Forging the future of the Canadian Coast Guard fleet
Every day, Canadian Coast Guard teams brave the tides to keep our waterways safe for mariners, protect the marine environment and respond to calls for help. Since 2015, Public Services and Procurement Canada (PSPC) has assisted the Canadian Coast Guard with a different kind of mission, to build 20 new high-endurance search and rescue lifeboats to serve Canadians across the country when they’re on the water.
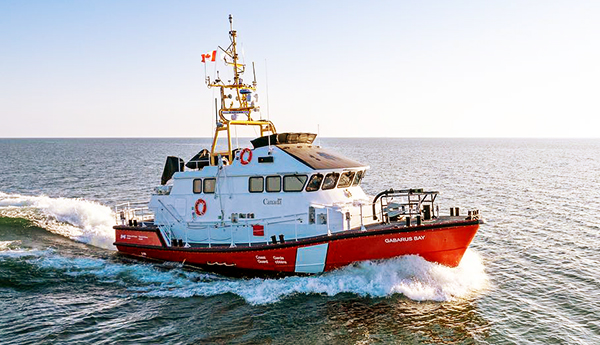
As each ship is named after a Canadian bay, they are known as the Bay Class vessels. To date, 14 ships have been completed, delivered, and are being used by the Canadian Coast Guard. Ships 15 and 16 will be completed in the fall of 2023, and work has already begun on the last 4 vessels. In addition to modernizing the Canadian Coast Guard fleet, the project has played a part in revitalizing our marine industry, which creates jobs and economic benefits.
PSPC’s marine procurement experts have been involved in the project from its earliest phases through to the delivery of each ship at its service destination. Their support has helped chart the course of this rescue craft renewal initiative.
Embarking on a design
The Canadian Coast Guard started off with the design for a British lifeboat model, which they modified for Canadian conditions and operations. PSPC awarded a contract to a Canadian naval architectural firm to finalize the revised concept. The main requirements were to convert the ship’s body from fibreglass to aluminum while updating the equipment and machinery for service on this side of the ocean.
Based on the resulting design, PSPC invited shipyards to bid on building up to 10 of these vessels each, ultimately awarding the build contracts to Chantier Naval Forillon of Gaspé, Quebec, and Hike Metal Products of Wheatley, Ontario.
The 2 shipyards were asked to review the design and propose potential improvements. For example, some elements were refined to make production more efficient while maintaining the original concept of the design and respecting the Canadian Coast Guard’s requirements, explains Amine Ali Haider, from the PSPC team. “The shipyards are experts on production, so we took advantage of their insight.”
Navigating the production
Each ship is comprised of multiple components that are then assembled into a functional whole. “The primary pieces are the hull and keel that form the bottom and the superstructure that sits over the top,” says Luc Girard, also with PSPC.

Alongside the engine and controls, other components include cables, pumps, climate control systems, medical equipment for rescue efforts and much more. “Gathering all of the items ahead of time was a key step in ensuring everything fit together and the pieces for the ship’s structure could be cut correctly the first time,” Haider notes.
On the surface, it might seem like the ships are identical, but there are some differences between them. Regional Canadian Coast Guard crews have input into the equipment selected based on their unique operational requirements. “In addition, equipment changes are driven by the industry,” says Haider. “We’ve been building the boats for several years, so parts get discontinued or upgraded.”
Any changes can lead to recalculations and an engineering review, especially in these self-righting vessels, which return to an upright position if they capsize. “So the weight on the boat must be strictly controlled,” says Girard. The self-righting system was put through a rigorous test as soon as the first ships were ready. “The shipyards used cranes to tip the boats over and see if they roll back up,” Girard recounts. “That was a nerve-wracking experience for everyone, but it was a success and, afterwards, we proceeded full speed ahead with the builds.”
For PSPC, that means monitoring timelines and work quality, discussing design updates and necessary contract amendments, and meeting with the shipyards for progress reports and technical briefings. The PSPC team is always onsite for the delivery of a ship. “The vessel goes through some final tests and there is a run-through of its operation,” says Haider. “We sign the documents that conclude the handover.”
Pride, leadership and longevity
“There is so much to be proud of in terms of this project, starting with the amazing partnerships with the Canadian Coast Guard and all the stakeholders involved, which allowed us to sail relatively smoothly through the project,” Haider points out.

The work was done in Canada, using many domestic suppliers, and has informed other initiatives under the National Shipbuilding Strategy. It has demonstrated leadership in the marine sector and attracted the interest of the US Coast Guard.
For the Canadian Coast Guard, the vessels have been a welcome addition to the fleet. “They’re very happy with their performance,” says Girard, “and they can look forward to years of service by modern vessels backed by 3D models and detailed manuals for repairs. Best of all, we’ve taken safety to the next level, not just for the mariners they assist, but for their own crews that risk their lives on the water.”
Learn more about the ships and the status of the project. Both shipyards also offer videos of the self-righting tests for the boats: Chantier Naval Forillon and Hike Metal Products. For other interesting articles about PSPC, see Our stories.
Page details
- Date modified: