Caring for basketry and plant materials
Janet Mason
Caring for basketry and plant materials is part of CCI’s Preventive conservation guidelines for collections online resource. This section presents key aspects of managing the preservation of basketry and plant materials in heritage collections based on the principles of preventive conservation and risk management.
Table of contents
List of abbreviations and symbols
Abbreviations
- CCI
- Canadian Conservation Institute
- HEPA
- high efficiency particulate air
- IPM
- integrated pest management
- portable document format
- MOA
- Museum of Anthropology
- RH
- relative humidity
- UBC
- University of British Columbia
- UV
- ultraviolet
Symbols
- cm
- centimetre
- in.
- inch
Understanding basketry and plant materials
Plant materials originating from grasses, shrubs and trees (such as straw, stems, thin branches, leaves, roots, bark and wood splints) are often woven or intertwined into structures that form decorative or utilitarian objects such as baskets, hats, mats and bags. Some objects can be small, finely assembled and decorative; others may be robustly constructed to withstand hard use or heavy loads, such as a wood splint basket for carrying fruit crops or a woven cane chair seat. Basketry is usually defined as objects made by a two- or three-dimensional interworking of long plant fibres of a larger diameter than textile fibres. Objects made of bark sheets (e.g. birchbark) that are stitched together will also be considered here.
Common plant materials
Unlike cells in animal tissue, plant cells have a cell wall that makes them rigid and provides structural support. Major constituents of cell walls are cellulose, hemicellulose and pectin. Cellulose, a long-chain carbohydrate polymer, provides mechanical strength. Hemicellulose surrounds cellulose but does not chemically bond with it. Pectin forms a gel-like matrix that protects the cellulose and aids flexibility. Plants that grow on land also contain lignin, which provides rigidity and stiffness to the structure. Other polymers such as suberin and cutin may also be present in plant cell walls.
Plant materials have a great ability to absorb and desorb water, thus causing them to swell and shrink. New cellulose-based materials are flexible when wet or when exposed to high humidity; they can therefore be woven or interworked into complex shapes that become stiffer upon drying.
General categories of common plant materials used to construct objects are outlined below.
Bark
Bark describes the outer layers of stems, branches and roots of woody plants. The outermost tissue of a tree is composed mostly of dead tissues called “cork cells” that contain suberin, a fatty and waxy substance that makes the outer bark more resistant to water and microbial action.
Bark also contains lenticels that function as pores on the living tree and allow the exchange of gases. They can appear as light or dark lines or spots and can be used as an identification aid (Figure 1).
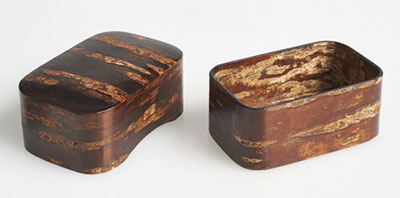
© Government of Canada, Canadian Conservation Institute. CCI 126827-0028
Figure 1. Lenticels in the cherry bark of the box and lid appear as mottled light lines.
Birchbark (bark from Betula papyrifera, known as white, paper or canoe birch) is commonly used by several Indigenous communities in Canada to make objects such as open containers, boxes, cradles, scrolls with pictograms, decorative ornaments (bark biting) as well as covers for shelters and canoe frames. Birchbark is collected in the winter or summer, but the winter bark is usually sturdier and thicker and is also darker coloured, usually orange-red to dark brown. The dark layer can be partially removed to create decorative designs (Figure 2). The bark is easier to remove in early summer when the sap is flowing, but if peeled from the tree in hot weather, the bark can separate into thin layers (Adney and Chapelle). Prior to use, the bark is usually submerged in water to make it more pliable and therefore easier to shape. Birchbark is naturally resistant to decay and is waterproof. Well-stitched and caulked birchbark can be made into containers that hold water or into leak-free canoes that float on water (Figure 3).
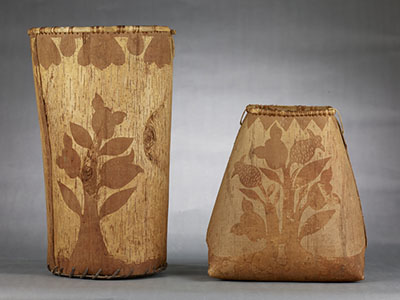
© Government of Canada, Canadian Conservation Institute. CCI 126702-0297
Figure 2. Two birchbark containers with designs created by partial removal of the darker layer of bark.
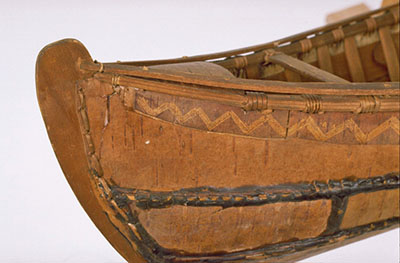
© Government of Canada, Canadian Conservation Institute. CCI 73692-0177
Figure 3. A small model birchbark canoe with a design scratched into the bark and caulking applied to the seam lines of the stitched panels.
Some barks are fibrous, such as what is commonly called “cedar bark” (Figure 4), which is inner bark of the western red-cedar (Thuja plicata) or the yellow cedar (Cupressus nootkatensis). On a living tree, the outermost layers of inner bark cells die progressively, forming a protective layer. As cells behind the protective layer die and the diameter of the tree trunk increases, the outermost layer shreds off. When traditionally harvested for use, a long strip of bark is pulled off the tree, the rough outer surface is removed and the inner bark is dried. Strips are woven or otherwise interworked to create baskets, mats, hats, garments (Figures 5a and 5b) and cordage. They are also used as strands attached to objects such as Northwest Coast masks.
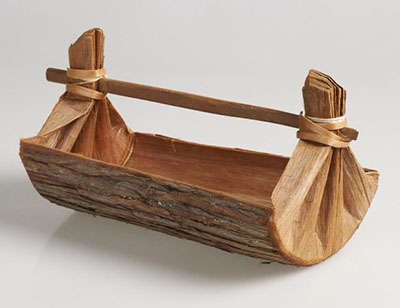
© Government of Canada, Canadian Conservation Institute. CCI 126827-0021
Figure 4. The basket is made of a rectangular piece of western red-cedar bark. The outermost layer of bark was removed from each end, and the inner bark was folded and gathered and then tied to a stick that serves as a handle.
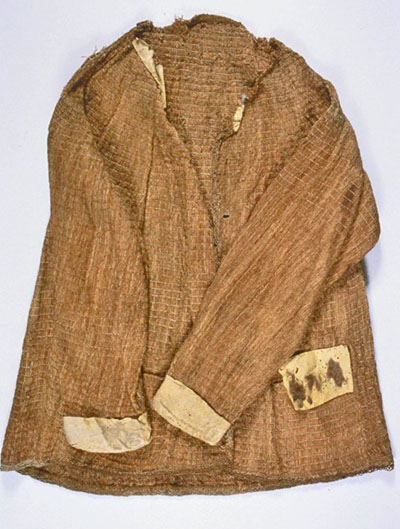
© Government of Canada, Canadian Conservation Institute. CCI 2004933-0001
Figure 5a. A jacket made of cedar bark (probably yellow cedar). This object belongs to the Canadian Museum of History (accession number: VII-X-58B).
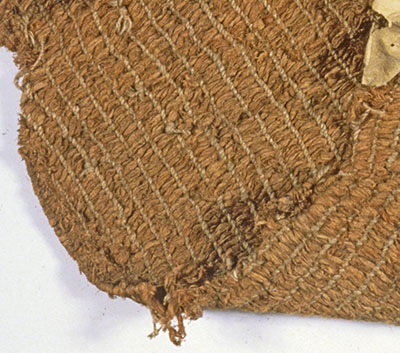
© Government of Canada, Canadian Conservation Institute. CCI 2004933-0003
Figure 5b. Detail of stitched cedar bark used to create a jacket.
Root
Root is used as a lashing and binding material and can be woven into intricate objects (Figure 6). Spruce root in particular is often used by Indigenous peoples of Canada; western red-cedar, pine and other tree roots are also used. Roots have the same basic cells as those found in the tree stem, but the cell walls are thinner and the tissue is more porous. Young and tough roots from mature spruce trees are excavated in the spring, when the bark is easier to remove. Soon after collecting the root, its bark is removed, exposing a smooth surface with a satin lustre. Roots are split and then dried to prevent the growth of mould on them. Prior to use, the root is soaked in water until it becomes flexible.
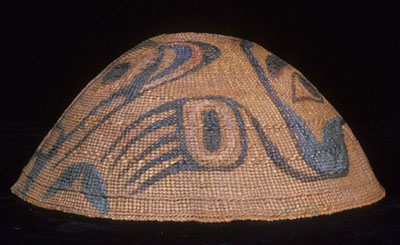
© Government of Canada, Canadian Conservation Institute. CCI 2004829-0001
Figure 6. A Nootka hat made of twined root, possibly spruce, with a painted design. This object belongs to the Canadian Museum of History (accession number: VII-F-807).
Wood splint
Varieties of young hardwoods (e.g. maple, ash, white oak) are split to produce thin, flat and flexible splints that are used to make various objects. One method is to cut a log and beat it until strips can be removed along the growth rings. The strips can be thinned and smoothed, made to the desired width and then used to create the object (Figure 7).
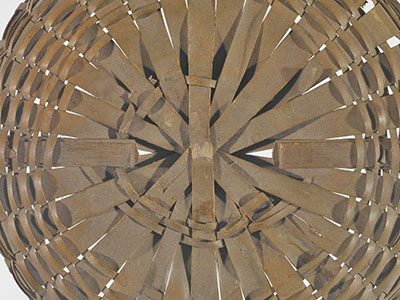
© Government of Canada, Canadian Conservation Institute. CCI 125773-0032
Figure 7. Wood splints were used to create this basket lid.
Leaves, stems and grasses
Many types of grasses, leaves and stems have been used to make or decorate baskets (Figure 8), hats, handbags, mats and other objects, as well as to make cordage. Some grasses and stems may be delicate, such as the maidenhair fern stem primarily used as a decorative element, or very strong and rigid, such as bamboo or rattan. Grasses characteristically have no, or very little, xylem (woody tissues) and have hollow stem interiors. Many have a long thin structure and can be easily worked, but they tend not to be as durable as woody tissues. The grasses are collected at the desired size and, depending on the type of plant, they may receive some treatment prior to their careful drying. Drying in the shade preserves their colour, while drying with some sun exposure will bleach and lighten colours.
Long strong leaves or husks (Figure 9) can also be used, such as leaves of corn, palm and raffia.
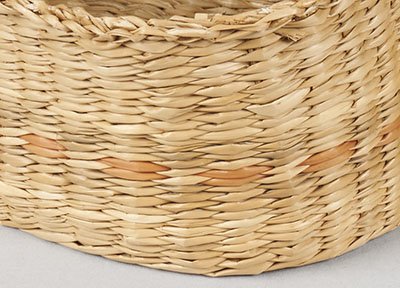
© Government of Canada, Canadian Conservation Institute. CCI 126827-0016
Figure 8. Detail of a basket made of grass stems.
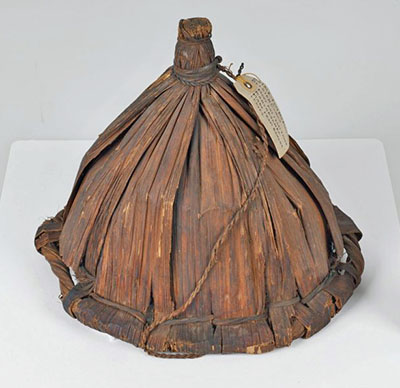
© Government of Canada, Canadian Conservation Institute. CCI 121103-0025
Figure 9. An African man’s hat, probably made of husks.
Cane
Cane usually refers to strips of the outer, shiny skin of rattan, a term used to describe several climbing palms of tropical Asia that have long, tough, slender stems. Cane is used to make chair seats or backs in a weaving pattern known as caning. “Cane” and “reed” are commonly used terms to refer to various grasses and reed species with a long, thin stem, many of which are used in basketry.
Wicker
Wicker is used to describe the stems or slender branches, either whole or split, of more than twenty types of immature willow. It is used to make relatively sturdy interworked objects (baskets, furniture, etc.) and is associated with a distinct weaving style called wicker or wickerwork. Wicker is also used as a more generic term to describe any whole or split basketry element that is sturdy, made from other plant species.
Preparation of plant materials
Plant parts are collected at certain times of the year and at specific growth stages in order to ensure that the parts will be supple and strong when dried. Drying must be carried out with care to prevent mould growth during storage. They can be prepared for use by being soaked in water of various temperatures. Controlled soaking increases flexibility and allows the removal of some plant components such as starches, sap or gums.
Dyes
Some plant parts can be readily dyed, but other parts may not allow good penetration of the dye. Barks, flowers and other plant parts have been used to colour plant materials for woven objects, although in the recent past, craftspeople and artists have turned to synthetic dyes.
An ancient dyeing technique to attain dark-coloured organic materials was to soak the material in a tannin-rich bath of barks and twigs, followed by soaking in an iron-rich solution such as water in an iron pot or with iron shavings or nails added, or immersion in iron-rich mud. Chemically, the iron acts as a mordant in the dyeing process and binds to the plant material. Depending on the barks and twigs used in the initial bath, the resulting materials may be black or very dark tones of brown, sometimes with a hint of olive green. But iron also has the ability to act as a catalyst for some chemical reactions; notably, it can catalyze cellulose degradation mechanisms. Thus, such black-dyed plant materials are particularly prone to damage and losses, because the iron bound to the fibres actively causes their degradation (Figures 10a and 10b). When a material deteriorates at a significantly accelerated rate due to internal compounds used in its manufacture, it is sometimes described as suffering from an inherent vice.
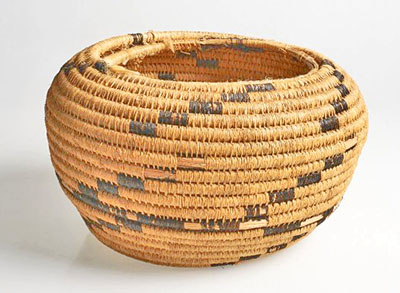
© Government of Canada, Canadian Conservation Institute. CCI 126827-0020
Figure 10a. A coiled basket with a foundation of bundled plant material.

© Government of Canada, Canadian Conservation Institute. CCI 126827-0019
Figure 10b. Detail of the coiled basket. Dark-coloured stitches that connect the coils are more brittle and weaker than the light-coloured stitches made of the same plant fibre, and much of the dark material has been lost. The dark fibres were most likely dyed using iron in the process. The iron within the fibres causes them to actively degrade.
Basketry construction techniques
Many basketry constructions are made of passive elements (spokes, stakes or staves, similar to warps in textiles), which form the structure’s foundation or base, and active or mobile elements (weavers, similar to wefts in textiles), which are actively interworked around the passive ones in a variety of ways. Three basic construction techniques are used: coiling, twining and plaiting (similar to weaving in textiles). Each basic technique can have many variations.
Coiling
A foundation material (one or several rods, or bundles of smaller plant materials) is coiled to create the shape of the object, and the coils are secured in place with stitches. Some foundations may be pierced through, or the stitches can bind one coil to another by using several connecting techniques. The stitching materials are the active materials, so they are usually more flexible than the passive foundation materials. Stitches can create decorative patterns (Figure 10a), as does varying the size of the foundation and the spacing of the coils.
For decorative purposes, different stitching materials and techniques can be used to create patterns, or a different material can be laid against the foundation and held in place with stitches. A technique called “imbrication” (overlap) is also used, where a strip of a decorative material is applied to the exterior side along a coil row. The strip is interlocked into the structure by inserting a fold under a stitch element; then, the stitch is pulled tight to wedge it securely in place. The strip is brought back over the stitch, where it is folded again and held in place by wedging it under the next stitch element (Figure 11a). The application continues so as to create the desired design (Figure 11b). Decorative patterns can be produced by having the overlay hidden along the coil behind several stitch elements for a certain length and then having it reappear further along by bringing it forward above the stitch element.
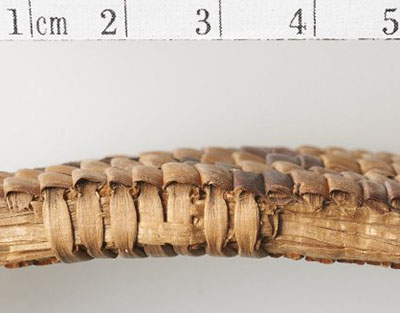
© Government of Canada, Canadian Conservation Institute. CCI 126827-0032
Figure 11a. Detail of a broken coiled basket shows the stitches (vertical axis) that held the coils (horizontal axis) together. The band along the top is decorative imbrication made from folded strips of bark bound to the coil while the basket was constructed.
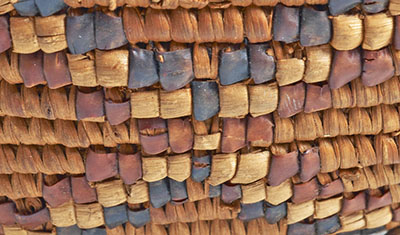
© Government of Canada, Canadian Conservation Institute. CCI 126827-0027
Figure 11b. Detail of a basket with an X-shaped pattern created with imbrication of beige, black and red-brown bark strips over a backdrop of brown stitch elements.
Twining
In twined basket construction, the vertical elements (stakes or warps) are passive and the horizontal elements (weavers or wefts) are active. Usually, two weft elements are used together—one element comes to the front of the work as the other goes to the back, and they go over and under each other to produce an intertwining. If the same warps are used for each row, it is identified as simple or plain twining; if the engaged warps are offset, a diagonal (twill) effect will be created. Wrapped twining involves the use of elements perpendicular to one another, held together with a flexible twining element. Figures 12a and 12b show how, row by row, flexible wefts secure together the areas where the two other stiff strands meet. Some twined basketry has warps that cross each other diagonally; the weft is worked in along the rows where the warps cross.

© Government of Canada, Canadian Conservation Institute. CCI 73988-0015
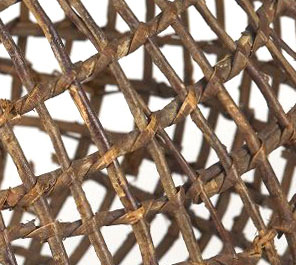
© Government of Canada, Canadian Conservation Institute. CCI 73988-0015
Figures 12a and 12b. The crab trap (left) is made with two stiff elements held together with the wrapping of a more flexible material (right). This object belongs to the Museum of Anthropology at the University of British Columbia (accession number: A2191).
False embroidery is used in plain twining as a method of structural decoration. A decorative material (e.g. grass stems, porcupine quills) is wound around the exterior weft so that the design shows only on the exterior side. The decorative material slants in the opposite direction to the weft (Figure 13). Designs can also be made with a material that overlays the weft, and if a half twist is made as it passes behind the warp, the pattern can be seen on the exterior and interior surfaces (Figure 14).
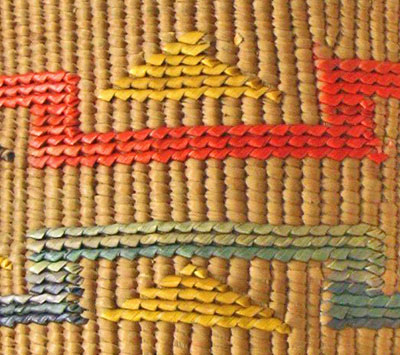
© Government of Canada, Canadian Conservation Institute. CCI 124825-0018
Figure 13. Detail of a twined basket with false embroidery. The colourful porcupine quills are slanted in the opposite direction to the light brown basketry weft strand.
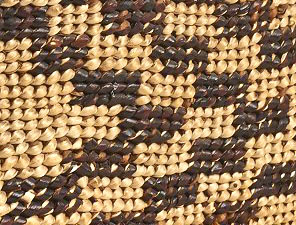
© Government of Canada, Canadian Conservation Institute. CCI 126389-0016
Figure 14. Detail of a twined basket with an overlay. The overlay has the same slant as the weft.
Plaiting
In plaited basketry, there are no distinct warp and weft elements: all elements are active and are often of the same size. Simple (checkerwork) plaiting is over-one, under-one in both directions; diagonal (twill) patterns can also be created.
Wickerwork
Wickerwork consists of strong interworked constructions suitable for using strands of wicker (slender branches of willow) to create objects such as sturdy baskets and furniture. Wicker is the traditional material of choice for these types of constructions, but other strong materials such as cane can be similarly used. Because the materials are more rigid, both horizontal and vertical elements may move within the structure. The wefts do not cross other wefts in a given row.
Splintwork
Wooden splints of various width are woven, usually using plaiting techniques. Additional thin strips can be added to the weft and twisted to create a decorative structure that projects out from the basket (Figure 15). The rim of the basket may also be reinforced with a separate hoop, possibly of carved wood, that is lashed to it.
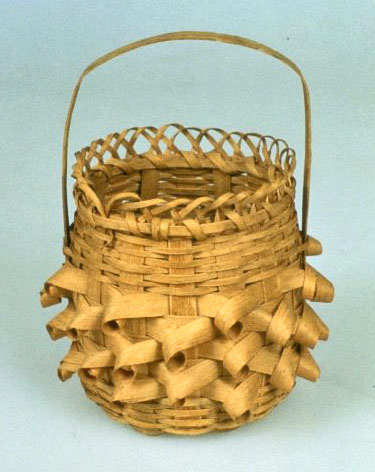
© Government of Canada, Canadian Conservation Institute. CCI 2000404-0001
Figure 15. The splint basket has a decorative element woven into the structure that is twisted and that extends out from the exterior basket wall. This object belongs to the Canadian Museum of History (accession number: III-I-211).
Sheets of bark
Birchbark can be used as a single piece, cut or folded to create the desired shape and then stitched together (Figure 16). The bark sheet side that originally was facing the tree trunk is usually placed to face the exterior side of the object. The bark can also be cut in strips and plaited. Birchbark can be the foundation for quill decoration (Figures 16 and 17).
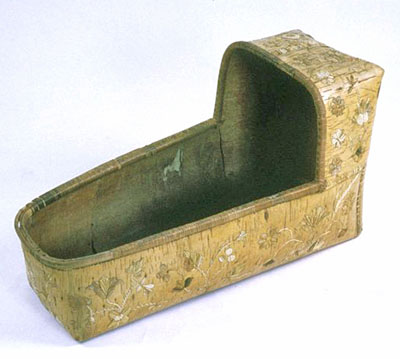
© Government of Canada, Canadian Conservation Institute. CCI 2003712-0001
Figure 16. Birchbark was cut, folded and stitched to create a cradle. This object belongs to the Canadian Museum of History (accession number: III-G-1178).
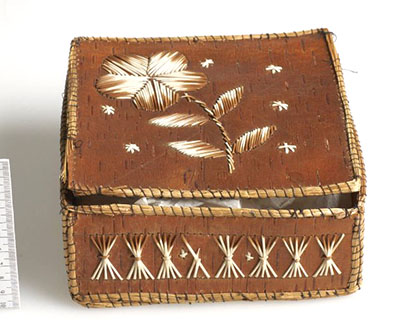
© Government of Canada, Canadian Conservation Institute. CCI 126827-0023
Figure 17. The birchbark box has been decorated with undyed porcupine quills. The edges are most likely sweetgrass stitched on with black thread.
Causes of damage to basketry and plant materials and preventive conservation strategies
Twined, plaited or coiled objects made from plant fibres and those made of bark sheets can be very fragile and are generally susceptible to the following agents of deterioration: physical forces, fire, water, pests, pollutants, light, incorrect temperature and incorrect relative humidity (RH). These agents tend not to work in isolation. Deterioration from light, heat and high or low RH will contribute to a more fragile condition that can easily lead to damage through physical force. Certain pollutants can accelerate damage with increased temperature and humidity. The extent of brittleness and fragility will depend greatly on the type of plant material used: tough and thicker plant materials like birchbark and root tend to be more resistant than more fragile structures like thin strips of fine grasses or weaker materials, such as cedar bark. This section discusses how these agents affect plant materials and presents general strategies for preventing or reducing damage to objects made of such materials.
Physical forces
Of the 10 agents of deterioration, physical forces are by far the most prevalent source of damage. These can often be linked to a weakened structure due to prior use before the object was collected, or it may be due to poor handling and storage practices once the object is part of a collection.
Some methods of construction can also physically stress the materials, which can lead to damage (Figure 18).
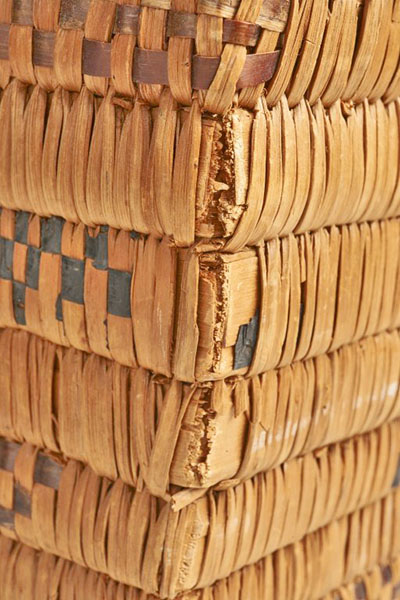
© Government of Canada, Canadian Conservation Institute. CCI 126827-0030
Figure 18. The wood slats that make up the foundation of the rectangular basket were folded at the corners at a 90° angle, and the wood broke at the outside edge.
The points where a flexible area of a structure meets a more rigid area may be a place of weakness, such as some basket rims or bases (Figure 19), or perimeters of cane chair seats where the cane meets the wooden frame. Structures are stressed where the movement of elements are halted. A mat of simple plaiting can withstand some stress because the elements are not attached to one another and can move independently as stress is applied. On coiled structures, the active elements (weft) usually break first, creating breaks in line with the foundation bundles. Twined baskets can break along the warp or weft (Figure 20) and, often, along both. Decorative elements such as imbrication on coiled baskets or false embroidery on twined baskets could become loose or also break.
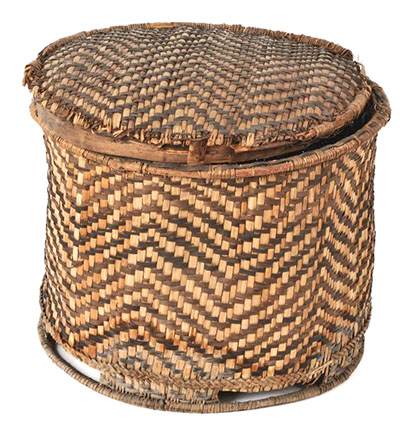
© Government of Canada, Canadian Conservation Institute. CCI 121103-0035
Figure 19. The rim of the lid on this African basket is damaged where the flexible woven structure meets the stiff wooden hoop.
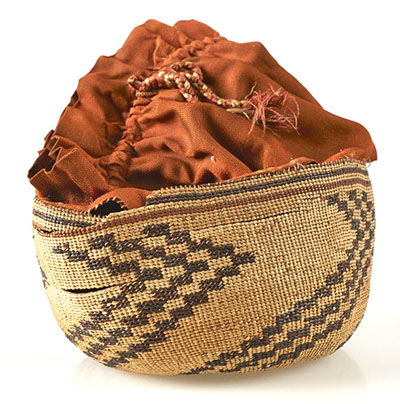
© Government of Canada, Canadian Conservation Institute. CCI 126389-0014
Figure 20. This twined basket made of spruce or cedar root, with an overlay of darkly-dyed fern stems or grasses, is broken in a few areas along a row of wefts and has breaks to both the warp and wefts near the rim area where a fabric inner pouch is attached.
Handles, rims of baskets or attached bases are very susceptible to damage, as these areas are usually weakened from having suffered repeated strain when the object was in use (Figures 21 and 22).
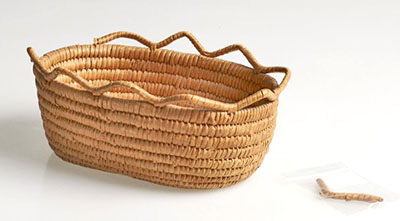
© Government of Canada, Canadian Conservation Institute. CCI 126827-0022
Figure 21. A decorative wave-like rim is attached with only a few stitches along the top of the oval basket. The rim broke at two points of attachment.
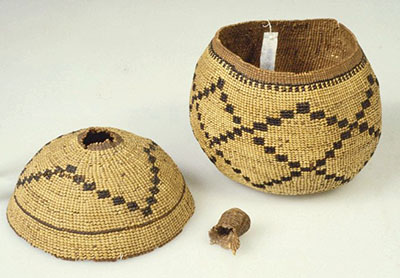
© Government of Canada, Canadian Conservation Institute. CCI 2005291-0001
Figure 22. A knob that was woven as part of the structure of the basket lid has broken off.
Other possible areas of weakness are cordage, thread or lashings of plant fibres used to bind or connect components (Figure 23). The threading or binding materials undergo stresses when the structure gets flexed, which often happens when the object is moved. The further an element extends outwards from the plane of the woven structure, the more vulnerable it becomes to damage. For example, decorative loops found in some splintwork are easily damaged (Figure 24). False embroidery and overlay decorations stick out slightly from the surface and, as such, are more prone to snagging.
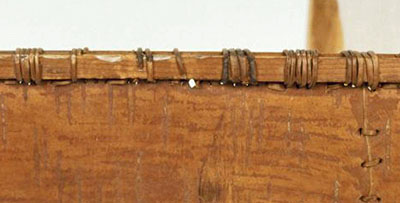
© Government of Canada, Canadian Conservation Institute. CCI 73692-0286
Figure 23. Detail of the gunwale on a canoe model. The root used to bind the birchbark to a wood strip is broken, and sections are missing.
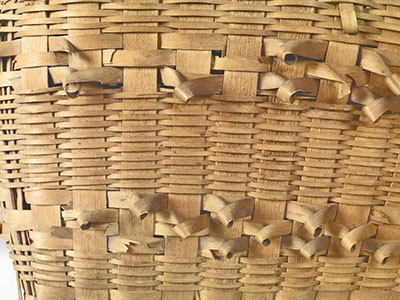
© Government of Canada, Canadian Conservation Institute. CCI 125773-0029
Figure 24. Some of the periwinkle-shaped wood splint decorative loops on the basket are damaged.
Fringes, such as those made of cedar bark on some Northwest Coast masks (Figure 25), hang freely without any support and are thus susceptible to physical damage and losses. Aged cedar bark is quite fragile and brittle, so even slight movement can cause thin strands to break and fall off.
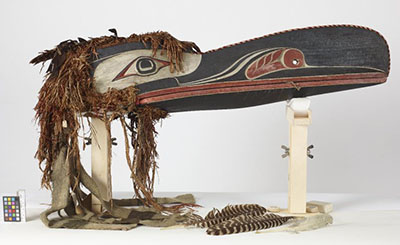
© Government of Canada, Canadian Conservation Institute. CCI 126379-0017
Figure 25. A Kwakwaka’wakw dance mask with red-cedar bark fringes.
Hollow structures, such as baskets or hats, are vulnerable because they have no inner support to absorb or withstand applied force. As materials become more brittle and fragile, forces will cause increasing damage. Once fractured, the structure becomes more vulnerable and the potential for additional breakage and loss increases.
Gravity can slowly deform flexible plant materials. Woven structures can become misshapen from lack of support, especially if exposed to high humidity. In addition, plant materials, especially older ones, cannot withstand folding and may break along the fold line (Figure 26).
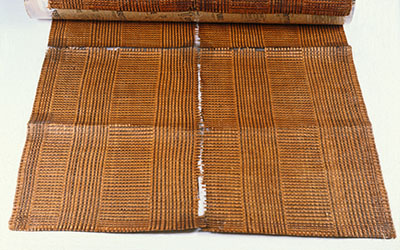
© Government of Canada, Canadian Conservation Institute. CCI 1000625-0001
Figure 26. A mat made of cedar bark was folded in storage and eventually broke or became distorted at fold lines. This object belongs to the Canadian Museum of History (accession number: VII-E-385).
Crowding in storage poses a high risk of distorting or even breaking basketry structures. It may also cause surface damage and abrasions that can affect their appearance, especially if it alters decorative elements, such as overlay decorations or scraped designs on birchbark. Stacking baskets one inside the other may save storage space, but it can also result in distortion and abrasion, and it prevents easy access to the inner objects.
Recommendations
- Provide enough space on shelving units for each object. This makes it easier to find an object, examine it and handle it. Follow good handling practices. Ensure that nothing will bump into or snag on elements that project out from the surface.
- Pad interiors of flexible baskets to maintain the shape, without overstuffing. Use soft materials that will not snag inner elements—crumpled archival tissue or a set of small polyethylene foam pieces covered with fabric or with a soft polyethylene non-woven sheet (Figures 27a and 27b). One can also insert a bag made of fabric, of polyethylene plastic or of polyethylene non-woven sheet (Tyvek) and gradually pad it out with polyester fibrefill. Ensure that distortions that indicate original use of the object are retained.
- Provide outer support around objects (Figure 27c). Outer supports can be made by cutting a recess for the basket into a block of polyethylene foam and lining it with thin foam, fabric or a non-woven sheet (Tyvek). Such supports are most needed for baskets with a small diameter base but larger diameter walls. Another option is to form rings, for example using fabric or medical stockinette (knit cotton, polyester or a blend) filled with polyester fibrefill, or using polyethylene foam pipe insulation made into a ring by stitching the ends together with twill tape or a dab of hot-melt glue.
- Enclose fragile or delicate objects in archival boxes or in plastic containers (Figures 27c and 27d). If there is more than one object per box, separate the objects with a protective layer of thin foam. On the exterior of the boxes and containers, indicate the objects’ accession numbers and apply images of the objects so that they are not handled unnecessarily.
- Larger or heavier objects such as a bark-covered canoe may need several supports placed at strategic points. Consider the use of carved rigid foam, shaped and padded wood or adjustable slings. (For a description of an adjustable sling, consult R.L. Barclay 1988.)
- Tie loose or broken elements to the object with soft fabric tape. Do not use tapes with adhesive (Figure 28).
- Baskets should not be stacked one inside the other, even if their condition is considered good. Stacking is suitable for flat objects (e.g. mats and tapa sheets) if there is an interleaf of archival tissue or lightweight paper between each object. The bottom object must be able to tolerate the weight load.
- Store flat objects in narrow drawer cabinets or archival boxes. Roll oversized objects on large diameter tubes to reduce the space needed for storage and to facilitate handling and movement. Note that the tubes should first be covered with Mylar or polyethylene sheeting then wrapped with unbuffered acid-free tissue paper or prewashed cotton sheeting. For further information on rolled storage, consult CCI Note 13/3 Rolled Storage for Textiles.
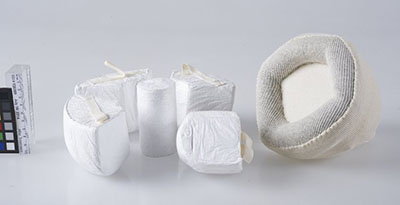
© Government of Canada, Canadian Conservation Institute. CCI 126389-0035
Figure 27a. A breakaway support is useful when a basket’s opening is narrower than the girth of its wall. Each piece of this support can be assembled together, one by one, within the basket. The five pieces on the left, which create the bottom part of the support, are made of polyethylene foam covered with polyethylene non-woven (Tyvek) sheeting and are topped with stitched Velcro strips that latch onto the jersey knit on the top support element, shown on the right.
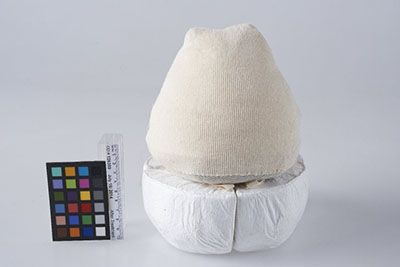
© Government of Canada, Canadian Conservation Institute. CCI 126389-0034
Figure 27b. The assembled inner support. The top cone-shaped support element is made of a soft cotton jersey filled with polyester fibrefill.
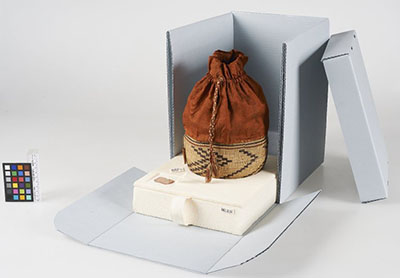
© Government of Canada, Canadian Conservation Institute. CCI 126389-0039
Figure 27c. Basket with an inner pouch attached at its rim, after treatment (consult Figure 20 for a view of the basket before treatment). The internal support (shown in Figure 27b) was assembled inside the basket. The basket sits in a curved recess cut into a polyester foam base that is lined with cotton jersey. The box’s lid is shown on the right.

© Government of Canada, Canadian Conservation Institute. CCI 126389-0038
Figure 27d. The basket on the foam support has been slipped inside a cardboard box. One of the side panels on the box can fold down when the box is opened—a design that provides easy access to the box’s contents.
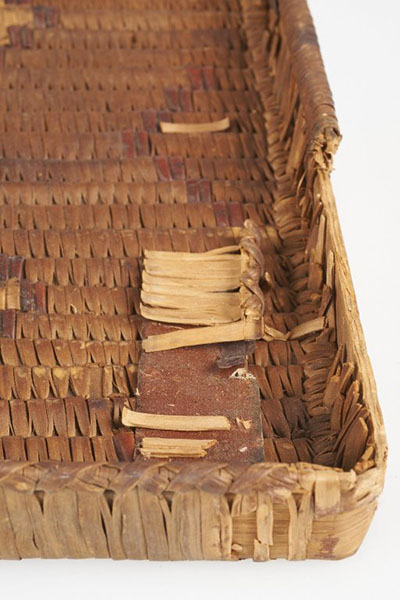
© Government of Canada, Canadian Conservation Institute. CCI 126827-0018
Figure 28. Damage caused by adhesive tape. An adhesive-backed tape had been used to secure broken basketry parts on a tray. At some point, there was an attempt to peel away the tape; instead, the adhered basketry elements broke off. Tape should never be used, as tape residues on objects are very difficult to remove and cause permanent stains.
Consult Handling heritage objects for further guidance on safe handling practices for heritage objects and collections.
Fire
Dry plant materials burn easily and quickly, even more so if the structure has an open weave and is made of thin or narrow materials. Birchbark objects, particularly those that are delaminating, are readily flammable.
Consult Agent of deterioration: fire for strategies on reducing fire risk and damage.
Water
When plant materials are soaked in water, their stiffness and strength are lowered. Deteriorated plant materials respond poorly to water: their weight increases while at the same time the materials become softer and weaker; therefore, tears and distortion easily occur. Plant materials in less deteriorated condition will react differently depending on the plant part (bark, grass, etc.) and its flexibility when moist. Thin and flexible fibres may become quite misshapen, but more rigid plant parts can be less affected. Furthermore, plant fibres are anisotropic, that is, they swell and shrink to different degrees depending on the fibre direction. This creates tensions when a woven structure is wet, and the finer elements, often the twined wefts or assembly stitches (e.g. holding a bottom to the walls), may rupture from the pressure of other swelling elements (often, the warps).
Plant materials often contain compounds that are soluble in water, some of which are produced as the materials degrade. Uneven wetting can result in the creation of light and dark patches as well as tide lines. A tide line is a line or ring of more intense, usually darker colour. Such a line or ring occurs when a liquid is applied and soluble materials are carried by wicking, then stop further along when the liquid starts to evaporate (Figures 29a and 29b). Also, colourants applied to dye fibres for decorative purposes may be soluble in water and thus bleed, staining other parts of the basket. More rarely, colourants may be washed off completely from the object.

© Government of Canada, Canadian Conservation Institute. CCI 121103-0176
Figure 29a. The interior of the basket’s base shows a darker circular tide line where water carried solubilized materials.
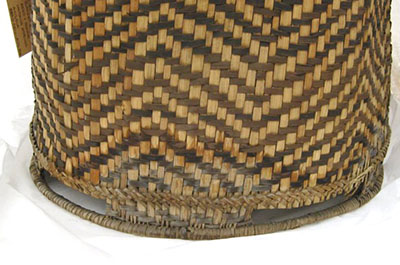
© Government of Canada, Canadian Conservation Institute. CCI 121103-0125
Figure 29b. A water stain on the exterior of the basket shown in figure 29a.
Recommendations
- Keep basketry and other objects made of plant materials away from water sources, such as water pipes or storage areas below washrooms.
- If objects made of plant materials do become wet, place them on a stiff board or tray and take them to a well-ventilated, drier area. If the structure is misshapen, pad it gently to shape using strips of thin foam, or a plastic bag filled with crumpled tissue paper, fibrefill or loose scraps of foam. After some drying has taken place, empty out and replace the plastic bag with loose crumpled tissue paper for further drying.
For further information on general issues concerning the risk of water damage and on the prevention of that risk, consult Agent of deterioration: water.
Pests
The most common insects that damage plant materials in collections within Canada are the cigarette beetle (Lasioderma serricorne) and the drugstore beetle (Stegobium paniceum). Insects hide well; often, insect activity is detected by finding particulate material generated from insect tunnelling that has collected on the object or on the display case or storage unit shelf around or against the object.
Rodents can gnaw plant materials and soil them with urine or excrement (Figure 30).
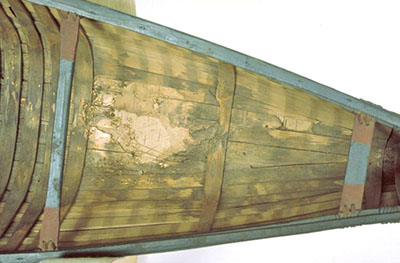
© Government of Canada, Canadian Conservation Institute. CCI 73692-0055
Figure 30. Inside structure of a small model of a birchbark canoe. Many wooden cross strips were gnawed by mice (only their pale outline remains against a darker background colour).
Recommendations
- Maintain good storage practices so objects can be easily accessed and seen.
- Design and maintain an integrated pest management (IPM) program.
- Bag and seal the object when insect activity is suspected. Isolate new acquisitions or loans so they can be observed for insect activity prior to integrating them in the collection.
- If insect activity on the object is confirmed, follow through with a method to kill any active insects.
For aids regarding pest identification and strategies to control pest damage, including IPM, consult:
Pollutants
Some stains or material remnants on utilitarian objects such as baskets may provide evidence of use and should be investigated. These materials are usually not removed.
Dust and dirt can accumulate on the intricate uneven surfaces of woven structures (Figure 31). Cleaning takes considerable time and can stress delicate materials and structures, especially if the dust or dirt has remained undisturbed for months or years. In the aftermath of a fire, soot deposits, which consist of fine particulates that can contain oily compounds, can also be very difficult to remove from the rough surface of interwoven plant fibres.
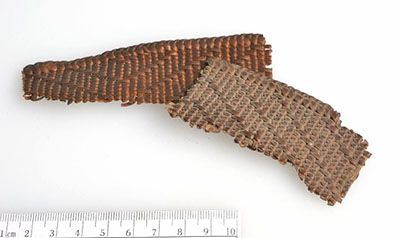
© Government of Canada, Canadian Conservation Institute. CCI 126827-0031
Figure 31. Dust deposited on the fragment of finely woven basketry on the right has created a surface that appears slightly grey, compared to the fragment on the left.
Dirty or soot-covered plant materials should be handled as little as possible until initial cleaning can be done, since putting pressure against dirty surfaces pushes dirt or soot into them. Remnants of ingrained dirt or soot may be impossible to remove. Wear gloves, specifically close-fitting nitrile or latex gloves, which offer good touch sensitivity.
Baskets or other objects made of plant materials may have been previously coated with waxes, poly(ethylene glycol) or glycerin in an effort to reverse dryness or brittleness. This application might have created an initial, superficial improvement, but the application would have darkened the object and, in the long term, increased dryness and deterioration and possibly created sticky surfaces that hold dust.
In older collections, plant materials might contain residual pesticides. Light-coloured powdery or crystalline substances found on a surface should be identified to determine if it is a natural component of the plant material or a material (toxic or non-toxic) applied after the object became part of a collection. Note as well that residual pesticides do not necessarily leave visible traces. If the object is part of a public collection in Canada, the museum, gallery or archive can apply for analysis at CCI. For more information, consult Scientific services.
Recommendations
- Maintain good housekeeping practices and keep collection areas clean. For additional protection in storage areas, keep basketry and other objects made of plant materials within closed storage units or drape them with tissue or lightweight plastic sheeting. In exhibit spaces, displaying the object within a case is preferable. If the object is on open display, then place it several metres away from the visitor route.
- Wear gloves, preferably close-fitting nitrile gloves, when handling objects. If powdery materials are found on the object, have the material identified. If it is toxic, consult with a conservator on handling procedures.
- Handle dirty objects as little as possible. Place the object on a support and move it by using the support. Dust, dirt and soot can detract from the visual appreciation of the object. These particles can also be abrasive and might attract pests. The following are some notes on the safe removal of dust, dirt and soot using a vacuum cleaner:
- Ensure that the dirt does not indicate prior use (anthropological evidence).
- Wear close-fitting gloves (nitrile or latex) and handle as little as possible.
- Select a vacuum cleaner that has a power reduction device that allows reduced suction, or create reduced suction by drilling holes in the suction tube or attachment. Use a vacuum with high efficiency particulate air (HEPA) filtration, if possible. To prevent detached pieces from being sucked into the vacuum cleaner, cover the opening with netting or plastic screening secured with an elastic band or cord.
- Work under good lighting.
- Depending on the suction, hold the vacuum tube or attachment at approximately 8–20 cm (3–8 in.) from the object. There should be enough suction to remove the dust and dirt but not enough to lift any part of the object. Mini vacuum tools might be useful in cleaning intricate basketry.
- Use a soft, clean brush (artist’s or cosmetic brush) to lift dirt from the object toward the vacuum nozzle. Continue over the whole object by moving slowly and methodically across its surface. Go over the surface again, lifting more dirt with a brush. To limit the danger of overcleaning, clean in repeated light passes rather than concentrating on one area. Overcleaning cannot be undone.
- If the surface of the plant material is being disturbed, or if applied decorations are loosened and risk becoming detached, stop and consult a conservator.
Light and ultraviolet
Absorption of both visible light and ultraviolet (UV) radiation triggers reactions that deteriorate the structure of plant materials. They will weaken, and yellowing, fading or darkening can occur (Figure 32). Applied dyes or paints can be very light-sensitive and readily fade (Figure 33).

© Government of Canada, Canadian Conservation Institute. CCI 120526-0035
Figure 32. The perimeter of the birchbark was exposed to light and is much lighter in colour than the central area that was shielded from light.

© Government of Canada, Canadian Conservation Institute. CCI 126827-0016
Figure 33. Dyed wefts on the basket are still colourful on the interior but have faded on the exterior.
Some products of light deterioration are readily soluble in polar solvents (e.g. water, alcohol), increasing the potential for staining if the object is exposed to water (as outlined under Water).
Gums or resins that may be used to secure components (e.g. resins used as caulking on birchbark canoes) can become brittle under exposure to light and UV.
For more information, consult Agent of deterioration: light, ultraviolet and infrared.
Recommendations
- Keep plant materials away from windows. In display areas, reduce light levels to approximately 50 lux. This is especially important if the plant components are coloured.
- Keep lights off in storage areas when access is not needed. Place objects in enclosed cabinets or on draped shelving.
Incorrect temperature and relative humidity
Incorrect temperature
High temperatures accelerate chemical reactions; conversely, lower temperatures slow them down. In the case of fibres dyed through a process using iron, iron-catalyzed deterioration, which makes the fibres become extremely weak and brittle (Figure 34), will occur at a slower rate if the ambient temperature is reduced. There can be benefits if the temperature is lowered by just a few degrees.

© Government of Canada, Canadian Conservation Institute. CCI 79410-0053
Figure 34. The birchbark cylindrical box has four bands of bark, wrapped with spruce root twining. From the bottom upward, the first and third bands were wound with dark-dyed root that contain iron, probably from the dyeing process. The dark root is extremely weak and most of it has been lost, while the light-coloured, undyed root wrapped on the two other bands remains largely intact. White porcupine quills interwoven within the root elements form lozenge motifs.
If higher temperatures result in low RH, plant materials become desiccated and brittle.
Waxes, gums or resins, applied to secure plant components, may become soft at high temperatures or brittle at lower temperatures, which might thus pose risks to the object’s structural integrity.
Recommendations
- The temperature of storage and display areas is usually set for human comfort, but lowering the temperature even by a few degrees Celsius will slow down chemical deterioration. Move plant materials away from sources of heat, such as heating vents and warm sources of light including windows and lighting.
- Identify objects that contain iron-based dyed fibres; these are dark-coloured and usually conspicuously weak and brittle. Bathophenanthroline test strips are simple means of carrying out conclusive identification; contact CCI for further information. Treat these objects with additional care, minimize their handling and provide protective supports. Cool, dark storage conditions, with low to moderate RH, will be of benefit to these objects.
- Dry plant materials kept at very cold temperatures (e.g. a seasonal museum in a cold climate) should not suffer adverse effects if they are carefully handled and supported. Gums or resins might be brittle, so no pressure should be applied to the structure. If freezing is used as a means of insect control, place the object in a plastic bag and seal the bag after having removed as much air as possible. Let the object come to room temperature before opening the bag.
Incorrect relative humidity
At high levels of humidity, over 65% RH, mould can grow. Consult Figure 4 in Agent of deterioration: incorrect relative humidity, which provides a chart indicating the mould growth rate by humidity level.
Exposure to high humidity can soften some materials or cause distortion of parts that had been shaped while moist, then dried in position. If deteriorated binding elements soften, they might not be strong enough to secure the structure and distortions can ensue.
Baskets are made of elements that are tied, woven or otherwise intertwined, so their structure has built-in constraints. Large RH changes cause anisotropic swelling and shrinking of the fibrous materials (as described in Water), which can lead to distortions, breaks and losses. Such damage usually occurs first to the thinner weft elements that are wrapped or twined around larger warps or other elements (Figure 35).

© Government of Canada, Canadian Conservation Institute. CCI 2003633-0001
Figure 35. The rim on this basket is partially damaged. The thinner twined wrapping probably broke first as a result of swelling and shrinking stresses and damage due to large RH fluctuations, most likely also coupled with physical stresses from poor handling. On the right, the basket’s lid has slumped in the centre, and the lid rim has spread out, possibly also due to anisotropic reactions of the fibres in high or fluctuating RH.
Below 40% RH, plant materials become increasingly desiccated and brittle. At low RH, it is therefore important to provide good support and to handle the objects with extra precautions to prevent physical damage.
Recommendations
- Prevent high RH that can cause mould or lead to distortions.
- Avoid large and repeated RH fluctuations. Since basketry, especially very thin types, can respond to RH within minutes, even short periods of extreme RH can cause damage.
- Use handling and storage supports.
For more information, consult Agent of deterioration: incorrect temperature and Agent of deterioration: incorrect relative humidity.
Examples of preventive conservation practices
This section provides practical examples in the care of basketry and plant materials.
Basketry storage at the New Brunswick Museum
Dee Stubbs-Lee
Conservator
New Brunswick Museum
Saint John, New Brunswick
At the New Brunswick Museum, most of the First Nations baskets and birchbark containers are stored using customized polyethylene closed-cell foam (Ethafoam) support mounts. These mounts eliminate the danger of the baskets knocking or crowding together in storage and provide some protection from shock and vibration. The white colour of the mount makes it very easy to regularly monitor the collection for signs of insect activity, without having to handle the objects themselves (Figure 36a). The mounts are clearly numbered, further minimizing the need for handling in order to find the accession number on the objects and, therefore, the risk of accidental damage to the collection during such handling.
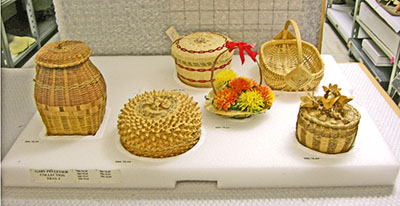
© New Brunswick Museum – Musée du Nouveau-Brunswick, www.nbm-mnb.ca
Figure 36a. A plank of polyethylene foam with baskets sitting in the custom-sized cut-outs.
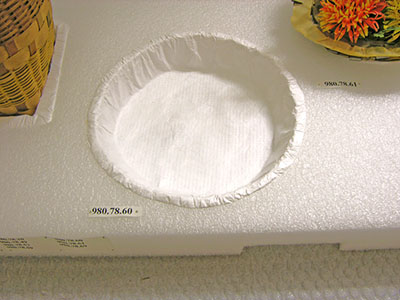
© New Brunswick Museum – Musée du Nouveau-Brunswick, www.nbm-mnb.ca
Figure 36b. Detail of a cut-out for a basket. The recess has been lined with a polyethylene non-woven sheet (Tyvek) that has been tucked into a shallow cut in the foam.
Each basketry mount was made to fit the width of the standard shelving unit that houses the objects. These mounts are quite simple and fairly inexpensive to construct. A recessed area was carved out of a polyethylene foam plank to conform to the shape and size of each object and lined with a polyethylene non-woven sheet (Tyvek), tucking the cut edge of the sheet neatly into a groove around the cut-out (Figure 36b). The non-woven sheet is held in place simply by friction on the wedged edges; there is no need for any adhesive or pins. The surface is smooth, eliminating risks of basketry fibres snagging on the foam. A layer of polyester quilt batting can be placed between the foam and the non-woven sheet if further cushioning is needed for more fragile objects. Taller or top-heavy objects can be further stabilized using cotton twill tape threaded through the foam plank. Handle notches can be cut out from the underside of the foam plank so as to make handling easier and to allow the mounts to be slid forward on the shelves in order to examine the objects in situ (Figure 37).

© New Brunswick Museum – Musée du Nouveau-Brunswick, www.nbm-mnb.ca
Figure 37. The foam storage mounts, with baskets, within the shelving unit. Large baskets are tied in place with cotton tape. A notch cut out from the front edge makes it easy to remove the panel.
Handling mounts for basketry at the Museum of Anthropology, University of British Columbia
Heidi Swierenga
Senior Conservator
Museum of Anthropology, UBC
Vancouver, British Columbia
At the University of British Columbia (UBC), the Museum of Anthropology (MOA) uses handling mounts for the storage and display of basketry. The mounts were developed to allow for the safe and efficient movement of objects in the collection with minimal direct handling of the objects themselves.
Several different designs are used for basketry mounts, depending on the weave structure as well as the shape, condition and size of the basket. The tray design that is by far the most common uses small cross-linked polyethylene (Plastazote) foam wedges to support and hold each side of the basket inside the tray (Figure 38a). Each tray is made slightly larger than the object it carries, thus ensuring the baskets do not touch each other when placed side by side on a shelf. A metal edge strip is used to secure the tray corners (Figure 38b) as well as the foam wedges (Figure 38c), thereby eliminating the use of tapes or adhesives in the construction of the mounts. All components are custom-made to fit the individual shape and size of the basket, and all materials used are subjected to Oddy testing to ensure that they meet conservation standards.
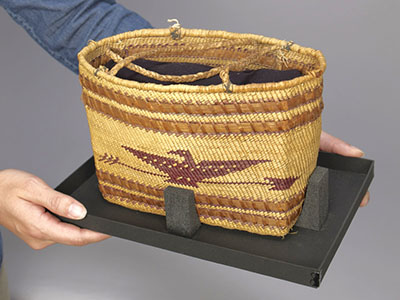
© Courtesy of UBC Museum of Anthropology, Vancouver, Canada
Figure 38a. Basket Nb11.229 being moved by hand on a custom-made handling mount.

© Courtesy of UBC Museum of Anthropology, Vancouver, Canada
Figure 38b. Detail of a wedge and of the metal edge strip securing one of the corners of the tray mount.

© Courtesy of UBC Museum of Anthropology, Vancouver, Canada
Figure 38c. Detail showing how the metal edge strip fastens a foam wedge to the tray.
Since a large portion of MOA’s collection is on display in the visible storage system, aesthetic aspects are an important consideration in mount development. Through consultation with a number of user groups, darker materials have been found to be preferable for use in mount construction at MOA. The darker palette recedes into the background and highlights the objects, whereas white board and foams are stark and clinical in appearance and draw the eye away from the objects. White materials are used, however, for baskets that are in poor condition in order to better observe their condition and deterioration.
Bibliography
Adney, E.T., and H. Chapelle. Bark Canoes and Skin Boats of North America. New York, NY: Skyhorse Publishing Inc., 2007, pp. 14–15.
Barclay, R.L. “A Handling Device for Large Wooden Objects.” Journal of the International Institute for Conservation — Canadian Group 13 (1988), pp. 8–10.
Bigelow, S. Cold Storage of Photographs at the City of Vancouver Archives (PDF format). [N.p.]: Canadian Council of Archives, 2004.
Clark, T. “Storage Supports for a Basket Collection: A Preventive Conservation Approach.” Journal of the American Institute for Conservation 27,2 (1988), pp. 87–99.
Daniels, V. “Factors Affecting the Deterioration of the Cellulosic Fibres in Black-Dyed New Zealand Flax (Phormium tenax).” Studies in Conservation 44,2 (1999), pp. 73–85.
Florian, M-L., D. Kronkright and R. Norton. The Conservation of Artifacts Made From Plant Materials. Marina del Rey, CA: The Getty Conservation Institute, 1990.
Frisina, A. “Plant Materials.” In S. Ogden, ed., Caring For American Indian Objects: A Practical and Cultural Guide. St. Paul, MN: Minnesota Historical Society Press, 2004, pp. 191–197.
Jaoul, M., and B. Goldstein. La vannerie française. Paris, France: Éditions de la Réunion des musées nationaux, Musée national des arts et traditions populaires, 1990.
National Park Service. Storage Supports for Basket Collections (PDF format). Conserv O Gram 5/1. Washington, D.C.: National Park Service, July 1993.
© Government of Canada, Canadian Conservation Institute, 2018
Published by:
Canadian Conservation Institute
Department of Canadian Heritage
1030 Innes Road
Ottawa, ON K1B 4S7
Canada
Cat. No.: CH57-4/6-3-2018E-PDF
ISBN 978-0-660-27963-3
Page details
- Date modified: