Control banding guideline
From: Employment and Social Development Canada
This guideline is intended to assist federally regulated workplace parties, who may lack occupational hygiene expertise, understand how to manage and control exposure to chemical agents, in particular those, which do not have occupational exposure limits, such as nanoparticles. The guideline will be especially useful for industrial hygiene specialists and health and safety professionals who may be recommending control measures including respiratory protection devices for such substances which do not have occupational exposure limits established, to ensure employee protection. The purpose of this guideline is to support the Labour Program’s mandate of fostering safe and healthy workplace environment.
On this page
- 1.Introduction
- 2. Generic control banding process
- 3. Limitations of control banding
- 4. Manufactured nanomaterials
- 5. Diesel engine exhaust emissions
- 6. Control banding applied to respirators
- 7. Use of safety data sheet information
- 8. Control banding example
Alternate formats
Large print, braille, MP3 (audio), e-text and DAISY formats are available on demand by ordering online or calling 1 800 O-Canada (1-800-622-6232). If you use a teletypewriter (TTY), call 1-800-926-9105.
1. Introduction
1.1 Summary
In general terms, control banding (CB) is a qualitative or semi-quantitative risk assessment and management approach used to determine prevention and control measures based on the so-called “band” of hazards and exposures. Once a hazard is recognized, it is necessary to control it to ensure that the health and safety of employees is protected. A hazard investigation requires that the hazard is evaluated and a decision is made on what can be done to reduce or control the risk. Control banding is a technique used to guide the assessment and management of chemical risks in a workplace. It is a generic technique that recommends a control measure or personal protective equipment suitable to prevent or minimize employee exposure to the chemical in question based on the toxicity of the chemical and the amount of the chemical present in the workplace. The consideration of other relevant details regarding the chemical in question improves the control banding process, such as the physical state and how it is used in the workplace. In other words, it is a complementary approach to the traditional methods of air sampling and analysis, but it is not a replacement for experts in occupational health and safety, nor does it eliminate the need to take air samples or to establish or replace occupational exposure limits (OELs).
This guideline has been developed by Employment and Social Development Canada (ESDC) Labour Program to assist federally regulated workplace parties, who may lack occupational hygiene expertise, understand how to manage and control exposure to chemical agents, in particular those, which do not have occupational exposure limits, such as nanoparticles. The guideline will be especially useful for industrial hygiene specialists and health and safety professionals who may be recommending control measures including respiratory protection devices for such substances which do not have occupational exposure limits established, to ensure employee protection.
1.2 Background
The concept of banding of risk relating to explosive events, radiation, lasers, and biological agents dates back to the 1970s.Footnote 1 During the late 1980s, the pharmaceutical industry developed a categorization system for exposure control using industrial hygiene as a foundational platform, known as the Control Banding ModeFootnote 1. This model offered a simplified solution for controlling worker exposures to chemicals often encountered in the workplace.Footnote 1 Moreover, the modernization of this model involved an approach developed for “non-experts to input hazard and exposure potential information for bulk chemical processes, receiving control advice as a result”.Footnote 1 The growth in the “use of chemicals in small business and emerging economies, where access to people with the experience to assess and control exposure to chemicals is limited,”Footnote 1 has led to the refinement of a new approach to the control of chemicals.Footnote 2
The Canadian Centre for Occupational Health and Safety (CCOHS) explains the CB system as groups of chemicals which have similar physical or chemical characteristics, and how these chemicals are to be handled or processed, and what the anticipated exposure is expected to be.Footnote 3
The concept of CB was first created and applied in the pharmaceutical industry to decide on control measures for dusts produced in the drug manufacturing process.Footnote 4 However, CB is not meant to replace more well-established occupational hygiene programs for specific chemical agents. It is a generalized procedure that can be applied to any chemical agent in the form of a dust or vapour.Footnote 5 The term “band” refers to the OEL range of airborne concentrations assigned to a certain health risk category.
Although current occupational health and safety regulations may not specifically address chemicals that lack an OEL, the employer still has a duty to protect the health and safety of its employees under the Canada Labour Code, section 124.Footnote 6 It is important for employers to take a precautionary approach for chemicals lacking an OEL or lacking information on health effects. CB is an attractive option for controlling chemical or bioaerosol exposures because it facilitates decision making for employers and employees based on incomplete information.Footnote 7
This guideline gives special attention to CB applied to manufactured nanoparticles and other carcinogens which do not have established OELs, and are the most relevant to the federal jurisdiction.
1.3 Issue
Control banding (CB) has been developed as a practical tool to manage the risk resulting from exposure to a wide variety of potentially hazardous substances in the absence of firm toxicological and exposure information and has become an attractive option for implementing suitable and feasible control measures where quantitative risk information is limited.Footnote 8
Thousands of chemicals do not have an established occupational exposure limit and many new chemicals are created each year, which also lack an established OEL based on scientific research.Footnote 9, Footnote 10 As well, the process of establishing an OEL for a chemical agent is long and expensive. Thus, the CB approach is used to supplement existing OELs so that the occupational health of employees who work with chemicals lacking an OEL is protected.
1.4 Definitions of key terms
Carcinogen: An agent capable of inducing benign or malignant neoplasms. Evidence of carcinogenicity comes from epidemiology, toxicology, and mechanistic studies. The notations of A1, A2, A3, A4, and A5 are used by the American Conference of Governmental Industrial Hygienists (ACGIH®) to define the categories for carcinogenicity. See Appendix A of the ACGIH® TLVs® and BEIs® publication for these categories and definitions, and their relevance to humans in occupational settings.Footnote 11
Corrosive: Having the quality of corroding or eating away; erosive.Footnote 12
Health hazard: A possibility that a substance will cause injury or harm. A degree of the health hazard depends on: physiochemical property of the substance; exposure dose; manner in which the substance is used; route of entry; individual susceptibility; synergistic and other effects.Footnote 13
Irritant: A biological, chemical, or physical agent that stimulates a characteristic function or elicits a response, especially an inflammatory response.Footnote 12
LC50: LC stands for lethal concentration. In industrial hygiene, LC values refer to the concentration of a chemical in air. LC50 is the concentration of a substance in air which causes the death of 50% of a group of test animals. The substance is inhaled over a set period of time, usually one or four hours. The LC50 helps to determine the short-term poisoning potential of a substance.Footnote 14
LD50: LD stands for lethal dose. LD50 is the amount of a material, given all at once, which causes the death of 50% of a group of test animals. The LD50 is one measure of a short-term poisoning potential (acute toxicity) of a substance.Footnote 14
Mutagenic agent: An agent capable of inducing mutation or increasing its rate.Footnote 12
Reproductive hazard: A biological, chemical, or physical agent that is toxic or causes harm to reproductive organs or to a fetus.
Sensitizer: An agent capable of producing dermal sensitization (DSEN) and/or respiratory sensitization (RSEN). The absence of a DSEN or RSEN notation does not signify that the agent lacks the ability to produce sensitization but may reflect the paucity or inconclusiveness of scientific evidence. RSEN and DSEN are ACGIH® terms.Footnote 11 Sensitization often occurs via an immunologic mechanism and should not be confused with hyperreactivity, susceptibility, or sensitivity.
Sensitizer: An agent capable of producing dermal sensitization (DSEN) and/or respiratory sensitization (RSEN). The absence of a DSEN or RSEN notation does not signify that the agent lacks the ability to produce sensitization but may reflect the paucity or inconclusiveness of scientific evidence. RSEN and DSEN are ACGIH® terms.Footnote 11 Sensitization often occurs via an immunologic mechanism and should not be confused with hyperreactivity, susceptibility, or sensitivity.
Surface chemistry: The chemical properties of the surface of a substance. Particle surface free radical activity is the primary factor that influences a nanomaterial's overall surface reactivity.Footnote 15 Nanoscale materials have far larger surface areas than similar masses of larger-scale materials. As surface area per mass of a material increases, a greater amount of the material can come into contact with surrounding materials, thus increasing reactivity.Footnote 16
2. Generic control banding process
2.1 Hazard identification
The employer is responsible for identifying chemical hazards to employee health and taking proper precautions to effectively control the chemical hazard in accordance with the Canada Occupational Health and Safety Regulations (COHSR) Part X: Hazardous Substances as well as Part XIX: Hazard Prevention Program.Footnote 17
2.2 Risk assessment
After an uncontrolled chemical hazard is identified, the employer must ensure that a hazard investigation is conducted by a qualified person in order to properly assess the health risks to employees (COHSR section 10.4).Footnote 17 The scope of the hazard investigation is to establish the degree of the health hazard.
Therefore, the qualified person must consider, among other things, the following factors in the hazard investigation:
- physical and chemical properties of the substance;
- exposure dose;
- manner in which the substance is used;
- routes of entry;
- individual susceptibility; and
- synergistic and other effects, if applicable.
The qualified person must issue a written report with recommendations respecting the manner of compliance with COHSR sections 10.7 to 10.26, including recommendations for sampling and testing methods. The employer must keep the report related to the hazard investigation for at least 30 years (COHSR section 10.6).Footnote 17
Table 1. Risk rating
Probability x Severity = Risk | Severity | |||
---|---|---|---|---|
Low | Medium | High | ||
Probability | High | Medium risk | High risk | High risk |
Medium | Low risk | Medium risk | High risk | |
Low | Low risk | Low risk | Medium or high risk |
Note: Table 1 was modeled after Table 9.1 in the ICOH publication Creating a Safe and Healthy Workplace: A guide to Occupational Health and Safety for Entrepreneurs, Owners and ManagersFootnote 13.
After a basic risk level is established for the chemical, a hazard band from A to E must be selected using a table similar to Table 2. The hazards identification and the toxicological information sections of the chemical safety data sheet (SDS) can be used to choose a hazard group and corresponding hazard band letter. Table 2 has been slightly modified by removing colours, modifying hazard descriptions to be more consistent with hazard statements relating to toxicity, and changing the name of the table from “Control banding by level of hazard” to “Hazard bands”.
Table 2: Hazard bands
Hazard band | Description in words (“toxic” here means poisonous) |
Hazard Group The chemical is described as having these effects, or effects that are similar or just as bad |
The OEL or exposure standard is in this range | |
---|---|---|---|---|
Exposure levels for dusts in air (mg/m3) | Exposure levels for chemical vapours in air (ppm) | |||
A | Minimal hazard. Not very toxic. | Skin irritation or mild eye irritation | 1 to greater than 10 | 50 to greater than 500 |
B | Harmful, moderate hazard. | Harmful on a single exposure | 0.1 to 1.0 | 5 to 50 |
C | Severe hazard, can cause serious health problems. | Very irritating to skin and eyes, corrosive, toxic | 0.01 to 0.1 | 0.5 to 5 |
D | Very toxic, highly dangerous. Can cause death or serious health problems. | Very toxic on a single exposure, may have bad effects during pregnancy or other serious disease or death | Less than 0.01 | Less than 0.5 |
E | Special cases | Chemicals that cause cancer* or that can cause sensitization* | Any level – these are special cases that require a professional evaluation |
*Exposure to any concentration of a carcinogen or sensitizer requires specialist advice.
Note: Table 2 was modeled after Table 9.2 in the ICOH publication Creating a Safe and Healthy Workplace: A guide to Occupational Health and Safety for Entrepreneurs, Owners and Managers (PDF format, 2,15 MB).Footnote 13
2.3 Control banding
After an employer conducts a hazard investigation, risk rating, and chooses a hazard band, the hazard band and probability factors of the risk rating must be used to determine the necessary control measures to prevent employees from overexposure. A control banding table, such as Table 3, is useful for this purpose. In order to find the most appropriate level of a control measure, in the far right column of Table 3, it is necessary to select the combination of a hazard band letter (A, B, C, or D) and the approximate amount of the chemical used in the workplace that applies to the process.Footnote 13 It must be noted that if from Table 2, hazard band E that requires a professional evaluation is selected, it is necessary to go from Table 2 directly to Table 4, in order to arrive at control band 4, requiring specialist advice.
Table 4. Control bands
Amount of the chemical present in the workplace at any one time (The letters in these boxes correspond to hazard bands in Table 2.) |
Recommended control measure (The numbers correspond to the control bands in Table 4.) |
|||
---|---|---|---|---|
A little (grams or millilitres) | Some (kilograms or litres) | A lot (hundreds of kilograms or litres up to a few metric tonnes or cubic metres) | Bulk (many metric tonnes or cubic metres tanks) | |
C | B | A | A | 1: General ventilation, basic hygiene |
D | C | B | A/B | 2: Local exhaust, engineering controls |
D | D | C | C | 3: Enclosure, containment, strict engineering controls |
Note: Table 3 was modeled after Table 9.4 in the ICOH publication Creating a Safe and Healthy Workplace: A guide to Occupational Health and Safety for Entrepreneurs, Owners and Managers (PDF format, 2,15 MB).Footnote 13
The four levels of control bands are illustrated more clearly below in Table 4.
Table 4. Control bands
Control Band | Basic approach for airborne hazards* | Basic approach for other risks |
---|---|---|
1 | General ventilation | Basic occupational hygiene practice, such as housekeeping, administrative controls |
2 | Local exhaust ventilation | Engineering controls |
3 | Isolation, containment | Enclosure, containment, strict engineering controls |
4 | Requires specialist advice | Requires specialist advice |
* Airborne hazards are dusts and chemical vapours.
Note: Table 4 was modeled after Table 9.3 in the ICOH publication Creating a Safe and Healthy Workplace: A guide to Occupational Health and Safety for Entrepreneurs, Owners and Managers (PDF format, 2,15 MB).Footnote 13
It is essential that the employer collaborate with the employees in the implementation of appropriate control measures for the chemical hazard (COHSR 10.5(a)(ii) and 10.5(b)),Footnote 17 as well as assess the effectiveness of the newly implemented control measures to ensure the protection of employees.Footnote 17 It is also necessary that the employer follow the requirements of the COHSR 19.1, including a plan implementation, hazard identification and assessment methodology, hazard identification and assessment, preventive measures, employee education; and a program evaluation.Footnote 17
It is recommended that the employer use an online tool to assist with CB. One such online tool is the United Kingdom Health and Safety Executive (HSE) Control Of Substances Hazardous to Health (COSHH) Essentials COSHH e-tool, which requires the risk phrases or hazard statements of the chemicals of interest.Footnote 18 Risk phrases and hazard statements are explained in section 7 of this guideline. If the substance or product is a liquid, then the boiling point must also be entered into the COSHH e-tool. The tool also requires general information about the task.Footnote 18 Using all gathered information, the COSHH e-tool outputs a recommended control band and provides advice on controlling risk.Footnote 3 An example of how to use the COSHH e-tool is provided in section 8.
Image description
Hazard Investigation
- Employer must identify the hazard (COHSR 19.4-6)
- Hazard investigation must be conducted by a qualified person
Risk Assessment (COHSR 10.4)
- Use risk rating table
- Prioritize hazards based on risk level<
Control Banding
- Use hazard band and amount to determine controls
- Implement and assess effectiveness of new control measures and training (COHSR 19.5-7)
2.4 Air sampling for control banding
Taking air samples is an important part of CB for monitoring airborne concentrations of chemicals in the workplace. Selecting an appropriate sampling and analysis method must be conducted by a qualified person in accordance with COHSR section 10.19.sFootnote 17
Also, the ESDC Labour Program guideline document Canadian Occupational chemical agent compliance sampling guideline should be consulted for more information on conducting air sampling.Footnote 19 It is important that all analyses of occupational exposure air samples be conducted in a laboratory that is accredited for the relevant analysis methods.
3. Limitations of control banding
Using CB may result in different workplaces using different CB ranges for the same chemical for the same industrial process. This reality will pose challenges for enforcing OHS compliance because it is possible for multiple suitable CB options for a workplace.
3.1 Limitations due to occupational hygiene expertise
It may not be possible for specific CB options to be proven correct or incorrect due to a lack of scientific research and validation of scientific research on the chemical agent of interest.Footnote 5 Similarly, although CB is meant for employers that lack occupational hygiene expertise, the risk of inappropriate CB implementation by an employer without occupational hygiene expertise is higher than for an employer that has occupational hygiene expertise.Footnote 20 As well, specialist advice from an occupational hygienist or other qualified person is required to assess employee risk from the exposure to carcinogenic substances and the effectiveness of new control measures implemented as a result of any CB initiative. Target ranges of exposure concentration in a CB table are much less specific than an OEL. This is an issue, since the wider range exposure concentration is not as protective for worker health as an OEL, which is chosen based on scientific research.
3.2 Limitations due to engineering controls
Several limitations of CB are discussed in scientific literature, including the subjectivity of the level of engineering controls applied to a chemical substance that has unknown health hazards.Footnote 5 The two most common approaches to an unknown chemical are to apply the strictest engineering controls meant for protection from high health severity chemicals, with the goal of limiting employee exposure to essentially zero; or to apply an approach that applies less strict engineering controls meant for protection from medium health severity chemicals.Footnote 15
In the first approach, an unknown chemical is assumed to have a high severity to employee health, while in the second approach, an unknown chemical is assumed to have a medium severity to employee health. The choice available to an employer between these two assumptions is indirectly influenced by the overall strictness of occupational health and safety legislation in the jurisdiction.
3.3 Limitations due to a possibility of underestimation of the risk to worker health
Another limitation of CB is that it can oversimplify the risks to worker health compared to an OEL.Footnote 21 As well, the lack of evidence-based scientific validation of control banding schemes compared to established OELs weakens the argument of control banding.Footnote 5
3.4 Limitations due to a lack of scientifically proven sampling methods
Lastly, conducting air sampling for an essentially unknown chemical presents technical challenges for accurately and precisely measuring the airborne concentration of the chemical. This technical challenge is due to a lack of specific scientifically proven air sampling and analysis methods for the chemical agent or agents in question. This is the case for diesel engine exhaust emissions (DEEE).Footnote 22
The hazard prevention program framework of the requirements of COHSR Part XIX should be used to address the limitations of control banding when implementing a CB scheme. COHSR section 19.7 explaining requirements for program evaluation, is especially important for CB.Footnote 17
4. Manufactured nanomaterials
Manufactured nanomaterials can also be called engineered nanoparticles, engineered nanomaterials, manufactured nanoparticles, nanomaterials or nanoparticles. Nanoparticles can be manufactured in a laboratory as a product or can be produced as a by-product of a chemical reaction, such as in diesel combustion. Examples of manufactured nanomaterials include titanium dioxide nanoparticles, carbon nanoparticles (carbon black), carbon nanotubes, carbon nanofibres, alumina, zinc oxide and silver nanoparticles.Footnote 4 Carbon black has an American Conference of Governmental Industrial Hygienists (ACGIH®) TLV® of 3 mg/m3, which is a measure of the mass of the substance per volume of air.Footnote 11 However, measuring a nanomaterial as a mass per volume concentration may lead to an underestimation of health effects since particle surface area and number of particles are a more relevant indicator for predicting health effects from exposure to nanomaterials than mass. Thus, more appropriate future OELs for nanomaterials should be in units of number of particles per volume.Footnote 4 Below, the CB Nanotool seeks to effectively address issues with assessing the health risks of nanomaterials.
Nanoparticles are particles of matter that have physical dimensions in the nanometre (nm) scale. Currently, with the above mentioned exception of carbon black, nanoparticles do not have established OELs. There are some on the horizon though, such as the United States National Institute for Occupational Safety and Health (NIOSH) recommended exposure limit (REL) for carbon nanotubes of 7 µg/m3.Footnote 23 Although an established OEL may exist for a chemical, it is not meant to be applied to particle sizes of that chemical in the ultrafine particle (UFP) range of less than 100 nm in size.Footnote 4 Thus, CB can effectively address this gap in occupational exposure research. For more information on manufactured nanoparticles, the ESDC Labour Program guideline document, Engineered nanoparticles: Health and safety considerations should be consulted.Footnote 4 Nanoparticles from diesel engine exhaust will be discussed in Section 5 of this guideline document.
4.1 Control banding applied to manufactured nanomaterials
In order for an employer to use control banding for a manufactured nanomaterial, the process outlined in Figure 1 must be followed. However, it is important to consider all aspects of the specific nanomaterial in question with respect to probability and severity. A specialized CB tool can be used to guide the CB process, such as the CB Nanotool.
4.2 CB Nanotool
CB Nanotool is a control banding tool designed for manufactured nanoparticles developed by Samuel Y. Paik, David M. Zalk and Paul Swuste. The semi-quantitative tool incorporates many weighted variables that each result in a score for that variable. The tool is broad enough to be applied to any pure nanomaterial of any shape and chemical composition. The scores for all applicable variables are added to result in a total risk score that falls into a range of scores of a specific risk level (RL) in a control banding table. CB Nanotool has four risk levels, each with corresponding recommended control measures.Footnote 15 The CB Nanotool 2.0 can be downloaded at the website.Footnote 15
4.2.1 CB Nanotool factors
Each severity factor is specific to the nanomaterial (NM) or parent material (PM). The parent material is the bulk or larger size particle version of the nanomaterial of interest.Footnote 15 The CB Nanotool uses 13 severity factors and 5 probability factors.Footnote 15 The values in brackets represent the number of points assigned.
Table 5. Severity factors
Number | Name | Assignment of points |
---|---|---|
1 | Surface chemistry | High (10), medium (5), low (0) or unknown (7.5) |
2 | Particle shape | long tubular/fibrous (10), irregular (5), compact/spherical (0) or unknown (7.5) |
3 | Particle diameter | 1-10 nm (10), 11-40 nm (5), 41-100 nm (0) or unknown (7.5) |
4 | Solubility | insoluble (10), soluble (5) or unknown (7.5) |
5 | Carcinogenicity | yes (7.5), no (0) or unknown (5.625) |
6 | Reproductive toxicity | yes (7.5), no (0) or unknown (5.625) |
7 | Mutagenicity | yes (7.5), no (0) or unknown (5.625) |
8 | Dermal toxicity | yes (7.5), no (0) or unknown (5.625) |
9 | PM OEL | 0-1 µg/m3 (10), 2-10 µg/m3 (5), 11-100 µg/m3 (2.5), > 100 µg/m3 (0) or unknown (7.5) |
10 | PM Carcinogenicity | yes (5), no (0) or unknown (3.75) |
11 | PM Reproductive toxicity | yes (5), no (0) or unknown (3.75) |
12 | PM Mutagenicity | yes (5), no (0) or unknown (3.75) |
13 | PM Dermal hazard potential | yes (5), no (0) or unknown (3.75) |
Table 6. Probability factors
Number | Name | Assignment of points |
---|---|---|
1 | Estimated amount of NM used during operation | >100 mg (25), 11-100 mg (12.5), 0-10 mg (6.25) or unknown (18.75) |
2 | Dustiness/mistiness | high (30), medium (15), low (7.5), none (0) or unknown (22.5) |
3 | Number of employees with similar exposure | >15 (15), 11-15 (10), 6-10 (5), 1-5 (0) or unknown (11.25) |
4 | Frequency of operation | daily (15), weekly (10), monthly (5), less than monthly (0) or unknown (11.25) |
5 | Duration of operation | >4 h (15), 1-4 h (10), 30-60 min (5), <30 min (0) or unknown (11.25) |
Table 7. CB Nanotool control bands
Probability | |||||
---|---|---|---|---|---|
Severity | Extremely unlikely (0-25) |
Less likely (26-50) |
Likely (51-75) |
Probable (76-100) |
|
Very high (76-100) |
RL 3 | RL 3 | RL 4 | RL 4 | |
High (51-75) |
RL 2 | RL 2 | RL 3 | RL 4 | |
Medium (26-50) |
RL 1 | RL 1 | RL 2 | RL 3 | |
Low (0-25) |
RL 1 | RL 1 | RL 1 | RL 2 |
RL: risk level
Control bands:
- RL 1: General ventilation
- RL 2: Fume hoods or local exhaust ventilation
- RL 3: Containment
- RL 4: Seek specialist advice
Note: Table 5, Table 6, and Table 7 were adapted from the Annals of Occupational Hygiene publication Application of a Pilot Control Banding Tool for Risk Level Assessment and Control of Nanoparticle ExposuresFootnote 15
4.2.2 Example of the CB Nanotool in use
In one process, carbon nanotubes are created in a chemical reaction when certain gases are passed through a horizontal tube furnace.Footnote 15 Nanoparticles are generated in a gaseous phase and then attach onto solid substrates in the tube furnace. The carbon nanotubes are fully attached to the substrates when they are removed from the tube furnace using forceps. The samples are then transferred into plastic containers for further characterization. Based on knowledge of the carbon nanotube characteristics and a thorough review of this process, the CB Nanotool indicated that the overall RL was RL 2.Footnote 15 The required engineering control, therefore, is a fume hood or local exhaust ventilation.
5. Diesel engine exhaust emissions
Diesel engine exhaust emissions (DEEE) are a complex mixture of hundreds of different compounds found as particulates, vapours and gases. This complex mixture is analogous to the complex mixture of chemicals that make up tobacco smoke as well as containing many of the same chemicals found in tobacco smoke.Footnote 24, Footnote 25 The specific chemical composition and particulate sizes of diesel exhaust differs depending on quality of fuel, engine type, fuel pump setting, workload demand, engine temperature and maintenance, and emission control system.Footnote 22
Diesel particulate matter (DPM) is the particulate component of DEEE, which includes diesel soot and aerosols such as ash particulates, elemental carbon, organic compounds including polycyclic aromatic hydrocarbons (PAHs), metallic abrasion particles, sulfates and silicates. Most diesel exhaust particles are tiny enough to be inhaled deep into the lungs where they pose significant risk to health. The DPM particle size distribution is mostly comprised of particles that have physical dimensions in the invisible sub-micrometre range of 100 nanometers (nm), also known as ultrafine particles (UFP) or PM0.1.Footnote 22
Gaseous compounds can include carbon monoxide, carbon dioxide, sulfur and nitrogen oxides, aldehydes (formaldehyde, acetaldehyde, acrolein), benzene and PAHs. Similar to diesel particulates, gases can be inhaled deep into the lungs.Footnote 26
The International Agency for Research on Cancer (IARC) classifies diesel engine exhaust as a Group 1 carcinogen, which means it has been confirmed as a human carcinogen.Footnote 27 This decision was on the basis of DEEE causing lung cancer. As well, weaker evidence is present for DEEE causing bladder cancer (IARC). According to CAREX Canada and many other experts, there is no safe level of exposure to DEEE.The International Agency for Research on Cancer (IARC) classifies diesel engine exhaust as a Group 1 carcinogen, which means it has been confirmed as a human carcinogen.27 This decision was on the basis of DEEE causing lung cancer. As well, weaker evidence is present for DEEE causing bladder cancer (IARC). According to CAREX Canada and many other experts, there is no safe level of exposure to DEEE.Footnote 26
As discussed in the Labour Program guideline document Control measures for diesel engine exhaust emissions in the work place, there is no scientific consensus on what components of diesel exhaust should be measured to accurately assess employee exposure and there is no established TLV®/OEL for DEEEs.Footnote 22 Consequently, a use of CB for DEEEs may not be the best option. Instead, other indicators discussed in the guideline document should be used to effectively evaluate the engineering and other control methods used to ensure full protection of employees.
6. Control banding applied to respirators
The Canadian Standard Association (CSA) technical subcommittee on bioaerosols for the selection of respiratory protection against bioaerosols has adapted the CB approach to tasks involving bioaerosols. The general procedure is to select an appropriate level of respiratory protection by combining ranges or bands representing three groups: the risk group, the generation rate and the control level. A control banding approach must be used for selection of respirators against bioaerosols with no established occupational exposure limits or in the absence of regulations or other guidelines, and must be used in conjunction with health and safety practices.Footnote 7
7. Use of safety data sheet information
According to the requirements of COHSR section 10.32, the employer shall obtain a supplier safety data sheet (SDS) for the hazardous product to be used in the workplace. SDS are important sources of health hazard information on workplace chemicals and must be consulted when implementing a CB scheme. This is especially the case for the HSE COSHH Essentials COSHH e-tool, which requires the risk phrases or hazard statements of the chemicals of interest found in the hazards identification section. If the substance or product is a liquid, then the boiling point must also be entered.Footnote 18 These pieces of information can be found on the SDS of the chemical agent. The risk phrases or hazard statements may only be available on the European version of the SDS.
In addition, several other safety data sheet sections can be helpful sources of information for control banding, including handling and storage, exposure controls/personal protection, and toxicological information. The LD50 and/or LC50 values in the toxicological information section can be used to inform the severity rating of the chemical.
7.1 Risk phrases
The list of risk phrases (also known as R-phrases) with associated codes are defined in Annex III of European Union Directive 67/548/EEC: Nature of special risks attributed to dangerous substances and preparations (PDF format, 166.95 KB).Footnote 28 These risk phrases are used internationally, not just in Europe, and there is an ongoing effort towards complete international harmonization. The system of risk phrases is currently being replaced by a system of hazard statements.
7.2 Hazard statements
Hazard statements form part of the requirements of the Globally Harmonized System (GHS) of Classification and Labelling of Chemicals. They are intended to form a set of standardized phrases with associated codes about the hazards of chemical substances and mixtures that can be consistently translated into different languages. An example of a hazard statement is H301: Toxic if swallowed.Footnote 29 As such, they serve the same purpose as risk phrases, which they are intended to replace. SDS meant for use in the European Union (EU) must contain health and safety warnings in the form of hazard statements in order to comply with Regulation (EC) No 1272/2008.Footnote 29 SDS in Canada, the United States and other countries may contain hazard statements in compliance with the GHS; however, different countries may not adopt all GHS requirements and may still accept the outdated term of material safety data sheet (MSDS) instead of SDS. If chemical hazard information on a manufacturer SDS or MSDS is not in the form of hazard statements, then the European version or version of the SDS from another country that contains hazard statements may be consulted to gain this information in the form of hazard statements.
7.3 REACH Regulation
Registration, Evaluation, Authorisation and Restriction of Chemicals (REACH) is an European Union (EU) regulation that regulates the production and use of chemical substances, and their potential impacts on both human health and the environment.Footnote 30 The aim of REACH is to improve the protection of human health and the environment by identification of the intrinsic properties of chemical substances.
The European Chemicals Agency (ECHA) is an agency of the EU which manages the technical, scientific and administrative aspects of the implementation of REACH.Footnote 31 The ECHA is the driving force among regulatory authorities in implementing the EU's chemicals legislation. The ECHA helps companies to comply with the legislation, advances the safe use of chemicals, provides information on chemicals and addresses chemicals of concern. It is located in Helsinki, Finland.Footnote 31
Although Canada is outside the jurisdiction of the ECHA, the ECHA website has useful resources and a database to search for additional technical information on new chemicals that may further inform a workplace CB initiative.Footnote 31 The safety data sheet for the chemical from the manufacturer must be consulted.
In Canada, a similar database to the ECHA chemical database is the Domestic Substances List (DSL).Footnote 32 The DSL is an inventory of approximately 23,000 substances manufactured in, imported into or used in Canada on a commercial scale. It is based on substances present in Canada, under certain conditions, between January 1, 1984 and December 31, 1986. The DSL is the sole standard against which a substance is judged to be "new" to Canada. With few exemptions, all substances not on this list are considered new and must be reported prior to importation or manufacture in order that they can be assessed to determine if they are toxic or could become toxic to the environment or human health.Footnote 32
It is crucial that notifiers determine whether the substance to be imported into or manufactured in Canada is listed on the DSL or on the Non-domestic Substances List (NDSL). Substances not appearing on the DSL are considered to be new to Canada and are subject to notification. Substances listed on the NDSL are subject to notification but with reduced information requirements.Footnote 32
8. Control banding example
The chemical agent amphetamine will be used for this CB example. It is a potent central nervous system stimulant, which at the present time does not have a readily available OEL, and it is neither a carcinogen nor a sensitizer. In the federal jurisdiction, a Canada Border Services Agency (CBSA) officer may encounter amphetamine by inspecting and opening a suspicious package.
The example provided below demonstrates how the control banding model can be used in a workplace to help an employer establish suitable control measures in order to reduce or eliminate employee exposure to the chemical in question.
Employer Z conducts a workplace hazard investigation to determine whether the amphetamine liquid used in their workplace poses an occupational exposure hazard and if it does, whether the hazard is adequately controlled. Employer Z hires a qualified person who conducts a risk assessment to determine the probability, severity, and risk of employee exposure to amphetamine. Amphetamine liquid is present in the workplace in quantities of millilitres (mL) and relatively only a few employees are at risk of exposure through respiratory, dermal, and oral routes. Another factor affecting a determination of the probability is a low probability of employee exposure. Thus, the qualified person appointed by Employer Z assigns a low probability in using the risk rating table (Table 1).
The SDS states that amphetamine is toxic with the following information:Footnote 33
- Signal word: Danger
- Hazard statement(s):
- H301: Toxic if swallowed.
- H311: Toxic in contact with skin.
The options for signal word are: Danger, Warning, or no signal word. Table 8 shows that the signal word or absence of a signal word is a very simplified version of the associated hazard statement.Footnote 34 Employer Z compares these hazard statements to other similar hazard statements within the same hazard class in order to determine a type of severity ranking.
Table 8. Amphetamine hazard statements and related hazard statements
Code |
Hazard statement |
Hazard class |
Signal word |
---|---|---|---|
H300 |
Fatal if swallowed |
Acute toxicity, oral |
Danger |
H301 |
Toxic if swallowed |
Acute toxicity, oral |
Danger |
H302 |
Harmful if swallowed |
Acute toxicity, oral |
Warning |
H303 |
May be harmful if swallowed |
Acute toxicity, oral |
n/a |
H310 |
Fatal in contact with skin |
Acute toxicity, dermal |
Danger |
H311 |
Toxic in contact with skin |
Acute toxicity, dermal |
Danger |
H312 |
Harmful in contact with skin |
Acute toxicity, dermal |
Warning |
H313 |
May be harmful in contact with skin |
Acute toxicity, dermal |
n/a |
Note: Table 8 was adapted from the Sigma-Aldrich® publication Hazard Statements Overview (PDF format, 155.06 KB)Footnote 34
Using Table 8, both hazard statements that apply to amphetamine are the second most severe hazard statements out of four options. These four hazard statements are similar to the Hazard Group column of Hazard Band C of Table 2, and therefore, hazard band C seems to be the most applicable choice.
Employer Z also uses the LD50 on the safety data sheet to further verify the severity rating of amphetamine with the below information: LD50 Intravenous - mouse - > 100 mg/kg.Footnote 33
Employer Z uses the CCOHS OSH Answers publication that explains LD50 and LC50 to assist in categorizing the toxicity of the amphetamine LD50.Footnote 14 A direct comparison of the intravenous mouse LD50 of greater than 100 mg/kg to the tables in the CCOHS publication cannot be made because intravenous LD50 information is missing from the tables. The two tables assist in verifying that amphetamine is “moderately” toxic, since its LD50 may fit in the third most toxic category out of six categories for both the Hodge and Sterner Scale table and the Gosselin, Smith and Hodge Scale table.Footnote 14
Next, Employer Z searches for “amphetamine” in the “Search for Chemicals” search box on the ECHA website home page, and the “Substance Information” results page states the following:Footnote 35
- GHS02: Flammable
- GHS06: Acute Toxicity
Danger! According to the classification provided by companies to ECHA, this substance is fatal if swallowed and is a flammable liquid and vapour.Footnote 35
The acute toxicity warning about amphetamine from the ECHA is consistent with the severity indicated by the hazard statements from the safety data sheet and the hazard band. As well, the warning about flammability is an important piece of information that is not disclosed on the safety data sheet and hazard band, but may not have a significant impact on the severity rating of amphetamine.
Using the information from the safety data sheet and ECHA, Employer Z assigns a medium severity in a risk rating using Table 1. The combination of a low probability with a medium severity in Table 1 results in a low risk rating.
Subsequently, Employer Z collaborates with the employees to use hazard band C with the probability factors, including the small amount of amphetamine used and supporting information to choose an appropriate control band using Table 3. CB 1 is selected because the amphetamine is used in small amounts and is moderately toxic. The control measure associated with CB 1 is good industrial hygiene practice and general ventilation. Employer Z now has completed the control banding process and can take steps in collaboration with the employees to implement new control measures suitable for the work process that will prevent employees from exposure to amphetamine [COHSR 10.5(a)(ii) and 10.5(b)]Footnote 17 After the new control measures are implemented, Employer Z assesses their effectiveness for reducing employee exposures to amphetamine present in the workplace to a level that is reasonably achievable.Footnote 17
8.1 COSHH e-tool example
Before implementing the controls of CB 1, Employer Z in collaboration with employees choose to cross-reference their control banding process results with the UK HSE COSHH e-tool that automatically recommends a control band based on the input of a few factorsFootnote 18
The COSHH e-tool requires the boiling point for liquids. According to the amphetamine safety data sheet, the initial boiling point and boiling range are 200 -203 °C at 1,013 hPa.33 Below are screenshots from the COSHH e-tool that summarize how Employer Z used the tool for their amphetamine process.
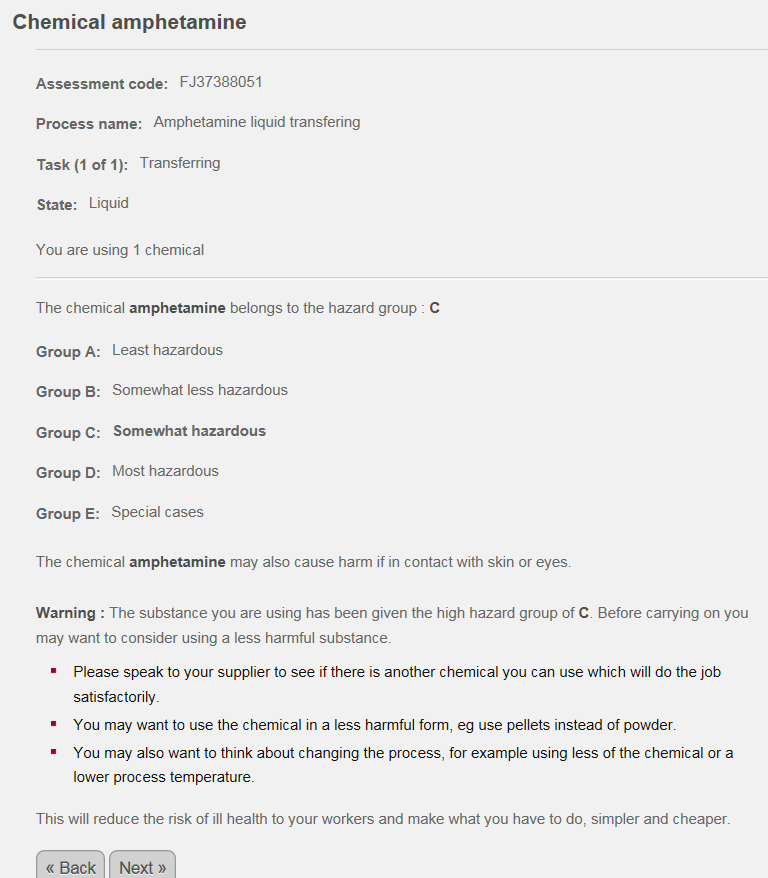
Figure 2 shows the screen ot the Chemical amphetamine. The COSHH e-tool places this amphetamine process in the hazard group C based on the two inputted hazard statements, H301: Toxic if swallowed and H311: Toxic in contact with skin. This is the same result found during the previous control banding process, where hazard band C was chosen. However, this is not the recommended control band, which will be assigned at the end of the COSHH e-tool process.
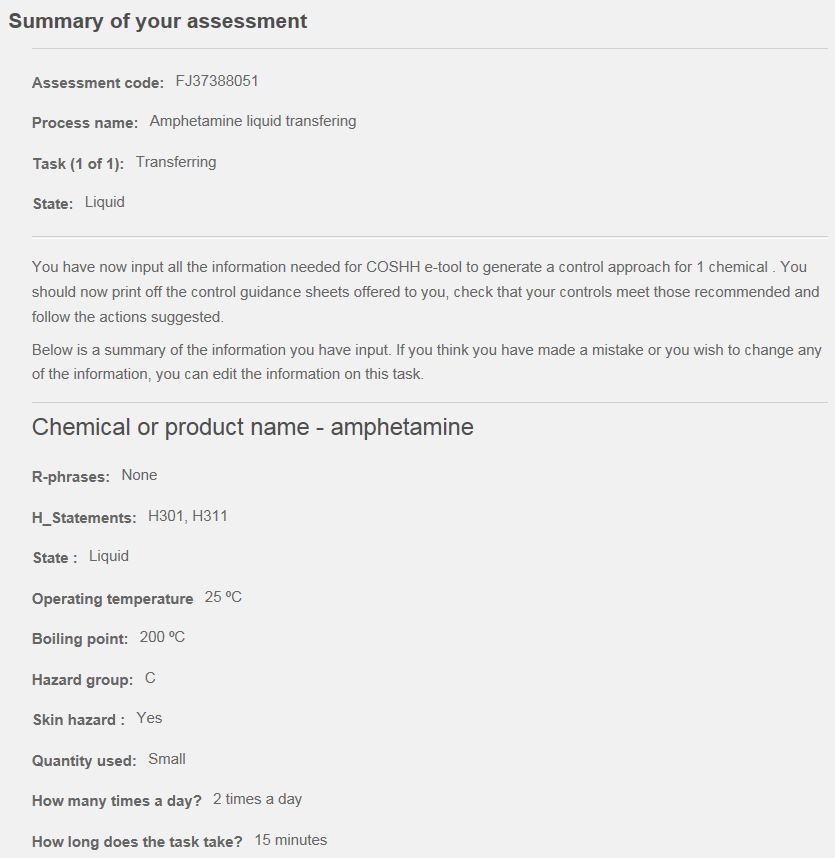
Figure 3 shows the screen of a summary of all inputted information that was required by the COSHH e-tool as well as the assigned hazard group (or hazard band). The frequency per day and length of time the task takes must also be inputted into the COSHH e-tool when prompted.
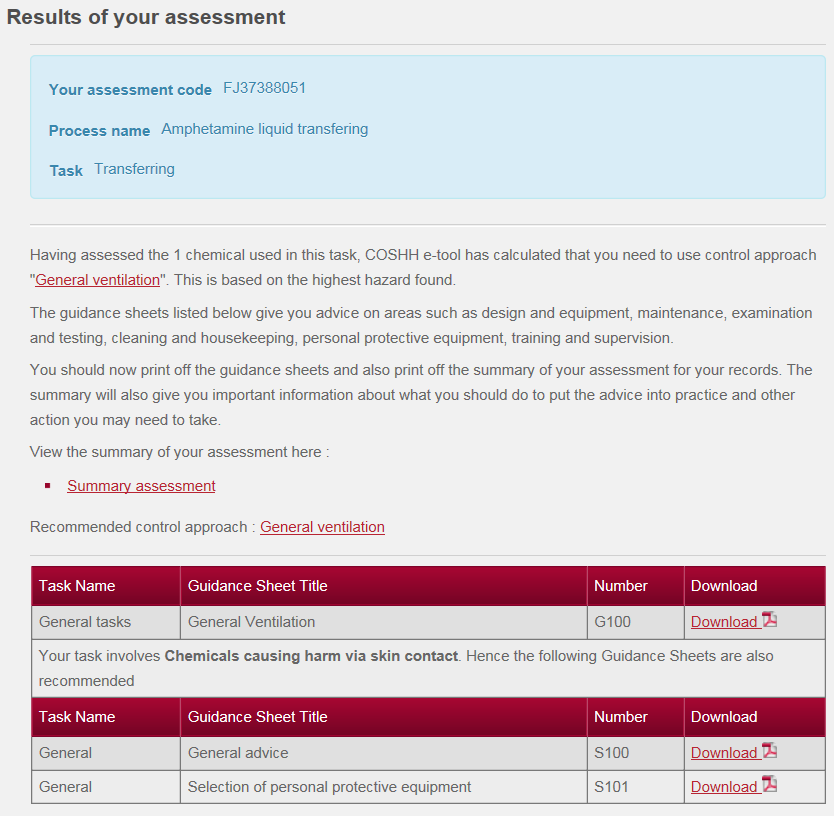
Figure 4 shows the Results of you assessment screen. This figure shows that the COSHH e-tool recommends general ventilation as a control approach for the amphetamine process, as well as personal protective equipment to prevent employees from skin exposure. Several guidance documents that describe these controls in more detail are provided. This result is the equivalent of a CB 1 in Table 4, and therefore, the same as control band 1 that resulted from the previous CB process using Table 2, Table 3, and Table 4.
In conclusion, Employer Z has completed the control banding process to establish the most appropriate control measures for the small amount of amphetamine in their workplace. They can proceed with the installation of a new general ventilation system or verification of the existing general ventilation system in the workplace. Employer Z will also provide the affected employees with suitable personal protection equipment to prevent employee skin absorption during handling of amphetamine.
Page details
- Date modified: