1000 g of sorbent equilibrated at 40% RH is available, then the humid sorbent (75% RH) needs to be added to the mix as follows:
- 1000 x (50 - 40) / (75 - 50) = 400 g of sorbent at 75% RH
- 400 g of humid sorbent at 75% RH will be mixed with 1000 g sorbent at 40% RH
- Take the quantity needed from the 1400 g mix
If the sorbent available is equilibrated at an RH higher than the target level, a dry sorbent needs to be added according to Equations 4 and 5.
Equation 4:
Equation 5:
Quantity of dry sorbent = total quantity of target sorbent - quantity of actual sorbent
Example: If 1000 g of sorbent equilibrated at 60% RH is available (actual), and the target RH is 40%.
- With Equation 4: 40 x 1000 / 60 = 667 g of sorbent at 60% RH
- With Equation 5: 1000 g - 667 g of actual sorbent (60% RH) = 333 g of dry sorbent
- Mix well the dry and humid sorbents equilibrated at 60%
For both scenarios, verify if the RH generated is close to the target RH. The new RH generated by the sorbent may not always match the target RH the first time. This is due to different factors such as the non-linear EMC relationship with RH, the use of non-fully dry sorbent and the hysteresis effect. If an adjustment is needed, use the equation that corresponds to your scenario (more humid sorbent or drier sorbent) and start with the last mixture of sorbents. Starting with the latest mixture will help to minimize the gap between RH obtained from the mixture and the target RH. When satisfied with the RH value generated by your mixture, ideally, let the mixed sorbents stabilize a few days before using them to buffer an enclosure. In practice, however, the mixture can be used immediately since the RH within the enclosure remains at the desired level while the beads are equilibrating.
Adding extra (dry or humid) sorbent into the sorbent container in the display case to reach the desired RH can be done if access to the sorbent is easy and space for extra sorbent is available. Depending on the sorbent, it is also possible to just add water to the sorbent while it is in the case. In both scenarios, the sorbent needs to be stirred.
Suppliers
Art-Sorb, bentonite clay (Desi Pak), molecular sieves 4A (zeolite), orange silica gel, PROSorb, regular silica gel and RHapid Gel are available from conservation supply companies:
Appendix 1. Determination of the specific moisture reservoir
The determination of the specific moisture reservoir is based on data obtained from the EMC (% g/g dry weight) of the sorbent at different RHs (referred to as the EMC/RH isotherm). From this isotherm curve, the change in moisture relative to changes in RH can be calculated.
Determination of the equilibrium moisture content
The determination of the percentage of EMC (100 x g H2O per g dry sorbent weight) was obtained by using a sorption analyzer which is run automatically and requires only a small quantity of sorbent. Isotherm curves of the sorbent (as shown in Figure 2) are generated from the weight gain or loss values measured at different RH levels. This was achieved using a TA Instruments TGA Q5000 SA sorption analyzer. For each sample (sorbent) tested, one to three granules (total weight around 20 mg) were placed in the instrument and were subjected to the series of steps listed in the following test protocol:
- The sample was conditioned at 20°C and 0% RH under nitrogen for 360 minutes.
- RH was increased in increments of 5% in the 0% to 10% range (the RH was increased after a weight change of less than 0.015% for 5 minutes or a maximum dwell time of 240 minutes).
- RH was increased in increments of 10% in the 10% to 60% range (the RH was increased after a weight change of less than 0.015% for 5 minutes or a maximum dwell time of 400 minutes).
- RH was decreased in increments of 5% from 60% to 40% (the RH was decreased after a weight change of less than 0.015% for 5 minutes or a maximum dwell time of 300 minutes).
- RH was increased in increments of 5% from 40% to 60% (the RH was increased after a weight change of less than 0.015% for 5 minutes or a maximum dwell time of 300 minutes).
- Steps 4 and 5 were repeated two more times, resulting in three cycles of 40% to 60% RH fluctuation.
- RH was decreased in increments of 5% from 60% to 40% (the RH was decreased after a weight change of less than 0.015% for 5 minutes or a maximum dwell time of 300 minutes).
- RH was decreased in increments of 10% from 40% to 10% (the RH was decreased after a weight change of less than 0.015% for 5 minutes or a maximum dwell time of 300 minutes).
- RH was decreased in increments of 5% from 10% to 0% (the RH was decreased after a weight change of less than 0.015% for 5 minutes or a maximum dwell time of 240 minutes).
- The sample was dried at 60°C and 0% RH under nitrogen for 360 minutes.
- The sample was equilibrated at 20°C and 0% RH under nitrogen for 240 minutes.
The length of the analysis varied from one and a half to seven days depending on the nature of the sorbent. Three to five measurements were done on each sorbent depending on the uniformity of the beads.
Calculation of M and MH
The specific moisture reservoir (M) is the amount of water (in grams) that is gained or lost by 1 kg of dry sorbent for each 1% change in RH. MH (for hysteresis adjusted) is used when sorption–desorption cycles happen due to RH fluctuations. MH can be obtained with the summation of the average value of M for sorption and desorption.
For example, Table 2 shows changes in equilibrium moisture content and the weight of a sorbent (same sorbent as in Figure 2) as the RH changes.
RH (%) | EMC (%) (100 x g H2O per g dry weight) at 20°C |
Conditioned sorbent weight (g) |
---|---|---|
0 | 0 | 0.028530 |
40 | 21.90 | 0.034778 |
50 | 26.57 | 0.036111 |
60 | 34.56 | 0.038390 |
50 | 30.29 | 0.037172 |
40 | 21.94 | 0.034790 |
The MH for the RH range 40% to 60% [MH (50% ± 10%)] with a set point at 50% is determined as follows:
M(RH1 to RH2) = gain (or loss) in water (g) per kg of dry sorbents at RH1 / [RH2 (%) - RH1 (%)]
Sorption M(RH1 to RH2) = [(weight at RH2 - weight at RH1) x (1000 g/1 kg) / Weight at 0% RH] / [RH2 - RH1]
Sorption M(50% to 60%) = [(0.038390 g - 0.036111 g) x (1000 g/1 kg) / 0.028530 g] / [60% - 50%] = 7.99 g/kg for a 1% RH change (rise)
Desorption: M(60% to 50%) = [(0.037172g - 0.038390 g) x (1000 g/1 kg) / 0.028530 g] / [50% - 60%] = 4.27 g/kg for a 1% RH change (drop)
MH (50% ± 10%) will be the average of M(40% to 50%), M (50% to 60%), M(60% to 50%) and M(50% to 40%) = 6.32 g/kg for a 1% RH change of dry sorbent.
Appendix 2. Equilibrium moisture content
The EMC for different sorbents studied are shown in Table 3. Knowing these values is critical for conditioning the sorbent for the specific RH required. The data is used in the section Measuring the sorbent's weight.
RH (%) | EMC (%) of the sorbent from dry to humid at 20°C | ||||
---|---|---|---|---|---|
RHapid Gel | PROSorb* | Art-Sorb | Regular silica gel (clear) | Orange silica gel | |
0 | 0.00 | 0.00 | 0.00 | 0.00 | 0.00 |
10 | 3.55 | 3.46 | 5.50 | 4.96 | 4.45 |
20 | 7.43 | 7.14 | 8.57 | 10.00 | 8.94 |
30 | 11.92 | 11.51 | 11.41 | 15.48 | 13.86 |
40 | 17.66 | 24.69 | 14.49 | 21.09 | 19.10 |
50 | 25.32 | 33.97 | 18.37 | 27.07 | 24.14 |
60 | 34.46 | 39.22 | 23.93 | 31.46 | 27.28 |
* Data for 40 to 60% RH has been provided by the distributor.
Bibliography
Brimblecombe, P., and B. Ramer. "Museum Display Cases and the Exchange of Water Vapour." Studies in Conservation 28,4 (1983), pp. 179–188.
Calver, A., A. Holbrook, D. Thickett and S. Weintraub. "Simple Methods to Measure Air Exchange Rates and Detect Leaks in Display and Storage Enclosures." In I. Sourbes-Verger, ed., ICOM-CC 14th Triennial Meeting, The Hague, 12–16 September 2005: Preprints. London, UK: James & James, 2005, pp. 597–609.
Greenspan, L. "Humidity Fixed Points of Binary Saturated Aqueous Solutions." (PDF format) Journal of Research of the National Bureau of Standards, A. Physics and Chemistry, vol. 81A (1977), pp. 89–96.
Lafontaine, R.H. Silica Gel. Technical Bulletin 10. Ottawa, ON: Canadian Conservation Institute, 1984.
Padfield, T. "The Control of Relative Humidity and Air Pollution in Showcases and Picture Frames." Studies in Conservation 11 (1966), pp. 8–30.
Tétreault, J. Airborne Pollutants in Museums, Galleries and Archives: Risk Assessment, Control Strategies and Preservation Management. Ottawa, ON: Canadian Conservation Institute, 2003.
U.S. National Park Service. Using Silica Gel in Microenvironments (PDF format). Conserve O Gram 1/8. Washington, D.C.: U.S. National Park Service, 1999.
Weintraub, S. "Demystifying Silica Gel." In Proceedings of the Objects Specialty Group Session, 30th AIC Annual Meeting, Miami, 10 June 2002: Objects Specialty Group Postprints, vol. 9. Washington, D.C.: American Institute for Conservation of Historic and Artistic Works, 2002, pp.169–194.
© Government of Canada, Canadian Conservation Institute, 2023
Published by:
Canadian Conservation Institute
Department of Canadian Heritage
1030 Innes Road
Ottawa ON K1B 4S7
Canada
Revised in 2023
Second edition published in 2020
First edition published in 2018
Cat. No.: CH57-3/1-33-2020E-PDF
ISSN 2562-0282
ISBN 978-0-660-35489-7
Page details
- Date modified: