Preventing and Treating the Dezincification of Brass – Canadian Conservation Institute (CCI) Notes 9/13
List of abbreviations
- CAC
- Canadian Association for Conservation of Cultural Property
- M
- molarity
- MRS
- Materials Research Society
- SCE
- standard calomel electrode
- SHE
- standard hydrogen electrode
- V
- volt
- wt%
- weight percentage
Introduction
When brass corrodes, it can undergo dezincification, a process in which zinc is lost and copper is left behind. Mild dezincification may simply cause a cosmetic change, namely, the colour of the surface turning from yellow to pink, but severe dezincification can lead to the weakening of brass and even its perforation. This Note explains what dezincification is and where it can be encountered in conservation as well as how to prevent and treat it. The Note also describes a demonstration of mild dezincification.
The dezincification process
Dealloying and dezincification
An alloy is a mixture of two or more elements, where at least one of the elements is a metal. Sterling silver, an alloy of silver and copper, contains two metallic elements; steel contains one metallic element (iron) and one non-metallic element (carbon). Brasses are alloys of mainly copper and zinc, with small percentages of other elements such as tin, lead or arsenic.
In many alloys, corrosion may result in the loss of the more reactive component of the alloy, with the less reactive component left behind. General terms for this process are "dealloying," "selective corrosion" or "selective leaching." More specific terms applying to the loss of specific metals are "decuprification" for loss of copper, "destannification" for loss of tin and "dezincification" for loss of zinc.
The actual mechanism of dezincification is still not completely agreed upon. For many years, there were two competing proposals (Weisser 1975). In one, the zinc preferentially corrodes and is removed from the alloy, leaving the copper behind. In the other, both the copper and zinc corrode and are removed from the alloy, but the copper ions in solution plate back onto the surface. In the first proposal, the surface of the metal should become porous after dezincification but, otherwise, should not change. The second proposal, although more complicated, is needed to explain cases where copper crystals appear on the surface after dezincification (Walker 1977).
More recently, a third mechanism has been gaining support (Weissmüller et al. 2009, Newman et al. 1988). In this mechanism, the zinc dissolves out of the brass, leaving behind the copper, and then the copper rearranges on the surface of the metal, leading to the formation of copper crystals. This rearrangement is possible because the copper on the surface is attracted by negative ions in the solution. The attraction is not enough to dissolve the copper, but it does weaken the binding of the copper to the surface, allowing the copper to move around more rapidly (Erlebacher et al. 2012).
Dezincification usually occurs in relatively mild conditions, such as in slightly acidic or alkaline solutions (Moss 1969). For example, Weisser (1975) observed the dezincification of a brass object after treatment in an alkaline solution. In strong acids, however, both the copper and zinc dissolve and the surface is not enriched in copper.
Dezincification can also occur when brass is exposed to solutions that contain chloride ions, such as seawater (Moss 1969). One example is dezincification of brass doors and brass kickplates that had been exposed to de-icing salt. Morissette (2008) reported dezincification of a set of brass doors that had changed colour from yellow to pink after being cleaned with hydrochloric acid.
Brass
There are several possible atomic arrangements of copper and zinc in brass, but only the alpha and beta phases are important in commercial brasses. The alpha phase ranges from pure copper to about 35 wt% zinc. The beta phase has zinc contents near 50 wt%. Between 35 wt% and 50 wt% zinc, brass is a mixture of alpha and beta phases, called duplex brass. Commercial brasses are either alpha brass or duplex brass.
Brass containing less than 15 wt% zinc resists dezincification, but brass with more than 15 wt% zinc is susceptible to the phenomenon. Duplex brass is even more prone to dezincification than alpha brass (Scott 2002).
The first sign of dezincification of brass is a change in colour, from the yellow typically found in brass to the salmon pink of pure copper metal. The pink colour may then turn reddish and then brown if the surface copper corrodes to form cuprite. More severe dezincification produces a porous, weak metal, which is mainly copper (Dinnappa and Mayanna 1987). Severe dezincification of brass plumbing fixtures can perforate the brass and cause leaks.
Figure 1 compares the colour of brass to the colours of pure copper and zinc. The brass in the figure is an alloy of 70 wt% copper and 30 wt% zinc, which is known by various terms, such as "cartridge brass," "alloy C26000" or "C260 brass." It is the strong difference in colour between brass and copper that leads to the dramatic changes in appearance when zinc is removed from the brass by dezincification.
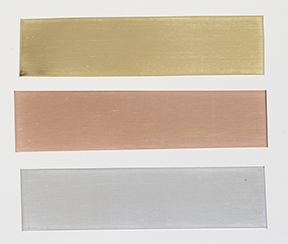
© Government of Canada, Canadian Conservation Institute. CCI 129915-0014
Figure 1. From top to bottom: cartridge brass, pure copper and pure zinc.
Relative reactivity of zinc and copper
When a metal or an alloy corrodes, metal atoms lose electrons through an electrochemical reaction and either dissolve in the solution as ions or are incorporated into a corrosion product such as an oxide. In an alloy, as opposed to a pure metal, the more reactive component has a greater tendency to react. In brass, zinc is more reactive than copper, and so the zinc is lost preferentially.
The relative reactivity of zinc and copper can be estimated through their position on electrochemical scales. There are two common scales that can be used for this estimate. The scale of standard reduction potential gives the values of potential for electrochemical reactions under standard conditions, usually for concentrations of 1 M for all chemical species in solution. On this scale, zinc has a potential of −0.763 V versus the standard hydrogen electrode (SHE), whereas copper has a higher value, 0.340 versus SHE (Dean 1992). The lower potential for zinc indicates that zinc is more reactive, and the size of the difference, about 1 V, indicates a considerable difference in reactivity.
Alternatively, zinc and copper can be compared using the galvanic series, which gives the potentials of metals measured in some solution, usually seawater. On this scale, zinc is in the range of −0.8 to −1.03 V versus the standard calomel electrode (SCE), whereas copper is −0.29 to −0.36 V versus SCE (LaQue 1975). Here, zinc is about 0.6 V below copper, again indicating that zinc is significantly more reactive. The galvanic series is discussed further in the CCI learning resource Understanding galvanic corrosion.
Dezincification of objects
Examples of dezincification of objects
Figure 2 shows a French horn affected by dezincification; for comparison, Figure 3 shows a similar horn in pristine condition. The horns are made of brass, and the moving slides, supports and stays are made of nickel-silver (an alloy of copper, zinc and nickel). The dezincified horn was used in a school band for about thirty years, and was rarely, if ever, polished or cleaned. The dezincification was caused by the handling of the horn with bare hands. In the musical community, dezincification of brass in musical instruments is called "red rot," but this term is used more often in conservation to describe the deterioration of leather.
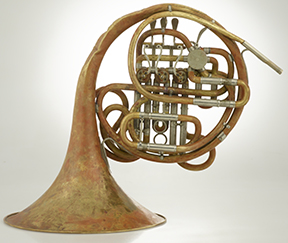
© Government of Canada, Canadian Conservation Institute. CCI 129915-0003
Figure 2. French horn (made circa 1966), showing pink areas typical of dezincification.
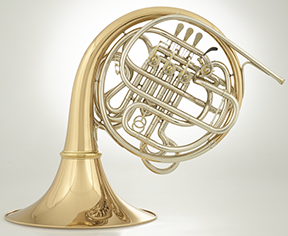
© Government of Canada, Canadian Conservation Institute. CCI 129915-0002
Figure 3. Modern French horn (made in 2010) showing the typical yellow colour of polished brass.
Some commercial polishes marketed for copper alloys are acidic and can cause dezincification. This is normally not noticed, because the polish also contains an abrasive. When the polish is rubbed on the surface, the abrasive removes the copper-rich surface as fast as the dezincification occurs. If the polish is left on the surface, however, dezincification can be observed.
Figure 4 shows a brass tray with dezincification produced by a commercial polish that contained citric acid. The pink areas in the photograph were originally covered with masking tape, which was applied around a small rectangular strip that was left uncovered. The central strip and the masking tape around it were covered with acidic commercial polish and left overnight. After the polish was rubbed off, the central strip was clean and shiny, probably because of the abrasive in the polish. When the masking tape was pulled off, the pink areas were revealed. Those areas had undergone dezincification because liquid from the polish had seeped under or through the tape. Dezincification also occurs when brass is cleaned with a mixture of salt and vinegar.
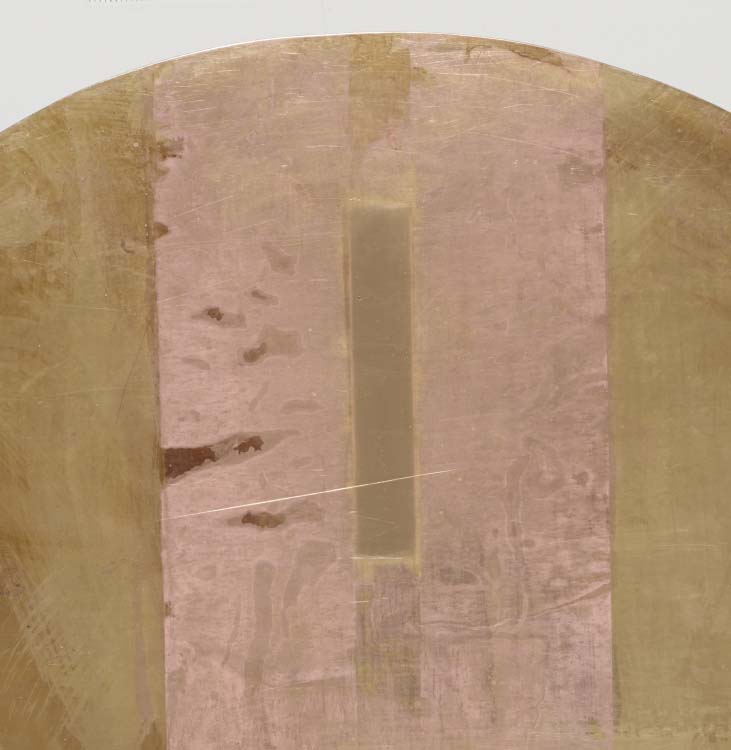
© Government of Canada, Canadian Conservation Institute. CCI 129915-0018
Figure 4. Part of a brass tray after exposure to an acidic commercial polish overnight. The pink regions, which had been covered with masking tape, have been affected by dezincification, whereas any signs of dezincification on the central strip, where there was no tape, were removed when the polish was rubbed off.
Preventing dezincification
Other elements can be added in brass with higher zinc concentrations to make the brass more resistant to dezincification. Ancient brass alloys, which generally contain tin or impurity elements, resist dezincification better than modern brass alloys that contain only copper and zinc (Scott 2002). Modern tin brass has about 0.5 to 1 wt% tin added to the copper-zinc alloy; such alloys are significantly more resistant to dezincification than the same alloys without tin (Selwyn 2004). When this amount of tin is added to cartridge brass, the resulting alloy is called admiralty brass. Further protection against dezincification is obtained if smaller amounts of arsenic, antimony or phosphorus, in the range of 0.02 to 0.1 wt%, are added to tin brass. Today's admiralty brass generally contains one of these three elements in addition to tin.
Brass should be kept clean and dust free. It should be handled with gloves to avoid contact with salts and acids in perspiration. Brass in public spaces should be cleaned regularly. If possible, commercial polishes should be avoided. Some of these contain acids to speed up cleaning; others contain ammonia to remove dirt and grease. Both acids and alkaline solutions can cause dezincification. An abrasive slurry could be prepared instead, based on precipitated calcium carbonate or other harder abrasives. For detailed preparation instructions, consult CCI Note 9/11 How to Make and Use a Precipitated Calcium Carbonate Silver Polish.
Whenever brass is cleaned, it should be rinsed well so that any residues from cleaning are removed. Residues of commercial polish left on copper alloys may react with the copper to produce green-blue compounds. Citric acid, for example, is found in some polishes and will produce green copper citrate. Even non-reactive residues will be noticeable if they accumulate in crevices.
Polished brass is often coated (for example, with a clear lacquer or wax) to protect the shiny surface from tarnishing. Such a coating will also minimize dezincification, as long as the layer remains adherent and undamaged. The disadvantage of a coating is that it has a finite lifetime and requires regular maintenance or removal and replacement. For questions about coatings, a conservator should be consulted. For further discussion on the care of historical brass and bronze, consult Deck (2016) and Harris (2006).
Dealing with dezincification
Signs of dezincification may be mild and confined to the surface of brass, or they may extend deeply into the brass, sometimes all the way through it. Severe dezincification may require that a piece be replaced, where this is feasible. The effects of mild dezincification, somewhat like tarnish on silver, can be removed with abrasive polishing. The decision to treat a brass object showing mild effects of dezincification or to replace a brass object severely affected by dezincification should be made jointly by a conservator and a curator.
Demonstrating the dezincification of brass
The following demonstration shows the dezincification of brass. The brass used in this demonstration was shim stock with a composition of 70 wt% copper and 30 wt% zinc and a thickness of 0.13 mm (0.005 in.). This thickness is a convenient choice because the brass can easily be cut with scissors or sheet metal shears without bending. Thicker brass is harder to cut, and thinner brass will bend or crumple when cut.
Prior to carrying out the procedure for dezincification, consult the safety data sheet for each chemical to be used. Wear recommended personal protective equipment such as eye protection, disposable gloves (such as nitrile) and protective clothing. When working with hydrochloric acid and organic solvents, use a fume hood, if possible, and always wear disposable nitrile gloves.
Equipment and materials required to dezincify brass
- Brass, size 51 mm × 13 mm × 0.13 mm
- Hydrochloric acid, about 0.1 M, pH 1.0 (about 15 mL needed per piece of brass)
- Ethanol or acetone
- Water (distilled or deionized)
- Lint-free tissues such as Kimwipes
- Beaker, 20 mL
- Abrasive sheets, such as regular abrasive papers (in 600–1500 grit range), or cushioned abrasives, such as Micro-Mesh (regular grade in 1800–6000 range)
Procedure for demonstrating dezincification
- Degrease a brass sample by rubbing with ethanol or acetone. (Brass sheets may have an oil coating applied during fabrication.) Make sure not to touch the surface after the brass is cleaned. Always wear gloves and hold the piece by the edge.
- Polish the sample with an abrasive sheet, such as the 6000 Micro-Mesh used in this example. Wipe away any residual abrasive with a lint-free tissue, such as the Kimwipes used in this procedure, wetted with ethanol or acetone.
- Dry the sample quickly with a tissue so that solvent does not cool the sample by evaporation; otherwise, water can condense on the sample and leave spots as it dries.
- Stand up a brass strip of 51 mm × 13 mm in a 20-mL beaker.
- Fill the beaker with enough 0.1 M hydrochloric acid to cover the bottom half of the brass strip.
- Monitor the colour of the brass every two hours or so. If needed, leave the brass sample inside the solution overnight.
- Remove the brass strip, rinse with water and dry.
- Polish off the pink dezincified area using a series of abrasive sheets, such as those used in this procedure. Start with 1800 Micro-Mesh, then use 3600, 4000 and, finally, 6000.
Results of this demonstration
Figure 5 shows how the dezincification progresses with time. The brass strip on the left was not immersed in hydrochloric acid, while the other three strips were immersed for varying lengths of time. The dezincification occurred mainly in the first few hours, and there was not much change after 24 hours.
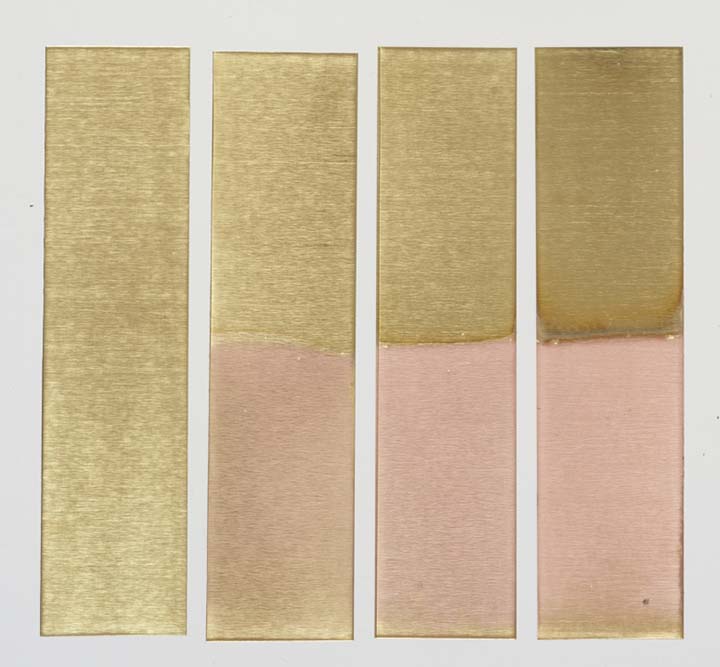
© Government of Canada, Canadian Conservation Institute. CCI 129915-0015
Figure 5. Four strips of brass shim stock showing dezincification after different amounts of time in 0.1 M hydrochloric acid, without stirring. From left to right: no exposure to hydrochloric acid, 6 hours of exposure, 24 hours of exposure and 72 hours of exposure.
The layer produced by dezincification in this demonstration is thin enough to be removed by polishing. Figure 6 shows a strip of brass that was partly dezincified in hydrochloric acid for 24 hours and then partly polished.The right two-thirds of the brass strip was immersed for 24 hours in the acid, rinsed and then dried, producing a pink surface. Then the upper half of the strip was polished with Micro-Mesh abrasive sheets, starting with 1800, then 3600, 4000 and, finally, 6000. The polishing completely removed the pink dezincified layer from the right end of the brass. The polished area in Figure 6 appears dull because the lighting in the photograph was adjusted to enhance the pink colour. The vertical lines in the lower portion of the brass in Figure 6 are from the manufacturing process.
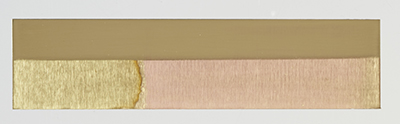
© Government of Canada, Canadian Conservation Institute. CCI 129915-0016
Figure 6. Effect of polishing on lightly dezincified brass.
Acknowledgements
Special thanks to Ghazaleh Rabiei for her help in developing this Note. Thanks also to Roger Baird for supplying the French horns used in the photographs.
Suppliers
Note: the following information is provided only to assist the reader. Inclusion of a company in this list does not in any way imply endorsement by CCI.
Chemicals and laboratory supplies
Chemicals, such as 0.1 M hydrochloric acid, and laboratory supplies are available from chemical supply companies, such as Fisher Scientific.
Copper alloys
Brass foil is sold as shim stock by Lee Valley Tools.
Micro-Mesh abrasive sheets
Micro-Mesh abrasive sheets are available from Micro-Surface Finishing Products.
Bibliography
Dean, J.A. Lange's Handbook of Chemistry, 14th ed. New York, NY: McGraw-Hill, 1992, pp. 8.124–8.139.
Deck, C. The Care and Preservation of Historical Brass and Bronze (PDF format). Dearborn, MI: Benson Ford Research Center, 2016.
Dinnappa, R.K., and S.M. Mayanna. "The Dezincification of Brass and Its Inhibition in Acidic Chloride and Sulphate Solutions." Corrosion Science 27,4 (1987), pp. 349–361.
Erlebacher, J., R.C. Newman and K. Sieradzki. "Fundamental Physics and Chemistry of Nanoporosity Evolution During Dealloying." In A. Wittstock, J. Biener, J. Erlebacher and M. Bäumer, eds., Nanoporous Gold: From an Ancient Technology to a High-Tech Material. Cambridge, UK: Royal Society of Chemistry, 2012, pp. 11–29.
Harris, R. "Metalwork." In The National Trust Manual of Housekeeping: The Care of Collections in Historic Houses Open to the Public. Oxford, UK: Butterworth-Heinemann, 2006, pp. 248–259.
LaQue, F.L. Marine Corrosion: Causes and Prevention. New York, NY: Wiley, 1975, p. 179.
Morissette, J.R. "Across the Country – Dans tout le pays: Québec Area — Centre de conservation du Québec." CAC Bulletin 33,1 (2008), p. 17.
Moss, A.K. "The Corrosion of Copper and Copper Alloys." Australasian Corrosion Engineering 13,5 (1969), pp. 5–11.
Newman, R.C., T. Shahrabi and K. Sieradzki. "Direct Electrochemical Measurement of Dezincification Including the Effect of Alloyed Arsenic." Corrosion Science 28,9 (1988), pp. 873–886.
Scott, D.A. Copper and Bronze in Art: Corrosion, Colorants, Conservation. Los Angeles, CA: Getty Publications, 2002, pp. 27–32.
Selwyn, L. Metals and Corrosion: A Handbook for the Conservation Professional. Ottawa, ON: Canadian Conservation Institute, 2004, pp. 55 and 70.
Selwyn, L. How to Make and Use a Precipitated Calcium Carbonate Silver Polish. CCI Notes 9/11. Ottawa, ON: Canadian Conservation Institute, 2016.
Walker, G.D. "An SEM and Microanalytical Study of In-service Dezincification of Brass." Corrosion 33,7 (1977), pp. 262–264.
Weisser, T.S. "The De-alloying of Copper Alloys." Conservation in Archaeology and the Applied Arts. Preprints of the contributions to the Stockholm Congress, 2–6 June 1975. London, UK: International Institute for Conservation of Historic and Artistic Works, 1975, pp. 207–214.
Weissmüller, J., R.C. Newman, H.-J. Jin, A.M. Hodge and J.W. Kysar. "Nanoporous Metals by Alloy Corrosion: Formation and Mechanical Properties." MRS Bulletin 34,8 (2009), pp. 577–586.
By Lyndsie Selwyn
© Government of Canada, Canadian Conservation Institute, 2019
Cat. No.: NM95-57/9-13-2019E-PDF
ISSN 1928-1455
ISBN 978-0-660-28433-0
Page details
- Date modified: