Understanding galvanic corrosion
Lyndsie Selwyn
List of abbreviations
- μL
- microlitre
- M
- molarity
- ppm
- part per million
- SCE
- standard calomel electrode
- SHE
- standard hydrogen electrode
- wt%
- weight percentage
- w/v
- weight per volume
This learning resource is for heritage professionals who want to learn about galvanic corrosion. It is part of the Canadian Conservation Institute's (CCI) "Care of Metals in Collections" workshop. The resource explains galvanic corrosion and where it can be encountered in conservation. It also describes what can be done to minimize the problems galvanic corrosion might cause. Lastly, it contains a demonstration that shows galvanic corrosion in a dramatic, colourful way.
Learning objectives
By understanding galvanic corrosion, heritage professionals will be able to:
- recognize the possible harm when two metals are in direct contact
- use a galvanic series and understand what it means
- identify ways to minimize corrosion problems
Background: aspects of galvanic corrosion
Most metals corrode when wet. When two wet metals are in contact, one of them usually corrodes faster than when the metals are separated. The increase in corrosion rate is called galvanic corrosion.
The galvanic series
Metals can be arranged in a sequence to make it easy to see which metal will corrode faster when two metals are touching. The sequence is called the galvanic series. Table 1 gives the galvanic series for various metals, as determined in seawater. Although graphite is not a metal, its conductivity is high enough that it can cause galvanic corrosion, so it is also included in Table 1. The metals are ordered from the most reactive at the bottom of the table to the least reactive at the top. For any pair of metals, the metal that is lower in the series is the more active metal, and the one that is higher is the more noble metal. When two metals are in contact, the more active metal may undergo galvanic corrosion. For example, if zinc is in contact with mild steel, the zinc may undergo galvanic corrosion because it is the more active metal of the two.
Series listed from more noble at top to more active at bottom |
---|
Graphite (carbon) |
Platinum |
Gold |
Stainless steel (alloy 316) |
Silver |
Nickel |
Copper nickel (70:30 wt%) |
Lead |
Tin bronze |
Lead-tin solder (50:50 wt%) |
Tin |
Copper |
Yellow brass |
Chromium (plated on steel) |
Mild steel, cast iron |
Cadmium |
Aluminum alloys |
Zinc |
Magnesium |
For galvanic corrosion to occur, the metals involved must be connected in two ways. First, they must be in electrical contact, either through direct physical contact or through another conducting material, to allow an electric current to flow from one metal to the other. Second, they must also be in ionic contact, so an ion current can flow between them. This requires an electrolyte, namely, a solution containing ions such as from a dissolved salt, an acid or a base. For ionic contact, the metals might be completely immersed in the electrolyte or coated with a continuous film of electrolyte that wets both metals, as can happen when the humidity is high.
There can be a beneficial side to galvanic corrosion. Although the more active metal corrodes faster due to galvanic corrosion, the more noble metal corrodes more slowly than it would alone. Thus, galvanic corrosion can be used to protect one metal from corroding by sacrificing a more active metal. The more active metal in this case is called a sacrificial anode. For example, zinc, aluminum and magnesium, which all lie below iron and steel in the galvanic series, have been used as sacrificial anodes to protect steel in seawater. Sacrificial anodes were used to protect a cast and wrought iron steam engine prior to excavation from a shipwreck in seawater (MacLeod 1990). As well, sacrificial anodes of magnesium were buried in the soil around an outdoor steel sculpture to protect the buried portions (Benson 2014). The technique of protecting metal with a sacrificial anode is an example of a more general approach called cathodic protection, which can also be done with a metal electrode and a power supply (Davis 2000).
Problems caused by galvanic corrosion
Conservators should be aware of the danger of galvanic corrosion whenever two different metals are in contact. Sometimes the danger is obvious, such as when two metals are used in a sculpture for artistic reasons. Let's take, for example, an outdoor tin bronze statue, where the figure is holding an object made of mild steel. The steel can rust due to galvanic corrosion whenever rain or high humidity dissolves salts or pollutants to produce an electrolyte, because steel is more active than tin bronze in the galvanic series. Corrosion products from the steel will stain the bronze with a rusty colour. Note that steel is an alloy of iron with a small amount of carbon, generally below 1 wt% (Selwyn 2004), but it is often referred to simply as iron.
Galvanic corrosion may also involve metals used in structural supports, and these metals might be hidden from view. For example, steel armatures were traditionally used for support inside bronze sculptures. If moisture gets inside the sculpture, either directly or as condensation, an electrolyte can be produced. When the bronze and steel are connected both by direct contact and through the electrolyte, the steel will undergo galvanic corrosion. Iron corrosion products from the corroding steel may leak out onto the surface of the sculpture, thus staining it (Lins 1985). Corrosion of steel can also cause "rust jacking," where the iron corrosion products build up and crack the bronze. Eventually, if the steel loses too much strength, the entire support system can be threatened.
Galvanic corrosion is often associated with the wrong choice of bolts. If aluminum is held in place with copper alloy bolts, the copper will cause galvanic corrosion in the aluminum. This is seen in Figure 1, where the white area around the central copper alloy bolt is aluminum corrosion. The aluminum corrosion is worse next to the copper alloy, as shown schematically in Figure 2. When steel bolts are used on bronze plaques, the steel can undergo galvanic corrosion and produce rust stains on the plaques.
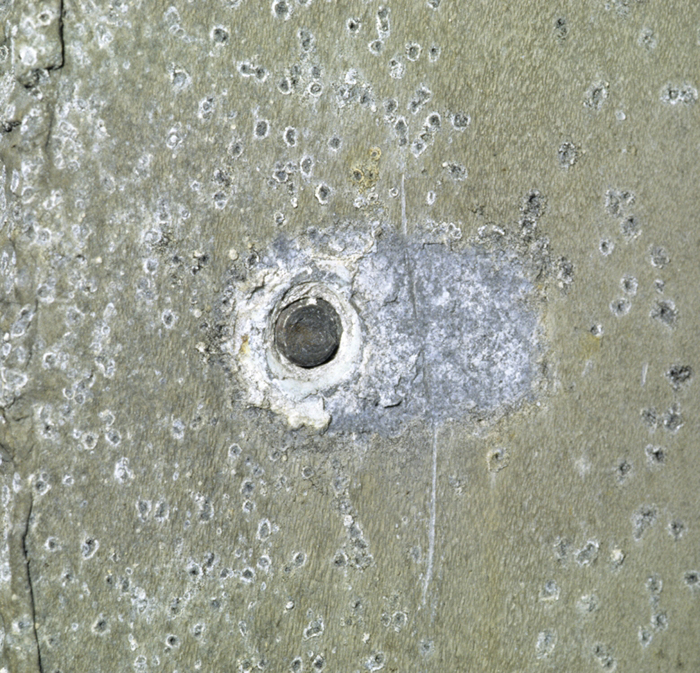
© Government of Canada, Canadian Conservation Institute. CCI 87306-0016
Figure 1. Galvanic corrosion of aluminum around a copper alloy bolt in an outdoor aluminum sculpture. The corrosion products form the white ring around the head of the dark-coloured bolt.

© Government of Canada, Canadian Conservation Institute. CCI 129916-0021
Figure 2. Schematic diagram of galvanic corrosion around a copper alloy bolt in an aluminum plate.
Carbon fibres, which are based on graphite, are becoming increasingly common to provide light, inert and strong support, whether on their own as fabric or rods, or embedded in polymers or other materials (Mallick 2008). They must, however, be used carefully with metals. Since carbon is at the top of the galvanic series in Table 1, most metals in contact with carbon can undergo galvanic corrosion. Even carbon fibres completely embedded in polymers can cause problems if the polymer degrades and the carbon comes in contact with a metal. Carbon fibres can also be embedded in metals to form metal-matrix composites, and these composites can undergo galvanic corrosion.
Plated metals where the plating metal is more active
Galvanic corrosion is often observed when one metal is plated onto another. The corrosion behaviour depends on whether the metal on top, called the plating metal, is the more active or the more noble metal. A common example where the plating metal is more active is galvanized steel, in which the steel has been coated with a layer of zinc.
The zinc coating protects the steel in two ways: as a physical barrier and through galvanic corrosion. If the zinc layer is intact, the zinc acts as a physical barrier to moisture and the steel does not corrode. Although zinc is more active than steel, it is protected by its corrosion products, typically zinc carbonate, and actually corrodes more slowly outdoors than unprotected steel. If the zinc layer is scratched or otherwise damaged so that the steel is exposed, zinc corrodes preferentially to steel and so protects the exposed steel by galvanic corrosion.
The protection through galvanic corrosion of zinc is one of the advantages of galvanized steel. On the other hand, because zinc lies below most other metals in the galvanic series, the zinc on galvanized steel may corrode rapidly if galvanized steel is used with other metals. This will leave the steel unprotected once most of the zinc is gone. An example of this is given by Maltby (2003) for galvanized steel in contact with steel.
Aluminum and cadmium also lie below steel in the galvanic series, and both have been used to protect steel. Alloys of aluminum and zinc are also used to coat steel, with trade names such as Aluzinc, Galfan, Galvalume and Zincalume. Cadmium was used to plate steel hardware on furniture in the past, but it is used less today due to its toxicity.
Plated metals where the plating metal is more noble
Plating a more noble metal onto a more active metal is often done to produce an object that has the appearance of the more noble metal. Some examples are copper-plated zinc sculptures, chrome-plated brass stair railings, silver-plated copper trays or gilded religious objects where gold is plated onto silver or copper alloys. Many different metals can be plated on steel: copper alloys, such as on brass bed frames; silver, in kitchen utensils; chromium, in automobile parts; tin, in tin-plated cans; and nickel, which is often plated onto steel before chromium is plated on top. As long as the coating is continuous, with no porosity, only the more noble metal is exposed, and it will act as a barrier to protect the underlying metal from corrosion. If the more noble metal corrodes slowly, the protection it offers can potentially last a long time.
If the plating metal has imperfections or is damaged, the exposed underlying metal can corrode. In this case, galvanic corrosion does not offer protection; instead, galvanic corrosion increases the corrosion rate of the underlying metal. Copper-plated zinc sculptures, for example, suffer from serious pitting at imperfections in the copper plating as a result of the galvanic corrosion of zinc, especially outdoors (Grissom 1994). Another example is a "tin can" which is actually made of tin-plated steel. Tin is more noble than steel, so the underlying steel will undergo galvanic corrosion if the tin is damaged.
The corrosion of the underlying metal, if concentrated in a small area, can undercut the plating layer, causing it to lift. Figure 3 shows the silver plating lifting from a silver-plated steel nutcracker, and Figure 4 shows the chrome plating lifting from a chrome-plated steel headlight rim.
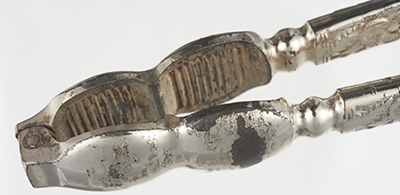
© Government of Canada, Canadian Conservation Institute. CCI 129916-0017
Figure 3. A silver-plated steel nutcracker that has suffered galvanic corrosion of the steel. The formation of iron corrosion products from the corroding steel has caused the plating to bubble and lift.
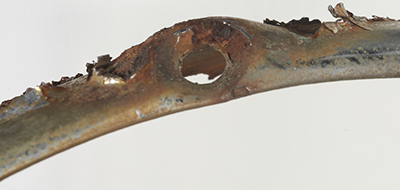
© Government of Canada, Canadian Conservation Institute. CCI 129916-0019
Figure 4. A chrome-plated steel rim for a headlight. The steel has undergone galvanic corrosion. The formation of iron corrosion products from the corroding steel has caused the plating to lift and the creation of stains on the surface of the chrome.
There are cases where plating occurs unintentionally, leading to galvanic corrosion. If the water in a fountain with an aluminum sculpture contains copper ions from copper pipes, copper will deposit onto the aluminum by electrochemical replacement plating; consult CCI Note 9/12 How to Plate Silver onto Copper Alloys Using Chemicals. The areas where copper has plated will then cause galvanic corrosion of the aluminum in unplated areas, producing pitting. The same problem arises when copper plates onto zinc; in fact, as little as 0.1 ppm of copper ions in water increases the corrosion rate of zinc (Zhang 2006).
Preventing and treating galvanic corrosion
It is important to be aware of what combinations of materials may lead to galvanic corrosion. This is particularly true when commissioning new works of art, because it is easier to avoid a problem in the design than to fix it later in the finished work. When two different metals are in contact, the metals used should be as close as possible to one another in the galvanic series. For example, if steel has been proposed for the armatures inside a bronze sculpture, it should be changed to stainless steel, which is higher in the galvanic series in Table 1.
Another approach to preventing galvanic corrosion is to separate different metals with an insulator such as Teflon or another plastic. This could be done, for example, with a more active metal armature in a more noble metal sculpture. Unfortunately, if there are many areas of contact, the failure of even one of these areas will bring the two metals into electrical contact. Moreover, if the insulator becomes porous as it ages, it can act as a sponge and trap electrolytes. This problem occurred in the Statue of Liberty, where separators made of asbestos soaked in shellac eventually became porous (Baboian and Cliver 1990). Insulators placed between metals to prevent galvanic corrosion should be inspected regularly as part of a maintenance program.
Nothing can be done to separate the two metals in a plated object. A plated object where the more noble metal is on top is an example of inherent vice, because the problem of galvanic corrosion is inherent in the object. The only thing to do is to keep the object in an environment that will not lead to galvanic corrosion. Since the metals are irreversibly joined by an electrical connection, the connection through an electrolyte must be avoided. The object should be stored in a dry environment or protected by regular waxing or other coatings. If a statue is meant to be displayed outdoors but would be destroyed by galvanic corrosion, then as a last resort, a replica made from different materials could be placed outdoors instead, while the original is stored indoors in a controlled environment.
If galvanic corrosion is threatening the structural integrity of an object, the corroded parts should be replaced. This can be a challenging task, especially for large sculptures. For example, in the Statue of Liberty, about 1800 wrought iron bars comprising the armature had to be replaced in the 1980s by stainless steel bars (Einbinder 1990, Baboian and Cliver 1990). In the case of the bronze statue of William Penn, which is just over 11 metres high and weighs 27 tonnes, that sits on top of city hall in Philadelphia, wrought iron bolts had been used to anchor the base of the statue when it was installed in 1894. By the 1970s, the bolts were at risk of failure because of deterioration through galvanic corrosion and had to be replaced (Lins 1985).
Activity: demonstrating galvanic corrosion
In the following demonstration of galvanic corrosion, brass, an alloy of copper and zinc, is used to speed up the corrosion of an iron nail. The brass foil used in this demonstration was shim stock with a composition of 70% copper and 30% zinc and a thickness of 0.025 mm (0.001 in.). At this thickness, the foil is easy to bend. The demonstration uses indicators in the electrolyte to show the products of the anodic and cathodic reactions. The electrolyte is mixed with agar to produce a gel so that the colours of the indicators do not disperse. Agar (also called agar-agar) is a fluffy beige powder that is insoluble in water at room temperature but dissolves easily in boiling water and then sets to a firm translucent gel as it is cooled below 40°C (Scott 2012). An inexpensive grade of agar intended for microbiology works well for this demonstration, but other grades should work equally well.
Prior to carrying out this demonstration or making the solutions, consult the safety data sheet for each chemical to be used. Wear recommended personal protective equipment such as eye protection, disposable gloves (such as nitrile) and protective clothing. Phenolphthalein is a presumed carcinogen. The samples from the demonstration should be dried and disposed of as hazardous waste.
Equipment and materials required for demonstrating galvanic corrosion of an iron nail
- Two 25.4 mm (1 in.) iron nails; use common nails, not galvanized
- Brass foil, size 51 mm × 13 mm × 0.025 mm (2 in. × 0.5 in. × 0.001 in.)
- Abrasive sheets, such as regular abrasive papers (in 600–1500 grit range), or cushioned abrasives, such as Micro-Mesh (regular grade in 1800–6000 range)
- Acetone
- Graduated cylinder, 50 mL
- Water (distilled or deionized, but not tap water), about 40 mL
- Glass beaker, 100 mL
- Balance accurate to 0.01 g
- Spatula
- Sodium chloride (NaCl), 1.20 g (not table salt)
- Agar, 1.20 g
- Hot plate
- Glass rod for stirring
- Stopwatch
- Adjustable pipette (also called micropipette) in 200–1000 μL range or graduated 1 mL syringe for transferring 400 or 800 μL volumes
- Graduated cylinder
- Stock solution of 1% (w/v) phenolphthalein in ethanol; consult Preparation of stock solution of indicator: 1% (w/v) phenolphthalein in ethanol.
- Stock solution of 1% (w/v) potassium ferricyanide in water; consult Preparation of stock solution of indicator: 1% (w/v) potassium ferricyanide in water.
- Two Petri dishes, small disposable polystyrene (60 × 15 mm)
- Thermometer (covering range from room temperature to 100°C)
- Small metal file
Procedure for demonstrating galvanic corrosion
- Degrease nails by rubbing with acetone, in case the nails have an oil coating, and dry.
- Use a file to create a straight edge on the head of each nail so that the nail lies horizontal along its length (Figure 5).
- Abrade nails with the slightly coarser abrasive sheet, such as 1800 Micro-Mesh.
- Use acetone to wipe off iron filings and dust from abrasion.
- Degrease the brass foil by wiping with acetone and dry.
- Abrade the brass with the slightly finer abrasive sheet, such as 6000 Micro-Mesh.
- Wipe off any particles from the brass with acetone.
- Gently wrap the brass around the shaft of one nail, leaving about 20 mm unwrapped; the brass does not need to be pulled tight against the nail (Figure 6).
- Place the nail and brass into the bottom of a Petri dish so that the nail lies horizontal (filed edge down) and the brass folds over the top rather than from under the nail.
- Place the other nail into the bottom of another Petri dish so that the nail lies horizontal.
- Prepare a solution containing agar and sodium chloride.
- Measure 40 mL of distilled water into a 100-mL glass beaker using a graduated cylinder.
- Weigh 1.20 g of NaCl using the spatula and the balance, transfer to the water and swirl to dissolve, giving a solution of 3% (w/v) or 0.51 M NaCl.
- Weigh 1.20 g of agar using the spatula and the balance; transfer it to the salt and water mixture, giving a solution of 3% (w/v).
- Use the hot plate to heat the solution until it boils. Stir gently while the solution is heating to prevent agar from sticking to the bottom of the beaker and turning brown.
- Once the solution starts to boil, continue boiling for three minutes (timed). Continue to stir gently while the solution boils.
- Remove from heat and continue to stir gently as the solution cools. At room temperature, it takes about 15 minutes for the solution to cool from boiling to 50°C.
- Monitor the temperature of the solution as it cools. When the solution reaches about 65°C, add the indicators.
- Add 800 μL of potassium ferricyanide solution with an adjustable pipette. The agar solution will turn pale yellow. Mix well so that the colour is even.
- Add 400 μL of phenolphthalein solution with an adjustable pipette. The colour of the solution should remain yellow. Mix well.
- Continue monitoring the temperature of the solution and stirring gently. (Avoid vigorous stirring as this introduces bubbles; continuous stirring prevents the agar from gelling and sticking to the cooler surface of the glass beaker.)
- When the temperature of the solution reaches 50°C, gently pour the solution into the two Petri dishes so that there is just enough to cover the metal samples but no more (about 10 mL). If the flat area of the brass is too close to the bottom of the dish, an air bubble may become trapped under the brass. However, the brass also has a tendency to float, so pouring a little bit of solution on top of the brass as the dish fills will prevent this.
- Record the time. The agar should set fully after about five minutes. Once the agar has set, you should be able to invert the Petri dishes and nothing will fall out.
- Note the colour of the solution at the start of the experiment.
- Monitor the colour for several hours or overnight.
Results of the demonstration of galvanic corrosion of an iron nail
Figure 5 shows a nail with part of the head filed flat, compared with an unfiled nail. Filing the nail this way allows it to lie flat in the Petri dish. Figure 6 shows an iron nail that has been wrapped in brass foil, placed with the filed side down and the foil coming over the top.
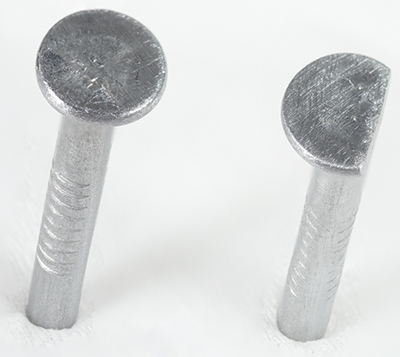
© Government of Canada, Canadian Conservation Institute. CCI 129916-0003
Figure 5. Two iron nails. The head of the nail on the right has been filed down so that the edge is flush with the shaft of the nail.
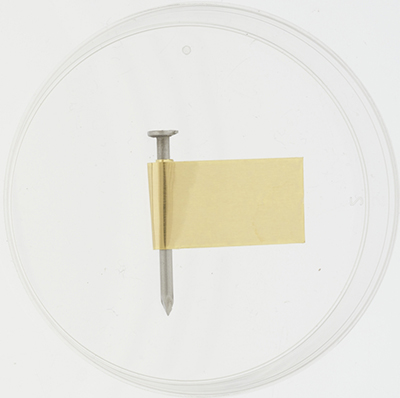
© Government of Canada, Canadian Conservation Institute. CCI 129916-0004
Figure 6. Iron nail wrapped in brass foil in Petri dish.
Figures 7, 8 and 9 show the corrosion of two nails, one in contact with a brass foil and the other with no foil. The pale yellow colour of the agar is caused by the potassium ferricyanide. Figure 7 was taken about two minutes after the agar solution was poured into the Petri dishes. Faint areas of blue and pink are visible. In Figure 8, taken after an hour, the blue and pink regions are well defined, and in Figure 9, after eight hours, they are larger. The corrosion of the nail produces iron(II) ions (Fe2+), which react with the potassium ferricyanide to give a blue colour. Where the oxygen is reduced, OH− ions are produced, which react with phenolphthalein to give a pink colour. The growth of the coloured regions as the nail corrodes is shown in a time-lapse video of galvanic corrosion.

© Government of Canada, Canadian Conservation Institute. CCI 129916-0006
Figure 7. Iron nail and brass foil in Petri dish (on the left) and iron nail in Petri dish (on the right), two minutes after the agar solution has been poured into the Petri dishes. Faint regions of pink and blue are beginning to develop.
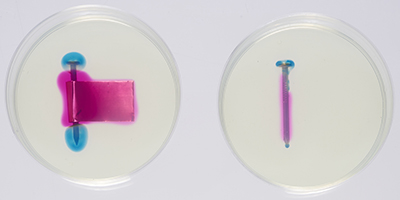
© Government of Canada, Canadian Conservation Institute. CCI 129916-0007
Figure 8. Iron nail and brass foil in Petri dish (on the left) and iron nail in Petri dish (on the right), after one hour. Regions of pink and blue are now clearly defined.
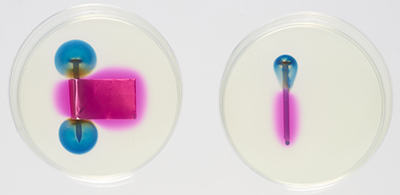
© Government of Canada, Canadian Conservation Institute. CCI 129916-0014
Figure 9. Iron nail and brass foil in Petri dish (on the left) and iron nail in Petri dish (on the right), after eight hours. Regions of pink and blue have increased in size.
In each case, the blue and pink regions are clearly larger for the nail wrapped in brass foil, indicating that the brass has increased the corrosion rate. The increased corrosion is a result of galvanic corrosion of the iron due to contact with the brass. On the nail without brass, the iron generally corrodes where the nail has been stressed during manufacture. In the example here, only the head corroded, but often both ends of the nail corrode to give a blue colour at each extremity and a pink colour in the middle.
The blue colour is from the indicator potassium ferricyanide, which reacts with Fe2+ ions produced by the corrosion of the nail. Potassium ferricyanide (K3[FeIII(CN)6]) dissolves in solution to produce ferricyanide ions ([FeIII(CN)6]3−), which react with the Fe2+ ions to make Prussian blue (Ware 2008). In Figure 9, after eight hours, there are traces of brown within the blue regions. The brown is from Fe(III) compounds, which formed from Fe2+ ions that reacted with oxygen in the solution to form brown rust instead of reacting with the potassium ferricyanide.
The pink colour is from phenolphthalein, a common pH indicator. Phenolphthalein is colourless in neutral and mildly acidic solutions and pink in basic solutions above about pH 8 (Skoog et al. 2014). In Figures 8 and 9, hydroxide ions are produced in the cathodic reaction of oxygen on the surface of the brass in the Petri dish on the left and on non-corroding areas of the nail in the Petri dish on the right. The hydroxide ions make the solution more basic, producing the pink colour. The separation of the pink and blue regions demonstrates that the reaction of oxygen and the corrosion of the nail occur at separate locations.
Additional procedures
Preparation of stock solution of indicator: 1% (w/v) phenolphthalein in ethanol
The following procedure can be used to prepare 100 mL of 1% (w/v) phenolphthalein solution in ethanol.
Equipment and materials required to prepare phenolphthalein stock solution
- Phenolphthalein (white powder)
- Balance accurate to 0.01 g
- Anhydrous ethanol
- Volumetric flask, 100 mL
- Spatula
- Pasteur pipette
- Funnel
- Brown bottle to hold 100 mL
- Label
Procedure to prepare phenolphthalein stock solution
- Fill the 100-mL volumetric flask about halfway with ethanol.
- Weigh 1.00 g of phenolphthalein using the spatula and balance.
- Add phenolphthalein to the ethanol in the volumetric flask.
- Swirl to dissolve as much as possible.
- Fill the volumetric flask to just below the 100-mL mark with ethanol. Mix well.
- Adjust the bottom of the meniscus to the 100-mL line with ethanol using the Pasteur pipette. Note: the solution should be colourless.
- Transfer to the bottle using the funnel.
- Label the bottle.
Preparation of stock solution of indicator: 1% (w/v) potassium ferricyanide in water
The following procedure can be used to prepare 100 mL of 1% (w/v) aqueous potassium ferricyanide solution.
Equipment and materials required to prepare potassium ferricyanide stock solution
- Potassium ferricyanide (red-orange salt)
- Balance accurate to 0.01 g
- Water (distilled or deionized)
- Volumetric flask, 100 mL
- Spatula
- Pasteur pipette
- Funnel
- Brown bottle to hold 100 mL
- Label
Procedure to prepare potassium ferricyanide stock solution
- Fill the 100-mL volumetric flask about halfway with water.
- Weigh 1.00 g of potassium ferricyanide using the spatula and balance.
- Add potassium ferricyanide to the water in the volumetric flask.
- Swirl to dissolve as much as possible.
- Fill the volumetric flask to just below the 100-mL mark with water. Mix well.
- Adjust the bottom of the meniscus to the 100-mL line with water using the Pasteur pipette. Note: the solution should be a yellow-green colour.
- Transfer to the brown bottle using the funnel.
- Label the bottle.
The science behind galvanic corrosion
Corrosion potential and the galvanic series
When a metal corrodes in an electrolyte, atoms from the metal separate into ions and electrons (e-), with the ions dissolving into the electrolyte. For example, for iron (Fe) the reaction is:
Fe → Fe2+ + 2e−
This is called an anodic reaction and Fe2+ ions are formed. Other reactions remove the electrons; for example, oxygen (O2) dissolved in an electrolyte can react to form hydroxide ions (OH−), as follows:
O2 + 2H2O + 4e− → 4OH−
This is called a cathodic reaction. The electrons are deposited in the metal in the anodic reaction and removed from it in the cathodic reaction. A balance is reached when the electrons are deposited and removed at the same rate.
The electric charges of the ions and electrons cause the metal to develop an electric potential. For a corroding metal, where two or more reactions are occurring simultaneously, this potential is called a mixed potential or corrosion potential. The galvanic series given in Table 1 is based on values of corrosion potential. Figure 10 shows corrosion potentials for various metals and alloys measured in seawater, taken from LaQue (1975). The corrosion potential depends on the reactivity of the metal involved. For example, zinc develops a lower (more negative) corrosion potential than iron, placing it below iron in the galvanic series.

© Government of Canada, Canadian Conservation Institute. CCI 129916-0022
Figure 10. Galvanic series for selected metals in seawater. The horizontal bars show the range of corrosion potential for each metal, measured in volts (V) versus a standard calomel electrode (SCE, lower scale) or versus a standard hydrogen electrode (SHE, upper scale). Values are taken from LaQue (1975).
Description of Figure 10
The metals listed below are in order from more noble to more active.
Graphite
Platinum
Stainless steel (alloy 316)
Silver
Nickel
Copper nickel (70:30 wt%)
Lead
Tin bronze
Lead-tin solder (50:50 wt%)
Tin
Copper
Yellow brass
Mild steel, cast iron
Cadmium
Aluminum alloys
Zinc
Magnesium
The corrosion potential depends on all of the reactions occurring at the metal surface; thus, it depends on various factors, such as the composition of the electrolyte and the amount of dissolved oxygen. In Figure 10, the corrosion potential of each metal has a range of values, rather than a single value, because of the variations of such factors. Also because of these variations, references for the galvanic series may show differences in the ordering of the metals. For example, the position of lead in Figure 10 and Table 1 is higher than in the series given by the U.S. Department of Defense (U.S. Department of Defense 2016).
Published tables or graphs of galvanic series may show stainless steel and some other alloys in two positions. One position, usually labelled as "passive," corresponds to the alloy under normal conditions. This is the position for stainless steel given in Table 1 and Figure 10. The other position, labelled as "active," is lower in the galvanic series and applies if the passive film protecting the alloy breaks down, as can happen in pits and crevices (LaQue 1975).
Corrosion of metals in contact
When two metals such as silver and iron are connected in an electrolyte, the potential of the two is forced to be equal and settles to a new value in between the corrosion potentials of the two metals. As a result, the corrosion rates of the two metals change. The more active metal, iron, corrodes more rapidly than it would alone, whereas the more noble metal, silver, corrodes more slowly. At the same time, the rates of the cathodic reactions, such as the reaction of oxygen, change in the opposite direction: that is, the cathodic reaction speeds up on the more noble metal and slows down on the more active metal. The increased corrosion rate of the more active metal, iron in this example, is galvanic corrosion. The galvanic series in itself does not reveal how much the corrosion rate will change, although typically galvanic corrosion is more serious for metals that are far apart in the galvanic series.
Figure 11 shows an example of these reactions in an area where a plated layer of silver has been damaged, exposing the underlying iron. The corrosion in this case is enhanced by the relative areas of the two metals; the top silver layer provides a large area on which oxygen can react.

© Government of Canada, Canadian Conservation Institute. CCI 129916-0020
Figure 11. Schematic diagram of corrosion at a scratch or defect in silver-plated iron.
Acknowledgements
Special thanks to Jacqueline Riddle for her help in developing this CCI learning resource. Thanks also to Jean-Bernard Memet for providing the recipe used in the preparation for the demonstration.
Suppliers
Note: the following information is provided only to assist the reader. Inclusion of a company in this list does not in any way imply endorsement by CCI.
Chemicals and laboratory supplies
Chemicals such as agar, phenolphthalein and potassium ferricyanide are available from chemical supply companies, such as:
Copper alloys
Brass foil is sold as shim stock by Lee Valley Tools.
Micro-Mesh abrasive sheets
Micro-Mesh abrasive sheets are available from Micro-Surface Finishing Products.
Bibliography
Baboian R., and E.B. Cliver. "Corrosion on the Statue of Liberty: An Overview." In R. Baboian, E.B. Cliver and E.L. Bellante, eds., The Statue of Liberty Restoration. Houston, TX: National Association of Corrosion Engineers, 1990, pp. 75–83.
Benson, P.L. "Some Considerations in Determining New Paint Systems for Use in the Treatment of Painted Fiberglass and Steel Outdoor Sculptures." In L. Beerkens and T. Learner, eds., Conserving Outdoor Painted Sculpture: Proceedings from the Interim Meeting of the Modern Materials and Contemporary Art Working Group of ICOM-CC, Kröller-Müller Museum, Otterlo, the Netherlands, 4–5 June 2013. Los Angeles, CA: Getty Conservation Institute, 2014, pp. 87–94.
Davis, J.R., ed. Corrosion: Understanding the Basics. Materials Park, OH: ASM International, 2000, pp. 407–421.
Einbinder, M. "Armature Replacement on the Statue." In R. Baboian, E.B. Cliver and E.L. Bellante, eds., The Statue of Liberty Restoration. Houston, TX: National Association of Corrosion Engineers, 1990, pp. 129–130.
Fontana, M.G. Corrosion Engineering, 3rd ed. New York, NY: McGraw-Hill, 1986, p. 43.
Grissom, C.A. "The Conservation of Outdoor Zinc Sculpture." In D.A. Scott, J. Podany and B.B. Considine, eds., Ancient and Historic Metals: Conservation and Scientific Research. Marina del Rey, CA: Getty Conservation Institute, 1994, pp. 279–304.
LaQue, F.L. Marine Corrosion: Causes and Prevention. New York, NY: Wiley, 1975, p. 179.
Lins, A. "Outdoor Bronzes: Some Basic Metallurgical Considerations." In V. Naudé, ed., Sculptural Monuments in an Outdoor Environment. Philadelphia, PA: Pennsylvania Academy of the Fine Arts, 1985, pp. 8–20.
MacLeod, I.D. "Conservation Management of Iron Steamships—the S.S. Xantho (1872)." In A. Moulds, B.W.S. James, J.F. Moynihan and C. Keith, eds., Fifth National Conference on Engineering Heritage 1990: Interpreting Engineering Heritage, Perth, 3–5 December 1990: Preprints. Perth, Australia: Institution of Engineers, 1990, pp. 75–80.
Maltby, S.L. "The Conservation and Preservation of Architectural Sheet Metal Work." In National Association of Corrosion Engineers Northern Area Eastern Conference, Ottawa, 15–17 September 2003. Ottawa, ON: NACE, 2003. Proceedings on CD.
Mallick, P.K. Fiber-Reinforced Composites: Materials, Manufacturing, and Design, 3rd ed. Boca Raton, FL: CRC Press, 2008, pp. 6–23.
Scott, C.L. "The Use of Agar as a Solvent Gel in Objects Conservation." American Institute for Conservation of Historic and Artistic Works Objects Specialty Group Postprints 19 (2012), pp. 71–83.
Selwyn, L. Metals and Corrosion: A Handbook for the Conservation Professional. Ottawa, ON: Canadian Conservation Institute, 2004, pp. 96–97.
Skoog, D.A., D.M. West, F.J. Holler and S.R. Crouch. Fundamentals of Analytical Chemistry, 9th ed. Belmont, CA: Brooks/Cole, 2014, pp. 323–326.
U.S. Department of Defense. MIL-STD-889C. Department of Defense Standard Practice: Dissimilar Metals. N.p.: Department of Defense, United States of America, 2016.
Ware, M. "Prussian Blue: Artists' Pigment and Chemists' Sponge." Journal of Chemical Education 85,5 (2008), pp. 612–621.
Zhang, X.G. "Zinc." In R.W. Revie, ed., Uhlig's Corrosion Handbook, 2nd ed. Hoboken, NJ: Wiley, 2006, pp. 887–904.
Page details
- Date modified: