Caring for metal objects
Robert L. Barclay, Carole Dignard and Lyndsie Selwyn
Caring for metal objects is part of CCI's Preventive conservation guidelines for collections online resource. This section presents key aspects of managing the care of metal objects in heritage collections based on the principles of preventive conservation and risk management.
Table of contents
- Understanding metals and corrosion
- Causes of metal corrosion and preventive conservation strategies
- Strategies for protecting against corrosion: the multi-level approach
- Other agents of deterioration
- Examples of preventive conservation practices
- Bibliography
- Glossary
List of abbreviations and symbols
Abbreviations
- CCI
- Canadian Conservation Institute
- HVAC
- heating, ventilation and air conditioning
- LDPE
- low-density polyethylene
- MDF
- medium-density fibreboard
- MERV
- minimum efficiency reporting value
- NGC
- National Gallery of Canada
- portable document format
- PET
- poly(ethylene terephthalate)
- ppb
- part per billion
- RH
- relative humidity
- UV
- ultraviolet
- VOC
- volatile organic compound
Symbols
- cm
- centimetre
- e-
- electron
- Fe
- iron
- Fe2+
- ferrous ion
- H2O
- water
- in.
- inch
- mm
- millimetre
- O2
- oxygen gas
- OH-
- hydroxide ion
Understanding metals and corrosion
A variety of metals, metal alloys and metal finishes can be found in museum collections. As a group, metals share some common and unique properties. One such property is that, generally, they are susceptible to corrosion (gold and other noble metals being the exception). Each type of metal has its own degree of vulnerability to corrosion.
Please note that issues relating to metals in an outdoor setting are discussed more specifically in Caring for outdoor objects.
Understanding metal objects
Metal properties
Metals share many useful properties; namely, they are strong, are often lustrous, are good conductors of heat and electricity and they can be cast. In pure metals, the atoms are all the same size, and this makes it easy for them to slide over each other when a force is applied. That is why relatively pure metals are soft, malleable and ductile. They are easily shaped by bending, drawing and hammering (Figure 1).
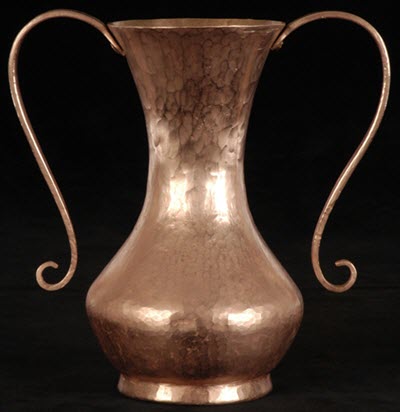
© Government of Canada, Canadian Conservation Institute. CCI 87306-0001
Figure 1. An elegantly formed copper vase with a hammered finish.
In alloys—mixtures of two or more elements, of which at least one is a metal—the comparative sizes of the atoms give a measure of how malleable or ductile the metal may be. For example, zinc and copper atoms are similar in size, so their alloy, brass, is relatively soft and easily worked; on the other hand, tin atoms are considerably larger than copper atoms, so their alloy, bronze, is more difficult to work (Figure 2). The presence of impurities also influences workability.
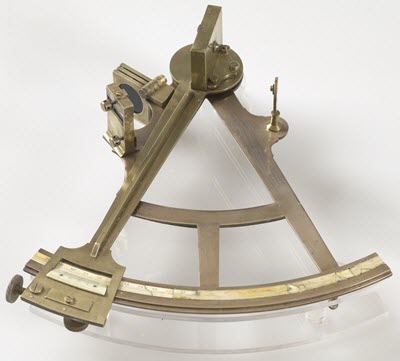
© Government of Canada, Canadian Conservation Institute. CCI 97899-0011
Figure 2. A mid-1800s sextant made of bronze and brass from Fort William Historical Park made by R.H. Cogswell, a well-known nautical instrument maker in Halifax, Nova Scotia. The instrument's main frame is made of bronze (85% copper, 10% tin, 4% lead and 1% zinc), a material usually harder and stronger than brass, which explains its use for the most structural part of this instrument. Smaller components are made of brass (71% copper, 27% zinc and trace amounts of lead, tin and nickel). Brass is often used in decorative pieces as it casts details well.
Grain structure of metals
At a microscopic level, metals show a granular structure where each grain is formed from an even array of atoms. These grains can be likened to crystals, such as those found in table salt, except that they can be deformed under pressure. The size of the grains depends upon many factors, including the rate of cooling of the metal and, in the case of an alloy, its particular constituents. Grain formation can easily be seen with the naked eye in zinc-plated (galvanized) steel objects, such as heating ducts, where the characteristic spangled effect of large zinc grains is very noticeable (Figures 3a and 3b). The orientation of the atoms between individual grains varies, so at the boundaries of the grains—where each one touches the next—there are inconsistencies in the way the atoms are stacked. The metal is more vulnerable to corrosion at these locations because they are more chemically active.
During the process of working a metal, the grains become distorted, resulting in hardening. Controlled heating will cause the grains to return to a more uniform shape, thus softening the metal; this process is called "annealing."
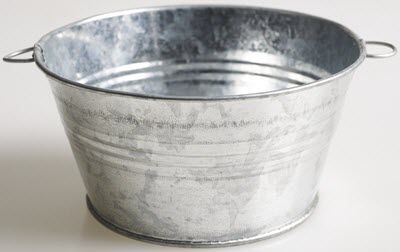
© Government of Canada, Canadian Conservation Institute. CCI 125773-0038
Figure 3a. A zinc-plated (galvanized) steel pan.
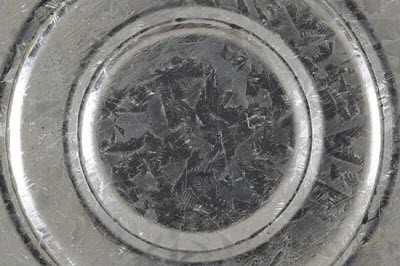
© Government of Canada, Canadian Conservation Institute. CCI 125773-0039
Figure 3b. Detail of pan in Figure 3a, showing the characteristic crystalline spangle pattern on the zinc-plated steel.
Variety of metals
It is important to know and be able to recognize what specific metal objects are made of because this will give clues about their susceptibility to corrosion and will narrow down which preventive conservation measures should be implemented.
There is a wide range of metal elements. In museum collections, the chief ones encountered in any quantity are aluminum, copper, gold, iron, lead, nickel, silver, tin and zinc.
Of these metals, a wide range of alloys have been produced for many purposes. Most metals found in collections are alloys; objects made of a pure metal are rare. Examples of common alloys in collections are brass (copper and zinc), bronze (copper and tin), steel (iron plus carbon, manganese, nickel, chromium, etc.), sterling silver (silver and copper) and nickel silver, also called "German silver" (copper, nickel and zinc). Aluminum is usually alloyed with other metals (e.g. copper, manganese, magnesium, but many others are possible), while gold is often alloyed with silver, platinum or copper. The colour, tone and sheen of a variety of common metals and alloys are shown in Figure 4.
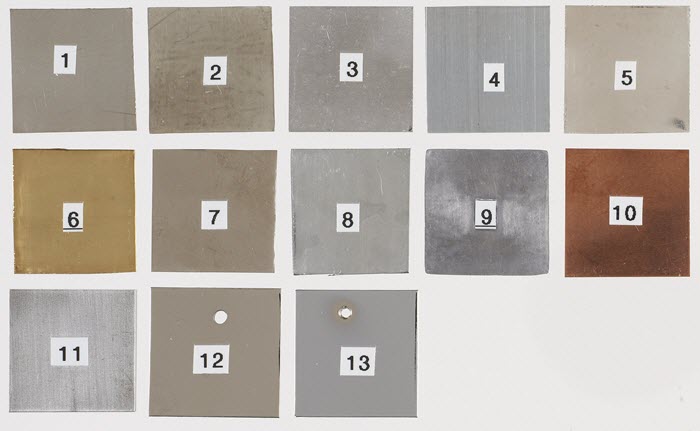
© Government of Canada, Canadian Conservation Institute. CCI 120260-0069
Figure 4. Various metal samples. From left to right, first row: nickel (1); tin (2); aluminum (3); zinc (4); sterling silver (5). Second row: brass (6); tin-plated iron (7); galvanized steel (8); lead (9); copper (10). Third row: steel (11); nickel-plated iron (12); chrome-plated iron (13).
Metal plating
Collections also contain plated metal objects, as these are fairly common, especially for contemporary items. Plating metal objects is a process in which a fine layer of one metal is applied on the surface of another metal (the core metal). This process is often done using an electric current and is then called "electroplating" (a process patented in 1840). Silver, for example, is frequently electroplated onto copper and copper-nickel alloys (Figures 5a and 5b). Objects plated with silver are as lustrous but less expensive than those made entirely of sterling silver (an alloy containing 92.5% silver and 7.5% copper). Examples of silver-plated objects include flatware, serving dishes, jewellery, liturgical objects, candlesticks and trophies.

© Government of Canada, Canadian Conservation Institute. CCI 97196-0006
Figure 5a. A silver-plated fork. The stamp located on the back at the thinnest area of the handle is shown in Figure 5b.
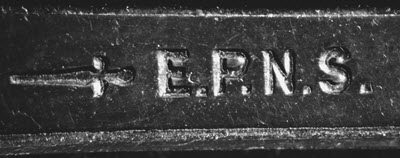
© Government of Canada, Canadian Conservation Institute. CCI 87306-0037
Figure 5b. The stamped letters E.P.N.S. stand for "electroplated nickel silver," which means that the silver electroplating is over a nickel silver base, which consists, in fact, of a copper-rich alloy containing nickel and zinc, but no silver.
Iron and steel are also frequently electroplated, typically with a layer of zinc, tin, nickel or chromium. There are many common examples such as steel cans plated with tin (commonly known as tin cansFootnote 1), chrome-plated car parts or steel containers galvanized with zinc (Figure 3a). These platings protect the underlying metal against corrosion as long as the plating layer remains continuous.
Metal finishes
Metals can be artificially finished or patinated with a variety of chemical and physical techniques, and it is important to identify these original finishes from other possible surface layers. Steel, for example, can be finished with heating (Figure 6). During heating, attractive colours or tonal effects may be produced; thus, their presence on a metal surface provides information about the technique of fabrication (e.g. colour case-hardening). Artificial patinas are often created on iron, bronze (Figure 7) and other metals using chemicals. Natural corrosion processes also produce, over time, patinas that are often prized and sought after. Chemically, a patina is a corrosion layer; however, the term is often specifically used to refer to an aesthetically pleasing layer that enhances the metal object and should not be removed.
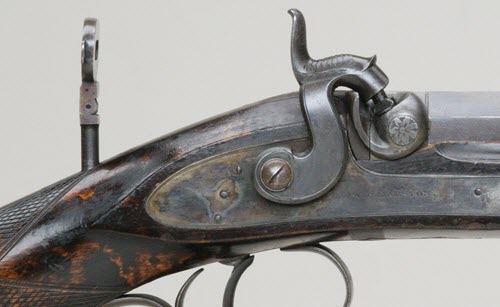
Percussion rifle, CWM 20000201-001, Canadian War Museum
Figure 6. Detail of a musket showing heat-treated steel on the lock plate.
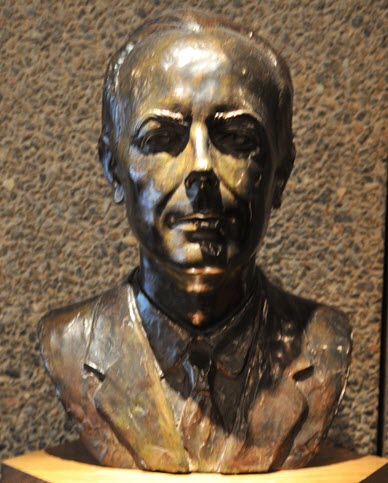
© Government of Canada, Canadian Conservation Institute. CCI 122863-0090
Figure 7. Patinated bronze bust of composer and pianist Béla Bartók, by Hungarian sculptor Pál Pátzay, exhibited at the National Arts Centre in Ottawa.
As well, metal objects may be coated with lacquers that are an important feature of their original appearance. These may be transparent or coloured. Such lacquered finishes are common on scientific instruments (Figures 8a, 8b and 8c).
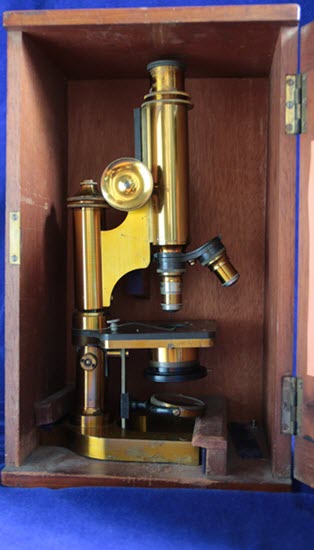
© S. Michalski
Figure 8a. An overall view of a lacquered brass microscope in its original case. The microscope is in generally good condition but has some spots of corrosion.
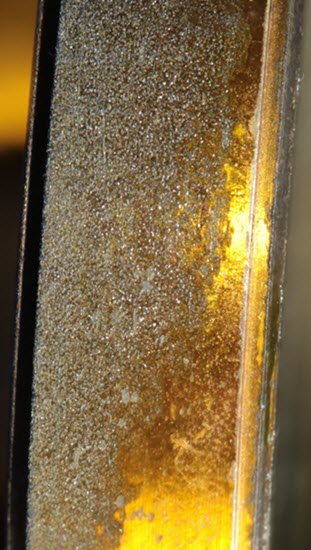
© S. Michalski
Figure 8b. Detail of corrosion on the mirror rim where the user's fingers would make frequent adjustments.
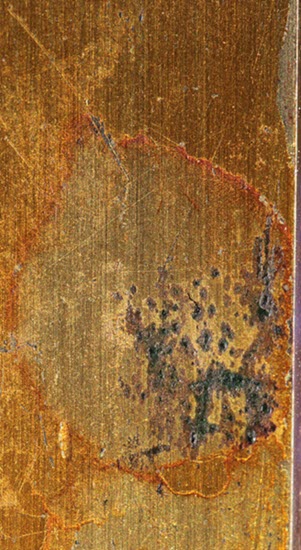
© S. Michalski
Figure 8c. Detail of the base where corrosion formed after a user dropped solvent on the lacquer.
Finishes, patinas and lacquers are often extremely thin surfaces and can be damaged by even a small amount of abrasion or chemical cleaning. A key issue in the care of metal objects is the importance of recognizing and preserving original finishes.
Understanding corrosion
Why metals corrode
Corrosion products on metals are familiar occurrences in everyday life (Figures 9a, 9b and 9c). A corrosion product is a compound usually formed from the reaction of a metal (or alloy) with a non-metal. Except for noble metals, such as gold or platinum, most metals are inherently unstable and have a strong tendency towards corrosion.
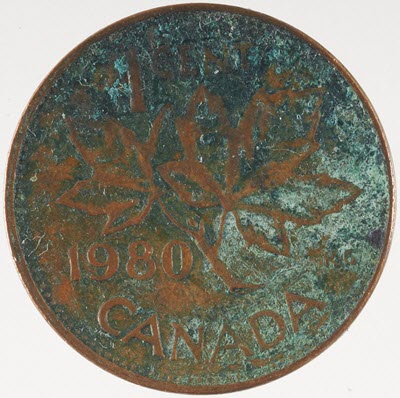
© Government of Canada, Canadian Conservation Institute. CCI 123557-0062
Figure 9a. Canadian penny dated 1980 with heavy green, brown and black surface corrosion products.
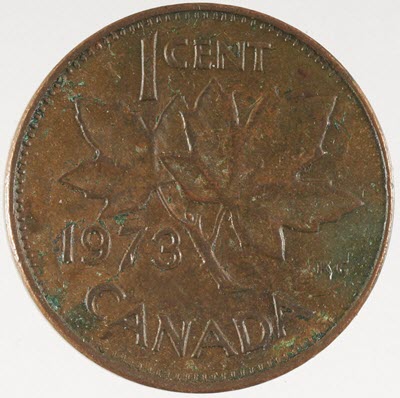
© Government of Canada, Canadian Conservation Institute. CCI 123557-0062
Figure 9b. Canadian penny dated 1973 with brown surface patina (tarnish).
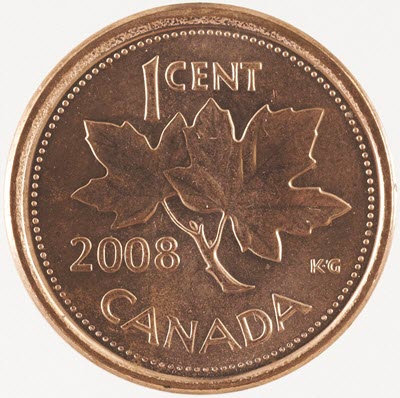
© Government of Canada, Canadian Conservation Institute. CCI 123557-0062
Figure 9c. Canadian penny dated 2008, virtually untarnished.
The necessary ingredients for corrosion to take place are:
- metal
- water (an electrolyte)
- oxygen
When brought together, these components result in an electrochemical cell, which allows free movement of electrons and ions (Figure 10). For example, for iron, the reaction at the anode is
Fe → Fe2++ 2e-
and the reaction at the cathode is
½ O2 (gas) + H2O + 2e- → 2OH-
In the presence of an electrolyte (typically water), electrons flow within the metal (from the anodic area to the cathodic area). The metal ions (in the example of Figure 10, the iron ions Fe2+) either remain in solution or react with surrounding species and precipitate, forming corrosion products.
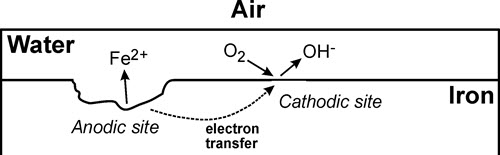
© Government of Canada, Canadian Conservation Institute. CCI 87306-0063
Figure 10. Illustration of the corrosion process on a piece of iron covered with a thin film of water. The anodic site is where the action is—where the iron is oxidized and forms iron ions (here, Fe2+) that, at least initially, dissolve in the electrolyte. Simultaneously, at the cathodic site, water molecules combine with oxygen gas (O2) and with electrons that transfer from the anodic site to form hydroxyl (OH-) ions.
The presence of salts dissolved in the water can greatly accelerate corrosion. Among the most destructive are chloride salts, which, unfortunately, are also very prevalent. They are found, for example, in fingerprints left on a metal surface after manipulating it with bare hands. These salts are highly soluble, and it is extremely difficult, if not impossible, to render metal stable in their presence. Copper can combine with chloride ions to form certain corrosion products that are unstable in the presence of moisture. For iron contaminated with chloride salts, any moisture will cause a continuing chain of corrosion until the metal is consumed.
Pollutants, dust (which can contain salts) and other contaminants can also cause or contribute to corrosion. For example, sulfur compounds cause silver to tarnish (consult Understanding how silver objects tarnish for more information). Most pollutants come from outdoor sources, but some may originate from inside buildings (e.g. organic acids, such as acetic acid, are emitted from wood and wood-based products as well as from many alkyd, oil and latex paints).
Metals most prone to corrode
Some metals are more prone to corrosion than others. Metals are arranged in order of reactivity or potential for corrosion in what is known as a galvanic series (Table 1).
Most noble ![]() Least noble |
Platinum Stainless steel 304, passive Silver Nickel Lead Copper-nickels Tin bronzes Lead-tin solder (50/50) Tin Copper Yellow and red brass Stainless steel 304, active Mild steel, cast iron Aluminum alloys Zinc |
The more noble the metal in the series, the less likely it is to corrode. (Gold is not normally listed in a galvanic series; it falls close to platinum.) If two metals in direct contact (e.g. an alloy, a plated metal, or soldered or joined metal components) are both exposed to a moist environment, a galvanic effect (galvanic corrosion) takes place, where the less noble (or baser) metal in the series will corrode faster than if it were not in contact with the nobler metal. For example, if an aluminum rivet is used to join a piece of copper, and there is sufficient humidity in the air to act as an electrolyte, the aluminum will corrode at the point of contact with the copper. Plated iron, such as tin-plate, is another example: it is stable if in good condition but is prone to corrosion when scratches or dents expose the underlying iron, making it possible for galvanic corrosion to occur in the presence of sufficient humidity (Figures 11a and 11b).
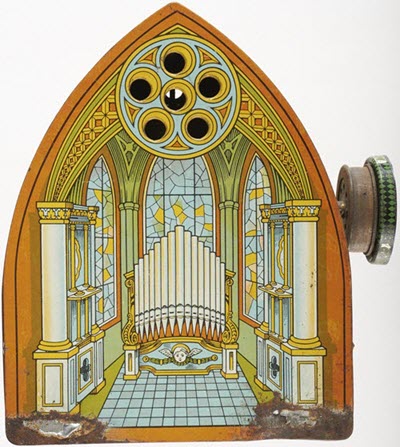
© Government of Canada, Canadian Conservation Institute. CCI 123557-0141
Figure 11a. A painted tin-plated musical box. On both corners of the base, abrasion damage to the paint and tin-plate exposed the iron underneath, which then rusted due to some moisture in the air.
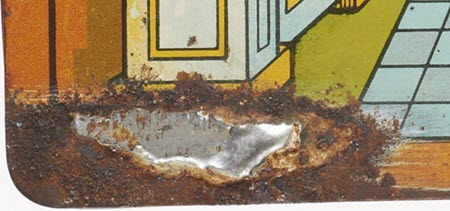
© Government of Canada, Canadian Conservation Institute. CCI 123557-0141
Figure 11b. Detail of Figure 11a, showing abrasion damage and rust on the left bottom corner of the toy musical box.
Stable surfaces versus active corrosion
How can one recognize the difference between a stable surface and one that is actively corroding?
- Stable surfaces: If a strong, even film of corrosion is formed on a metal, this will often protect the underlying metal against further corrosion by providing a barrier against new chemical reactions. Thus, a stable passivating layer is produced. Stable surfaces on metal objects are generally adherent and the thickness does not increase (or increases only minimally) with time. They are usually thicker and more uneven on archaeological objects than on non-archaeological ones. The majority of metal objects in museums have stable surfaces if kept at moderate levels of relative humidity (RH) (45–50%).
- Active corrosion: This term is generally used to refer to fresh or new corrosion on an object. Signs of active corrosion include surface cracking or spalling on the object, as well as powder or loose flakes of surface material surrounding the object (Figure 12). This kind of physical damage or material losses may be due to recent corrosion that has formed at the metal layer under the surface, thus causing an expansion in volume that pushes against the overlying material (such as older corrosion products, paint or plating layer) and causes cracks and flaking. Similar damage also occurs when salt contaminates a metal: if moisture is present, the salts hydrate and increase in volume, thus fracturing the cohesion of the surface layers and causing losses. Efflorescence and deliquescence are also indicators that corrosion-stimulating salts may be present. Active corrosion has a characteristic appearance on different metals and alloys, as described below.
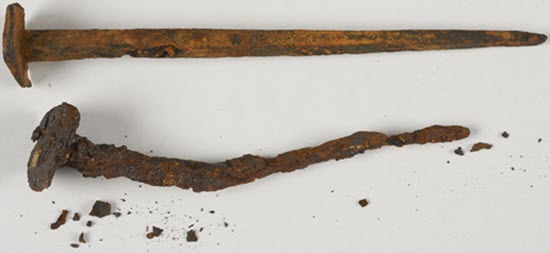
© Government of Canada, Canadian Conservation Institute. CCI 125773-0070
Figure 12. The corrosion products flaking off the bottom nail are evidence that this nail is unstable and suffering from active corrosion. The nail at the top is stable.
Recognizing types of corrosion on common metals
Learning to recognize the common surface appearances of metals through physical examination is a useful skill since corrosion layers often have a distinctive look that can help to identify the metal. For each of the following common metals, its typical corrosion product colour is listed, and the appearance of both its stable corrosion surface and its actively corroding surface(s) is described.
Aluminum
Typical corrosion product colour: white
Stable surface: A very thin, stable oxide film that prevents further deterioration. Most aluminum objects indoors in museum collections should be stable.
Active corrosion: Salts and acids contained in dirt can accumulate on aluminum surfaces, mostly in external locations. These contaminants, in combination with water (rain, flood, etc.), penetrate the aluminum oxide film and cause pitting on the surface (Figure 13). Chlorides in common salt (sodium chloride) rapidly attack the aluminum oxide layer, producing a white powdery corrosion product. Indoors, however, active corrosion is rare.
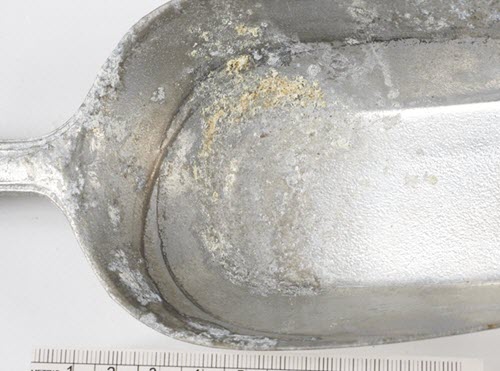
© Government of Canada, Canadian Conservation Institute. CCI 123557-0011
Figure 13. Detail of a corroded aluminum scoop, probably due to having been exposed to salts. The corroded areas are white and powdery in contrast to the smooth surface of the aluminum.
Copper and copper alloys (bronze and brass)
Typical corrosion product colours: red, brown, black, blue, green
Stable surface: There are a wide variety of stable surface layers, or patinas, both natural and artificial, on copper and copper alloys (most commonly bronze and brass). Stable patinas on these metals are generally coherent, adherent and smooth and can be golden-coloured (Figure 14), red, brown (Figure 15), black, green (Figures 7 and 16) or blue.
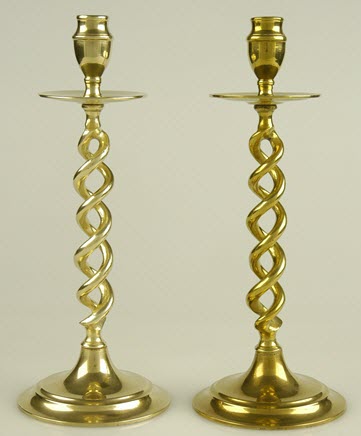
© Government of Canada, Canadian Conservation Institute. CCI 85802-0008
Figure 14. The polished brass candlestick on the left is a lighter yellow than the tarnished darker one on the right. Exposure to air containing some moisture and pollutants, such as hydrogen sulfide, slowly forms this thin, stable corrosion layer, also called a "patina."
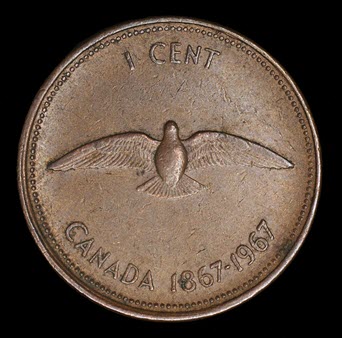
© Government of Canada, Canadian Conservation Institute. CCI 125773-0040
Figure 15. An example of a stable brown patina that has formed naturally on this well-circulated 1967 Canadian centennial penny. The brown stable tarnished surface can eventually become quite dark.
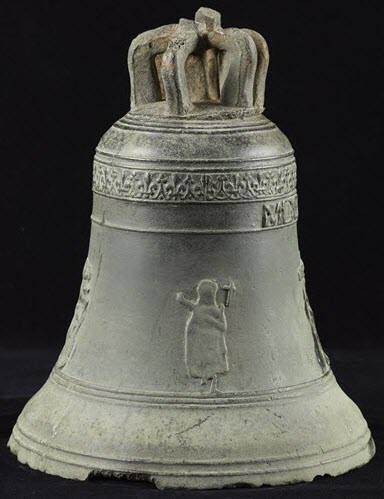
© Government of Canada, Canadian Conservation Institute. CCI 68548-0012
Figure 16. A stable green-black patina on a copper-alloy (probably bronze) bell dated circa 1648 and believed to be of French origin, currently in the collection of Sainte-Marie Among the Hurons Mission National Historic Site.
Active corrosion: Local spots or wider areas of green corrosion may appear on a stable patina. Localized green corrosion products occurring on museum objects are often a result of contamination due to inappropriate polishing (harsh ammonia-based or acid-based cleaning compounds, polish residues, etc.; Figure 17). Many pollutants and contaminants react with copper to form green corrosion products, but these are more common in a polluted outdoor environment than inside a museum (Figure 18).
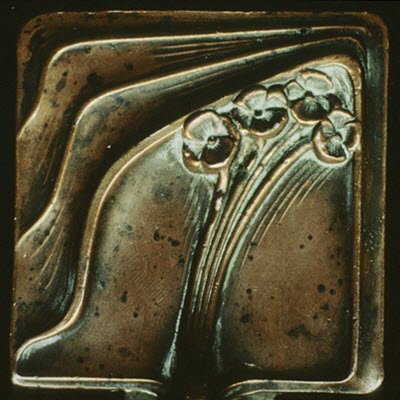
© Government of Canada, Canadian Conservation Institute. CCI 129955-0008
Figure 17. The overall brown colour on this copper object is the naturally formed patina. The green corrosion products are most likely due to hard-to-remove metal polish residues trapped within recesses of the floral design. Black spots on the patina are probably due to localized deposits of contaminants (e.g. polish residues, salt, dust).
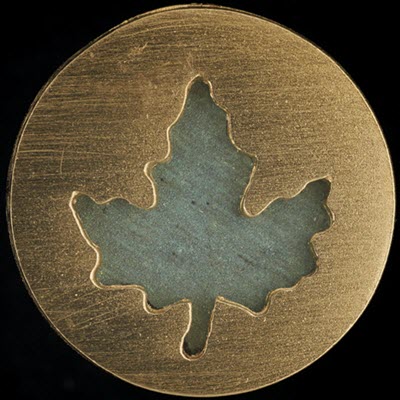
© Government of Canada, Canadian Conservation Institute. CCI 125773-0041
Figure 18. Maple leaf broach. The green leaf was crafted from sheets of corroded copper roofing that covered Canada's Parliament Buildings from 1918 to 1996.
Green corrosion can also develop when copper or its alloys are in contact with some natural plant and animal products, such as beeswax, lanolin and linseed oil. The acids in fats, oils and waxes will attack copper, resulting in waxy green corrosion products (copper soaps, e.g. stearates). Copper-based components of leather objects (e.g. leather straps, bags and boots with brass rivets, fasteners or decorative beads) often show such corrosion because leather contains fats and oils which are incorporated into it during its manufacturing process; in addition, it is common for oil-based products (e.g. lubricants, leather dressings) and waxes to have been applied to it during the object's use (Figures 19 and 20). Green corrosion spots also occur, for example, on a brass chandelier where drops of candle wax have fallen.
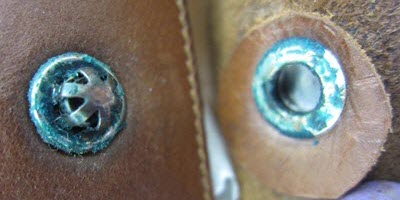
© Government of Canada, Canadian Conservation Institute. CCI 124883-0027
Figure 19. Detail of a snap or rivet fastener on vegetable-tanned leather boots. Green corrosion products are commonly observed when copper or copper alloy elements are in contact with leather.
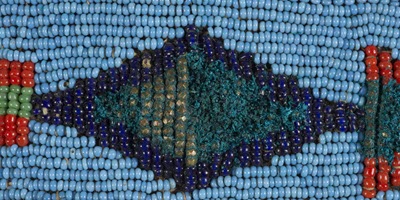
© Government of Canada, Canadian Conservation Institute. CCI 100641-0004
Figure 20. Detail of a Northern Plains leather belt decorated with turquoise, blue and red glass beads and with brass beads within the chevron design. The brass beads are covered with waxy green corrosion products due to a reaction with oils, most likely from a leather dressing.
A special form of active corrosion called "bronze disease" is usually seen on archaeological objects and is due to the presence of chloride salts from the burial environment that react with copper to form the corrosion product copper(I) chloride. It is characterized by the development of a light green powder erupting in spots over the surface (Figure 21) as the copper(I) chloride reacts with moisture and air. This form of active corrosion can occur when the humidity is above 55%. Objects suffering from bronze disease need to be stored at a low RH, typically less than 42% (Rimmer et al. 2013).

© Government of Canada, Canadian Conservation Institute. CCI 125773-0064
Figure 21. An example of bronze disease on an archaeological copper alloy blade that appears as green powdery spots.
Gold
Typical corrosion product colours: none
Stable surface: Pure gold does not corrode. However, gold alloys can corrode. In the presence of sulfur-containing gases, the silver and copper components of gold alloys will darken as they tarnish.
Many gold objects, such as serving plates or religious ware, are gold-plated and so not entirely made of gold. These may be parcel-gilt (i.e. made of silver where only part of the surface is gilded), and in these cases, it can happen that the tarnish on the silver creeps over the gilding.
Active corrosion: none (Gold and gold alloys are stable.)
Iron and steel
Typical corrosion product colours: black, red, orange, yellow, brown
Stable surfaces: These are compact, adherent and vary in colour between blue-black and red-brown. Museum objects made from iron and steel, especially those that have been used outdoors or stored in an uncontrolled environment, are often covered with a stable red-brown rust layer (Figures 22 and 23).
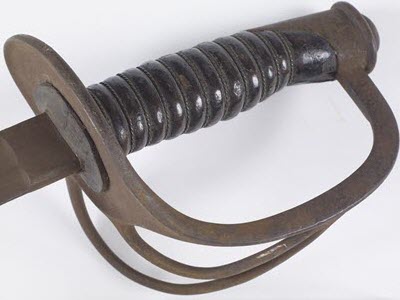
© Government of Canada, Canadian Conservation Institute. CCI 98217-0005
Figure 22. An even, stable layer of red-brown rust on the hilt of a steel sword.
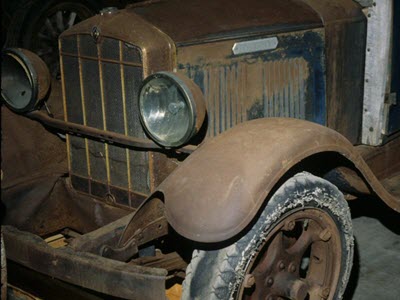
© Government of Canada, Canadian Conservation Institute. CCI 85802-0012
Figure 23. Stable rust is often red-brown in colour, usually well adhered to the metal and is caused by exposure to moisture at some time during an object's lifetime. Shown in this photograph is a historical vehicle with many of its steel components covered with rust. This rust will remain unchanged as long as the RH remains low.
Active corrosion: Active iron corrosion is observed when rust progresses or intensifies. It is characterized by new bright orange corrosion (flash rusting at high RH) or by flakes falling off from a surface that is left with pits and depressions with orange spots in their centres (Figure 24; consult Understanding flash rusting for more information). It is due to the presence of sufficient moisture to promote corrosion, from either high humidity or hygroscopic salts (mainly chloride-containing) that have picked up moisture from the air.
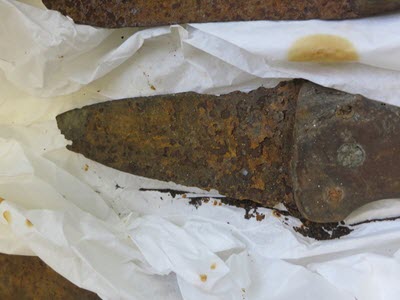
© Government of Canada, Canadian Conservation Institute. CCI 124716-0044
Figure 24. Iron knife blade showing active orange corrosion, pitting of the surface and losses.
A special form of active corrosion is found mainly on untreated archaeological iron and is caused by the presence of chloride ions in the burial environment, which contaminate the metal. It is characterized by sweating or weeping where yellow, brown or orange droplets appear on the metal surface when the RH is above 55% approximately. In drier conditions, this active corrosion takes the form of orange-brown glassy blisters (Figure 25). Another chloride-containing iron corrosion product, known as akaganéite, may also be present. Objects suffering from this kind of active corrosion need to be stored at a low RH, typically less than 20% (Rimmer et al. 2013).
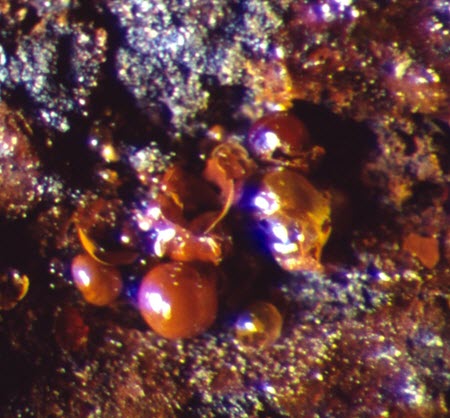
© Government of Canada, Canadian Conservation Institute. CCI 87306-0007
Figure 25. Detail of chloride-contaminated iron showing blisters that have formed after weeping.
Lead
Typical corrosion product colour: white
Stable surface: Lead develops a stable dark grey, non-powdery patina.
Active corrosion: Lead is readily attacked by organic acid vapours (e.g. acetic acid) emitted from wooden storage or display units (especially oak), as well as poor-quality paper and cardboard and many types of freshly applied paints. The corrosion appears as a loosely adherent white powder (Figure 26). The powder may appear evenly over the surface or as a network of white spots.
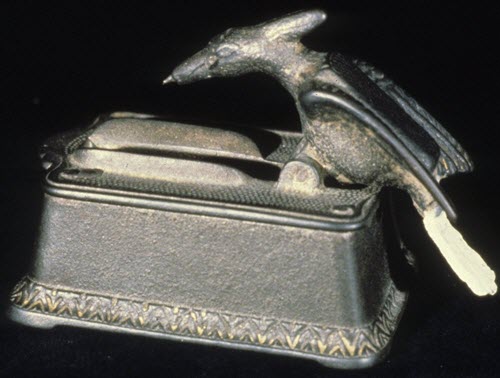
© Government of Canada, Canadian Conservation Institute. CCI 129955-0009
Figure 26. This cast iron object is a match-picking device: it consists of a pivoting woodpecker that picks up a match from among those stored in the base. The tail of the bird is made of lead, now totally covered with white corrosion products due to long-term display in an oak cabinet. (Match-picker from the collection of the Musée du Séminaire de Sherbrooke.)
Note: Lead and its corrosion products are toxic; proper safety precautions must be taken to prevent exposure. In particular, white lead corrosion products are powdery and can easily transfer, or become airborne, posing an even-greater risk in terms of contact and inhalation (Selwyn 2005).
Nickel
Typical corrosion product colour: green
Stable surface: Nickel is resistant to corrosion and remains bright under normal indoor museum conditions for a long time. The surface gradually dulls over time as the nickel oxide layer thickens, particularly if the RH is high.
Active corrosion: When exposed outdoors to pollutants such as sulfur-containing gases, nitrogen oxides and chloride ions, a nickel surface dulls (in a process called "fogging") as it reacts with the pollutants and forms a thin layer of green nickel corrosion products.
Silver
Typical corrosion product colour: black
Stable surface: Silver develops a stable surface corrosion layer of silver sulfide tarnish when exposed to sulfur-containing gases. Initially, when the layer is thin, it can appear as a gold, blue or purple colour. Slight differences in thickness give rise to iridescent colours. As the tarnishing continues, it develops into a dense, black, compact and adherent layer (Figure 27).
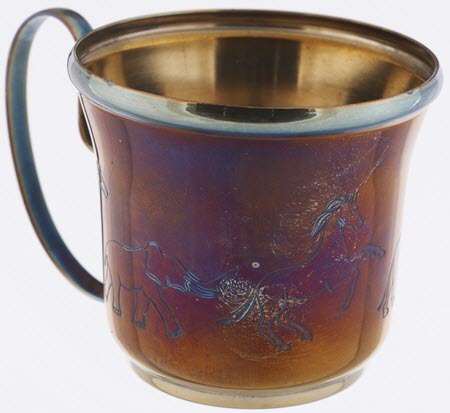
© Government of Canada, Canadian Conservation Institute. CCI 120260-0051
Figure 27. A tarnished silver cup, showing a range of colours.
Active corrosion: In rare cases, whiskers of black silver sulfide can form on silver. These are likely to form when there are high levels of sulfur-containing gases and slow air movement.
Tin and tin alloys
Typical corrosion product colours: white, black (the patina usually appears grey from a mixture of the white and black corrosion products)
Stable surface: Tin is mainly found in collections as a plating (e.g. tin-plated iron) or as tin alloys because pure tin metal alone is usually too soft to make objects. "Old pewter" refers to a tin alloy containing lead which was commonly used to make various objects from ancient times to a few centuries ago; it generally has a dull grey patina (Figure 28). In comparison, pure tin metal, tin plating and modern pewter—various tin alloys that contain no lead—remain bright for a long time but gradually turn dull over time as a surface oxide forms (Figure 29).
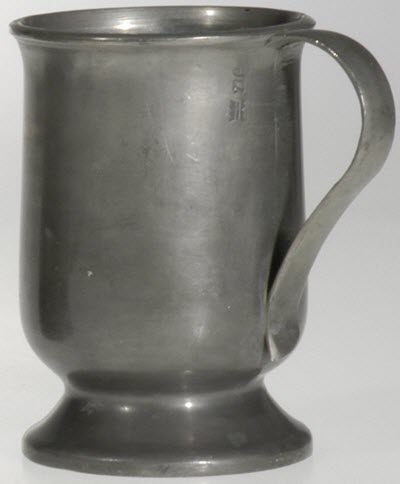
© Government of Canada, Canadian Conservation Institute. CCI 85802-0011
Figure 28. A tankard made from old pewter. The surface has gradually darkened with time to form a dull grey patina.
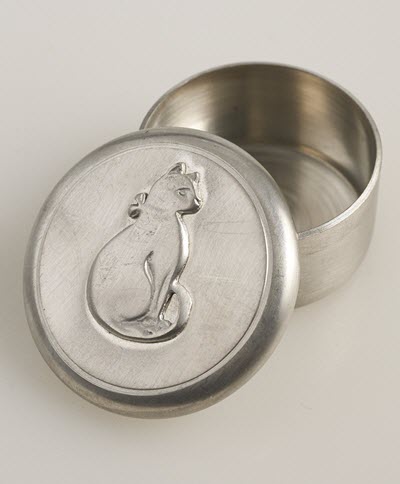
© Government of Canada, Canadian Conservation Institute. CCI 125773-0035
Figure 29. A jewellery box made of modern pewter, a tin alloy that contains no lead. It remains stable.
Active corrosion: Tin and tin alloys do not exhibit active corrosion.
Note: Tin-plated iron objects such as cans, some dishes and various kitchen utensils are often miscalled tin. These often present corrosion problems associated with rust formation by the iron, usually after the tin plating layer has been damaged (Figure 30a and 30b). Consult Plated metals for more information on this type of corrosion.
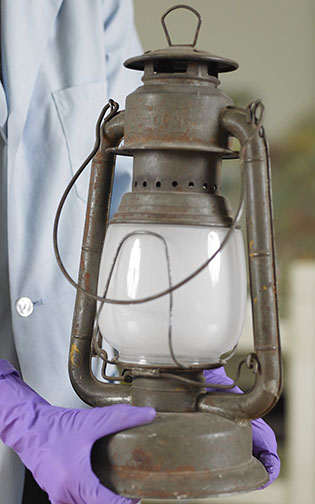
© Government of Canada, Canadian Conservation Institute. CCI 125773-0001
Figure 30a. Lantern made of tin-plated iron.
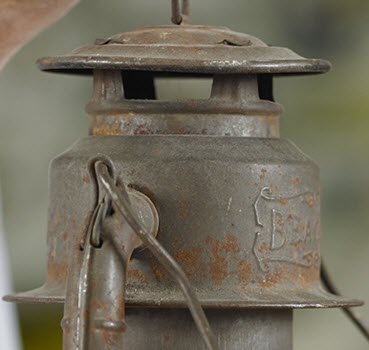
© Government of Canada, Canadian Conservation Institute. CCI 125773-0002
Figure 30b. Detail of the lantern in Figure 30a, showing the dark grey patina on the tin surface as well as areas where the tin plating has worn off and the underlying iron is rusting.
Zinc
Typical corrosion product colour: white (Figure 31)
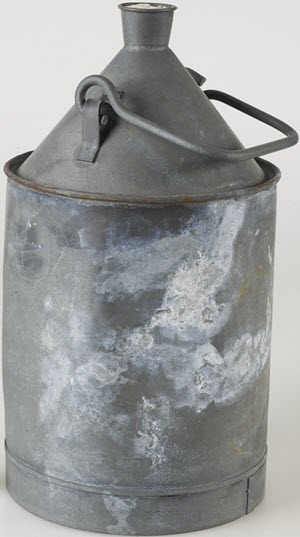
© Government of Canada, Canadian Conservation Institute. CCI 89037-0227
Figure 31. A zinc-plated (galvanized) steel fuel can, circa 1930, showing areas where the zinc plating is corroding. Excavated from Krüger's archaeological site, Axel Heiberg Island, Nunavut.
Stable surface: The surface of a zinc object remains bright for a long time (Figure 3a) and only slowly loses its lustre with the growth of a relatively adherent layer of zinc corrosion products.
Active corrosion: Zinc surfaces corrode and form white corrosion products when exposed to water or high levels of humidity. The corrosion rate of zinc accelerates when pollutants increase the acidity or alkalinity of the water or when salts increase the conductivity of the water. These compounds are often present or adsorbed into dust particles. Zinc objects found in wet archaeological settings may show this type of corrosion, especially if they are exposed to salty water (Figure 31).
Plated metals
Stable surface: Stable plated surfaces, particularly those plated with gold, silver, nickel and chromium, often retain their original bright metallic appearance when kept under appropriate environmental conditions, although the shine may be obscured by grime or dirt. As long as the plating layer remains continuous, the underlying metal is protected from corrosion.
Active corrosion: The underlying metal may start to actively corrode if it is exposed to air and moisture. This can happen if the plating layer is defective and porous or if it is physically damaged (e.g. abraded, scratched, dented).
Active corrosion on plated metals appears in various ways depending upon the underlying metal, the plating and the nature of the corrosion. The plating usually lifts because the corrosion products of the underlying metal expand (Figure 32). Corrosion products from the underlying metal may also find their way to the surface via microflaws or pores puncturing the surface layer. Pitting also occurs on plated objects when the plating is perforated, and corrosion products grow in spots from the underlying metal. All active corrosion on plated metals is accompanied by an expansion in volume, which leads to loose powder around the object or to blisters of more coherent corrosion products on the surface.
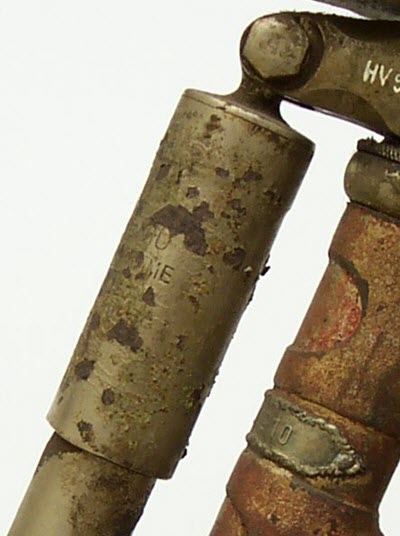
© Government of Canada, Canadian Conservation Institute. CCI 73174-0002
Figure 32. Detail of a motorized bicycle frame part showing the way that nickel plating typically peels away from the steel.
Causes of metal corrosion and preventive conservation strategies
Metal objects need to be protected primarily from water and high RH as well as from pollutants and contaminants. These agents of deterioration can often be controlled together. Preventive conservation measures focus mainly on keeping the objects in as dry an environment as possible to prevent outbreaks of corrosion and keeping the air pollution-free and the metal surfaces free of contaminants. Identifying priority objects allows a multi-level preservation approach ranging from overall controls to object-specific microenvironments. Other agents of deterioration that affect metal objects are also reviewed.
Water and relative humidity
Both liquid water and high ambient RH pose serious risks to almost all metal objects: exposure to either will foster corrosion.
Water
If liquid water contacts metal objects (e.g. a flood), some degree of corrosion takes place. Immersion in water can lead to corrosion. Corrosion in water is especially rapid or aggressive if the water is well oxygenated or if salts are present. Short exposure can result in rapid surface corrosion, such as when flash rusting occurs on iron or steel objects that have been even momentarily wetted (Figure 33).
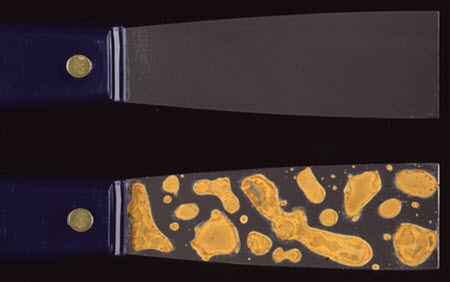
© Government of Canada, Canadian Conservation Institute. CCI 87306-0026
Figure 33. Top: A putty knife with a steel blade. Uncorroded steel typically has a silvery-grey colour such as here. Tools and machinery are often made from steel. Bottom: Flash (rapid) rusting on a similar steel putty knife. Flash rusting is rapid rusting on iron just after exposure to high humidity (e.g. a flood) or brief wetting. The rust that forms is bright orange, and the stains occur in areas where the water pooled on the steel.
High relative humidity
In ambient conditions, there is some degree of moisture in the air, which can cause corrosion. The higher the RH, the greater the risk.
Above 65% RH, there is enough adsorbed water on most clean metal surfaces to approach the behaviour of bulk water and therefore create an electrolyte that will support the corrosion process (Figure 34). In general, above the threshold of 65% RH, all metal corrosion significantly speeds up.
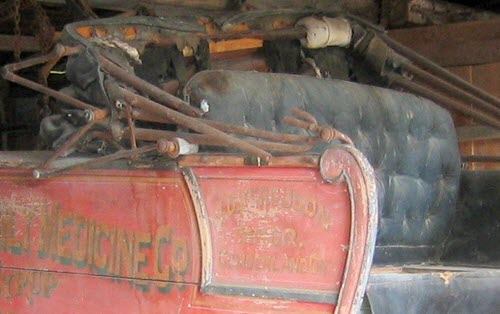
© Government of Canada, Canadian Conservation Institute. CCI 129955-0010
Figure 34. Detail of an old horse-drawn carriage. A thin layer of mould on the leather seats and deep rusting of all the iron components are typical outcomes for objects kept in a shed that is dry most of the year but damp in the spring and fall.
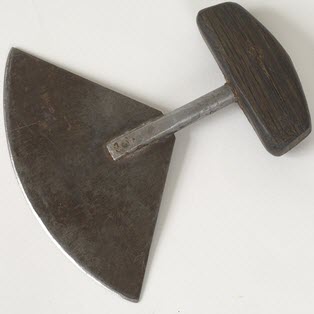
© Government of Canada, Canadian Conservation Institute. CCI 129955-0001
Figure 35. This composite object, an Inuit ulu (knife) made of iron with a wood handle, has been kept for years at moderate levels of RH (approximately 50% +/-5%). The metal remains relatively stable, and the RH is at a safe level for the wood handle.
Since the corrosion process on metals requires water (moisture), reducing the humidity in the air will be beneficial in slowing or arresting corrosion. In general:
- Dry environments (30% or lower) are ideal for metals.
- At moderate RH (40–55%), the majority of metals will exhibit no immediate problems. This is because most metals have a thin passivating corrosion (or oxide) layer on their surface. Moderate RH levels are also the range recommended for composite objects (objects containing both metal and organic components; Figure 35). For these, avoiding low RH levels prevents the organic components from drying out, which can lead to physical damage (cracks, splits, lifting, warping, deformations, etc.).
Pollutants and contaminants
Gaseous pollutants
Table 2 provides a summary of gaseous pollutants most harmful to metals, the average outdoor and indoor concentration ranges and their usual sources (adapted from Tétreault 2003, pp. 8; 26; 32; 99–105).
Pollutant: corrosion onset threshold* (μg m-3) (metal) | Average outdoor concentration (μg m-3) and common outdoor sources | Average indoor concentration (μg m-3) and common indoor sources |
---|---|---|
Hydrogen sulfide (H2S): 0.1 (silver); 1 (copper) |
0.01 to 10 Sources: fuel and coal combustion, petroleum and pulp industries (kraft processes), vehicle exhaust, volcanoes, marshes, ocean, some natural waters |
Room: 0.03 to 40 (with people) Sources: visitors and staff, certain foods (eggs, mayonnaise), arc-welding activities, rubber, animal glues, some modelling clays, some paints, pyrite in mineral specimens, sulfate-reducing bacteria in archaeological objects |
Carbonyl sulfide (COS): 30 (copper); 500 (silver) |
0.7 to 1 Sources: coal combustion, coastal ocean, soils, wetlands, oxidation of carbonyl disulfide (CS2) (sources of CS2: rotting organic matter in oceans, soils and marshes, fungal growth) |
Room: 0.3 to 0.5 Emissions from wool in a dark room: 0.03 Emissions from wool in sunlight: 1 Sources: degrading wool, degrading polysulfide-based sealants |
Sulfur dioxide (SO2): 50 (copper) |
0.1 to 100 Sources: combustion of sulfur-containing fossil fuels, pulp and paper industries, petroleum refineries |
Room: 0.1 to 50 Sources: vulcanized rubbers, degrading sulfur-containing materials (proteinaceous fibres, some dyes, pyrite in mineral collections) |
Acetic Acid (CH3COOH): 400 (lead) 1000 (copper); 20,000 (zinc) |
0.3 to 30 Sources: degradation of organic matter |
Room: 40 to 100 Wood crate: 80 to 3000 Oak chest: 300 to 7000 Emulsion paint or two-part epoxy paint dried for five weeks: 3000 to 20,000 Oil paint dried five weeks: 20,000 to 70,000 Acid-type silicone, cured three days, one week, four weeks: 14,000, 1000, 100 Degrading cellulose acetate films: 900 to 100,000 Sources: wood and wood-based products, alkyd and oil-based paints, many emulsion paints, acid-type silicone sealants, green cleaning products (based on vinegar), degrading cellulose acetate (vinegar syndrome), degrading organic materials, flooring adhesives, linoleum, human metabolism, microbiological contamination of air conditioning filters |
Formic acid (HCOOH): 200 (lead); 8000 (copper) |
0.1 to 20 Sources: degradation of organic matter |
Room: 0.1 to 30 Wood crate: 2 to 2000 Sources: wood and wood-based products, oil-based paints, degradation of organic materials |
Ozone (O3) |
2 to 400 Sources: photochemical smog |
Room: 0.1 to 100 Room with ozone generator or photocopiers: 4 to 600 Sources: electronic air cleaners, electronic arcing, electrostatic filtered systems, laser printers, photocopiers, ultraviolet (UV) light sources, lightning, insect electrocuters |
Nitrogen dioxide (NO2): 50 (copper) |
2 to 100 Sources: oxidation of nitrogen (NO) compounds (sources of NO: agricultural fertilizers, fuel combustion from vehicle exhaust and thermal power plants, gas heaters, lightning, photochemical smog) |
Room: 2 to 90 Emissions from cellulose nitrate films: 4000 Sources: degrading cellulose nitrate (plastic or film) |
Ammonia (NH3) |
0.7 to 20 Sources: concrete dust, fertilizer industries, inorganic process industries, underground bacterial activities, animal excrement |
Room: 0.6 to 60 Building with 400–3000 visitors/day: 10 to 30 Sources: household cleaning products (window cleaning fluids), concrete dust, emulsion adhesives and paints, alkaline-type silicone sealants, visitors |
*Estimates based on data for clean metals at 50 to 60% RH and 20°C to 30°C. |
Sulfur-containing gases (H2S, COS and SO2) affect metals in general, but in particular, they react with silver, copper and copper alloys, causing them to tarnish (Figure 36). Hydrogen sulfide (H2S) is especially a problem because it reacts with silver and copper at very low concentrations. Silver exposed to merely 0.1 μg m-3 (1 ppb) will typically tarnish within a year; this is a level commonly found indoors (Table 2), and it is also below the odour threshold level (Tétreault 2003). Carbonyl sulfide and sulfur dioxide can also cause corrosion, especially to copper and its alloys. Sources of sulfur-containing gases originate both outdoors and indoors, with visitors and staff being one of the largest single sources. Freshly polished metal is more prone to tarnishing than if already covered with a tarnish layer.
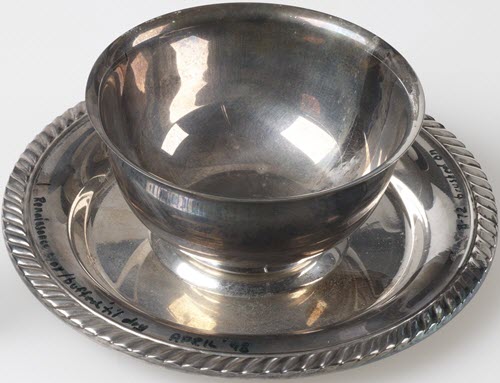
© Government of Canada, Canadian Conservation Institute. CCI 121590-0011
Figure 36. A silver object showing a light degree of tarnish (slight black tint with yellow highlights) as a result of exposure to atmospheric sulfur.
Acetic and formic acids are corrosive pollutant emissions that can react with some metals—with lead being by far the most sensitive. Lead will corrode if exposed to merely 400 μg m-3 of acetic acid or to 200 μg m-3 of formic acid (Tétreault 2003). These levels of emissions are easily found in proximity to certain materials, such as wood and wood-based products, oil or alkyd-based paints and coatings, as well as many sealant materials (Table 2). A prime example in museums is lead stored within a wood display case or storage cabinet: it will develop a white powdery corroded surface (Figure 37). Lead-tin alloys (old pewter) are not as susceptible to these acidic volatiles as pure lead. Formaldehyde is mentioned by some authors as a potential risk for lead, zinc, copper and copper alloys; however, the risks are negligible in normal museum conditions (Tétreault 2003).
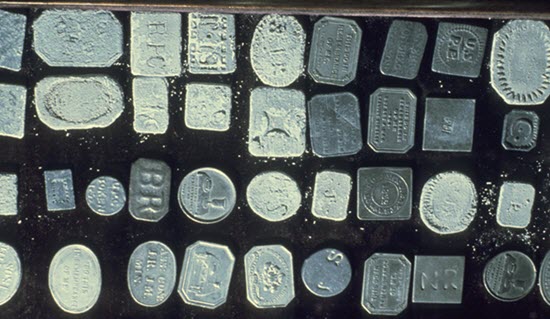
© Government of Canada, Canadian Conservation Institute. CCI 87306-0059
Figure 37. White, powdery corrosion appears on the surface of some lead and pewter medallions and tokens in a storage drawer. Corrosion rates differ according to the alloy present and the stability of the patina. This corrosion is the result of products in the immediate environment that emit organic acids. Lead is particularly prone to this type of corrosion.
Note: The white powdery corrosion products on lead are toxic. When these are present, wear personal protective equipment (nitrile gloves, mask), bag the object to prevent the products from spreading and consult a conservator about safe corrosion removal and disposal.
Ozone and nitrogen oxide compounds contribute to corrosion; e.g. they increase the rate of silver tarnish (Rimmer et al. p. 14). Nitrogen oxide compounds (NOx) are also capable of causing corrosion reactions on various metals, particularly on iron (Figure 56b). Ammonia, which may be present indoors due to the use of household cleaning products (window cleaning fluid) or from concrete dust, is corrosive to metals.
Dust, fingerprints, salts, fatty acids, polish residues
Dust settling on metal objects can contain salts and particulates that are hygroscopic and cause local corrosion. In addition, the dust can obscure decorative details and act as an abrasive against a polished surface if rubbed off.
Fingerprints and perspiration (or sweat) from hands contain salts, oils, moisture, etc., that easily transfer onto metal surfaces and can lead to noticeable corrosion, especially on polished metal surfaces (Figure 38). Sodium chloride (salt) from fingerprints reacts with silver to form silver chloride, which is light sensitive and can darken over time, resulting in fingerprint stains that are highly visible and obtrusive on polished pieces.
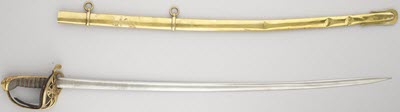
© Government of Canada, Canadian Conservation Institute. CCI 128594-0011
Figure 38a. Overall view of sword and its brass scabbard.
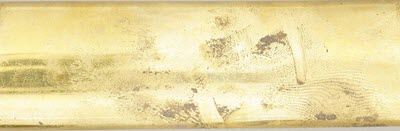
© Government of Canada, Canadian Conservation Institute. CCI 128594-0017
Figure 38b. Detail of fingerprint marks etched onto the surface of the sword's brass scabbard. Marks like these are virtually impossible to remove without polishing.
A significant problem for metals in maritime locations is the presence of salts (mainly chlorides) in the air (sea salt aerosols).
Fatty acids can corrode metals; materials containing oils, fats and waxes in contact with copper-based metals will cause the development of green corrosion products (copper soaps; Figures 19 and 20).
A common problem observed on museum objects made of copper and copper alloys is a characteristic pale green corrosion caused by the reaction between the metal and polish residues (Figure 39).
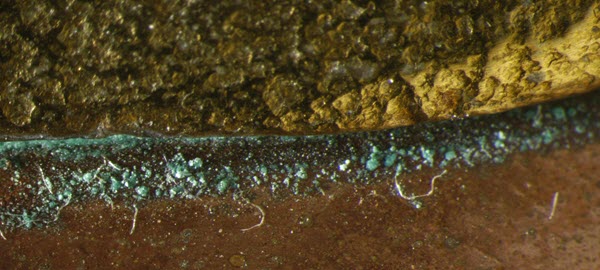
© Government of Canada, Canadian Conservation Institute. CCI 85802-0009
Figure 39. Residue of abrasive polish can remain in crevices or engraved areas because of inadequate rinsing. Here the residues appear pale green in colour because green corrosion products have stained the white abrasive.
Combined effects of pollutants and contaminants with relative humidity
RH has a major influence on the degree of corrosion that pollutants and contaminants can cause. For silver, at a given level of pollutant, the tarnish rate will decrease by a factor of three when the RH is lowered from 75% to 15% (Rimmer et al. 2013). The effect is estimated as being even more pronounced for other metals: as a rule of thumb, lowering the RH by 10% can as much as double the pollutant's minimum dose needed to cause corrosion (Tétreault 2003). In other words, the higher the RH, the lower the pollutant threshold concentration that can cause a metal to corrode.
The deleterious effects of salt, oils and metal particulates are also greatly influenced by RH:
- Salts are hygroscopic and actively cause corrosion even at low to moderate RH levels (Rimmer et al. 2013):
- Salt-contaminated iron and its alloys can suffer from active corrosion (Figures 40a and 40b) at an RH as low as 20% and, in some cases, even at 12%. At RHs between 20–30%, the corrosion rate increases gradually. At RHs over 30%, the corrosion rate increases sharply, and at 50% or more, corrosion is very rapid.
- Salt-contaminated copper and its alloys are only at low risk of corrosion if kept below 42% RH. At levels between 42–68%, the risk is present and probably moderate to high, while over 68%, the risk of corrosion is very high.
- In many cases, corrosion begins when a particle (dust) is deposited on a metal surface.
- Metal particulates deposited on a metal surface pose additional problems because they can foster new corrosion processes.
- Oily residues tend to absorb airborne pollutants, and so they increase the pollutants' overall effects (Tétreault 2003, p. 28).
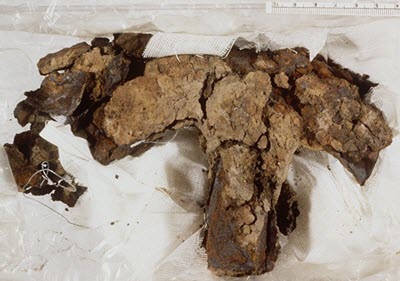
© Government of Canada, Canadian Conservation Institute. CCI 129955-0011
Figure 40a. This highly corroded axe head is a typical example of active corrosion of a salt-contaminated archaeological iron object.
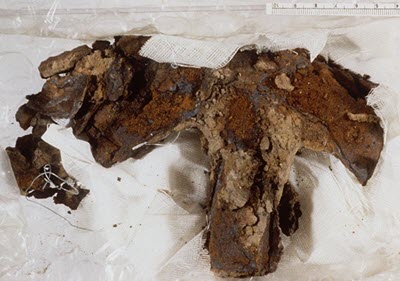
© Government of Canada, Canadian Conservation Institute. CCI 129955-0012
Figure 40b. The axe head shown in Figure 40a, with fractured layers removed, revealing brightly coloured corrosion products next to the metal surface.
Strategies for protecting against corrosion: the multi-level approach
Metals are sensitive to both RH and to pollutants in general, but to different degrees: some metals are more at risk of damage in normal indoor conditions. That is why adopting a multi-level preservation approach will optimize results. Some strategies, such as ambient climate control to moderate RH levels (avoiding dampness) and pollutant filtration, should be applied to provide a basic overall level of protection for the whole collection. Localized enhanced measures, such as microenvironments, can then be applied to further protect the most vulnerable metal objects in the collection, focusing on the objects that will benefit most.
The multi-level preservation approach requires identifying the metal objects most at risk within the collection. It is not cost-effective to provide all metals in the collection the highest level of protection, nor is it advisable to assume all metals require the same basic level of care.
Strategies for the whole collection
Protect against liquid water
- Avoid all potential sources of water: water may come from burst pipes, melting ice, leaks because of heavy rain and wind, floods or condensation.
- Raise objects off floors (Figure 41). In the case of heavier items, this can incur the use of lifting gear and specially constructed pallets.
- Cover the top of storage shelves with a waterproof dust sheet (e.g. clear polyethylene plastic sheet or non-woven polyethylene sheet [Tyvek]). If possible, drape the dust sheet at a slight sloping angle so that, if there is water infiltration, water coming down from the ceiling will not pool on the dust sheet but will shed towards both ends of the storage shelf.
- Enclose small metal objects in archival quality bags or water-resistant boxes (consult Enclosures).
- Avoid storing or displaying metal objects in areas where there is a risk of water leaking (e.g. near water pipes).
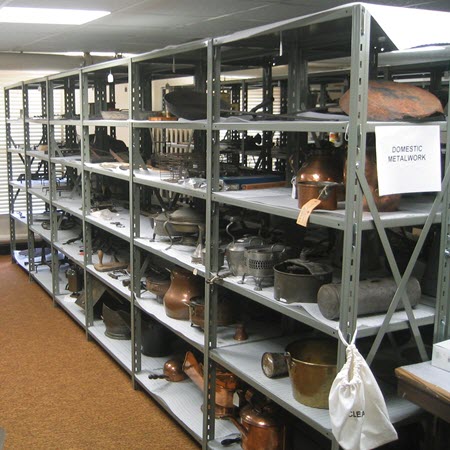
© Government of Canada, Canadian Conservation Institute. CCI 125773-0185
Figure 41. Storing objects off the floor on sturdy metal shelves.
Keep relative humidity levels moderate and avoid damp
The priority for metals is to avoid exposing them to high RH (damp, or RH >65%). A moderate RH range (40–55%), which is usually recommended for objects made of organic materials (such as wood, textiles and paintings) or for composite objects, will be adequate to keep corrosion risks low for the majority of metals in the collection, but not for all: some metals will require dryer conditions. Eliminating all risks of high RH will benefit the whole collection and will improve the efficiency of localized measures that will need to be put in place for more sensitive metals, helping to keep their low RH microenvironments stable and effective for longer periods (Rimmer et al. 2013).
Climate control for the building's interior can be achieved by using an active mechanical system (i.e. a building's HVAC system), if the institution has one, and using passive means via improvements to the building fabric (i.e. repairs to prevent risk of water ingress, improved insulation and airtightness).
Temperature has a large impact on RH. In historic houses during cold weather, poorly insulated walls can lead to cold spots that will cause dampness; metals will be more at risk of corroding in these areas. Also, a rapid decrease in the external temperature can cause the indoor RH to increase, which is conducive to corrosion.
Basic RH control strategies include the following:
- Keeping objects away from colder areas in a room (e.g. exterior walls with windows) because these will cause localized, damp pockets of air and result in higher corrosion risks for metal objects.
- Improving building insulation to eliminate temperature gradients and cold spots.
- Providing for air circulation, as this may prevent local concentrations of high humidity enough to at least slow down the rate of corrosion.
- Monitoring the environment to identify cold or damp spots. Equip the area in which metals are stored and displayed with RH and temperature control monitors (data-loggers, hygrothermographs, RH indicator strips, etc.).
Consult Agent of deterioration: incorrect relative humidity for more strategies.
Filtration
Air quality targets recommended for museums, galleries and archival collections are provided under Agent of deterioration: pollutants (consult Table 2 for gaseous pollutants and Table 6 for dust and particulates). These targets are general; further protective measures (enclosures, etc.) are required for metals most sensitive to pollutants (e.g. silver, lead), as discussed below in Strategies for enhanced protection.
Strategies to filter dust and corrosive gases will depend on the context. If the building already has an HVAC system, it may be possible to add a more efficient dust filter and a gas filtration unit into it. This will require more power to run the system because of the additional air resistance. Dust filters vary depending on the size of the particles they capture. Dust filters that have a minimum efficiency reporting value (MERV) rating of 10 are often used as the recommended filters for office space. It is recommended to choose a higher MERV rating for museums, up to a MERV 16 filter, which is similar to a HEPA filter and is used in special clean rooms, notably for surgery or high-tech activities. Different types of sorbent products exist that can filter specific gaseous pollutants. Multiple active (blended) sorbents are most often used in museums since they can trap a large variety of compounds. However, if a specific gas is found to be the core problem for the collection, it is possible to select a sorbent optimized to capture it.
Monitors for some key gases at the ppb level should be present before and after the air passes through the filtration system. It is also possible to measure the corrosivity of the air by placing metal coupons in the room for a set number of weeks and then sending them for analysis (some filter companies provide technical services of this type). This is a means of verifying the filtration system's performance and also of predicting how long the filters will last before having to replace them. A filter's replacement frequency can also be determined by sending the filter's medium (the actual filtering material), after a few months of use, to a company that can measure how much of its filtering capacity remains. If no testing can be done, replacing the gas filters every year is suggested.
If the building does not have an HVAC system (e.g. some older buildings and historic houses), it is possible to consider having portable particle or gas-and-particle filtration units in the rooms where objects are at risk of corrosion.
Dust protection
Protect metal objects from dust deposits using enclosures, when possible (consult Enclosures), and dust sheets. Dust sheets can be applied over shelving units or as curtains against the sides or over individual objects or groups of objects on individual shelves. Oversized metal objects should be protected with a dust cover. Minimize sources of dust inside the museum (e.g. use carpets at entrances to capture dirt brought in from the outside, but avoid carpets in other rooms since they generate lint). Consult Agent of deterioration: pollutants for more strategies to protect objects from dust.
Gloves
Avoid touching metal surfaces with bare hands. Fingerprint stains on metal are a common problem when visitors are able to touch the objects on display or when good handling procedures among staff are not enforced (Figure 42).
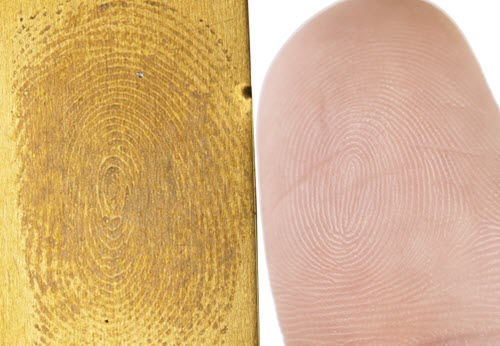
© Government of Canada, Canadian Conservation Institute. CCI 120260-0065
Figure 42. Touching metal surfaces with bare hands can leave fingerprint stains like this thumbprint etched onto brass.
Clean, suitable plastic gloves (e.g. nitrile gloves) are recommended for handling objects (Rimmer et al. 2013). The safest kind to use on metals, especially polished ones, are disposable nitrile gloves made without chemical accelerators (e.g. N-DEX Free nitrile gloves). Clean cotton gloves can also be used, but note that chloride salts have been found to have penetrated through cotton gloves after just a single use. Also, brand new cotton gloves contain residual chloride from processing, so they need to be washed prior to use.
Safe storage and display products
Avoid products that emit harmful volatiles in the vicinity of metal objects, in particular:
- Wood and wood-based products, unless sealed (described below): they emit formic acid, acetic acid, aldehydes and peroxides.
- Freshly applied latex (emulsion) paints and coatings (described below): they emit acetic acid and ammonia.
- Oil or alkyd paints and coatings: they emit formic acid, acetic acid and peroxides.
- Silicone sealants (gasketing, rubbers) and adhesives: some are acid-type, which emit acetic acid; others are alkaline-type, which emit ammonia.
- Rubber gasketing and any rubber products: they emit sulfur-based gases.
Use products that are known to be safe for making mounts, boxes, cabinets, display cases (e.g. acid-free matboard, acrylic or polyethylene plastic panels, silicone-free sealants, metal, glass). Pay particular attention to the choice of materials used to make enclosed spaces that will contain metal objects. Carefully review products (cloth, felt, adhesive, paint, gasket) to be used inside display cases and other types of enclosures to ensure that the products are safe. In particular, note the following:
- Wood and wood-based products: avoid using over large surface areas; instead, use safe products such as medium- or high-density overlaid plywood panels (where the wood surface is sealed with a barrier layer made of paper impregnated with a stable resin); or seal wood surfaces with plastic-foil laminate (Marvelseal; Figure 43) or other suitable barriers. Paints, varnishes and other such coatings are generally not effective barriers against wood emissions (not to mention that most paints and varnishes themselves are typically sources of harmful emissions, as discussed below).
- Paints, varnishes and other coatings: in general, keep metal objects far away from rooms, furniture or decorative surfaces coated with paint or varnish, especially if freshly or recently applied. When a paint, varnish or coating must be applied on a surface within a room which will house metal objects, choose among latex (i.e. emulsion) products, as these are less harmful to metals. Even so, make sure to plan downtime for airing out prior to placing metals in the same general environment, because even latex products will emit high levels of harmful volatiles, but only over the short term. Enclosed spaces such as display cases or other types of enclosures need to air out for at least four weeks before metal objects are placed within them. As for surfaces in an open, well-ventilated room, they need to air out at least four days.
- Use interleaves such as clear polyester film (Melinex) to avoid direct contact between metal objects and emissive products, notably wood, wood products or any painted or varnished surfaces, including those coated with latex products.
- Avoid using an object's original storage case (such as a musical instrument case or medal presentation case) if it is made of wood, cardboard, foam or leather unless it has been assessed to ensure that it is not acidic and does not produce volatiles.
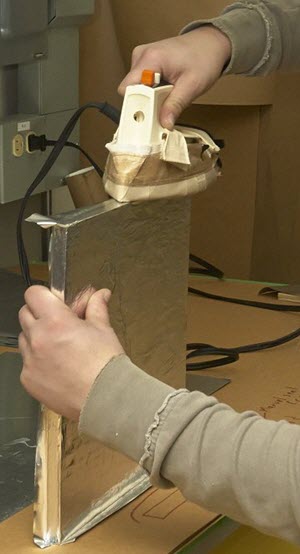
© Government of Canada, Canadian Conservation Institute. CCI 124491-0028
Figure 43. A plastic-aluminum barrier film (Marvelseal) is being applied to a wooden surface using an iron. Gases cannot permeate through the Marvelseal's aluminum layer; thus, if all surfaces are covered and heat sealed, harmful emissions from wood and wood products will be fully blocked.
Consult Technical Bulletin 32 Products Used in Preventive Conservation for more details on safe products for storage and display, and Technical Bulletin 21 Coatings for Display and Storage in Museums for more details on paints, varnishes and other coatings used in a museum context.
Contact or proximity with museum objects that produce emissions
Some museum objects emit harmful volatiles or produce harmful by-products, in particular:
- Cellulose nitrate (e.g. French ivory)
- Degrading cellulose acetate (vinegar syndrome)
- Pyrite mineral specimens (specimens can degrade and produce sulfuric acid)
- Rubber
- Degrading wool
- Wood objects, especially where large surface areas of wood are involved
- Painted objects, especially where large surface areas of paint are involved
Metal objects should neither be in direct contact with these objects, nor should they be placed in close proximity to them within an enclosed space. It is also, in general, safer for other museum objects not to be in direct contact with a metal object to prevent the risk of stains from corrosion products.
Strategies for enhanced protection
Objects requiring enhanced protection
The multi-level approach towards protecting a metal collection from corrosion involves identifying metal objects that are unstable or more at risk in order to provide them with tailored, enhanced protection. Those demonstrating active corrosion (as described under Stable surfaces versus active corrosion) require further action. Typical signs of active corrosion include cracks and spalling, flaking or loose powder around the object (Figures 44a, 44b and 45).
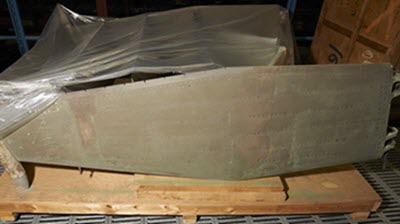
© Government of Canada, Canadian Conservation Institute. CCI 125760-0012
Figure 44a. A hydrofoil removed from a 1956 Baddeck boat made of a copper alloy, possibly Monel (a copper-nickel alloy). Green corrosion products have fallen onto the wood pallet, a sign of active corrosion. This is a clear sign that the room-level control measures are insufficient for this object.
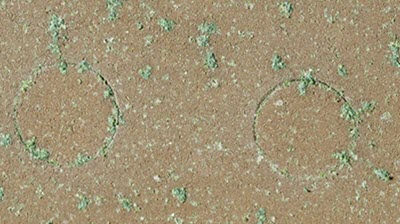
© Government of Canada, Canadian Conservation Institute. CCI 125760-0018
Figure 44b. Detail of Figure 44a showing the pitted surface with bright green corrosion spots. Analysis at CCI identified the presence of copper, nickel and chlorides in the corrosion products.
Metal objects that typically require enhanced protection are listed below, along with preventive conservation strategies for each. Means of implementing these strategies are discussed in Microenvironments.
- Chloride-contaminated iron and its alloys (e.g. marine and archaeological objects, industrial machinery contaminated with outdoor dust or road salt deposits): keep as dry as possible (0–10% RH) using desiccants in tightly sealed enclosures made of a low moisture permeability material. If actively corroding (like the object shown in Figure 45), an anoxic environment (using specialized barrier films and an oxygen absorber) with a desiccant is often the most effective strategy.
- Chloride-contaminated copper alloys (e.g. objects of archaeological or marine origin): use airtight enclosures (e.g. containers or bags) with a desiccant so as to maintain the RH as low as possible. Corrosion risk lowers significantly if the RH is maintained below the threshold of 42% (Rimmer et al. 2013). Anoxic environments with desiccant are also an effective option.
- Silver, particularly if polished: handle with gloves, ensure that no dust or contaminants are deposited on the surface and enclose the clean object within a sealed airtight bag or another type of enclosure. Include a material effective at removing sulfur-containing gases (e.g. tarnish-preventing fabrics, such as Pacific Silvercloth; Figure 46). Use a desiccant to create a dry environment. Ensure that no products used in constructing the enclosure or objects in the vicinity contain sulfur-emitting materials (such as rubber or some paints). Avoid frequent polishing; if tarnishing reoccurs, it is a sign that the silver needs a more enhanced level of protection (such as increasing the enclosure thickness [e.g. double bag], improving airtightness, installing filters specifically for that area, using more desiccant or using a sorbent more effective against sulfur gases).
- Polished copper and alloys: employ enhanced strategies as for silver, listed in the previous description.
- Lead (including old pewter and lead solder): avoid direct contact, containment within and proximity to materials that emit organic acid volatiles (wood and wood derivatives, acidic cardboard, paints, sealants, etc.). Protect lead objects from organic acid volatiles normally present in the ambient air by placing them in airtight enclosures made of safe materials (e.g. acid-free matboard, metal, glass, safe plastics, wood sealed with a barrier film [Marvelseal]). If needed, enhance protection using activated charcoal. If paints cannot be avoided in the room housing lead objects, use a latex paint and air out well beyond the minimum four days (if possible, for several weeks), and protect the lead objects using enclosures with activated charcoal.
- Metals exposed to pollutants or dust: if pollutants or dust in certain rooms or areas are high and it is not possible to either eliminate their source or to lower their levels sufficiently using ventilation or other building or room-level means of control, then use sealed enclosures to create a sheltered microenvironment around the metal objects at risk. Further protection is possible by using desiccants and sorbents within the enclosures. If an object is dusty or soiled, consider whether dusting or cleaning is possible or advisable, and contact a conservator for guidance.
- Valuable items for which even small amounts or slow rates of corrosion are deemed unacceptable: provide optimal protection against RH, dust and pollutants using airtight enclosures and a desiccant, and a sorbent tailored to the metal involved (e.g. tarnish-preventing fabric for silver, activated charcoal for other metals).
- Composite objects with a metal component actively corroding: if appropriate and possible, separate the metal from the rest of the object (e.g. a metal sword can possibly be separated from its scabbard made of organic materials) and provide the metal with an improved, lower RH. An alternative option is to store the whole object in a sealed anoxic environment while maintaining the RH at normal ambient levels (around 40–50%, as lowering the RH would harm the organic components). The oxygen absorber, which removes the oxygen, should stop most corrosion reactions, often even those of salt-contaminated iron or steel. Otherwise, use conditioned silica gel to keep the RH at the best compromise value for the needs of the object's metal and organic parts.
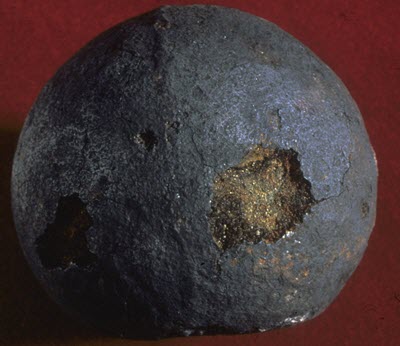
© Government of Canada, Canadian Conservation Institute. CCI 129955-0013
Figure 45. Handling this cannon ball caused a piece to fall off, revealing active orange corrosion due to the presence of chloride salts. Chloride contamination, prevalent in objects from a marine environment, causes a very destructive form of corrosion. Storage and display in a very dry environment (e.g. below 20%) will slow the reaction. Chemical treatment is necessary to further stabilize the object.
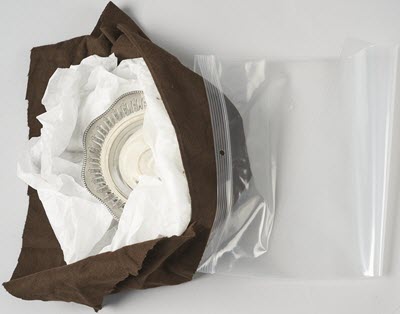
© Government of Canada, Canadian Conservation Institute. CCI 125773-0069
Figure 46. Protecting a silver object by wrapping it in acid-free tissue paper and a tarnish-preventing fabric (e.g. Pacific Silvercloth), then sealing it in a zip-lock bag.
Document the condition of the metal objects in the collection, and monitor the objects regularly. In particular, document the extent of corrosion present, and monitor any outbreak of corrosion. Photographs can be very useful. This will provide a means of verifying whether the control strategies adopted against corrosion work effectively. If problems are identified, proceed to correct the conditions or to enhance the level of protection specifically for the objects requiring it. Train staff to recognize problems and have a reporting mechanism to ensure that issues are documented and promptly addressed.
Microenvironments
The most commonly applied solution to protect metal objects at risk of corroding is through the use of microenvironments. A microenvironment is an isolated, sealed space separate from the rest of the room and within which a distinct environment is maintained, aimed at better preserving the metal object enclosed within that space. A microenvironment is created through the use of an enclosure (a container made of a barrier material assembled with tight seals) in which is included one or more specialized products (e.g. a desiccant to lower the RH, a gas sorbent to capture certain pollutants or an oxygen absorber to create an anoxic environment which will arrest oxidation). Components needed to create a microenvironment are further described below.
Enclosures
An enclosure is any type of physical structure that completely encloses and isolates an object from the rest of the room (e.g. bags, boxes, storage cabinets or display cases; Figures 47, 48 and 49). Enclosures are most effective when made of good barrier materials and assembled with tight seals. Placing metal objects into enclosures provides protection against several threats, such as:
- Physical forces: enclosures with padding, be they designed for individual objects or made with separators for multiple objects, have the advantage of preventing objects from touching or accidentally bumping into each other during storage and handling, and of inhibiting physical damage such as nicks and scratches as well as possible spots of galvanic corrosion.
- Dust, soiling, fingerprints and salt aerosols: enclosures will provide protection from all of these threats, although some ingress of dust and aerosols will occur unless the enclosures are airtight.
- Gaseous pollutants: enclosures can provide significant benefits against gaseous pollutants, even simple options such as sealable polyethylene bags (Figure 48). In areas where the external air is polluted, the 100–10–1 rule of thumb can be used to estimate the benefits of using one or two protective envelopes. For example, if there are 200 ppb of nitrogen dioxide outside, the level inside a room in a building will typically be 20 ppb and the level inside a sealed enclosure (tight display case, sealed bag) will be 2 ppb. An enclosure provides protection only if, within it, there is no internal source of pollutant (e.g. no emissive product used to make the enclosure and no emissive object stored with the metal object [consult Safe storage and display products]). Pollutant protection can be further enhanced using sorbents (outlined in Pollutant sorbents).
- RH: an enclosure alone provides some limited effects against unfavourable ambient RH conditions. Depending on the material it is made of, it may shield the object to some extent against high spikes in RH and short-term fluctuations. However, the low RH environment that sensitive metals require is only achieved by adding a desiccant (consult Desiccants). Airtight materials with low moisture permeability should be used to optimize performance.
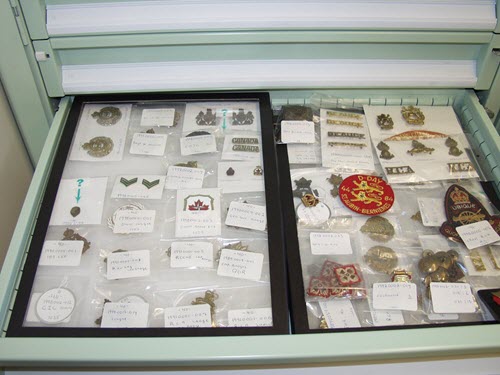
© Government of Canada, Canadian Conservation Institute. CCI 125773-0187
Figure 47. Example of good storage for metals. A baked enamel metal cabinet is stable and non-emissive. Objects are bagged to prevent contact, which could cause galvanic corrosion as well as nicks and scratches. Objects rest on a foam liner used as padding.
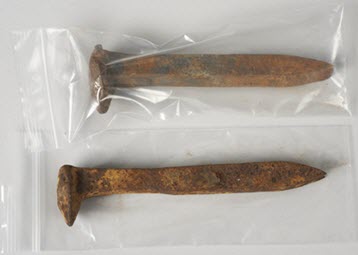
© Government of Canada, Canadian Conservation Institute. CCI 125773-0067
Figure 48. Simple zip-lock bags are an easy and economical way of reducing corrosion risks caused by external sources of pollutants. They also protect from fingerprints, dust and other contamination. Squeeze out the excess air from the bag when sealing.
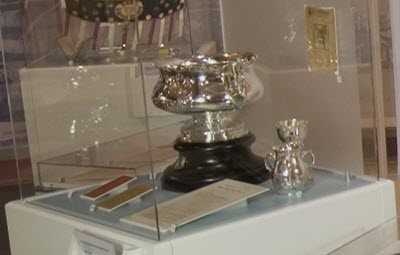
Artefacts on display: Pair of Skates – Canada's Passion for Skating, 2006. Canadian Museum of History, IMG2009-0363-0017-Dm (detail)
Figure 49. Display cases are most frequently used to protect silver objects from ambient air (pollution, dust, moisture) on exhibit. A tray hidden under the base of the vitrine is filled with conditioned silica gel to reduce the RH levels inside the case. Activated charcoal or other types of sorbents that capture gaseous sulfur compounds can also be included.
How effectively an enclosure protects against moisture and pollutants depends on the type of barrier material used (more specifically, on the material's permeability coefficients to water vapour or to the pollutants it must guard against), on the barrier material's thickness and on the tightness of the enclosure assembly seals. Protection is enhanced by multiplying the barrier layers, e.g. keeping objects wrapped in several layers of acid-free tissue and doubling the enclosures (double plastic bag, or a plastic bag within a box or vice versa), or by using bags and closed boxes within closed cabinets. Adding layers increases the shield effect, especially against dust and external pollutants.
Disadvantages of enclosures are the costs involved, the time it takes to enclose large collections of objects and, if desiccants or sorbents are used, the restricted access to the object (a sealed environment is needed to preserve the conditioned environment within the enclosure).
Enclosure materials
It is important that no enclosure material emits corrosive volatiles (consult Safe storage and display products). The following are some common options that have at least some barrier properties.
- Polyethylene bags: sealed polyethylene bags are an economical option against dust and pollutants in a general way and can also mitigate, to a limited degree, the effects of sudden large RH fluctuations or short-term damp. One advantage of polyethylene is that it can be heat-sealed to create an airtight seal. However, polyethylene bags are not efficient in maintaining a low RH environment with desiccants because the polyethylene (here, low-density polyethylene [LDPE]) is a weak water vapour barrier material over the long term, and most bags provide only a thin barrier layer as compared to the wall thickness of a solid tight-fitting (e.g. gasketed) plastic box. Performance is improved by using thick-grade polyethylene sheeting or thicker-walled bags (freezer bags) and/or by doubling the layers. Some commercially available polyethylene sheets and bags have a limited lifetime, the plastic becoming brittle and tearing after 5–10 years; however, food-grade LDPE bags are probably more stable than other types. Note that because the anti-blocking and slip agents inside the bag (which prevent each side of the bag from sticking to one another) can scratch silver, wrap silver objects first in acid-free tissue paper (Figure 50).
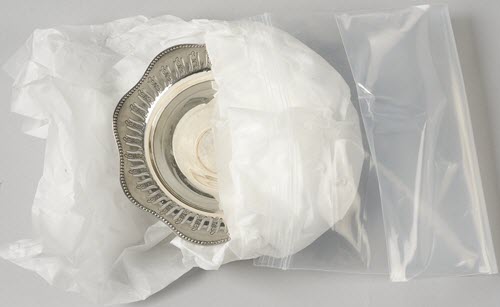
© Government of Canada, Canadian Conservation Institute. CCI 125773-0068
Figure 50. Wrap silver in tissue paper before sealing inside a polyethylene bag.
- Clear polyester film [poly(ethylene terephthalate) (PET), Melinex, Mylar] bags: a sheet of PET plastic is 100 times less permeable to hydrogen sulfide (H2S) gases than a sheet of LDPE plastic (Tétreault 2003, p. 135). PET bags or wrapping are thus useful to protect silver objects in storage (Figure 51). A disadvantage is that it cannot be heat-sealed.
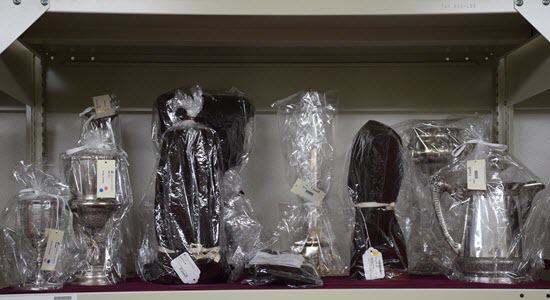
Photo Canadian Museum of History, Rebecca Latourell, IMG2018-0026-0001-Dm
Figure 51. Silver objects wrapped in PET (Melinex, formerly called Mylar). Some are first protected with a layer of tissue paper and then covered with brown tarnish-preventing cloth inside the plastic wrap.
- Low permeability laminated barrier films: these laminates are designed to be virtually impermeable to gases, water vapour and oxygen. Sheets can be heat-sealed together to make bags with air-tight joins. Metal foil laminates (usually made of an aluminum core with a plastic layer on each side, e.g. Marvelseal) are generally the most effective barrier material, but they have the disadvantage of not being transparent. Some specialized plastic laminates (e.g. Escal films) are virtually as effective and are transparent — but they are also expensive. Bags made of these film materials provide the best possible protection against the ingress of water vapour, oxygen and pollutants.
- Gasketed containers: these commercially available containers (e.g. Lock & Lock food containers) are made either entirely of fairly thick polyethylene plastic (and are milky clear) or of a clear glass bottom with a plastic lid. Their lid is fitted all-around with a sealing gasket and has foldable fasteners on each side that lock onto the container's bottom, thereby creating a fairly tight seal (Figure 52).
- Polystyrene containers: these have the advantage of being crystal clear, but they do not close tightly enough to keep a low RH environment for long periods.
- Display case glazing (Figure 49): for display cases that need to maintain their own microenvironments, glass is required since acrylic sheeting (Plexiglas, Acrylite) is not sufficiently impermeable to water vapour to maintain a low RH environment for long periods.
- Wood and wood products: these are permeable to water vapour, unless they are sealed. Appropriately sealed wood surfaces also ensure a non-emissive internal environment. Conservation-safe options include using appropriately pre-sealed wood products, such as high- or medium-density plywood overlay panels, or using any wood product that is heat-sealed with plasticized foil (Marvelseal).
Airtightness and quality of seals
Enclosures can maintain microenvironments only if their seals are airtight: they then block air infiltration from the outside environment. In the case of soft packaging like polyethylene or Escal bags, they must be sealed well enough so that, when squeezed slightly, one can feel the resistance of the trapped air. Generally, the best seals are made by heat-sealing; zipper-type seals or those made by folding and using adhesive tape may not be as tight. Containers with locking lids or compression seals can also achieve fairly good airtightness. For display cases and storage cabinets, achieving low air infiltration means minimizing holes and cracks (any crack or hole should be so tiny as to be difficult to see with the naked eye), plus having joints and gasketing close-fitting enough so that a normal sheet of paper cannot be slipped into any of the joints. Typically, constructing tightly sealed display cases requires special design considerations in order to ensure that their seals are sufficiently tight to maintain an air exchange rate of one per day, which is the maximum allowed to sustain a low RH microenvironment (Tétreault 2003, p. 48). Consult the vast literature on airtight display case designs that can be used to protect metal objects on display, for example Rimmer et al. 2013.
Temperatures must remain constant in order to avoid affecting the RH inside an airtight enclosure. Remove excess air if possible (e.g. squeeze out excess air from a collapsible bag) and do not place the enclosure near sources of cold, since cold temperatures would cause an RH increase on the inside, which is to be avoided for safeguarding metals. Keep the enclosure at least 10 cm away from an exterior (cold) wall or floor, or provide insulation (Tétreault 2003).
Desiccants
Using desiccants is the best way to create a dry environment (30% or lower) that is ideal for metals. Desiccants, such as desiccated silica gel or other similar products (Desi Pak, ProSorb), absorb moisture from the surrounding air. Hence, when they are added within a sufficiently well-sealed enclosure, they create low RH environments within it (Figure 52).
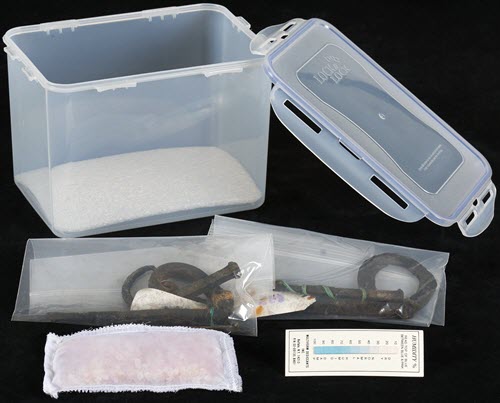
© Government of Canada, Canadian Conservation Institute. CCI 126258-0001
Figure 52. To slow down corrosion, these iron objects are wrapped within zip-lock bags, then placed inside a gasketed plastic box containing desiccated silica gel at the bottom. A pouch containing desiccated silica gel and an RH monitor card are placed on top.
When using desiccants:
- Investigate the differences between various products; some products achieve higher performance than others within a targeted RH range or are simpler and more convenient to use (like pre-bagged desiccants, such as Desi Pak).
- The quality of the enclosure (barrier material and seals) plays at least as important a role as the desiccant does in maintaining the low RH within the enclosure.
- Use sufficient desiccant for the volume of air enclosed. As a minimum, use the amount recommended by the manufacturer, but consider increasing it (for example, double, triple or even quadruple it) to reduce the maintenance frequency. Because bags are flexible, a bag enclosure makes it possible for the user to evacuate most entrapped air, thereby reducing the amount of desiccant required to control the air volume. However, the water vapour permeability of the bag material itself must also be considered (e.g. use Escal bags; even thick, double polyethylene bags are usually too permeable to work with desiccants).
- Ensure that the desiccant is suitably preconditioned (follow manufacturer's instructions), and recondition periodically to maintain the low RH environment within an acceptable range. Usually, heating silica gel at about 100ºC for 8–10 hours totally removes its adsorbed water: the silica gel is then desiccated and ready for use to create an RH close to 0% within a sealed enclosure. Because no enclosure is perfectly impermeable, with time the RH will drift upwards. Decide on the RH range that is acceptable for the object (e.g. between 0 and 30% RH), and plan for having a detection mechanism to know when the upper threshold has been reached, which means that maintenance is required. Investing in high-quality enclosure materials that make good seals and providing more desiccant within the air volume than the minimum required will help extend the system's performance time span and reduce the maintenance frequency.
- Make sure there is sufficient air circulation between the desiccant and the air around the object. With regards to display cases, this has design implications. Typically, the base of the vitrine has holes or gaps (hidden under a fabric) that allow for sufficient air circulation from a tray full of desiccant underneath. Plan for direct access to the desiccant tray located in the base of the display case.
- Monitor the RH within the enclosure using a detector close to the object. This is needed to ensure that the desiccant achieves and maintains the RH level sought. For objects in storage, RH indicator cards in transparent enclosures are convenient for this purpose (Figure 52).
- Avoid desiccants that contain lithium chloride, which can cause metals to corrode if in direct contact. Also avoid older silica gel that contains the blue indicator cobalt chloride, since it might be carcinogenic (consult Conserve O Gram 2/15 Cobalt Indicating Silica Gel Health and Safety Update [PDF format, 224 KB]). Alternatives include Sorbead Orange desiccant.
Examples of the use of tight enclosures with desiccants are provided under Preventive care measures for the Birks silver collection at the National Gallery of Canada and Caring for archaeological collections – Dry storage for corroding iron objects.
Anoxic environments
An anoxic environment, in which the oxygen is removed from the object's surroundings, is very effective in arresting corrosion and, in the case of extreme corrosion (e.g. chloride attack of iron), is the most effective solution. Specialized products are required, as discussed below.
- Suitable low-oxygen permeability barrier films, such as Marvelseal foil laminate or Escal transparent barrier film, can be used to enclose the metal object, along with oxygen scavengers, such as RP products (Figure 53). These materials are specifically manufactured for this purpose. An example of their use is discussed under Using an anoxic atmosphere to save the Ferryland Cross. An oxygen detector (e.g. AGELESS-EYE; Figure 54) may be added to signal when the oxygen absorber needs to be changed; however, the lifetime of the AGELESS-EYE itself is short (e.g. typically six months).
- AGELESS Z is another oxygen scavenger used in conservation. It is not effective in very dry conditions and, therefore, is not suitable for creating dry microenvironments for chloride-contaminated archaeological iron.
- Some oxygen-absorbing products are available with or without a desiccant, e.g. the RP-A (yellow) sachets include a desiccant, while the RP-K (green) ones do not (often called moisture-neutral). To arrest metal corrosion, it is more effective to eliminate both the water and the oxygen within the enclosure with RP-A; however, for composite materials, use the RP-K oxygen absorber so as to keep the enclosed RH at ambient levels, which is better for organic components.
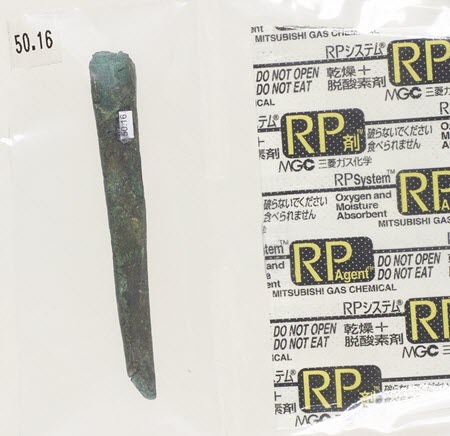
© Government of Canada, Canadian Conservation Institute. CCI 123028-0045
Figure 53. An Inuit copper chisel from an archaeological site in northern Canada is stored in a sealed Escal bag with an RP-A sachet (oxygen absorber and desiccant).
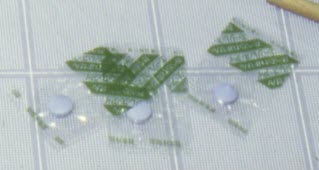
© Government of Canada, Canadian Conservation Institute. CCI 122641-0003
Figure 54. Three samples of AGELESS-EYE oxygen detector (blue capsule) in their plastic wrapper.
A disadvantage of wrapping and sealing objects for anoxic storage is the lack of physical access. Note that, whenever the bag is opened for access, the object is exposed to oxygen and not protected from further corrosion, and the anoxic environment is lost. It is then necessary to replenish the bag with a new quantity of oxygen absorber before resealing it.
Pollutant sorbents
Using pollutant sorbents (products that absorb or adsorb one or more pollutants, also sometimes called scavengers) within enclosures increases the level of protection against gaseous pollutants. The amount of sorbent required varies depending on the sorbent type and situation. Sorbents become exhausted and need to be changed or regenerated after a certain period, depending on the emission rate of the internal source of pollution or on the rate of infiltration of external pollutants. To be efficient in reducing the level of pollutants, the sorbent must cover a large surface area within a display case, storage cabinet or any type of enclosure. Consult the manufacturer's information or Tétreault (2003) for further information. There are typically two format types for these products: those in bead or granular form and those where the sorbent is incorporated within a fabric.
Bead and granular
- Zinc oxide catalyst: it has very good sorption performance for sulfur-based compounds such as hydrogen sulfide and carbonyl sulfide. It cannot be regenerated.
- Activated charcoal: it is probably the most commonly used sorbent in museums. Its sorption performance is good for acetic acid, hydrogen sulfide, sulfur dioxide and nitrogen dioxide; performance is medium for formic acid and ozone. By using 500 g of activated charcoal in the 6–14 mesh size range (e.g. Fisher Scientific activated carbon charcoal or Fisher granular activated carbon [coconut charcoal]) per cubic metre, the level of pollutants inside the enclosure should reduce by a factor of 10 as compared to the level in the room, provided that the enclosure is well sealed (good airtightness) and that it does not contain internal emissive products. This quantity should last one year. Activated charcoal can be regenerated by heating at about 120ºC for approximately 12 hours. It is often practical to use it enclosed in long thin snake-like pouches, because these offer a large surface area in contact with the surrounding air and thus maximize pollutant retention. The pouches should be made of a fabric that can withstand heating so that the whole pouch can be heated when regenerating the charcoal.
- Activated alumina impregnated with potassium permanganate: it has very good sorption performance for hydrogen sulfide; good performance for sulfur dioxide, acetic acid and ozone; and medium performance for nitrogen dioxide. It cannot be regenerated. Its colour changes from pink to brown when exhausted.
Note: Activated charcoal and activated alumina products can also be impregnated with other active compounds such as potassium carbonate, potassium hydroxide or sodium bicarbonate for better sorption or for increased efficiency in trapping various types of pollutants.
Fabrics
- Activated charcoal cloths: these are convenient since they are ready to use as linings and wrappings (no need to create pouches for the activated charcoal granules); however, their performance is more limited. They are good for acetic acid and ozone; performance is medium for sulfur dioxide and poor for hydrogen sulfide and nitrogen dioxide.
- Tarnish preventing cloths (e.g. Pacific Silvercloth): these are a good option for silver as they are designed to protect silver from tarnishing. Embedded in the cloth are tiny silver particles that are very reactive to tarnish-producing pollutants. Its most effective use is by wrapping a silver object entirely within it so that the cloth's silver particles sacrificially react first with any outside gaseous sulfur compounds. To err on the side of caution, first wrap the object in acid-free tissue paper, then wrap it in a double layer of this cloth and seal it within a tight-fitting enclosure (container, display case, etc.; Figures 55a, 55b and 55c).
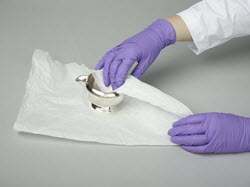
© Government of Canada, Canadian Conservation Institute. CCI 125773-0195
Figure 55a. First, wrap each silver object in acid-free tissue paper.
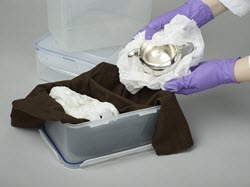
© Government of Canada, Canadian Conservation Institute. CCI 125773-0188
Figure 55b. Once fully wrapped in tissue paper, the objects are then wrapped in Pacific Silvercloth and placed in a gasketed plastic box.
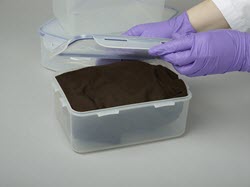
© Government of Canada, Canadian Conservation Institute. CCI 125773-0192
Figure 55c. The box is sealed. Label the box before storing to facilitate retrieval.
Active mechanical systems
A more costly solution to the passive systems (microenvironments with desiccants) is to use active mechanical systems that can achieve very low levels of dehumidification (desiccation). These systems are called "active" because they need a constant source of power for the machinery to work and maintain the required RH level; thus, a disadvantage is that they will fail during power outages. Some systems are designed for museum display cases (e.g. CCI low RH control modules), others, for a whole room (e.g. vault). They can be set for whatever conditions are required (e.g. typically, for metals, the setting is an RH below the threshold of 30%). Using such systems requires space considerations to accommodate the unit within the display case base or within the room, as well as design considerations to hide the electrical power connections. The dehumidification unit should incorporate automatic drainage (if applicable) to reduce the otherwise frequent maintenance required. The area receiving the mechanical system's climate-controlled environment (e.g. a display case, a vault, a room) should be airtight to reduce leakage. A discussion on an active low RH system for a vault is provided in Preventive care measures for the Birks silver collection at the National Gallery of Canada.
Interleaf barriers
If metal elements that are part of a composite object corrode, the intimate contact of the metal and corrosion products can be harmful to the other components of the object. Sometimes, the combination of materials on the object inherently causes corrosion (Figures 56a and 56b). Removing the corroding metal element is not always possible because of the construction of the object or because removal would affect the original integrity of the whole piece. A simple beneficial measure, which at least protects the organic components, is to insert an isolating interleaf barrier to prevent the corrosion from staining the materials it is in contact with. Metal ions transferring onto organic materials can also further their degradation (catalysis of oxidation reaction of cellulose and proteinaceous materials).
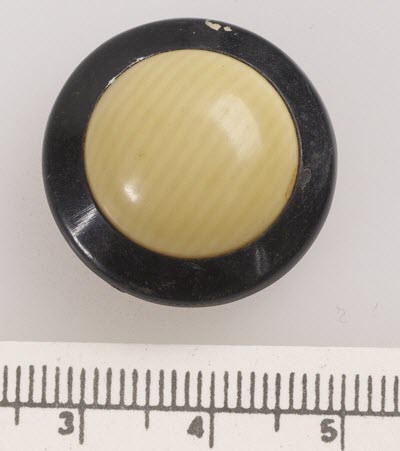
© Government of Canada, Canadian Conservation Institute. CCI 97196-0017

© Government of Canada, Canadian Conservation Institute. CCI 97196-0016
Figures 56a and 56b. Cellulose nitrate button, front and back. The steel back (Figure 56b) is actively corroding because of the presence of corrosive nitrogen oxide gases emitted from the cellulose nitrate. In this case, removing the metal from the rest of the button is not an option. If this button were on a costume, the corrosion products would stain and degrade the fabric. A simple solution is to insert a barrier interleaf layer between the button and the fabric.
In the case of copper or its alloys that are part of a composite object, to prevent their corrosion when they are in direct contact with a material that contains fats, oils or waxes (e.g. leather), insert a barrier film between the metal and that material. The film must remain totally removable whenever necessary. For example, slip an interleaf of clear polyester film (Melinex) between the two (Figures 57a and 57b). Consult a professional conservator for advice on cleaning.
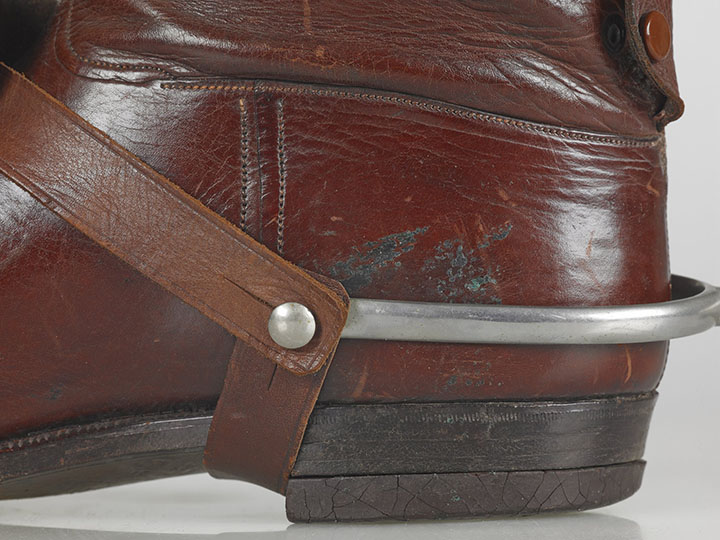
© Government of Canada, Canadian Conservation Institute. CCI 124883-0014
Figure 57a. Detail of a leather boot owned by former Governor General Georges Vanier (from the collection of the Musée Royal 22e Régiment, Québec). The green waxy products on the leather close to the spur are corrosion products resulting from the metal in contact with the leather.

© Government of Canada, Canadian Conservation Institute. CCI 124883-0019
Figure 57b. After surface cleaning, to prevent direct contact and future corrosion, an interleaf made of clear polyester film (Melinex) was slipped through a small strap onto the spur and placed in between the leather and the metal.
Coatings
Organic coatings on metals (oils, waxes, varnishes, lacquers, etc.) are not impervious to oxygen and water vapour, and it is only a matter of time before these gases penetrate the coating and corrosion is initiated (Figure 58). This is why coatings applied as a protective layer fail (especially outdoors) and need to be reapplied on a regular basis. The application of a coating tends to be an insufficient remedy. Instead, it is preferable to deal with the real issue of the object being in an inhospitable environment (a high RH) and to find a solution that will permanently solve the problem. In general, coatings are not recommended because of the difficulty of applying them evenly (tiny imperfections may initiate corrosion or pitting) and of removing them when, eventually, it is necessary to do so.
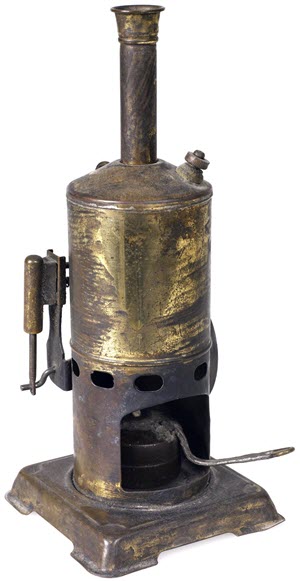
© Government of Canada, Canadian Conservation Institute. CCI 129955-0014
Figure 58. The surface of this toy steam engine illustrates the fate of lacquers over time—the mostly dark areas are where the original lacquer has failed and a patina developed. The shiny gold-yellow areas are still intact because the original lacquer was brushed on in a particularly thick layer in these areas.
However, applying protective coatings to vulnerable objects may, in some instances, have net benefits; for example, they may be considered for metal objects on open display or those that are designated to be handled by visitors. Three types of coatings may be considered:
- Lacquer: it may be appropriate to apply a lacquer under some conditions. Types of lacquers include cellulose nitrate lacquers (e.g. Frigiline and Agateen, which have been used on silver) and thermoplastic acrylic resins (e.g. Paraloid B-72, occasionally used for iron or copper). Protective lacquer films can start breaking down and allow local corrosion to take place, giving an uneven and unsightly surface (Figures 56a and 56b). A review of the use of cellulose nitrate lacquers on a collection of silver objects on open display in a historical setting found that the lacquers can be effective up to 25–30 years but may fail within 10–15 years, especially if the object's shapes (which the lacquer must perfectly and evenly follow) are complex; therefore, it is recommended to reassess their effectiveness every 5–10 years (Pouliot et al. 2014). Further advice about lacquers can be found in CCI Notes 9/3 The Cleaning, Polishing and Protective Waxing of Brass and Copper and 9/7 Silver — Care and Tarnish Removal
- Wax: In cases where some protective coat is needed, a wax can be applied. A microcrystalline wax paste can be gently applied and warmed with hot air to spread it evenly. However, a wax coating may not be aesthetically desirable on highly polished metals. Also, wax applied to the rough, porous surface of archaeological metals is extremely difficult to remove. For advice on cleaning and waxing consult:
- CCI Note 9/3 The Cleaning, Polishing and Protective Waxing of Brass and Copper
- CCI Note 9/6 Care and Cleaning of Iron
- CCI Note 9/7 Silver — Care and Tarnish Removal
- Conserve O Gram 10/2 Caring for Silver and Copper Alloy Objects (PDF format, 450 KB)
- Light oil: Bare ferrous metals, especially those that are handled frequently, can benefit from a coating of light machine oil. Apply sparingly, then rub the surface of the object well with a soft cloth to distribute the oil evenly and remove excess. The procedure is detailed in CCI Note 9/6 Care and Cleaning of Iron.
Polishing
Polishing metals is a customary procedure for cleaning personal items; however, transferring domestic or commercial polishing techniques to museum objects can result in much damage. It is important to realize that:
- A tarnished surface is stable and does not need to be polished. Moreover, the tarnished surface is somewhat protective, reducing the metal's overall tarnishing rate. In comparison, a polished surface is more reactive than a tarnished one and will be prone to re-tarnishing.
- Polishing is abrasive in nature: some of the original surface is always removed. More abrasive damage will occur with frequent or vigorous polishing or if hard abrasive compounds are used. Plated objects are especially vulnerable to damage by polishing: the plating is very thin and risks being removed (Figure 59).
- Polishing pastes and compounds can be difficult to clean off completely from the metal's surface as they can lodge into small recesses in the design or under rivets.
- Polishing compounds are often acidic or alkaline. If residues remain on the metal, they will attack the surface (as shown in Figures 17 and 39).
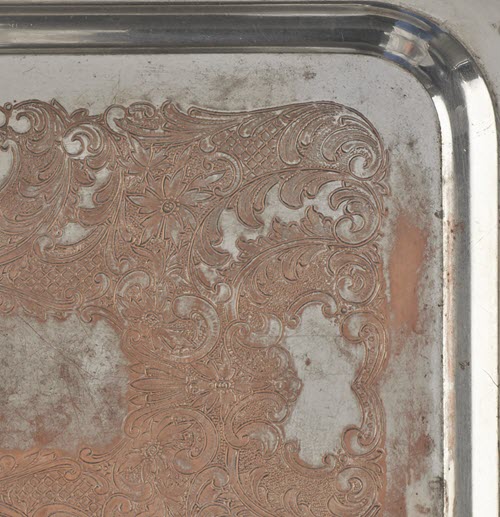
© Government of Canada, Canadian Conservation Institute. CCI 120260-0318
Figure 59. Detail showing the loss of the silver layer from a silver-plated copper tray that was caused by repeated cleaning with an abrasive polish. There is very little silver left on the highlights of the design: the pink areas are the exposed copper core.
The following are three basic guidelines concerning polishing:
- Avoid polishing in general; polishing should occur only in rare circumstances.
- Polish only using appropriate methods and products. Remove dust, dirt and grease first to make polishing easier and to prevent hard dust particles from also acting as an abrasive. Use the softest polish abrasive for the job, e.g. a paste of precipitated calcium carbonate and water (consult Tarnished silver: the treatment is clear). Wash carefully to remove all polish residues.
- Prevention is key. Prevent tarnishing from occurring by reducing the pollutants in the object's environment so as to minimize the need for polishing. Unless prevention measures are in place, the metal surface will re-tarnish shortly after being polished.
For further advice on polishing, consult CCI Note 9/7 Silver — Care and Tarnish Removal and Conserve O Gram 10/2 Caring for Silver and Copper Alloy Objects (PDF format, 450 KB).
For more preservation strategies on water and RH, consult Agent of deterioration: water and Agent of deterioration: incorrect relative humidity.
For more preservation strategies on pollutants, consult Agent of deterioration: pollutants.
Other agents of deterioration
The following agents are risks to all objects in collections, including metal objects. Consult Agents of deterioration for a broader selection of strategies that can be applied for each specific agent.
Physical forces
Physical forces can damage metals, causing dents, distortions and even breakage (Figure 60) if excessive forces are applied. Scratches and abrasion are other common forms of physical damage (consult, for example, Polishing). Soft metals (gold, silver, lead, copper) are especially vulnerable to dents, scratches and abrasion. Archaeological metals are often brittle due to the deterioration they have undergone during burial, so they can be prone to cracks and fractures.
Preventive conservation strategies to prevent physical damage include:
- Identify metal objects most at risk of physical damage and focus preventive actions on these.
- Provide containers and padding as appropriate for the fragility of the objects.
- If several objects are placed together within a box, a tray or a drawer, separate them with padding to prevent their contact and the risk of nicks and scratches when they are moved or when the drawer is opened. Other options include using custom-made carved nests (Figure 61) or immobilizing objects onto a padded surface using twill-tape ties.
- Provide mounts or bases for objects that are unstable, unbalanced or top-heavy (objects with a high centre of gravity).
- Handle objects in their boxes and storage trays carefully using appropriate techniques and equipment.
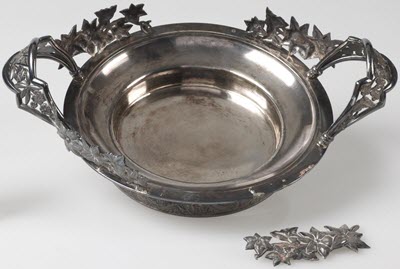
© Government of Canada, Canadian Conservation Institute. CCI 121590-0001
Figure 60. A decorative silver bowl. One of the ornamental pieces of foliage that was soldered onto the bowl's rim is now broken off.
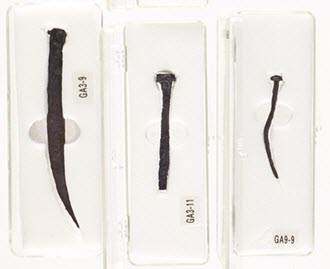
© Government of Canada, Canadian Conservation Institute. CCI 82540-0008
Figure 61. Thin fragile archaeological nails are nested within foam padding and stored individually in polystyrene boxes.
Thieves and vandals
Precious metals and valuable items (jewellery, coins and collectibles) are at risk of theft (Figure 62) and so require enhanced measures to prevent this.
Dissociation
Small metal parts, including functional items such as screws or nuts and bolts, may sometimes be loose or insecurely attached to an object. When the object is handled or moved, these parts could be at risk of detaching and possibly becoming dissociated from the object. Consult CCI Technical Bulletin 17 Threaded Fasteners in Metal Artifacts for advice on preventing dissociation and ensuring that small metal parts on objects are well preserved.
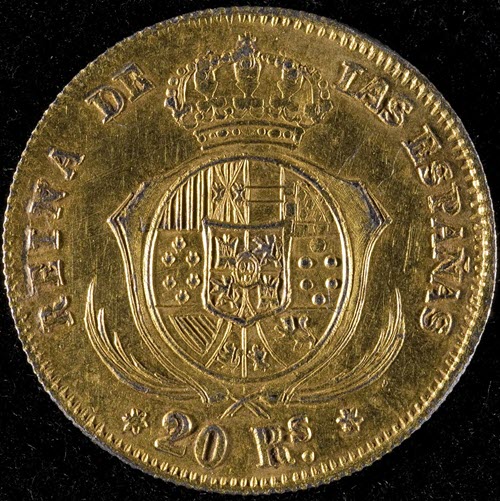
© Government of Canada, Canadian Conservation Institute. CCI 97889-0004
Figure 62. A historically counterfeited 1861 Spanish 20-reales gold coin. Rather than being pure gold, the coin is gold-plated over a platinum core.
Fire
Low melting point alloys—such as pewter or lead-tin solders—are especially at risk in case of a fire.
Incorrect temperature
Higher temperatures increase the rate of chemical reactions, including corrosion reactions (if other factors fostering corrosion are also present such as high RH). For example, for a given RH, iron will corrode twice as fast at 29°C than at 18°C.
As noted under Keep relative humidity levels moderate and avoid damp, temperature has a large impact on RH and needs to be controlled in order to properly manage RH levels. Consult Agent of deterioration: incorrect temperature for more details on how temperature affects RH.
Examples of preventive conservation practices
Tarnished silver: the treatment is clear
Lyndsie Selwyn
(Edited from text first published in CCI Newsletter 23, June 1999)
It must surely be a common problem. Old friends are coming for dinner and the silver candlesticks they gave us for a wedding present are about to be used for the first time in years. The relief of finally locating them quickly turns to dismay as we unwrap them and see... tarnish! Exposure to sulfur-containing gases has caused a thin film of silver sulfide to form on the surface, and the result is a dull lackluster finish (Figure 63). To restore the original brilliance of the silver, the sulfide film must be removed.
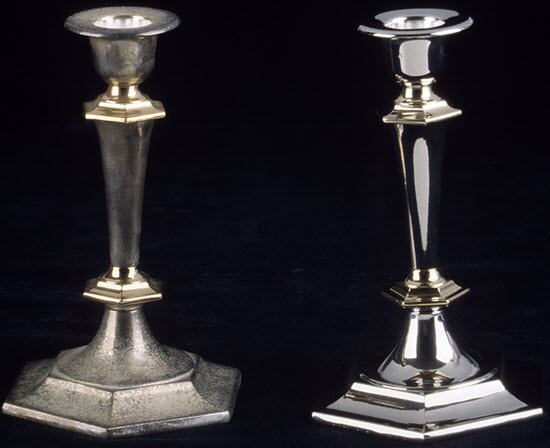
© Government of Canada, Canadian Conservation Institute. CCI 72776-0001
Figure 63. The author's wedding present candlesticks (silver-plated zinc with gold highlights), before and after polishing.
At the turn of the century an industrious homemaker published the following recipe for silver polish (Hiscox 1907): "The best polish for silverware—that is, the polish that, while it cleans, does not too rapidly abrade the surface—is levigated chalk [...]. The usual metal polishes, such as [...] finely ground pumice stone [...] cut away the surface so rapidly that a few cleanings wear through ordinary plating."
The 1907 opinion is still valid today. The only modification is the stipulation that the chalk be precipitated from solution rather than levigated (ground into a fine powder). This stems from the fact that precipitation gives better control of the particle size than grinding and avoids the large particles that can leave behind visible scratches during polishing (small particles also leave scratches, but if the particles are small enough, the scratches are invisible to the unaided eye). One reason for the enduring use of chalk is that it is a soft material (hardness about 3 on the Mohs scale). Harder abrasives such as pumice (hardness about 6 on the Mohs scale) remove more material with each stroke and so cause more damage: if polishes containing the harder abrasives (such as all-purpose metal polishes) are used on silver plate, they rapidly remove the entire silver layer, revealing the underlying base metal; if they are used on sterling silver, they can rub away delicate engravings. This is one case where time has simply polished the advice!
Preventive care measures for the Birks silver collection at the National Gallery of Canada
Doris E. Couture-Rigert
Chief Conservator
Conservation and Technical Research, National Gallery of Canada
Introduction
The National Gallery of Canada (NGC) started collecting silver as early as 1960 and had acquired a modest number of objects by the time it received, in 1979, a massive gift from the Henry Birks Collection of Canadian Silver that consisted of over 7000 pieces. Since then, the NGC has continued to actively collect silver objects by acquiring key works, carefully chosen to complete and balance the existing historic collection and to expand it into the 20th century. Although important American and European pieces have been acquired as well, the NGC is known for its outstanding Canadian silver collection, the largest in Canada, of which the Birks donation still today forms its substantial core.
Included in the Birks donation were a number of well-built wooden cabinets in which the collection was stored at Birks headquarters in Montréal. These wood cabinets, however, were far from being the ideal environment in which to store or display silver objects, which became quite evident in the form of a recurring need for silver cleaning. This posed a tremendous maintenance issue, considering the number of objects in this collection. Hence, the implementation of preventive conservation measures to reduce tarnishing was a pressing issue and, when planning began for a new purpose-built structure to house the NGC and its collections, the provision for new cabinets in a low RH storage vault, as well as new display cases, were identified as a high priority. Specifications were developed and implemented in 1988 with the move into the current landmark building in Ottawa, on Sussex Drive (Figure 64).
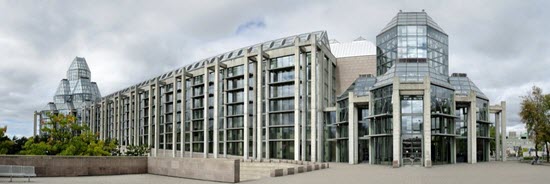
Photo © National Gallery of Canada
Figure 64. The National Gallery of Canada, Ottawa, Ontario, home to the Birks Silver Collection.
Environmental conditions at the National Gallery of Canada
To ensure a largely contaminant-free environment throughout the museum's gallery spaces and storage vaults, the NGC uses a complex air handling system. The air supplied to the building is prefiltered before it passes through an additional bank of filters that consist of pleated particle filters and gas filters (activated charcoal). The air sent through the filtering system is a mixture of outdoor air and recycled indoor air, its ratio changing depending on outdoor temperature and visitor density. To determine the optimal ratio, carbon dioxide and dew point sensors are strategically placed throughout the galleries. A reverse osmosis water filtration plant, which includes a UV-treatment process to kill microorganisms, is responsible for humidification and de-humidification of the building, providing 50 ± 3% RH in the summer, and 44 ± 3% RH in the winter, the transition obtained gradually over a 60-day period in the fall, followed by a reversed trend in the spring. The temperature is maintained at 21 ± 2°C year-round. The current system is a 2011 upgrade and is now fully automated and digitally controlled. Indoor air quality tests are performed on a regular basis to assess and monitor the performance of the systems output, ensuring that both particle and gaseous contaminants of the air throughout the museum and storage vaults are maintained within the permissible levels.
Creating an ideal environment for the preservation of silver objects
While the above-described environment is ideal for most types of artworks, silver requires further measures. Metal in general is most stable in low RH, and silver in particular requires enhanced dust and pollution control measures in addition to a low RH environment at a stable temperature in order to eliminate or drastically reduce the formation of tarnish (silver sulfide). This requirement is especially important for silver because, unlike other types of metals, the intended and desired appearance of silver is usually that of a bright (tarnish-free) surface. Where tarnish is not prevented, the repeated removal of thin layers of silver sulfide, aside from being a costly maintenance issue, will result in surface loss over time, which can become evident in the loss of definition throughout decorative surface work.
As a result, it was necessary to implement further preventive measures to protect the NGC silver collection within the museum's ambient storage and display environment through the use of microclimates.
Low relative humidity silver storage vault
When planning a separately controlled art storage vault, there are two approaches to consider: either the vault itself is conditioned as a microclimate or the cabinets provide the desired microclimate within the ambient environment of the room. Depending on the use of the collection, one may choose one system over the other. As the NGC silver collection is frequently accessed for study purposes, in-house installations, on-tour exhibitions and loans, it made most sense to condition the room itself. This allows for unhurried removal of art objects from the cabinets, as there are no worries of losing dry air from the cabinets since both the cabinets and the room are of the same conditioned air. In addition, this option allows the objects to be left out on the table, in some cases for several days, permitting individual pieces to be studied by curators and scholars while remaining in their ideal environment.
Hence, the silver and metals storage vault was purpose-built to the following specifications:
- Painted walls, ceiling and floor covering to be free of any sources of contaminants through appropriate material choices and time allowance for off-gassing.
- All access doors to the vault to be fitted with stable non-emissive gaskets effective at maintaining a sealed microclimate.
- Separate air supply and return air circuit conditioned to:
- 35% ±3% RH and
- 21 ± 2°C (same as elsewhere in the building).
- Elimination or reduction of gaseous and particulate atmospheric pollutants by means of activated charcoal and dust filters.
Note: When choosing the RH set point for a metal storage vault, one must consider the secondary materials that may be stored in this room. Many secular or sacral silver pieces have knobs, handles or other decorative elements made from hygroscopic materials, such as ivory and wood. An RH of 35% was chosen to accommodate such materials while still providing a dry environment for the metal; this has proven to be both safe and effective in preserving the NGC's silver collection.
Silver storage cabinets
The silver storage cabinets used in the vault are custom-built, made from steel with a powder coated baked polyester finish, which is non-reactive, solvent-free and emission-free. Large glass doors with minimal frames were chosen for optimal viewing of the cabinet's contents (Figure 65). For full access to the width of the cabinet, doors open a full 180° and lie flat against the adjacent cabinets (Figure 66). As the room is conditioned to 35% RH, the cabinets have vented backs for passive air exchange, allowing free air circulation between the room and the cabinets (Figure 67). The glass doors have no gaskets, but they are equipped with magnets to hold them closed before locking.
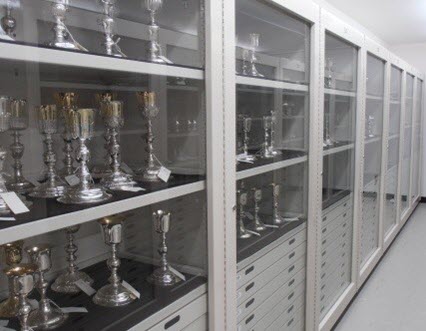
Photo © National Gallery of Canada
Figure 65. View inside the NGC silver storage vault showing a row of cabinets.

Photo © National Gallery of Canada
Figure 66. Silver storage cabinet with glass door fully opened and two drawers pulled out.
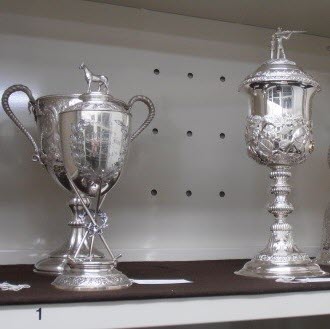
Photo © National Gallery of Canada
Figure 67. Vent holes on the back of each cabinet.
The cabinets are rather shallow (56 cm deep) to avoid having too many rows of objects per shelf. This allows easy viewing and locating of individual objects and makes their retrieval more straightforward and, therefore, safer.
To further reduce the chance of tarnish (i.e. silver sulfide formation), each shelf and drawer is lined with Pacific Silvercloth tarnish-preventing cloth (Figure 68) sewn over 3 mm thick white crosslinked, closed-cell polyethylene foam sheets (Nalgene).
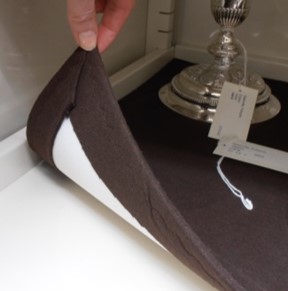
Photo © National Gallery of Canada
Figure 68. Pacific Silvercloth liners.
Silver display cases in the National Gallery of Canada galleries
Special display cases were designed to allow the safe exhibit of the silver objects, a standard type and a system type (with a motorized system that lifts the Plexiglas top). Both the standard type and the system type display cases successfully provide secure, stable and dust-free enclosures in which a desired microclimate can be easily achieved and maintained (Figure 69).
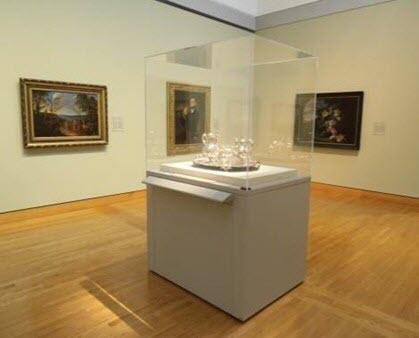
Photo © National Gallery of Canada
Figure 69. National Gallery of Canada silver display case.
The following are the general specifications of the NGC's silver display case design:
- Main body: medium-density fibreboard (MDF)
- Plexiglas (acrylic) top: 1/4-inch Plexiglas with fused, mitred joints along sides to reduce visibility of seam
- System cases: motorized lifting device for Plexiglas top, plus Plexiglas compartment within the base for the placement of controlling agents (Figure 70)
- Standard cases: manual lifting of Plexiglas top; controlling agents are placed under the deck or landscape blocks (blocks that serve to display objects at various heights within the case)
- High performance seal: located between base and Plexiglas top for the creation of a microclimate
- Outside surfaces finish: two-part epoxy spray paint for durability
- Inside surface finish, including deck and landscape blocks: interior-grade latex (water-based) paint with an acrylic or acrylic-urethane binder
- Air circulation: painted deck and landscape blocks are raised off the surface with 3 mm spacers to allow air circulation, while the fabric-covered version has perforated sides
When choosing a particular paint formula, selecting one with a low volatile organic compound (VOC) count (e.g. 10 g/l) is recommended for human health; however, low VOCs do not correlate with safe usage in relation to works of art. Many additives in paint are the source and cause of material deterioration, tarnish and corrosion. Therefore, it is recommended to consult the material safety data sheets under section 5, "Hazardous decomposition products" (consult The MSDS: A Basic Guide for Users - Canadian WHMIS Version for more information) when selecting a paint product, avoiding those that list silver-tarnishing compounds such as hydrogen sulfide, sulfur dioxide or carbonyl sulfide. The same applies in the selection of the MDF board, as some types of MDF contain a sulfur-based adhesive that can release harmful sulfur compounds.
Acrylic latex paints and two-part epoxy resin spray paints take approximately four days to cure and another three to four weeks before most VOCs have evaporated. Consequently, before installing any works of art, most particularly silver, the following minimum time allowance must be scheduled for the necessary off-gassing:
- For in-the-open well-ventilated surfaces, including walls, display platforms and pedestals: Seven days for lead, five days for silver and four days for all other metals or materials. A Mylar (Melinex) interface is placed between the object and display surface, unless the paint was off-gassed for a minimum of three weeks.
- For enclosed spaces such as display cases and vitrines: 28 days for lead, 21 days for silver and all other metals or materials.
The deck and landscape blocks covered with fabric require the following preparatory work:
- The MDF is first sealed with three coats of blond shellac or painted with acrylic latex paint, followed by three weeks off-gassing.
- All fabrics used for this purpose are tested for sulfur using sodium azide reagent (Daniels and Ward 1982; Thickett and Lee 2004) or the lead acetate test (Tétreault 2004). Each new order, even if it is the same fabric from the same supplier, is tested before use.
To create a low RH environment for silver, the highly efficient and economical desiccant Desi Pak is used, as it exceeds the moisture vapour adsorption of regular silica gel.
In contrast to a chemically synthesized sorbent, Desi Pak contains bentonite, a volcanic ash weathering product consisting mainly of montmorillonite clay, a naturally occurring mineral. While it is supplied in various forms and sizes, the eight-unit non-woven polyethylene (Tyvek) bag has proven to be well suited for our display cases, as it fits easily into the perforated Plexiglas compartments of the system cases (Figures 70 and 71) as well as under the deck or landscape blocks of the standard cases, where space is limited. Depending on the leakage rate of a given display case and the RH level sought, the amount of Desi Pak required varies. However, as a rule of thumb, if the case is well sealed, one or two eight-unit bags of Desi Pak are sufficient to desiccate one cubic meter of enclosed air. Placing small digital temperature and RH indicators inside the display case allows for easy monitoring.
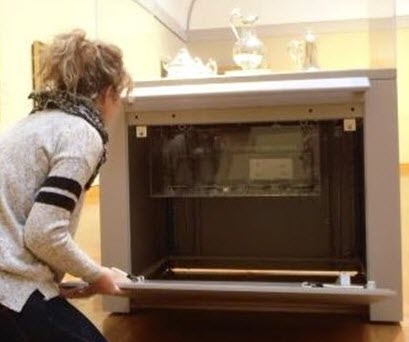
Photo © National Gallery of Canada
Figure 70. Compartment behind the trap door of a silver display case for the placement of controlling agents.
To adsorb gases that cause the formation of tarnish, activated charcoal is added to each display case (approximately 500 g or 12 cartridges per cubic metre) along with the desiccant (Figure 71). With this approach, the silver objects are maintained in a dry and pollution-free environment while on display.
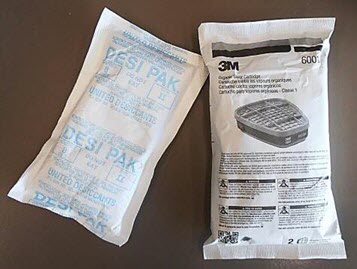
Photo © National Gallery of Canada
Figure 71. Controlling agents used in NGC's standard and system display cases for silver—desiccant (Desi Pak) and activated charcoal (in cartridge form).
These high performing display cases continue to be used in the European galleries. However, since June 2017, as part of the major redesign of the Canadian and Indigenous Galleries, which introduced a new aesthetic and reconfiguration, the silver objects are now shown in new high-tech custom-built display cases, such as free-standing, wall-mounted and inset-type vitrines (Figure 72). The powder coated steel and anti-reflective glass (Groglass Artglass AR Protect) construction provides a pollution-free environment with a superior clarity for viewing. Depending on the style, the controlling agents (desiccant and activated charcoal) are fitted into compartments situated either under or along the sides of the cases (Figure 73). The desiccant, in the form of Desi Pak, has been maintained in the same ratio as with the previous display cases, while the charcoal cartridges have been replaced with custom-sewn Reemay (non-woven polyester fabric) bags containing 4 mm pellet activated carbon charcoal (virgin coal) (Figure 74). The recommended quantity, based on an air exchange rate of 0.3 per 24 hours, is 500 g of activated charcoal per cubic meter of display volume, with an expected interval for replacement of three years. The motivation to change to charcoal pellets is that of cost-effectiveness, as some of our new cases are very large, requiring a large quantity of controlling agents for up to 8 cubic metres of display volume.
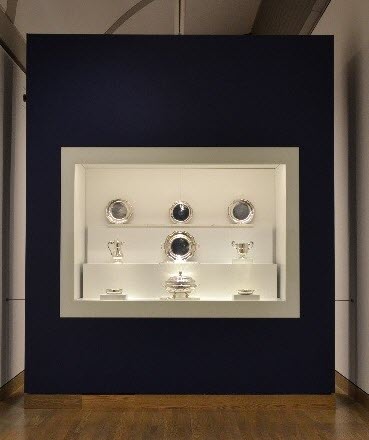
Photo © National Gallery of Canada
Figure 72. National Gallery of Canada's new silver inset display case.
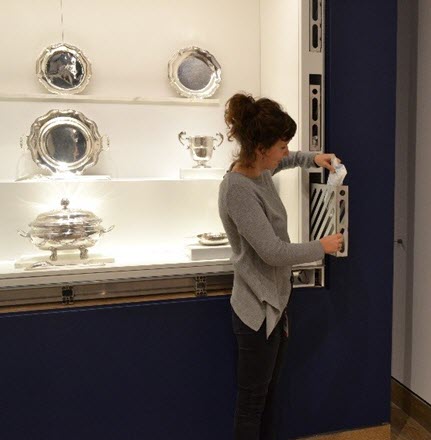
Photo © National Gallery of Canada
Figure 73. Compartment for controlling agents along the sides of the display case.
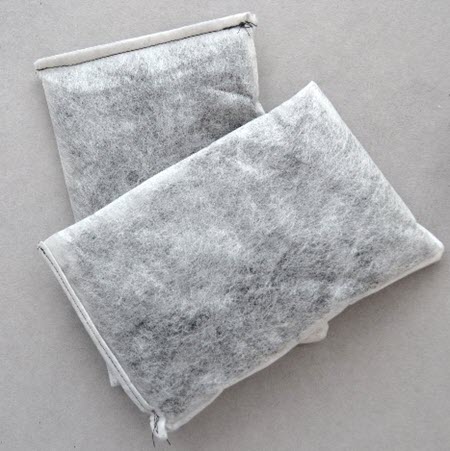
Photo © National Gallery of Canada
Figure 74. Custom-sewn Reemay (non-woven polyester fabric) bags containing 4 mm pellet activated carbon charcoal.
As time has shown, the Pacific Silvercloth liners in storage as well as the controlling agents (desiccants and activated charcoal) in the well-designed and air-tight standard and system display cases perform at full capacity up to 10 years before they need to be replaced. Together with the building's air filtration system and RH control, the environment created forms the basis of preventive care for silver. Consequently, in the course of the past 25 years, the need for cleaning objects from the NGC silver collection has become nearly obsolete, and maintenance needs shifted from very high to very low. Performance statistics continue to be collected with the new glass display vitrines, and similar results are expected.
Dry storage for corroding iron objects
Consult Caring for archaeological collections – Dry storage for corroding iron objects to learn how to create a dry microenvironment storage solution for such objects.
Using an anoxic atmosphere to save the Ferryland Cross
An anoxic microenvironment was used to stop the process of deterioration of an archaeological metal object called the Ferryland Cross. Learn more about it in Caring for archaeological collections – Using an anoxic atmosphere to save the Ferryland Cross.
Powdery white corrosion in storage
Lead corrodes in the presence of acetic acids. Visit Agent of deterioration: pollutants – Vignette 1 to learn about the sources of acetic acid and how to prevent lead objects from being exposed to this harmful pollutant.
Bibliography
Ankersmit, B., M. Griesser-Stermscheg, L. Selwyn and S. Sutherland. Recognizing metals and their corrosion products. Ottawa, ON: Canadian Conservation Institute, n.d.
Barclay, R.L. Care of Objects Made of Zinc, revised. CCI Notes 9/9. Ottawa, ON: Canadian Conservation Institute, 2007.
Barclay, R. L., and C. Hett. The Cleaning, Polishing and Protective Waxing of Brass and Copper, revised. CCI Notes 9/3. Ottawa, ON: Canadian Conservation Institute, 2007.
Chilton, J.P. Principles of Metallic Corrosion. London, UK: Chemical Society, 1973.
Daniels, V., and S. Ward. "A Rapid Test for the Detection of Substances Which Will Tarnish Silver." Studies in Conservation 27,2 (1982), pp. 58–60.
Drayman-Weisser, T. "Metal Objects." In H. Whelchel, ed., Caring for Your Collections. New York, NY: Harry N. Abrams, 1992, pp. 108–121.
Hiscox, G., ed. Henley's Twentieth Century Book of Recipes, Formulas and Processes. New York, NY: The Norman W. Henley Publishing Company, 1907.
Logan, J., R.L. Barclay, C. Newton and L. Selwyn. "The Ferryland Cross Revisited." CCI Newsletter 36 (Fall 2005), pp. 8–9.
Logan, J., R.L. Barclay, P. Bloskie, C. Newton and L. Selwyn. "Saving the Ferryland Cross: 3D Scanning, Replication, and Anoxic Storage." In E. Williams and C. Peachey, eds., The Conservation of Archaeological Materials: Current Trends and Future Directions. BAR International Series 2116. Oxford, UK: Archaeopress, 2010, pp. 127–134.
Logan, J. and L. Selwyn. Recognizing Active Corrosion, revised. CCI Notes 9/1. Ottawa, ON: Canadian Conservation Institute, 2007.
Logan, J. and L. Selwyn. Storage of Metals, revised. CCI Notes 9/2. Ottawa, ON: Canadian Conservation Institute, 2007.
Logan, J. and L. Selwyn. Care and Cleaning of Iron, revised. CCI Notes 9/6. Ottawa, ON: Canadian Conservation Institute, 2007.
Logan, J., L. Selwyn, C. Cook and T. Grant. Tannic Acid Coating for Rusted Iron Artifacts, formerly published under the title Tannic Acid Treatment, revised. CCI Notes 9/5. Ottawa, ON: Canadian Conservation Institute, 2013.
National Park Service. Using Silica Gel in Microenvironments (PDF format, 478 KB). Conserve O Gram 1/8. Washington, D.C.: National Park Service, 1999.
National Park Service. Caring for Historic Longarms: Storage and Handling Requirements. Conserv O Gram 10/1. Washington, D.C.: National Park Service, 1999.
National Park Service. Caring for Silver and Copper Alloy Objects (PDF format, 450 KB). Conserv O Gram 10/2. Washington, D.C.: National Park Service, 1999.
National Park Service. Preparing Historic Motorized Vehicles for Storage or Exhibit (PDF format, 514 KB). Conserv O Gram 10/3. Washington, D.C.: National Park Service, 1999.
National Park Service. Cobalt Indicating Silica Gel Health and Safety Update (PDF format, 224 KB). Conserv O Gram 2/15. Washington, D.C.: National Park Service, 2005.
National Park Service. Creating A Microclimate Box for Metal Storage (PDF format, 321 KB). Conserv O Gram 4/16. Washington, D.C.: National Park Service, 2011.
Pouliot, B., C. Matsen, J. Mass, W. Donnelly, K. Andrews and M. Bearden. "Three Decades Later: A Status Report on the Silver Lacquering Program at Winterthur." Objects Specialty Group Postprints, vol. 20. Washington, D.C.: American Institute for Conservation, 2013.
Prytulak, G. Mechanical Removal of Rust from Machined Ferrous Surfaces, revised. CCI Notes 9/8. Ottawa, ON: Canadian Conservation Institute, 2007.
Rimmer, M., D. Thickett, D. Watkinson and H. Ganiaris. Guidelines for the Storage and Display of Archaeological Metalwork. Swindon, UK: English Heritage, 2013.
Schweitzer, P.A. Metallic Materials: Physical, Mechanical, and Corrosion Properties. New York, NY: Marcel Dekker, 2002.
Selwyn, L. Metals and Corrosion: A Handbook for the Conservation Profession. Ottawa, ON: Canadian Conservation Institute, 2004.
Selwyn, L. "Health and Safety Concerns Relating to Lead and Lead Compounds in Conservation." Journal of the Canadian Association for Conservation 30 (2005), pp. 18–37.
Selwyn, L. Silver - Care and Tarnish Removal, revised CCI Notes 9/7. Ottawa, ON: Canadian Conservation Institute, 2007.
Selwyn, L. Lead in Museum Collections and Heritage Buildings. CCI Notes 1/8. Ottawa, ON: Canadian Conservation Institute, 2010.
Selwyn, L. Understanding flash rusting, 2016.
Selwyn, L. Understanding how silver objects tarnish, 2016.
Selwyn, L. Understanding galvanic corrosion, 2019.
Stone, T. Basic Care of Coins, Medals and Medallic Art, revised. CCI Notes 9/4. Ottawa, ON: Canadian Conservation Institute, 2007.
Tétreault, J. "Display Materials: The Good, The Bad and The Ugly." In Exhibitions and Conservation: Preprints of the Conference Held at the Royal College of Physician's, Edinburgh, April 21–22, 1994. Edinburgh, UK: Scottish Society for Conservation and Restoration, 1994, pp. 79–87.
Tétreault, J. Airborne Pollutants in Museums, Galleries and Archives. Ottawa, ON: Canadian Conservation Institute, 2003.
Tétreault, J. Products Used in Preventive Conservation. Technical Bulletin 32. Ottawa, ON: Canadian Conservation Institute, 2017.
Thickett, D., and L.R. Lee. "The Azide Test - For Sulphur-Containing Materials." In The Selection of Materials for the Storage or Display of Museum Objects. Revised edition. British Museum Occasional Paper Number 111. London, UK: British Museum, 2004, pp. 16–17.
Weintraub, S. "Demystifying Silica Gel." In V. Greene, ed., Objects Specialty Group Postprints, vol. 9. Washington, D.C.: Objects Specialty Group of the American Institute for Conservation, 2002, pp. 169–194.
Glossary
- Active corrosion:
- Fresh or new corrosion, or corrosion that is progressing; often seen as spalling, cracking or flaking.
- Active state:
- Condition in which a metal reacts with its environment (i.e. freely corrodes) because it is thermodynamically unstable and the corrosion products are soluble. Compare with "Passive state."
- Alloy:
- Metallic material containing two or more elements, at least one of which is a metal (e.g. brass, bronze, pewter, steel).
- Anneal:
- Heat treat a metal to change its physical properties (e.g. heat treatment might soften a metal by removing internal stresses caused by work-hardening).
- Anode:
- Electrode in an electrochemical cell at which oxidation half-reactions occur and electrons flow away in the external circuit. The anode is usually where corrosion occurs and where metal ions enter the solution. Compare with "Cathode."
- Anoxic environment:
- An environment that has low levels of oxygen, compared to normal ambient air.
- Brass:
- Alloy of copper with varying amounts of zinc; other metals, for example, tin or lead, may also be present.
- Bronze:
- Alloy of copper that contains varying amounts of tin and may include other metals (e.g. zinc, lead). In modern bronze alloys, the tin may be replaced with elements such as aluminum or silicon.
- Cathode:
- Electrode in an electrochemical cell at which reduction half-reactions occur. Electrons flow toward the cathode in the external circuit. Compare with "Anode."
- Corrosion:
- Electrochemical reaction between a metal and its environment that causes the metal to deteriorate. The electrochemical process involves the transfer of electrons from the metal to another species during simultaneous oxidation and reduction reactions.
- Desiccant:
- A substance that reduces RH by removing moisture from the ambient air. A common type is desiccated silica gel.
- Electrochemical cell:
- Combination of two electrodes (an anode and a cathode) in electrical contact and immersed in an electrolyte; the anode and cathode may be different metals or dissimilar areas on the same metal surface.
- Electrolyte:
- Ionic conductor containing positive and negative ions (anions and cations) that migrate in an electric field (e.g. an aqueous solution containing dissolved salts).
- Electroplate:
- Deposit a layer of metal onto a conducting surface by making it the cathode in an electrolytic cell.
- Enclosure:
- An enclosure is any type of physical structure that completely encloses and isolates an object from the rest of the room (e.g. a plastic bag, a box, a storage cabinet or a display case). An enclosure functions most effectively when made of good barrier materials and assembled with tight seals.
- Finish:
- Process (e.g. flame bluing, artificial patination, engraving, electroplating, painting, lacquering) used during the final steps of constructing an object to provide decoration or further protection.
- Galvanic corrosion:
- Accelerated corrosion of a metal in electrical contact with a more noble metal (or a non-metallic conductor) in an electrolyte.
- Galvanic series:
- List of metals, alloys and conducting materials arranged according to their electrode potentials in a specific wet environment (e.g. seawater). The series is ordered from the metals that are least prone to corrosion (e.g. noble metals such as platinum) to the ones that are more susceptible to corrosion (e.g. active metals such as zinc and aluminum).
- Galvanized:
- Covered with a thin protective zinc coating by dipping into molten zinc or by electroplating. The term applies to iron and steel.
- Grain:
- Individual crystal in a polycrystalline metal. Each grain contains atoms ordered in a regular geometric pattern.
- HVAC system:
- Heating, ventilating and air conditioning system.
- Microenvironment:
- A distinct and sealed environment within the larger room environment, where environmental conditions are created and maintained to enhance the preservation of the object(s) enclosed within that space. A microenvironment is usually created through the use of an enclosure (a container made of a barrier material assembled with tight seals) in which is included one or more specialized products (e.g. desiccant, sorbent).
- Noble metal:
- Metal with a low tendency to corrode (e.g. gold, platinum). Refer to "Galvanic series."
- Oxidation:
- Chemical reaction in which the constituents lose electrons. If a metal or metal ion is oxidized, the oxidation state is increased. Compare with "Reduction."
- Oxygen absorber:
- Substance that absorbs or removes oxygen from the surrounding air. Synonym: oxygen scavenger.
- Passive state:
- Condition in which a thermodynamically unstable metal has a low corrosion rate because the metal surface has reacted with the environment to form a protective corrosion layer (a passivating layer). Compare with "Active state."
- Passivating layer:
- Thin protective corrosion layer (or oxide layer) on a metal surface which reduces the metal's corrosion rate.
- Patina:
- Corrosion layer on the surface of a metal. A patina may occur naturally as a result of long-term exposure to weather, pollution, etc., or it may be artificially induced through the application of various chemicals.
- Pewter:
- Alloy of tin (typically 80–90% by weight of tin) with lead (in the case of old pewter, common in the Middle Ages) or antimony (modern pewter).
- Plated metal:
- A metal that is covered, either by electrolytic process (electroplating) or chemical process, with a thin layer of another type of metal, which is usually nobler. The metal plating protects the underlying metal (the core metal) from corrosion.
- Reduction:
- Chemical reaction in which the constituents gain electrons. If a metal ion is reduced, the oxidation state is reduced. Compare with "Oxidation."
- Scavenger:
- Synonym of pollutant sorbent.
- Sorbent:
- A material that provides a sorption (absorption or adsorption) function. Sorbents can extract some compounds present in the ambient air and retain them by an affinity or reaction process. A common type is activated charcoal. Synonym: scavenger.
- Tarnish:
- A thin layer of corrosion that develops on a metal surface and causes its discolouration. Used most frequently to describe such a layer on silver or copper due to a reaction with sulfur.
© Government of Canada, Canadian Conservation Institute, 2020
Published by:
Canadian Conservation Institute
Department of Canadian Heritage
1030 Innes Road
Ottawa, ON K1B 4S7
Canada
Cat. No.: CH57-4/6-7-2020E-PDF
ISBN 978-0-660-35196-4
Page details
- Date modified: