Caring for plastics and rubbers
Julia Fenn and R. Scott Williams
Caring for plastics and rubbers is part of CCI's Preventive conservation guidelines for collections online resource. This section presents key aspects of managing the care of plastic and rubber objects in heritage collections based on the principles of preventive conservation and risk management.
Table of contents
- Understanding plastics and rubbers
- Causes of damage to plastics and rubbers and preventive conservation strategies
- Agents of deterioration of general concern to plastics
- Agents of deterioration of specific concern to plastics
- Control strategies for mixed collections containing malignant plastics
- Basic control strategies
- Optimum control strategies
- Five stages for controlling malignant plastics in mixed collections
- Use and formulation for cresol red and modified bromocresol green indicators
- Examples of preventive conservation practices
- Bibliography and further reading
List of abbreviations and symbols
Abbreviations
- ABS
- acrylonitrile-butadiene styrene
- AU
- polyurethane, polyester type
- BR
- polybutadiene rubber
- CA
- cellulose acetate
- CAB
- cellulose acetate butyrate
- CCI
- Canadian Conservation Institute
- CDA
- cellulose diacetate
- CF
- casein-formaldehyde
- CME
- coefficient of moisture expansion
- CN
- cellulose nitrate
- COC
- cycloolefin copolymer
- CP
- cellulose propionate
- CPVC
- chlorinated poly(vinyl chloride)
- CR
- polychloroprene rubber
- CTA
- cellulose triacetate
- CTE
- coefficient of thermal expansion
- ECTFE
- ethylene chlorotrifluoroethylene
- EP
- epoxy
- EPDM
- ethylene propylene diene monomer rubber
- ESC
- environmental stress cracking
- ETFE
- ethylene tetrafluoroethylene
- EU
- polyurethane, polyether type
- EVA
- ethylene vinyl acetate
- EVOH
- ethylene vinyl alcohol
- FEP
- fluorinated ethylene propylene
- FSI
- fluorosilicone
- HDPE
- high-density polyethylene
- HDT
- heat deflection temperature
- HIPS
- high impact polystyrene
- IIR
- isobutylene isoprene rubber
- IR
- polyisoprene rubber, synthetic
- IRS
- infrared spectroscopy
- LDPE
- low-density polyethylene
- LLDPE
- linear low-density polyethylene
- MDPE
- medium-density polyethylene
- MF
- melamine-formaldehyde
- NBR
- acrylonitrile butadiene
- NR
- polyisoprene, natural rubber
- PA
- polyamide
- PAN
- polyacrylonitrile
- PB
- polybutylene
- PBT
- poly(butylene terephthalate)
- PC
- polycarbonate
- PCTFE
- polychlorotrifluoroethylene
- portable document format
- PE
- polyethylene
- PET
- poly(ethylene terephthalate)
- PF
- phenol-formaldehyde
- PFA
- perfluoroalkoxy
- PI
- polyimide
- PLA
- polylactic acid
- PMMA
- poly(methyl methacrylate)
- PMP
- polymethylpentene
- POM
- polyoxymethylene (acetal)
- PP
- polypropylene
- PS
- polystyrene
- PTFE
- polytetrafluoroethylene
- PVAC
- poly(vinyl acetate)
- PVAL
- poly(vinyl alcohol)
- PVB
- poly(vinyl butyral)
- PVC
- poly(vinyl chloride)
- PVDC
- poly(vinylidene chloride)
- PVDF
- poly(vinylidene fluoride)
- PVF
- poly(vinyl fluoride)
- PUR
- polyurethane
- TPU
- thermoplastic polyurethane
- RH
- relative humidity
- SAN
- styrene acrylonitrile
- SBR
- styrene-butadiene rubber
- SI
- silicone
- UF
- urea-formaldehyde
- UHMWPE
- ultra-high molecular weight polyethylene
- UP
- unsaturated polyester
- UV
- ultraviolet
- XLPE
- crosslinked polyethylene
Symbols
- °C
- Celsius
- Tbrittle
- brittleness temperature
- Tg
- glass transition temperature
Understanding plastics and rubbers
The care of plastics in collections is challenging. Plastics are a new class of materials and their individual weaknesses are little known and often unexpected. Traditional display and storage methods accelerate deterioration of plastics, and the ensuing chemical and physical damage can be unattractive, highly corrosive, irreversible—and largely untreatable. Because of the diversity and versatility of plastics, they have been used in a huge range of common objects since their introduction in the 19th century. Unfortunately, for the first part of their history, their long-term properties were not well understood. Older plastic objects can deteriorate more rapidly and in a greater variety of ways than those made from traditional materials. More recent plastics may also deteriorate rapidly as a result of planned obsolescence, such as biodegradability.
Plastics, rubbers and elastomers
Plastics always have complex chemical compositions. They contain the basic polymer that gives the plastic its name (e.g. polyethylene, polystyrene, poly(vinyl chloride), phenol-formaldehyde), plus additives that modify the inherent properties of the base polymer to give suitable end-use properties to the plastic. Thus, different plastics made from the same polymer type can have different properties, depending on variations in the polymer. Variations may include molecular size (e.g. molecular weight, degree of polymerization) and molecular shape (e.g. linear, branched, crosslinked). Properties are also affected by the types of additives present (e.g. plasticizers, slip agents, colourant, ultraviolet (UV) absorbers, heat stabilizers, antioxidants, and mineral and organic fillers).
Rubbers are also plastics in the sense that they have complex chemical compositions containing a basic polymer and additives. Rubbers are a subtype of plastics. They have the property of elasticity—the capability of recovering size and shape after deformation. Rubbers include natural rubber (containing naturally produced polyisoprene from plant sap), and synthetic rubbers, such as synthetic polyisoprene, polybutadiene, polychloroprene and silicone (SI). Rubbery, elastic plastics are also called elastomers.
In this document, the term "plastics" will be used to indicate the class of all plastics, including all rubbers and elastomers. Whenever the rubbery elastomeric product made from plant sap is discussed, the term "natural rubber" will be used.
Table 1 lists some plastics (including their abbreviations, and common names and trade names) and typical plastic objects that can be found in collections.
Plastic |
Abbreviation |
Common name and trade name examples |
Common occurrences in collections |
---|---|---|---|
Thermoplastics (Melt) |
|||
Cellulose nitrate |
CN |
celluloid French ivory Pyralin Pyroxylin Xylonite |
Simulated natural materials for solid plastic costume accessories (such as buttons, jewellery), toiletry items, stays and supports, fans |
Cellulose ester |
Bexoid Tenite |
Simulated natural materials for solid plastic costume accessories, toiletry items, stays and supports, fans, appliance housings, fibres |
|
Cellulose acetate |
CA |
||
Cellulose acetate butyrate |
CAB |
||
Cellulose propionate |
CP |
||
Polyethylene |
PE |
Ethafoam Tupperware |
Translucent plastics, containers, toys, packaging foams, sheets and films |
Low-density PE |
LDPE |
||
Linear low-density PE |
LLDPE |
||
High-density PE |
HDPE |
||
Ultra-high molecular weight PE |
UHMWPE |
||
Crosslinked PE |
XLPE |
||
Polypropylene |
PP |
Coroplast |
Translucent plastics, containers, toys, sheets and films |
Polystyrene |
PS |
Styrofoam Lustrex |
Hard, often clear, plastic accessories (such as clasps, handles, jewellery, buttons), containers, packaging and insulation foam, appliance cases, toys, model cars, trains, and airplanes |
Acrylonitrile-butadiene-styrene |
ABS |
||
Styrene-acrylonitrile |
SAN |
||
Poly(methyl methacrylate) |
PMMA |
Acrylic Plexiglas Lucite Perspex |
Hard, often clear, sometimes coloured sheets and extruded profiles, costume accessories, glazing, signage |
Polycarbonate |
PC |
Lexan Tuffak Cyrolon Makrolon |
Hard, often clear, sometimes coloured sheets, panels, containers, extruded profiles, glazing |
Poly(vinyl acetate) |
PVAC |
Carpenter's Glue |
Emulsion and hot melt adhesives, lamina in sheets and films |
Poly(vinyl alcohol) |
PVAL |
Laminated packaging films (e.g. meat and produce wrapping), adhesives |
|
Poly(vinyl chloride) |
PVC |
Tygon Sintra |
Flexible costume accessories such as belts, artificial leather; rigid accessories, handles and clasps, jewellery; sheets and films; extruded profiles and pipes; toys |
Polyamide PA 4 PA 6 PA 4.6 PA 6.6 PA 11 PA 12 PA 6.10 where the figures refer to the number of carbon atoms in the amine and acid, respectively. |
PA |
Nylon Zytel |
Toiletries items (combs, tooth brushes), mechanical components (gears, wheels, housings), fibres and fabric |
Polyoxymethylene |
POM |
Acetal |
Mechanical components |
Poly(ethylene terephthalate) |
PET |
Hostaphan Melinex Mylar Dacron Terylene polyester |
Sheets and films, bottles, trays, fibres, textiles, clothing |
Fluoropolymer |
Non-stick, friction-reducing applications such as utensil coatings, bearings, gears |
||
Polytetrafluoroethylene |
PTFE |
Teflon |
|
Fluorinated ethylene propylene |
FEP |
Teflon |
|
Ethylene tetrafluoroethylene |
ETFE |
Tefzel |
|
Ethylene chlorotrifluoroethylene |
ECTFE |
Halar |
|
Poly(vinylidene fluoride) |
PVDF |
Kynar |
|
Perfluoroalkoxy alkane |
PFA |
Teflon |
|
Thermosets (Char) |
|||
Casein-formaldehyde |
CF |
Ameroid Erinoid Galalith Lactoid |
Opaque plastic costume accessories and toiletry items (such as buttons, beads, buckles, and combs), knitting needles, pens |
Melamine-formaldehyde |
MF |
Arborite Formica Melmac Perstorp |
Tableware, high-pressure laminate (MF on PF) |
Phenol-formaldehyde |
PF |
Bakelite Catalin Durez Marblette |
Early moulded plastics, especially in electrical apparatus because of its insulating properties; cast costume jewellery and accessories |
Urea-formaldehyde |
UF |
Bandalasta Plaskon |
Tableware, costume jewellery |
Epoxy |
EP |
Araldite |
Adhesive, some cast or moulded objects |
Polyurethane |
PUR |
many foams |
Fabric coatings to waterproof and give wet look, simulated leather and suede; foam padding in hat bands, shoulder pads, bust pads; packaging and insulation foams |
Silicone (polysiloxane, polydimethylsiloxane) |
SI |
RTV Silastic |
Caulks, gaskets and seals; moulds |
Unsaturated polyester |
UP |
fibreglass resin fibreglass reinforced plastic (FRP) |
Boats, sculptures, tanks, machine housings |
Hard rubber |
NR |
Ebonite |
Jewellery, wind musical instruments, electrical insulators, chemical tanks |
Rubbers (elastic, bouncy) |
|||
Polyisoprene, natural rubber |
NR |
SMR |
Waterproof coatings, rubber garments, elastic garments, elasticized fabric and threads, bathing caps, footwear, dolls, toys, electrical insulators |
Polyisoprene, synthetic rubber |
IR |
Ameripol SN |
Gaskets, seals, bumpers, vibration isolators, elastic components, bouncy objects, foams |
Polybutadiene |
BR |
Buna CB |
|
Acrylonitrile butadiene |
NBR |
Perbunan N |
|
Styrene butadiene |
SBR |
SBR |
|
Isobutylene isoprene |
IIR |
Butyl |
|
Ethylene propylene diene monomer |
EPDM |
Vistalon |
|
Polychloroprene |
CR |
Neoprene |
|
Silicone |
SI |
Silastic Elastosil |
|
Fluorosilicone |
FSI |
FSE Silastic Sylon |
|
Polyurethane, polyester type |
AU |
AdiPRENE |
|
Polyurethane, polyether type |
EU |
PUR |
|
For more extensive lists of abbreviations for plastics, consult: Plastics Abbreviations and Acronyms or Plastic - Wikipedia. |
Thermoplastics and thermosets
Plastics are classified as thermoplastics or thermosets, according to their thermal properties. Thermoplastics melt, thermosets char. Elastomers can be either thermoplastic or thermoset. This classification is useful for predicting properties like creep, compression set, solubility, exudation, melting and strength. Table 2 shows a comparison of the properties of thermoplastics and thermosets.
Thermoplastics |
Thermosets |
---|---|
Can be melted (or softened) |
Hard to melt, chars instead |
Formed by moulding or extruding |
Shaped by polymerization in a mould, or shaped by machining of cured blocks |
Linear molecular structure, not network crosslinked |
Usually crosslinked, network polymers |
Creep and deform under stress |
Minimal creep |
Soluble |
Insoluble |
Malignant plastics
Plastics are made from many different materials and therefore have varied, often unexpected, types of deterioration. Conservation surveys of museum collections show that chemical deterioration of plastic objects is restricted predominantly to a small number of plastic types, namely:
- CN
- CA
- PVC
- PUR, especially PUR foam
- rubber, especially highly vulcanized hard natural rubber (e.g. Ebonite, Vulcanite)
In addition to being the most susceptible to chemical deterioration, these plastics, plus UF, now most commonly found in adhesives and binders in engineered wood, produce noxious degradation products that damage other objects in the collection. They become increasingly harmful as they degrade, corroding and polluting objects and storage materials in the immediate vicinity.
Plastics that spread damage to their neighbours are called "malignant plastics". Damage can occur by transfer of corrosive substances by direct contact with the malignant plastic (e.g. sulfuric acid on Ebonite), or by dispersion of noxious gases emitted by the malignant plastic to remote objects in the collection (e.g. nitrogen oxides from CN and sulfur oxides from vulcanized rubber). Even relatively inert plastics such as acrylics can absorb pollutants and become contaminated and corrosive. Because of their malignancy, conservation strategies must deal with these plastics as a first priority.
All plastics degrade over time, as do all organic materials but, for most plastics, the damage is mainly restricted to the plastic itself, not to its neighbours. These "benign plastics" are not dangerous to the collection unless they have absorbed harmful volatile compounds that are subsequently desorbed.
Identifying potentially malignant plastics is often difficult. A dressing table set made from a relatively benign plastic such as CF may look very similar to one made from CN. From the late 19th century, plastics have been used successfully to imitate a wide range of materials such as gems, ivory, tortoiseshell and coral. Since the 1960s, plastic imitations of wood, leather, silk and building materials have also become commonplace. Therefore, malignant plastics may be masquerading unrecognized in natural history, ethnographic and textile collections. They may also be used in the simulation and restoration of period rooms and historic houses. For this reason, we have included tests for the identification of, and strategies for dealing with, malignant plastics under Control strategies for mixed collections containing malignant plastics, available in Causes of damage to plastics and rubbers and preventive conservation strategies.
Care of plastic and rubber objects requires re-evaluation of the materials and methods usually recommended for preserving collections. Sometimes, excellent curatorial practices, such as protective wrapping in buffered tissue, can actually accelerate the degradation of several very common plastics (Figure 1).
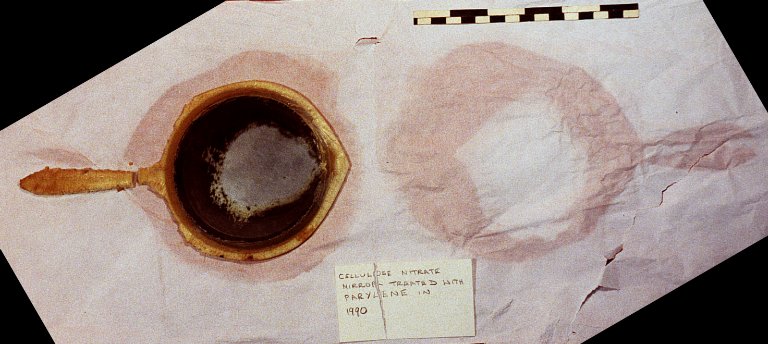
© Government of Canada, Canadian Conservation Institute. CCI 120210-0088
Figure 1. Buffered tissue aggravates deterioration of CN. The deterioration of this CN mirror was accelerated by wrapping it in alkaline buffered tissue. Nitrogen oxides emitted by the CN mirror reacted with alkaline buffering calcium carbonate in the tissue to form deliquescent calcium nitrate, clearly shown here as wet patches in the tissue. Irreversible damage occurred when salts in the wet patches reacted with the mirror surface.
Identification of plastics
Because there are many different plastics, each with its own degree of vulnerability or malignancy, identification of the plastics in the collection is crucial to effective preservation.
There are two options for identifying plastics: chemical spot tests and instrumental analysis, particularly infrared spectroscopy (IRS). Spot tests are notoriously ambiguous; IRS is preferred. Another advantage of IRS is that portable infrared spectrometers are now available, so that IRS can be carried out on-site in the museum, sometimes without taking samples.
There are some good spot tests that yield relatively unambiguous results for the detection of the six most malignant plastics (Rémillard 2007). Since most of the test reagents are harmful to the plastic, the test should be done on a tiny sample removed from the object. A good way of getting an inconspicuous sample is to draw a ground glass slide against the base of the object. The line of removed plastic on the slide is usually enough for several spot tests (Figure 2 and Table 3). This method is commonly employed to get a sample from the edge of photograph negatives.
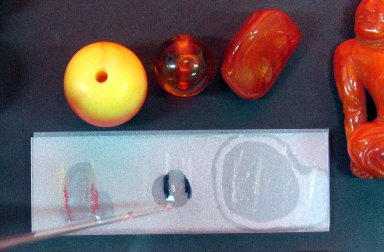
© Government of Canada, Canadian Conservation Institute. CCI 120210-0106
Figure 2. Diphenylamine spot test on various real and imitation amber beads from a single collection using samples made by scratching the amber across a ground glass slide. One bead is identified as PF by the appearance of a red colouration; another is identified as CN by the appearance of a blue colouration; and another is identified as genuine amber because it showed no colour change.
Plastic |
Spot test |
Test result |
Reference |
---|---|---|---|
CN |
Diphenylamine/ |
Blue colour develops |
CCI 1994; Williams et al. 1998 |
CA |
Alkaline hydroxylamine plus ferric chloride acidified |
Burgundy red colour develops |
Coxon 1993 |
PVC |
Beilstein test: copper wire heated in torch flame |
Colourless flame turns green |
CCI 1993; Williams et al. 1998 |
Sulfur vulcanized rubber (Ebonite, Vulcanite) |
Iodine/sodium azide reagent |
Bubbles develop in reagent |
Daniels and Ward 1982 |
PUR |
Dimethyl amino benzaldehyde in glacial acetic acid |
Canary-yellow colour develops |
Roff et al. 1971 |
Causes of damage to plastics and rubbers and preventive conservation strategies
This section describes the causes and types of damage to plastic and rubber objects, and the preventive conservation strategies that reduce the risks of damage.
Agents of deterioration of general concern to plastics
Plastics can be damaged by all 10 agents of deterioration. Dissociation, thieves and vandals, pests, water and fire (except for CN) are non-specific agents of deterioration for plastics with the same preventive conservation strategies as for the majority of other types of museum objects.
Dissociation
Dissociation results in loss of objects, or object-related data, including documentation, or of the ability to retrieve or associate objects and data. Both actions and failures to act can contribute to dissociation-related risks. An example of an action causing dissociation is misplacing an object. An example of a failure to act is failure to document an outgoing loan. Disasters can cause dissociation. Plastic objects in museums need preventive conservation strategies to prevent dissociation. For further information on preventing dissociation, consult Agent of deterioration: dissociation.
Thieves and vandals
Plastic objects or objects containing plastics, such as jewellery and toiletry articles made of early French ivory, Bakelite and Lucite, are often small and collectible, and therefore attractive to thieves. Art objects made of plastics are sometimes controversial and may be subject to vandalism. Plastic objects in museums need preventive conservation strategies against thieves and vandals. Sealed enclosures against theft may be dangerous to many plastics unless effective sorbent systems or filtered ventilation systems are incorporated into exhibit cases. Large modern art sculptures should be set well out of reach behind barriers and monitored by alarms and surveillance systems. For further information on protecting collections from thieves and vandals, consult Agent of deterioration: thieves and vandals.
Pests
Few plastics are fodder for pests or are attractive to pests, although some, such as CF, may be derived from natural products or have components based on natural products, like plasticizers from soya oil or PUR foam based on adipates, and may be nutrients for microbial growth. Plastic objects may contain fodder, and pests will damage the plastic barrier to get to it. Plastic objects may also provide nesting materials or nesting places. Biocides (especially fumigants and volatile biocides) pose far greater risk to plastics than pests. For information on preventive conservation strategies to control pests, consult Agent of deterioration: pests.
Water
Most plastics are not very permeable to water so brief immersion should not cause structural damage such as dissolution, distortion, disintegration or bleeding of components. Degraded plastics are most susceptible to water damage. Undegraded plastics that should be unaffected by water immersion for less than a day followed by air drying include CA, CN, PA, PC, PET, PE, PP, PMMA, PS and PVC. Immersion may cause water-sensitive plastics that rapidly absorb water and swell, such as CF, PF with organic fillers, and some PA, to warp, especially if parts are restrained against movement. Extended periods of wetness may cause hydrolysis of CN and CA, some PA, PUR and UF. Hydrolysis is discussed in the section Incorrect relative humidity. The key factor affecting water damage is duration of immersion.
The appearance of a plastic object is dependent on the condition of its thin surface layer. This layer may be affected by even short exposure to water, resulting in the appearance of a plastic object being significantly altered to show mottling, etching, etc. CF, PF and hard rubber (Vulcanite, Ebonite) are susceptible to surface damage by water. Although the surface may be marred, the structural integrity of the object should be unchanged. Wet plastics may have softer surfaces than expected, so care must be exercised when handling or patting dry.
Freeze-drying is often suggested as treatment for flooded objects. However, for most plastic objects this is unnecessary and may be harmful. Temperatures below freezing increase the brittleness of plastics, so expansion of water frozen in cracks and fissures of embrittled plastic parts may lead to increased fracture damage. One prime reason for freeze-drying is to prevent mould growth. Since plastics seldom support mould growth, freeze-drying is unnecessary. Immediate drying in air will prevent mould growth on plastic parts.
The preferred treatment for wet plastics is quick rinsing with clean water followed by drying in air, preferably with forced ventilation, e.g. fans. Freeze-drying should be avoided.
Recommendations
- Do not store objects or packages directly on floors.
- Use protective waterproof covers in storage and display, assuming that all pipes will leak and all sprinklers will activate.
- Use waterproof storage containers, such as PE bags and PE and PP boxes (except malignant plastics).
- Avoid freezing wet plastics (do not freeze-dry).
For more information on mitigating risks from water, consult Agent of deterioration: water.
Fire
All plastics are damaged by heat and flame. Heat from a fire can cause plastics to soften, distort, melt or char. When exposed to flame, plastics will ignite and burn with or without flame, and may char and emit toxic gases and smoke. All plastics are fuel and will burn at a sufficiently high temperature, which varies from plastic to plastic. The risk of fire to most plastics is equivalent to, or less than, the risk of fire to organics, like paper and wood. Smoke generated by fires can spread and cause damage elsewhere in the collection, such as soiling by deposition of soot and smoke particles, corrosion and odours. Most burning plastics, but not CN, can be extinguished by methods suitable for Class A fires.
Thermoplastics are damaged at lower temperatures than thermosets. Thermoplastics, including CA, CAB, PA, PC, PET, PE, PP, PMMA, PS and PVC, melt and may form burning droplets, which can spread the flame. Fire-retardant additives will not prevent melting and possible dripping of molten plastic onto other materials. Heat-resistant thermosets, such as CF, PF, UF, PUR, hard rubber (Vulcanite, Ebonite), SI and PTFE, will be charred and cracked beyond repair if engulfed in flames, but they do not melt and may survive if exposed only to smoke and hot gases. Flame spread rates are usually much lower for thermosets than for thermoplastics.
For more information on preventive conservation strategies to control fire, consult Agent of deterioration: fire.
The flammability of cellulose nitrate
CN is of particular concern because it is the most flammable plastic and it generates oxidizing gases as it burns, making the fire impossible to extinguish by depriving it of oxygen. Fire suppression sprinklers and misters, foam-producing nozzles, pre-charged carbon dioxide and Freon substitute dump systems have all been shown to be ineffective for CN motion picture fires. Fires in motion picture archives have been extinguished with massive amounts of water, which is thought to have cooled the burning CN below the ignition temperature, thus extinguishing the fire (Vitale 2009).
CN is made from cellulose reacting with nitric acid, which replaces some hydroxyl groups on the cellulose with nitrate groups. The extent of replacement (degree of substitution) is measured by the nitrogen content. Products with different nitrogen contents are used for different purposes, for example, plastics and lacquers contain 10.5-11.5% nitrogen; lacquers, films and film sheets contain 11.5-12.3% nitrogen; and explosives and gun powders contain 12.4-13.5% nitrogen. Fire risk increases with nitrogen content. Motion picture film has higher nitrogen content than photographic sheet film, which in turn has higher nitrogen content than plastics and lacquers.
Serious fires in motion picture archives have been attributed to spontaneous combustion of degraded motion picture films. No fires have been attributed to spontaneous combustion of sheet film stored in paper sleeves or of plastic objects. The fire hazard of CN objects is similar to that of other flammable materials such as gasoline and solvents.
CN objects should be stored in special regulated storage, preferably at low temperatures in refrigerators or freezers. In addition to reducing risk from a CN fire, segregation reduces risk of exposure to the rest of the collection to harmful oxidizing and acidic volatile degradation products.
CN objects should not be sealed within unventilated enclosures, such as bags and cabinets. In these conditions, degradation gases accumulate around the plastic in the enclosure and increase the rate of degradation, thereby increasing fire risk by decreasing the ignition temperature of the plastic. If sealed storage is required, such as to control relative humidity (RH) in a bag, then sorbents should be included in the bag to decrease the concentration of degradation gases in the bag.
Recommendations
- Treat risk of fire for most plastics (except CN) as equivalent to or less than natural organic materials like paper, natural fibres and wood (Class A).
- Burning plastics (except CN) can be extinguished by methods suitable for Class A fires.
- Segregate CN from general collection.
- CN should be stored in cold storage in appropriate freezers (small collection) or refrigerated rooms (large collections) to reduce degradation, preserve objects and reduce fire risk.
- Large collections of CN are preferably stored in a separate, specialized storeroom, built according to relevant codes.
Additional information for the display and storage of museum objects containing CN can be found in CCI Note 15/3 Display and Storage of Museum Objects Containing Cellulose Nitrate.
Agents of deterioration of specific concern to plastics
The primary agents of deterioration that cause specific structural and chemical damage to plastic objects are stress and other direct physical forces, pollutants (including oxygen), light and UV, incorrect temperature and incorrect RH. Ideally, plastic objects should be stored on strong, padded supports in well-ventilated, cold, dark, dry and oxygen-free conditions.
Not all plastics are vulnerable to the same agents, nor to the same extent. Plastics have varying resistance to thermal oxidation, photooxidation and hydrolysis, the main degradation reactions caused by these agents. For example, PE has poor resistance to thermal oxidation and photooxidation, but has excellent resistance to hydrolysis; CN has poor resistance to all three degradation processes. The overall effect on the collection depends on the fraction and specific vulnerability of each type of plastic in the collection. Controlling chemical deterioration is the most important factor in preserving these types of objects.
Because some plastics are more susceptible to specific agents, it is beneficial to concentrate on controlling that specific agent for that specific plastic. Identifying the material you are dealing with is the key to selecting appropriate preventive conservation strategies.
Physical forces
Degraded plastics can be surprisingly brittle, especially when cold. CA, CN, CF, some PF, PMMA and PS can be broken easily by impact. Do not assume that, because rubber and PVC objects may be flexible, it is not necessary to support them during travel, storage and display. Stress, such as that created by stretching rubbers, can increase the rate of chemical (oxidative) deterioration. Cracks tend to appear at right angles to the direction of the applied stress. For example, cracks may develop along a fold. Objects with cracks are more likely to break than undamaged objects, and they need more support. Packaging films, such as Cellophane, CA and PET, tear easily if they have been scratched or notched. Objects stored in a stressed state may distort and then harden into the distorted form. Exposure of stressed plastics to pollutants may lead to environmental stress cracking (ESC). PC, PE, PP, PMMA and PS are particularly susceptible. Aging reactions, such as crosslinking, oxidation and molecular rearrangement (physical aging), will "freeze" the plastic into the stressed (i.e. deformed) shape.
Flexible plastics, including PE, PP, PA and flexible PVC, may deform permanently under pressure by creep, e.g. sagging of appendages, flattening of bearing surfaces.
Well-padded supports, boxes, trays and mounts are necessary for storage, display and handling. Displaying and storing objects with proper supports, and in their proper shapes, will avoid stress and will prevent them from hardening into incorrect shapes. For instance, rubber shoes should be supported by a removable stiff interior form, such as a shaped block of PE foam. However, if the rubber is sticky, the support materials should be lined with a non-stick material, such as sheets of Mylar, Teflon, Gore-Tex or silicone release fabric.
Where possible, supports should be discontinuous, which allows gases to escape. PP needlepoint "canvas," for example, makes a good interior support for rubber boots. With all malignant plastics, there is a delicate balance between providing enough support and trapping emissions.
Most plastics have low scratch resistance (on the Mohs' scratch hardness scale, values of 2 [fingernail, amber, ivory] to 3 [copper penny]) and are soft, so they are susceptible to scratching, abrasion, denting and chipping caused by mechanical contact with other materials.
Recommendations
- Treat plastics as more fragile than expected.
- Avoid direct handling of objects
- Use trays and containers.
- Always support from below.
- Never handle by appendages or other features that jut out.
- Use rigid padded and shaped supports.
- Avoid flexing and vibration.
- Check for cracks and crazing, especially at glued joints, in painted areas and under or around adhesive labels, then support as required.
- Be wary of creep in objects and storage materials.
- Avoid contact with those solvents and solvent vapours that promote ESC.
- Avoid abrasive and chemical cleaners.
- Do not attach adhesive labels.
For more information on preventive conservation strategies to control physical forces, consult Agent of deterioration: physical forces.
Pollutants
Particles and dust adhere to sticky degrading surfaces, causing chemical damage and disfiguration that is not readily reversible. Abrasive dirt can scratch plastics, causing significant weakening in notch-sensitive plastics. All plastics are susceptible, but especially those that develop sticky surfaces due to migration of additives like plasticizers, such as CA, CN, PVC, PUR and rubber. Cleaning to remove particles and dust is very difficult to impossible, without causing more damage to the plastic.
Acidic atmospheric pollutants, such as sulfur dioxide and nitrogen dioxide, may accelerate decay and cause harmful effects, especially in humid conditions. Acidic pollutants catalyze hydrolysis of CA, CN, PA and PVC. Ozone, which might be produced by UV radiation or by electrostatic high-voltage sources, such as electrostatic air cleaners and photocopiers, can cause very rapid oxidative degradation. Most ozone emanates from exterior air pollution entering buildings. Until about the 1990s, fumigants and volatile biocides were commonly used in museums and these damage plastics. Pesticide and biocide residues in treated objects from this period continue to pose significant risks to adjacent plastic objects.
Other pollutants come from objects and materials in the museum as they degrade, such as nitrogen oxides from CN; acetic acid from CA, many woods and fresh paints; and sulfides and sulfur oxides from many vulcanized rubbers. Good ventilation is essential to prevent a build-up of harmful vapours around degrading or vulnerable objects.
Reused storage and display materials can be another, and often unexpected, source of pollutants. So-called "safe" materials, such as acrylics, can absorb harmful gases when used in one application, and then release those gases when re-used in a different application. The effect seems to be a question of solubility or polarity. For example, PE, a non-polar plastic, absorbs non-polar hydrocarbons readily, but hydrocarbons are not corrosive. PE does not absorb formic acid, which is corrosive. In both examples, PE remains non-corrosive. Polar plastics like PC, PMMA, PS and SI absorb acetic and formic acids, which are partially soluble in the plastics, but not nitric acid. In these scenarios, polar plastics may become harmful due to absorbed acids, depending on previous exposure to acidic environments.
Damage to plastics exposed to organic solvents and their vapours is often not immediately apparent. To complicate matters, specific plastics have specific vulnerabilities, e.g. some PMMA objects become crazed and cracked after exposure to ethanol. Vapour-induced ESC is enhanced by stress in the plastic, which often occurs if the plastic is restrained. Failure due to ESC depends on the material, the environmental conditions, and the nature and magnitude of the stress. ESC is therefore difficult to predict and can result in premature failure at stresses below normal fracture stress. Plastics prone to ESC may craze, spall or eventually fracture. ESC only occurs in amorphous plastics or the amorphous zones of semi-crystalline plastics (e.g. PE, PP, PMMA and PS). In addition to ESC, direct application of organic solvents and surfactants to plastics (such as during cleaning) will dissolve CA, CN, PA, PMMA and PS, or extract additives like plasticizers and stabilizers from PVC and rubber. For more information on cleaning, consult Five stages for controlling malignant plastics in mixed collections – Stage 5: clean.
Avoid all treatments on or near plastics that generate harmful gases. If an activity involving solvents is planned, for example painting or varnishing in the storage or gallery area, then remove all plastics temporarily to protect them from exposure.
Use of sorbents is recommended where ventilation is not possible. Combining the use of sorbents with the use of indicators, such as cresol red that detects nitrogen oxides produced by degrading CN (refer to Use and formulation for cresol red and modified bromocresol green indicators), is an effective method to slow the rate of deterioration and to detect the presence of noxious vapours should degradation occur. If the indicator has detected the presence of noxious vapours, it is time to replace the sorbents.
For plastics that degrade by oxidation, excluding oxygen from the air surrounding the objects is beneficial. Anoxic enclosures can be created using rigid containers like bell jars filled with inert gases, or bags made of flexible plastic barrier films filled with inert gases and oxygen scavengers (Figures 5 to 8). If transparent barrier films are used, the object remains visible and can be monitored, but cannot be examined closely as it is encapsulated. Plastics that are susceptible to oxidation and may benefit most from anoxic enclosures are hard rubber (Vulcanite, Ebonite) and PUR foam (especially ether-type). PA, unsaturated polyester, PE, PP, PS and flexible PVC are also susceptible to oxidation, but usually require light or UV exposure as well (photooxidation), so reducing light levels and removing UV are better options.
Recommendations
- Install good dust control.
- Check reused plastic products for absorbed pollutants, especially acids.
- Identify and monitor malignant plastics for emissions.
- Store objects at lowest temperature possible, to decrease degradation reactions.
- Block oxidation for objects susceptible to oxidation, such as rubber and PUR, by anoxic storage using bags made of flexible plastic oxygen barrier films, inert gas atmospheres, and oxygen absorbers. Anoxic storage is only suitable for objects that degrade by oxidation.
- Do not to clean surface accretions and dirt unless the object is to go on display or it is certain that accretions are causing degradation.
- If necessary, clean objects under dry conditions by careful brushing, vacuum cleaning, or dry wiping, taking care to avoid scratching by abrasive particles and action of solvents.
- Never use solvents, bleaches, detergents, wax or vinyl and rubber erasers.
- If water is required, use only moist wiping.
- Use non-stick shields and interleaves made of non-fibrous and non-foam sheets, such as PTFE, PET or SI, between sticky surfaces and objects to prevent staining by contact with surfaces having plasticizer or other additive exudation (bloom).
- Monitor objects in display and storage areas for emission of acids using indicator papers and ribbons with cresol red for nitric acid from CN and bromocresol green for acetic acid from CA (refer to Use and formulation for cresol red and modified bromocresol green indicators).
For further information on effects and mitigation of pollutants, consult Agent of deterioration: pollutants.
Light and ultraviolet
Light and UV damage both the structure of the polymer from which the plastic object is made, and non-polymer components of the object such as colourants, coatings and stabilizer additives (e.g. UV inhibitors). Manifestations of light and UV damage in plastic objects include discolouration (especially yellowing in uncoloured plastics), chalking, loss of impact strength, loss of tensile strength, embrittlement and cracking. Each effect may be caused by a different chemical process, and these processes probably occur at different rates. Some damage, such as yellowing, affects appearance but not mechanical strength (although it may indicate a serious degradation reaction), while other damage, such as embrittlement, affects the structural integrity of the object, leading to fractures and friable surfaces. Sensitivity of plastics to sunlight is shown in Table 4.
Level of sensitivity (maximum lifetime for daily exposure) |
Plastics sensitive to sunlight |
Plastics sensitive to UV |
---|---|---|
Low sensitivity No to negligible discolouration or embrittlement |
EP (some), fluoropolymers (FEP, PCTFE, PTFE), PMMA, PVAC, PVDF, PVAL, silicone rubber, UP |
fluoropolymers (ECTFE, ETFE, FEP, PCTFE, PTFE, PVDF), PMMA |
Medium sensitivity Slight discolouration, slight embrittlement |
ABS, cellulose esters (CA, CAB, CP), Cellophane, CF, ethyl cellulose, EVA, MF, PAs (PA 11, PA 6, PA 66), PC, PET, PF, POM, PS, HIPS, PVAC, PVAL, PUR, PVB, poly(vinyl formal), PVC (rigid, plasticized), PVDC, SAN, SBR, UF, UP, XLPE |
EVA, PAs (PA 11, PA 1.2, PA 4.6, PA 6, PA 6.6, PA 6.10), PET, PBT, PC, PFA, PVC (rigid, plasticized), PVDC, XLPE |
High sensitivity Discolouration, embrittlement, disintegration |
CN, polyolefins (HDPE, LDPE, LLDPE, XLPE, UHMWPE, PP, PMP, PB), PUR foam (rubber, natural, hard), SBR/Buna-N, shellac and natural resins |
ABS, HIPS, polyolefin (LDPE, LLDPE, HDPE, UHMWPE, PMP, PP), POM, PS, SAN |
Damage increases with increased intensity of incident radiation and with increased duration of exposure. Damage increases as incident radiation wavelength decreases (i.e. energy increases). Some plastics are discoloured or otherwise deteriorated by visible light but, in general, short wavelength radiation in the UV region is more damaging than longer wavelength radiation in the visible region. UV radiation should be eliminated by selecting lamps with no UV emission or by installing UV filters.
Most radiation damage involves oxidation. Oxidation proceeds more rapidly at a higher RH and higher temperature. Therefore, in addition to reducing intensity and duration of illumination, control strategies also should include reducing temperature, reducing RH, and reducing oxidation processes by, for example, incorporating antioxidants and using anoxic environments.
Recommendations
- Treat risk of light and UV damage to plastics as similar to natural organic materials, such as paper, wood, natural fibres and leather.
- Avoid all exposure to UV and sunlight.
- Use minimum intensity of light during display.
- Store objects in the dark.
For more information on damage caused by light, UV and infrared, as well as control strategies to prevent damage by them, consult Agent of deterioration: light, ultraviolet and infrared.
Incorrect temperature
The effect of increased temperature
Chemical degradation of plastics occurs mainly by oxidation (reaction with atmospheric oxygen) and hydrolysis (reaction with water contained in the plastic). Plastics have different sensitivities to oxidation at room temperature, as shown in Table 5.
When temperature is increased, the rate of oxidation and hydrolysis increases, and thus the rate of chemical deterioration increases. The effect on plastics is about the same as on natural organic materials like wood and leather. The rate of deterioration approximately doubles for each 5ºC increase or decreases by half for a corresponding decrease in temperature. Decreasing temperature is an effective control strategy for these degradation reactions, and is the current recommended practice for the storage of CN objects, and CN and CA photographic film (Bigelow 2004). Those plastics listed in Table 5 with the highest sensitivity to oxidation will be damaged most by increased temperature in storage, and conversely will benefit most by storage at decreased temperature.
Level of sensitivity to thermal oxidation at room temperature, approx. 20°C |
Plastics susceptible to thermal oxidation at room temperature |
---|---|
Low sensitivity (a few centuries, approx. 300 years) |
PC, PET, PF, PMMA, fluoropolymers (PTFE), SI |
Medium sensitivity (one human lifetime, approx. 100 years) |
CA, CF, some EP, MF, PAs (PA 6, PA 6.6), UP, PS, ester-type PUR foam, PVC, PVDC, UF |
High sensitivity (one human generation, approx. 30 years) |
PAN, polyolefins (PE, PP), POM, ether-type PUR foam, PVC, rubber (natural, hard) |
Temperature and physical properties
Physical and structural properties such as softness, flexibility, creep and strength change when temperature changes. Amorphous thermoplastics are particularly sensitive to temperature and are more likely to deform under stress at higher temperatures. This tendency is enhanced in the presence of organic solvents.
Measures of the sensitivity of plastics to increased temperature are:
- their glass transition temperature (Tg), the temperature at which the plastic changes from a stiff glassy material (below Tg) to a flexible rubbery material (above Tg)
- their heat deflection temperature (HDT), the temperature at which a bar of plastic measuring 127 mm (5 in.) in length, 13 mm (1⁄2 in.) in depth by any width from 3 mm (1⁄8 in.) to 13 mm (1⁄2 in.), supported at points separated by 101.6 mm (4 in.), becomes sufficiently flexible to deflect (bend) by 0.25 mm (0.01 in.) when subjected to a load of 1.82 Mpa (264 lb/in.2) at its centre
The greater the Tg or HDT of a plastic, the less likely the plastic is to deform as temperature is raised.
Ranges of interest for increased temperature are:
- 15 to 30°C in an occupied room
- 30 to 45°C in an unoccupied storage room without heating, ventilation or air conditioning
- above 45°C during heat treatments
Sensitivity of physical properties of plastics to increasing temperature ranked according to Tg and HDT is shown in Table 6.
Level of sensitivity of physical properties to increased temperature |
Plastics with Tg in increased temperature range Number beside plastic example indicates specific Tg temperature for that plastic.* |
Plastics with HDT in increased temperature range Number beside plastic example indicates specific HDT temperature for that plastic.* |
---|---|---|
High sensitivity Deformation may occur in the temperature range of 15 to 30ºC ("natural" variation in a room during summer with no heating, ventilation or air conditioning). These plastics have a Tg and HDT just above room temperature, so a slight temperature increase may cause loss of stiffness and deformation by sagging and creeping. |
Tg between 15ºC and 30ºC PMP (25) PVAC (29) |
HDT between EVA (23) |
Medium sensitivity Deformation may occur in the temperature range of 30 to 45ºC (possible in a room with heat sources and no heating, ventilation or air conditioning). These plastics have a Tg and HDT in this range, so they may become less stiff and deform by sagging or creeping when the temperature exceeds 30ºC. |
Tg between PAs (PA 11, PA 1.2, PA 6.10) (40) EVOH (43) PCTFE (45) |
HDT between LDPE (35) PMP (40) PVC plasticized (42) UHMWPE (42) MDPE (43) PA 11 (45) |
Low sensitivity No deformation occurs until temperature exceeds 45ºC (not likely in a room but possible during treatments involving heat). These plastics have Tg and HDT greater than 45ºC, so these plastics never lose stiffness, and deform by sagging or creeping. |
Tg between CA (49) PAs (PA 6, PA 6.6) (50-60) PLA (57) PBT (60-75) PVC, rigid (80-90) PVAL (85) HIPS (90) PFA (90) PS (90-100) ABS (96-108) CAB (100) CP (100) PMMA (100) |
HDT between HDPE (46) PTFE (48) PA 1.2 (48) PFA (49) XLPE (52) FEP (54) PP (55) PVDC (60) PBT (60) PVC rigid (65) ECTFE (65) CN (66) CA (67) PAN (69) CAB (70) ETFE (70) PA 6 (70) PET (73) CP (77) PF (77) HIPS (78) PS (80) PVF (80) PA 6.10 (83) PA 6.6 (85) PMMA (85) PVDF (88) ABS (89) SAN (95) CPVC (98) |
No sensitivity at temperature below 100ºC These plastics are commonly referred to as "engineering plastics." |
Tg above 100ºC CPVC (105) SAN (107.5) PTFE (115–130) PAN (117) CDA (120) PMMA (125) TPU (140) PC (150-175) COC (158) PI (295) aramid (375) |
HDT above 100ºC POM (123) PC (133) COC (134) PA 4.6 (153) PI (300) |
* Values for Tg and HDT are averages for the entire class of plastic listed. There can be a wide range of values for each plastic type. |
The effect of decreased temperature
As temperature is decreased, some plastics change from tough flexible materials to stiffer more brittle materials, especially if they are cooled below their Tg. Plastics shrink as they are cooled. Unrestrained plastics will not shatter spontaneously if they are cooled, but they will be more brittle and must be handled and supported accordingly, and not subjected to shock and vibration. Contraction of restrained plastic or plastic components in composite objects can result in fracture.
Measures of sensitivity of plastics to decreased temperature are Tg and brittleness temperature (Tbrittle), the temperature at which a plastic fails upon impact under specified conditions. Below this temperature, the plastic fractures. Above this temperature, no fracture occurs.
Ranges of interest for decreased temperature are:
- 15 to 4°C for objects moved from room temperature to cool storage in refrigerators
- 4 to -20°C for objects moved from cool to cold storage in freezers
- <-20°C for objects stored outdoors or in unheated storage rooms below freezer temperature
Sensitivity of physical properties of plastics to decreasing temperature ranked according to Tg and Tbrittle is shown in Table 7.
Level of sensitivity of physical properties to decreased temperature |
Plastics with Tg in decreased temperature range Number beside plastic example indicates specific Tg temperature for that plastic.* |
Plastics with Tbrittle in decreased temperature range Number beside plastic example indicates specific Tbrittle temperature for that plastic.* |
---|---|---|
High sensitivity Deformation may occur in the temperature range of 20 to 15ºC ("natural" variation in a room during summer with no heating, ventilation or air conditioning). These plastics have a Tg and Tbrittle just below room temperature, so a slight temperature decrease will increase stiffness, brittleness and fracture susceptibility. |
Near room temperature Tg between 15ºC and 20ºC No plastics have Tg in this temperature range. |
Near room temperature Tbrittle between 15ºC and 20ºC PMP (20) PS (20) HIPS (20) PMMA (20) SAN (20) |
Medium sensitivity Deformation may occur in the temperature range of 15 to 4ºC (moving from room temperature to cool storage). These plastics have a Tg and Tbrittle between room temperature and cool refrigerator temperature and cold freezer temperature, so they will be more stiff, brittle and susceptible to fracture, and may be damaged when moved to cool or cold storage. |
Cool Refrigerator Storage Tg between 4ºC and 15ºC No plastics have Tg in this temperature range. Cold Freezer Storage Tg between POM (-15) PVDC (-15) PE (-20) PP (-10 to 20) PVF (-20) |
Cool refrigerator storage Tbrittle between No plastics have Tbrittle in this temperature range. Cold freezer storage Tbrittle between -20ºC and 4ºC PA (0) ABS (0) PP (0 to -18) |
Low sensitivity Tg < -20ºC (Tg below freezer temperature) (plastic is always rubbery) Plastics with a Tg below freezer temperature are always in a rubbery state at any temperature above freezer temperature and do not pass through Tg when moved from room temperature to cool or cold storage. |
Tg below -20ºC PVC plasticized (-27.5) PVDF (-33.5) CR (-45.5) EVA (-48) PUR Elastomers (-48) POM (-55) BR (-68) NR (-70.5) IR (-80.5) BR (-90) SI (-98) PEs (LLDPE, LDPE, HDPE) (-110) |
Tbrittle below -20ºC PVC (-30) PET (-40) PUR elastomer (-51) NBR (-54) POM (-55) SBR (-62) natural rubber (-62) EPDM (-68) SI (-68) PUR (-70) PA (-80) PEs (PE, HDPE, LDPE, XLPE) (-100 to -120) PC (-135) Fluoropolymer (ECTFE, ETFE, PTFE, PFA, FEP) (-75 to -270) |
* Values for Tg and Tbrittle are averages for the entire class of plastic listed. There can be a wide range of values for each plastic type. |
When to use cool (4ºC in refrigerator) or cold (-18ºC in chest freezer) storage
Cool or cold storage should only be used for those plastics for which the benefit of reduced rates of oxidation and hydrolysis outweigh the risks of physical damage due to loss of flexibility and shrinkage-induced stresses, such as cellulose esters, PUR foam, natural rubber, and perhaps polyolefins. In all cases, objects should be supported and cushioned with inert materials to prevent objects from flexing.
Objects going into cool and cold storage should be bagged, preferably with moisture buffering material (e.g. matboard), with the bag collapsed so as to contain a minimum amount of air space. Bags and moisture buffers prevent damage from condensation when objects are moved from cold to warm conditions. Methods of implementing cool and cold storage are discussed below in the section Control strategies for mixed collections containing malignant plastics.
To decrease hydrolysis, temperature and RH should be reduced. Since storage at cool (refrigerator) or cold (freezer) temperatures requires equipment that is expensive to buy and maintain, it may be more beneficial and cost effective to use dry storage at RH less than 10% without refrigeration. This can be easily and inexpensively achieved by double bagging with dry desiccants and RH sensor strips to monitor RH. According to Michalski (2000), storage at 20ºC and 8% RH increases the lifetime of low stability objects by a factor of 10, from 30–100 years (at 20ºC and 50% RH) to 300–1000 years. With some cooling, the increase in lifetime will be even greater.
Shashoua (2004) noted that decreased temperature reduces the loss of volatile components, such as plasticizers, so highly plasticized plastics, such as flexible PVC, benefit from cold or cool storage.
Temperature fluctuation
The coefficients of thermal expansion (CTE) of plastics are about 10 times greater than those of metals and wood, and 100 times those of ceramics. Temperature changes cause physical stress in restrained plastics because of these high CTEs. Sudden temperature changes, even as small as 5ºC, can cause stress around fastenings or at the juncture with other materials. Freezing can be catastrophic if such a plastic is restrained in any way. When objects are moved to and from cold storage, the rate of cooling or heating should be such that the maximum temperature difference between parts of the objects (e.g. surface and core) is less than 6 to 10°C to prevent condensation (Padfield 2002). The importance of low rates of change of temperature becomes greater as the object thickness increases, because more time must be given for the object to equilibrate temperature across the greater thickness. Shashoua (2005) found no significant physical damage or condensation on thin walled objects (<1 cm / 0.4 in.) when cooled from ambient to freezer temperature at an uncontrolled rate. Condensation was detected on thick walled objects (> 1 cm / 0.4 in.) if temperature differences between the core and the periphery of the object exceeded 10°C. Controlled slow temperature changes must be maintained by gradual change of external temperature.
Recommendations
- Treat response of plastics to temperature as similar to that of natural organic materials.
- Avoid hot lights (e.g. exhibition and photography floodlights).
- Avoid proximity to any heat source (e.g. radiators, heating ducts).
- Avoid any storage or display practice that heats objects.
- Reduce temperature to decrease the rate of degradation reactions, to slow the loss of volatile components, such as plasticizers, and to decrease the amount of creep and distortion.
- Avoid flexing cold plastics, which become more brittle in decreased temperature.
- Use rigid, padded, shaped supports for cold objects.
- Avoid fluctuating temperature to decrease damage from stress cracking of restrained plastics.
Incorrect relative humidity
Water absorption by plastics is low, ranging from 0% to about 10% when immersed. Water absorption through exchange with ambient RH is even lower; equilibrium moisture content at 50% RH ranges from 0% to less than 5% for most plastics. As RH increases, moisture content increases; plastics swell, become more flexible (i.e. Tg decreases) and lose strength; and rates of chemical reactions like hydrolysis increase. Damp conditions support mould growth. Moisture content of plastics decreases as temperature increases, i.e. plastics dry out as they are heated. The magnitude of these changes varies for each type of plastic.
Damp, over 65% relative humidity
Damp is high RH but it is not wet, i.e. not covered by liquid water. Damp encourages mould growth if suitable nutrients, such as soluble protein, starch or sugar, are present. Table 1 in Agent of deterioration: incorrect relative humidity lists sensitivities of types of museum objects to mould. Synthetic polymers are not nutrients, so mould will not occur unless there is nutritious dirt like oils on the surface or the plastic contains nutrients like wood filler or plasticizers like diethyl sebacate, and there is sufficient moisture, in which case the plastic would have greater than medium sensitivity for mould growth. Most plastics have less than medium sensitivity.
Mould damage is usually restricted to unacceptable appearance such as staining, possibly accompanied by slight pitting of a thin surface layer by penetrating hyphae. Methods of dealing with mould can be found in Mould outbreak — an immediate response. Mould can be prevented by maintaining RH at less than 65%. There are no benefits to storage at greater than 65% RH, and there are few liabilities to less than 65% RH, so always maintain below 65% RH.
Relative humidity above 0%
Hydrolysis
Some plastics, particularly esters (CN, CA, PVAC), amides (protein, PA) and urethanes (PUR), degrade by hydrolysis, a reaction with water in the plastic. Hydrolysis is increased by acidic conditions, such as produced by pollution. The rate of hydrolysis is reduced by decreasing RH. The rule of thumb is that the rate of hydrolysis can be cut by more than half each time the RH is halved. The rate of hydrolysis decreases by much more than a factor of two each time RH is halved when RH is below 25% and reducing RH becomes increasingly more effective at reducing moisture content below about 10% RH. At some level of moisture content, there is so little water available for reaction that hydrolysis does not occur.
For example, PET will hydrolyze at processing temperatures if it is not dry. For processing of DuPont Teijin Mylar PET film, the manufacturer recommends to reduce the water content of the film to less than 0.1%, which occurs at about 10% RH, stating that more than this amount of water must be present in a system before the film can become embrittled due to hydrolysis (DuPont 2003). Thus 10% RH could be considered a critical upper value below which hydrolysis will not occur.
Sensitivity of plastics to hydrolysis at room temperature is shown in Table 8.
Level of sensitivity to hydrolysis at room temperature |
Plastics that are sensitive to hydrolysis |
---|---|
High sensitivity |
CA, CAB, CN, UF |
Medium sensitivity |
PA 6, PA 6.6, POM, PUR foam (ether-type), PUR foam (ester-type), rubber (natural, hard), CF, MF |
Low sensitivity |
epoxy, PAN, PC, PE, PET, PF, PMMA, polyester (unsaturated), PP, PS, PTFE, PVC, SI |
As plastics lose water as RH decreases, they become more brittle, more fragile, and more prone to fracture. Because of the increased fragility of plastics at low RH, extra support and care in handling will be required, as is normally appropriate for fragile objects. The benefits of decreasing the rate of degradation reactions by decreasing the RH outweigh the risk due to increased fragility, which can be controlled by proper handling and support. Information on the support of museum objects can be found in Mount-making for Museum Objects (Barclay et al. 1998).
Swelling
Swelling due to moisture uptake is quantified by the coefficient of moisture expansion (CME, also called coefficient of hydroscopic expansion and coefficient of swelling). This is the ratio of swelling to change in RH with the units of cm of swelling per cm of initial length per %RH (or microstrain/%RH, where [strain] = [change in length]/[initial length]). Sensitivity of plastics to moisture expansion (swelling) is shown in Table 9.
Plastics can only swell if they absorb moisture. A common measure of moisture absorption is the change in weight after immersion in water for 24 hours. This can also be a useful measure of susceptibility of plastics to damage after flooding. Water absorption of plastics is listed in Table 9.
Level of sensitivity to moisture expansion and water absorption |
Plastics that swell Number beside plastic example indicates specific CME in microstrain/%RH* |
Water absorption (24 h immersion) by plastics (%) Number beside plastic example indicates % increase in weight after 24 h immersion* |
---|---|---|
Low |
PS (0–2) fluoropolymer (0.6) PC (0.8) PVC-PVAC (6) PET (6) PF, cast, laminated (8-9) UF (11) PMMA (16) PVB (20) |
HDPE (0.0075) LLDPE (0.0075) UHMWPE (0.0075) PTFE (0.0075) XLPE (0.0075) COC (0.01) FEP (0.01) LDPE (0.01) PMP (0.01) PFA (0.02) Rubber, hard (0.02) PS (0.025) ETFE (0.03) PCTFE (0.03) PVDF (0.04) PP (0.055) EVA (0.068) CPVC (0.085) ECTFE (0.1) HIPS (0.1) PVDC (0.1) |
Medium |
POM (23) PF, moulded (30–40) ethyl cellulose (32–48) CAB (35) CN (40–42) CTA (42) PMMA (42) UF, moulded (70) |
PBT (0.15) PC (0.15) PET (0.15) PVC rigid (0.22) SAN (0.225) PMMA (0.25) PAN (0.3) POM (0.325) MF (0.4) PF (0.4) PA 610 (0.5) PVC plasticized (0.6) PUR (0.8) ABS (0.93) |
High |
CA (120) CF (1100) |
PA 1.2 rigid (1.15) PA 11 flexible (1.2) PI (1.39) PA 11 rigid (1.4) PA 12 flexible (1.4) UF (1.5) CAB (1.55) PA 6 (1.75) PA 66 (2) PVAC (2) CN (2) CP (2.1) CDA (2.15) PA 46 (2.5) CA (4.45) EVOH (8) CF (8) SBR (13) |
* Values for CME and water absorption are averages for the entire class of plastic listed. There can be a wide range of values for each plastic type. |
Note that CME for plastics (less than 200) is very much smaller than for natural biological materials like ivory (205), oil paint (248) and wood (400 to 700). Plastics, except CF, are much less sensitive to swelling than natural biological materials.
Plasticization by humidity
Water plasticizes plastics, which means that their Tg decreases as RH increases with a consequent increase in flexibility and decrease in strength. Strength changes could be abrupt if the Tg is lowered to ambient temperature. Loss of strength as RH increases could cause failures in load bearing applications such as nylon filaments suspending objects in display cases or plastic struts or adhesives in mounts. Failures could be gradual if filaments stretch by creep mechanisms or catastrophic if strength falls below breaking strength. Stresses can be created by the inherent weight of objects and parts.
Deliquescence of accretions
Some plastics, most notably highly vulcanized hard rubber (Ebonite, Vulcanite), CN, and CA, degrade by hydrolysis to produce ionic degradation products (sulfates, nitrates and acetates) that can react with atmospheric pollution or compounds in the plastic or surrounding materials to produce deliquescent accretions like ammonium sulfate, ammonium and calcium nitrate, and ammonium acetate (Figure 3). When the RH is greater than a specific value for each salt, deliquescent salts form droplets of salt solutions by dissolving in moisture absorbed from the air. Droplets of salt solutions on surfaces of plastics may damage other objects if they come into contact. Additional information on deliquescence is available under “RH above or below a specific critical value,” which can be found under Deterioration by incorrect relative humidity, and the collections most vulnerable in Agent of deterioration: incorrect relative humidity.
No plastics deliquesce, so this risk only occurs if there are deliquescent accretions on the plastics.
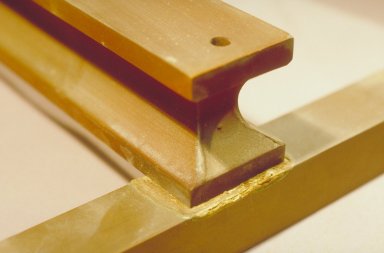
© Government of Canada, Canadian Conservation Institute. CCI 120210-0029
Figure 3. Sulfur in hard rubber (Ebonite, Vulcanite) oxidizes in air to produce sulfur oxide gases that react with moisture in the air to become acid solutions on the surface of the hard rubber. When in contact with metals, these acids react and produce deposits and accretions of corrosion products. These are often delinquent and dissolve in absorbed moisture at RH above critical deliquescence RH and produce puddles of corrosion products that spread across the metal. When the RH drops below the critical deliquescence RH, the puddles dry out and produce solid accretions of corrosion products.
Relative humidity fluctuations
For a detailed discussion on the effects of RH fluctuations, see the section "RH fluctuations" under Deterioration by incorrect relative humidity, and the collections most vulnerable in Agent of deterioration: incorrect relative humidity.
Rate of moisture absorption when relative humidity changes
RH fluctuations can only cause structural damage if a plastic absorbs or desorbs water fast enough that a significant change in water content occurs during the fluctuation. For example, for nylon, which is considered to be a moisture sensitive plastic, with 2.75% moisture content at 50% RH, the rate of moisture uptake or moisture change when RH changes is very slow. Hourly, daily, weekly, and maybe even monthly RH fluctuation by as much as 50% should have little effect on the moisture content of the plastic.
Recommendations
- Prevent high RH that can cause mould. Consult Agent of deterioration: incorrect relative humidity for details.
- Reduce RH.
- Low RH is better than high RH for all plastics because hydrolysis reaction rates are reduced.
- Assume that dry plastics are brittle so handle gently, avoid flexing, and use rigid, padded, shaped supports.
- Static electrical charge is enhanced at low RH so be wary of dirt pickup and disruptions of powdery and fibrous layers and surfaces.
- Avoid large RH fluctuations.
- This prevents cracking of moisture responsive plastics.
- RH fluctuation may cause surface crazing of UF.
- Excursions to high RH might cause swelling and warping of CF.
Control strategies for mixed collections containing malignant plastics
Do not panic when plastics are discovered in your collection—no matter how nasty they look nor how many there are! Most plastics are not malignant and even malignant plastics may not yet have become dangerous even if they look dirty, yellow or cracked. Instead:
- Identify which plastics are actually dangerous and remove them to a vented space for attention later.
- Identify the potentially dangerous plastics and arrange for them to be checked at regular intervals.
- Select one of the systems discussed in Stage 4 to suit the specific needs of the segregated items.
Basic control strategies
- Use barrier films to isolate malignant plastic components from the rest of the object (e.g. place a PET sheet between buttons and fabric on costumes or between the Ebonite insulator and brass conductor in telegraphy apparatus).
- Do not encapsulate or seal emissive plastics that emit degradation products, as this catalyzes degradation.
- Remove components of objects made from malignant plastics, and replace with replicated components made from benign plastics (e.g. replace CN costume stiffeners with PET replicas).
Optimum control strategies
- Avoid pollutants emitted by plastics in the collection by segregation of emissive malignant objects, adequate ventilation, and/or sorption of gases by sorbents.
- Ventilate storage areas to prevent accumulation of noxious emissions, which may catalyze degradation reactions.
- Use indicator papers and ribbons with cresol red to monitor and identify emissive CN objects, and use bromocresol green to monitor and identify emissive CA objects in display and storage areas (refer to use and indicator recipes below under Use and formulation for cresol red and modified bromocresol green indicators).
- Maintain storage and display areas at coldest possible temperature without temperature fluctuations.
Once properly contained, many of the objects can be returned to the storage room. Establishing priorities in this way controls hazards from degrading plastics without requiring excessive space, human resources or equipment. Collection resources are usually wasted on so-called "drastic plastics," i.e. the ones showing conspicuous, irreversible damage. Save your resources for those that can still be saved. Life-saving procedures are outlined in the following five stages.
Five stages for controlling malignant plastics in mixed collections
Stage 1: remove obviously harmful plastics
- If a plastic is clearly causing damage to surrounding objects and storage materials (i.e. they are corroding, sticky, discoloured, sweating or tendered); or
- If the plastic itself smells acidic, sulfurous, or is oozing, sweating, blooming or crumbling:
- Remove the plastic to a cool, segregated, ventilated space (e.g. fume hood or shaded porch), to be dealt with later (Stage 3 and 4). Handle with care; it is probably fragile and may have a very acidic surface. Immobilize any crumbly foam or fractured brittle plastics so that they will not be unnecessarily damaged by handling and movement.
- Clean the affected area, line the area with a PET sheet, and replace contaminated storage materials.
- Arrange for the conservation treatment of any non-plastic object that has been damaged.
- If a plastic is odourless, is not causing visible damage to its surroundings, and looks intact, proceed to Stage 2.
Stage 2: check the undeteriorated plastics for acidic emissions
In many cases, deterioration may still be in an early, invisible stage. Check each plastic with indicators so its emissions can be detected and controlled before they cause damage. Objects should be exposed to the indicator for at least 24 hours to ensure sufficient time to detect emissions.
- Cresol red will detect strong acidic oxidizing acids such as those emitted by CN.
- Modified bromocresol green indicator papers (A-D strips) will detect weak organic acids and sulfurous, sulfuric and hydrochloric acids, as well as plastics contaminated by acid emissions from poor storage conditions. The test should be carried out in the dark because A-D strips fade readily to a pale greenish colour, which is often mistaken for a positive acid reading. Bromocresol green is rapidly bleached by oxidizing agents, so has limited use as a monitor for CN plastics (refer to use and indicator recipes below under Use and formulation for cresol red and modified bromocresol green indicators).
- If the cresol red turns from yellow to pink, quarantine the plastic object in a cool, segregated and ventilated place (as above) to be dealt with later. Such a reading indicates that the object is already a severe hazard to the collection. Proceed to Stage 4.
- If the A-D strip changes from blue to green then yellow, quarantine in a cool, well-ventilated area and proceed to Stage 4.
- If no indicator changes colour, leave the plastic in storage and proceed to Stage 3.
Stage 3: identify potentially malignant plastics
At this stage, the actively harmful and visibly deteriorating pieces will have been removed from the collection and the remaining plastics will be (for the moment) quiescent. It will help in reducing the future workload to identify the potentially malignant plastics, since benign plastics will not need monitoring. Concentrate first on identifying objects containing CN, which is the most dangerous plastic in collections and needs special treatment. Fortunately, it is also one of the easiest to identify using spot tests. Reliable identification with spot tests takes practice so, if in doubt, skip Stage 3 and retest all plastics with indicators every six months, as in Stage 2.
By analysis or using spot tests (Table 3), determine which objects are malignant plastics.
- If the plastic is CN, leave in storage with a cresol red monitor (Figure 4). Check every six months and replace the monitor every two to three years.
- If the plastic is one of the remaining most malignant five, leave in storage and retest every six months with fresh indicators. (Unlike cresol red, A-D strips cannot be left as reference monitors.)
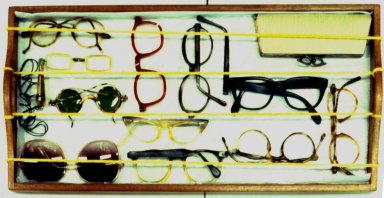
© Government of Canada, Canadian Conservation Institute. CCI 120210-0087
Figure 4. String dyed with cresol red used as reference monitor in storage. This method, with the monitor strung across mixed collections, is invaluable where CN has not yet been identified but is likely to be present (e.g. collections of fans, handbags, hats and semi-precious gems). The objects are accessible without removing the monitors.
Stage 4: cope with corrosive plastics
Once the plastics in storage have been monitored, it is time to revisit the quarantined items. There are several storage options, depending on the nature, size and strength of the plastic object. Rubber or highly plasticized objects may become soft and sticky, so they should be kept well-supported and interleaved, as necessary, with non-stick materials such as SI. The correct precaution may be selected from the following options.
Cool (4ºC) and cold (-18ºC) storage
Low temperatures reduce chemical reaction rates, and therefore reduce deterioration and emissions, creating a storage environment suitable for cellulose esters subject to hydrolysis and plastics subject to thermal oxidation. Slowing the rate of chemical decay reduces the physical stress that accompanies depolymerization and loss of stabilizers, thereby allowing the object to survive in displayable form for much longer.
Cool (about 4ºC), dark conditions are found in the refrigerator section of a frost-free refrigerator, or in a low-RH, cold storage room. Compared to room temperature, cool storage at 4ºC increases lifetimes by a factor of about 10, but does not stop it, so it must be combined with some method of removing emissions. Cold storage in domestic freezers, typically set at temperatures below -18ºC, reduces reaction rates and increases lifetimes by a factor of about 250.
Cool and cold storage is useful for small objects made from a single, unrestrained plastic, e.g. moulded Ebonite necklaces, PVC belts, foam rubber or PUR puppets. Composite objects with restrained components having different CTE may be at risk of fracture, but such occurrences seem to be rare. The benefits of low temperature storage outweigh the risks of thermal damage. This method is often used to prevent degradation of nitrate, acetate and propionate negatives until they can be copied onto a less reactive format. Consult the Incorrect temperature section for more details.
Objects going into cool or cold storage should be placed in water-proof containers to control humidity around the objects. Suitable containers are sealed glass or water-proof plastic containers or double bags such as PE or PET freezer bags. Plastics are more brittle when they are cold, so well-padded boxes and trays should be part of the package. Absorbents and buffers such as dry indicating silica gel or archival matboard should occupy about one-third of the air space remaining in the container.
The indicating silica gel will maintain its dry colour as long as the air in the container is dry. When the gel changes to its wet colour, it should be replaced with a fresh quantity. Used silica gel should be disposed; do not regenerate it because it is usually contaminated with volatiles from the plastics, which are difficult to remove completely. Monitoring should be done at least once a year.
Packages, such as recommended for cold storage of photographs, are appropriate. Bigelow (2004) describes suitable equipment and methods of cold storage.
Objects should be allowed to acclimatize to room temperature in their containers before being stressed by handling or exposed to ambient air and damaged by moisture condensing on the cool object. To reduce thermal stresses when moving an object from one temperature environment to another, place the object under thermal blankets or inside a Styrofoam cooler.
Sorbents
Some plastics emit volatile degradation products that may damage other objects nearby. It might be possible to control and lower the concentration of these emissions by methods used for collection facilities as described in Agent of deterioration: pollutants. For very emissive objects, or to control the immediate environment around the object, it may be necessary to isolate and contain the object in a sealed package. If so, the use of sorbents to remove emitted volatile degradation products will be necessary.
Sorbents can be used to remove emissions but they must be used with an understanding of their limitations or they can cause more damage than doing nothing. A major advantage in using sorbents is that the container of objects whose gases are being absorbed in a self-contained system can be returned to storage, provided there is regular monitoring.
i) Physisorbents (e.g. silica gel, activated charcoal, montmorillonite clays, zeolites)
Sorbents preferentially sorb specific compounds. To be effective, they must have selectivity for the pollutants, and have sufficient capacity to sorb large amounts of pollutants. For example, montmorillonite and zeolites are effective in controlling acetic and formic acid emissions from CA and UF. Physisorbents desorb as well as adsorb, so the adsorbed target pollutants may be displaced later by other gases, including moisture, or desorbed if the partial pressure of the pollutant drops and the pressure changes.
Physisorbents sorb water vapour. All gases surrounding a physisorbent compete for the reactive sites on the sorbent. In an atmosphere containing several gaseous components, the amount of each sorbed is approximately proportional to the concentration of the gas. At 50% and 25ºC, the concentration of water is about 10 g/m3 = 10,000 mg/m3. The odour threshold for acetic acid is 0.04 mg/m3. Thus, in a cabinet with a just perceptible odour of vinegar, the physisorbent will sorb predominantly water, not acetic acid. The corollary is that physisorbents will be most effective at sorbing pollutants in low RH conditions.
Method
A transparent box large enough for the object (or a tray supporting a double bag of a good vapour barrier such as PET) is lined with sorbent approximately one-third of the volume of the container. The object is placed on top, protected from direct contact with the sorbent by a cylinder of PP canvas or a shallow inner box. An indicator for the pollutant should be placed in the air space above the sorbent and close to the object, to enable monitoring that the sorbent is functioning and effective. The outer container is sealed.
ii) Chemisorbents (e.g. Ageless, calcium carbonate, or finely divided metal that removes contaminants by reacting with them to produce another substance)
Paper buffered with calcium carbonate has been used for many years to neutralize acids given off by CN and CA negatives by converting them into calcium nitrate and acetate. Unfortunately, its buffering action is not really effective at the low RH levels recommended for plastics, and the plastic object must not be in direct contact with the buffering agent because the reaction salts are deliquescent and absorb moisture from the atmosphere and liquefy.
Oxygen scavengers are suitable for PUR, rubbers, and plastics susceptible to photo and thermal oxidation. A simple and economic way of achieving oxygen-free conditions is to use an oxygen-absorbing material, such as Ageless, in envelopes or packages made from flexible, heat-sealed oxygen-barrier film (Figures 5 to 8). A disadvantage is the difficulty of knowing when to change the scavenger, because the Ageless Eye indicator is not very accurate. Oxygen scavengers are not useful for storing CN because the degrading plastic generates its own oxidizing agents and, more importantly, CN degradation occurs mainly through hydrolysis, not oxidation. Therefore, a better strategy for stopping hydrolysis is to reduce RH.
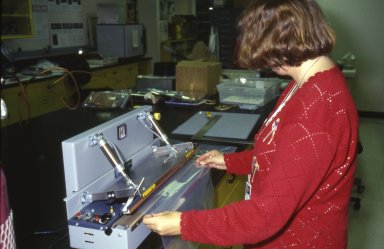
© Government of Canada, Canadian Conservation Institute. CCI 122641-0002
Figure 5. To prepare an oxygen-free (anoxic) storage envelope, begin by making a pouch by heat-sealing oxygen barrier film on three sides.
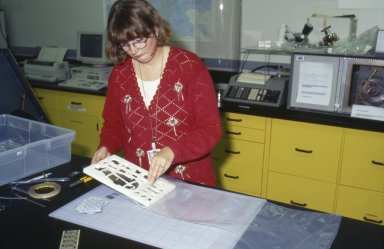
© Government of Canada, Canadian Conservation Institute. CCI 122641-0001
Figure 6. Mount objects into a support and then insert mounted objects into the prepared pouch.
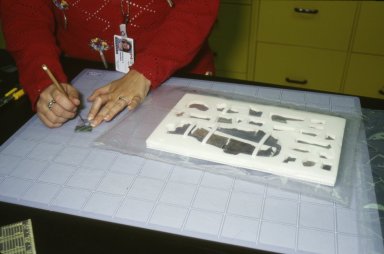
© Government of Canada, Canadian Conservation Institute. CCI 122641-0005
Figure 7. Puncture the Ageless Eye indicator sachet to expose the indicator to the atmosphere and then immediately insert the Ageless Eye indicator into the pouch with the mounted objects.
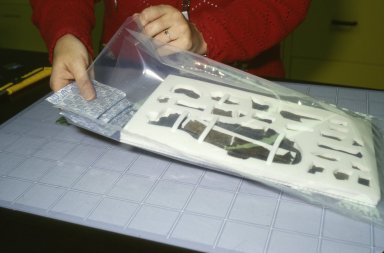
© Government of Canada, Canadian Conservation Institute. CCI 122641-0006
Figure 8. Insert a calculated number of Ageless oxygen absorber sachets into the pouch with the indicator and the mounted objects and then immediately heat-seal the open side to form a closed envelope.
Rigid containers like bell-jars that are flushed and then filled with inert gases can be used as an alternative to flexible plastic packages. Hermetically sealed display cases can be constructed and filled with inert gas, but these are difficult to build so that all seals are perfectly gas tight. Contact CCI for further information on sealed display cases.
Scavengers with particulate metal, for example Corrosion Intercept, are suitable for UF, PUR and rubber. Finely divided copper metal incorporated into a PE sheet or zipper-sealed bag acts as both a barrier and a scavenger; acid from objects enclosed in the bag reacts with the copper particles as it permeates through the PE. There is a visible change from a metallic copper colour to a dingy green-black when the reservoir of copper particles is used up. This makes monitoring very simple. The disadvantage is that the object is not visible, so fragile items must be carefully supported inside the wrapping, and bagged items should preferably be handled by means of trays. It is not known whether the rate of acid removal is always fast enough to prevent a harmful concentration of corrosive gases in the bag. If the odour from the object appears to be very strong, additional buffering material can be included.
Corrosion Intercept comes in sheet form, so heat-sealed containment can be tailored to fit awkwardly shaped items. Vacuum extraction to remove air can enhance the protection, or other sorbents can be enclosed with the object. Corrosion Intercept reacts with volatile sulfur compounds as well as acids. In combination with Ageless, it is a very promising storage method for rubber and PUR because the copper particles make the PE into an effective light and moisture barrier. However, there should be no direct contact with oily exudates, such as found on some PUR and PVC objects. Oily exudates swell the PE, and in some cases, the interaction of copper and PVC plasticizers creates stains on the PVC object.
Designated area with special ventilation and filtration
A designated area with special ventilation and filtration is suitable for all plastics. Good ventilation dilutes emissions to harmless levels around the object. Some institutions prefer to keep all of their plastics in one place in open storage, which allows emissions to diffuse away freely. Exposure to air, however, makes plastics vulnerable to damage from dust and pollution, especially if they have cracked or sticky surfaces. To preserve plastics, the ventilation area must have clean air, which can only be provided by special particle and gas filtration systems. Although once very expensive, improvements in the design of molecular filters and modifications in the size and distribution of the sorbents in commercial filtration systems has made filtration systems more effective and affordable. Additional details on ventilation and filtration control are found in Agent of deterioration: pollutants.
A designated area is the most expensive option, but it requires little ongoing maintenance. This option should be considered for highly priced collections, such as large plastic sculptures, or when a collection contains a large quantity of malignant plastics.
Stage 5: clean
Whether or not they are malignant, plastics from storage rooms are often dirty and may have sticky exudates that eventually harden and discolour. There is controversy about whether blooms and dirt should be removed. Given the state of knowledge at present, it is best not to clean unless the object is to go on exhibition and there is no substitute or replica that can be used instead.
Research on the cleaning of plastics by using dry mechanical methods with dry materials like cloths, sponges, brushes and cotton buds, and by using wet mechanical methods with the same cleaning materials moistened (not sopping wet) with aqueous cleaning agents containing dissolved agents like surfactants and chelating agents, and with organic solvents was recently reported by Balcar et al. (2012). Detailed information is given on the effects of these cleaning materials and agents for CA, HDPE, high impact polystyrene (HIPS), PMMA, and plasticized PVC.
The predominant parameters observed and evaluated after cleaning were scratching, change of gloss and cleanliness.
The main points revealed are that:
- Rubbing with dry cleaning materials tend to cause at least 10 times more scratching than the same cleaning materials moistened by cleaning agents (so long as the agents themselves do not cause damage). This was attributed to increased lubrication by the cleaning agents, but also could be due to softening of the cleaning materials by the cleaning agents.
- Cotton buds and microfibre cloths (polyester plus nylon) tend to be much more suitable than brushes and sponges when used with aqueous and organic solvent cleaning agents.
- High polarity solvents like acetone are damaging and unacceptable for cleaning any plastic.
- Least damaging but still effective organic solvents are those of low polarity such as white spirit, ethanol, isopropanol and xylene.
- Aqueous solution of surfactants and chelating agents are more effective for oily soils than organic solvents, but organic solvents are more effective than surfactants and chelating agents for waxy soils.
The best approach is to clean objects under dry conditions by careful brushing or vacuum cleaning. Sable hair brush, cotton buds, lens cleaning tissue made from pure cellulose or unimpregnated microfibre cloths are quite effective for wiping off surface dirt and bloom. Microfibre cloth of the kind specifically made to absorb oil is excellent for removing soaps and oily plasticizers. Do not use the same wipe on more than one plastic or more than one object for fear of cross-contamination with incompatible materials. Dispose of used lens cleaning tissue and buds and launder microfibre cloths very well. If simple techniques do not work, custodians are strongly advised to seek expert help from conservators.
In general, the recommended sequence for cleaning is:
- Remove dust by blowing clean air over the surface or vacuuming, assisted by sable hair brush.
- Remove loose particles with cloths (microfibre cloth is best) or cotton buds with a minimum number of gentle wipes applied with minimum force.
- Wipe with cloths or cotton buds moistened (not sopping wet) with distilled water.
- Wipe with cloths or cotton buds moistened with aqueous surfactant or chelating agent solutions.
- Wipe with cloths or cotton buds moistened with ethanol, isopropanol or white spirit.
Cleaning agents that were tested and are recommended are:
- 1% (w/w) non-ionic detergent (e.g. Dehypon LS45; Judith Hofenk de Graaff detergent concentrate: 50 g sodium dodecylbenzenesulphonate, 50 g triammonium citrate, 5 g carboxymethylcellulose in 1000 ml distilled water)
- 1% (w/w) anionic detergent (e.g. Orvus WA Paste)
- 2.5% (w/w) triammonium citrate
Never use oils, bleaches, wax, or vinyl and rubber erasers; these materials are no longer recommended because they can accelerate deterioration.
Risks of damage by cleaning
Degraded plastics are much more susceptible to damage by mechanical action as well as aqueous solutions and organic solvents, requiring greater vigilance to detect possible damage. Surfaces tend to become rougher and more fragile and therefore more susceptible to snagging by cleaning materials. Mechanical and structural properties change upon degradation and plastics may have unexpected behaviour, such as more susceptibility to ESC. Application of wet cleaning agents may result in absorption of water or solvent causing dimensional change and stress cracking. This is exacerbated if the plastic has lost strength due to degradation. This also is exacerbated if the plastic contains water absorbent fillers such as wood flour, commonly used in historic plastics, which swells much more than plastic. Microfissures produced as a result of degrading plastic may expose more filler.
Cleaning agents must be thoroughly rinsed from the object. Residues of surfactants and chelating agents are hygroscopic and increase the moisture content on the plastic surface. As RH decreases, these may dry out to become surface accretions.
Organic solvents are much more likely to cause damage to more types of plastic than aqueous solutions. This is the reason that aqueous treatments are listed first in the cleaning sequence.
Use and formulation for cresol red and modified bromocresol green indicators
The indicator(s) should be placed very close to the surface of the object but not in direct contact with it. It is easier and more effective to use string or netting to monitor large objects or whole drawers of objects than to suspend many small paper indicators (Figure 9a and 9b).
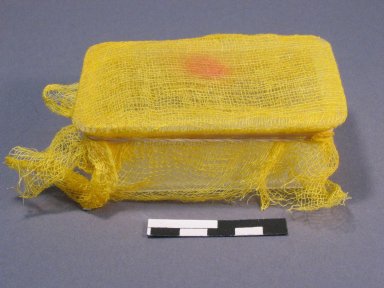
© Government of Canada, Canadian Conservation Institute. CCI 120210-0089
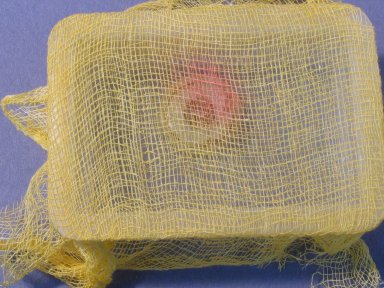
© Government of Canada, Canadian Conservation Institute. CCI 120210-0086
Figures 9a and 9b. Simple method for monitoring CN in storage using muslin dyed with cresol red. Emissions show clearly as red discolouration on the muslin, indicating that a plastic button on the object has become actively malignant and is a risk in storage unless the room is well ventilated. The open weave of the muslin allows the object to remain visible and noxious gases to escape (thereby lessening the chance of gas accumulating and further damaging the button).
Cresol red (for cellulose nitrate monitoring)
Cresol red should be applied only on cellulosic materials, e.g. blotting paper, boiled cotton string, muslin and netting. Although it will dye other materials, cresol red will interact with additives in synthetics, thereby affecting its accuracy as an indicator.
Dissolve 0.4 g cresol red powder in 100 ml water (0.40% w/v) or 0.005 g cresol red in 100 ml ethanol (0.005% w/v). The solution is red but cellulose immediately turns yellow when dipped. Tap the paper or wring the cotton to remove excess liquid. Turn frequently while it dries to prevent areas of high dye concentration. The dyed indicator material will become mottled as it dries unless there is access to a professional film-drying unit. Mottled indicators, however, work just as well. Re-dipping after it has dried gives a deeper colour (much more noticeable), but re-dipping is not necessary.
It usually takes at least 48 hours for a CN in the early stages of degradation to affect the indicator. Detection of rapid emissions is quicker, sometimes within an hour. Label any indicators left in storage as reference monitors, so they do not get thrown out by mistake. Notify all staff and volunteers of the significance of a colour change—and the imperative to report it. In this way, a CN object emitting noxious degradation products is likely to be detected well before the semi-annual check.
Bromocresol green (for cellulose acetate monitoring)
This formulation was perfected at the Image Permanence Institute (Rochester Institute of Technology), where blue paper indicators already impregnated with the bromocresol green dye (A-D strips) are available.
To prepare the bromocresol green reagent, first make an aqueous solution of sodium hydroxide by dissolving 4 g of sodium hydroxide in 1000 ml water. Then, take 160 ml of this solution and add 4.0 g bromocresol green.
Bromocresol green is light sensitive, so testing must be carried out in the dark. When testing plastics that are not museum objects—for example, Plexiglas display cases that are suspected of having become contaminated—the indicator paper can be placed directly on the plastic object to be tested then covered by a sheet of Mylar, which usually ensures a result within 24 hours.
Examples of preventive conservation practices
Segregating malignant plastic objects from the rest of the collection
Corrosion of metal components by CN objects in storage
Problem:
Within a storage drawer, some metal components, such as the iron tip of a buttonhook, were corroded (Figure 10). Examination showed that most of the plastic in the storage drawer was CN. The metals were corroding in the presence of oxidizing and acidic gases emitted by the degrading CN (Figure 11).
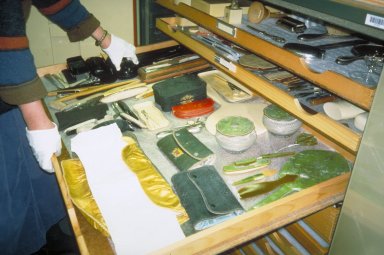
© Government of Canada, Canadian Conservation Institute. CCI 120210-0021
Figure 10. In a drawer filled with CN objects, corrosive nitrogen oxide gases can build up due to lack of ventilation.
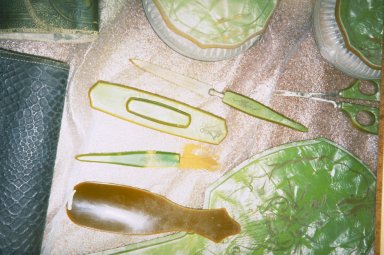
© Government of Canada, Canadian Conservation Institute. CCI 120210-0019
Figure 11. Corrosive gases from CN degradation have completely corroded the metal part of a buttonhook, leaving only a powdery corrosion residue in its place.
Solution:
Identify the CN objects and remove them to separate storage. Conditions in the separate storage should be as dry and cold as possible, and the storage well ventilated. Hydrolysis reactions are retarded at low RH, and low temperature slows all types of reactions. These conditions enhance preservation of CN. Also, low RH decreases the rate of corrosion of metals in the presence of acidic and oxidizing gases. Ventilation removes the acidic and oxidizing gases, thereby reducing their concentration in the storage space and consequently slowing the plastic degradation and metal corrosion reactions.
Isolating incompatible plastic components from the rest of the object
Exudation and deposition of additives on plastic surfaces
Problem:
Additives in plastics often migrate to, and deposit on, the surface of plastics (Figure 12). This problem is most often seen in plastics that are enclosed in a container or stored in cabinets, drawers or boxes with no or poor ventilation.
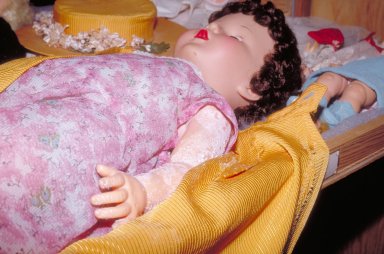
© Government of Canada, Canadian Conservation Institute. CCI 120210-0045
Figure 12. Additives in plastics often exude to, and deposit on, the surface, such as has occurred for metal carboxylates in this PVC doll.
Solution:
This phenomenon creates a dilemma. The exudates form on the surface in response to a concentration gradient: the concentration of the additive is greater in the plastic than on the surface so migration occurs to establish equilibrium. The exudate can be removed (or burnished to a less visible film) by wiping with a dry tissue. Removing the exudate may provide only a temporary solution. The deposit may form again because the concentration gradient still exists. Organic solvents or surfactant solutions should not be used because these can penetrate the plastic surface and cause future problems.
The deposit on the doll creates an additional problem. The exudate probably reacts with the clothing, either tendering or staining the cloth. The exudation occurs under the clothing as well as on the exposed arm. The plastic and clothing should be separated by removing the clothing from the doll, thus preventing damage to the fabric by the exudates.
Substituting inert materials for malignant plastics
Degradation products from CN damage adjacent materials
Problem:
The fabric of a collar is attacked and damaged by the acidic and oxidizing volatile degradation products from CN collar stays (Figures 13 and 14).
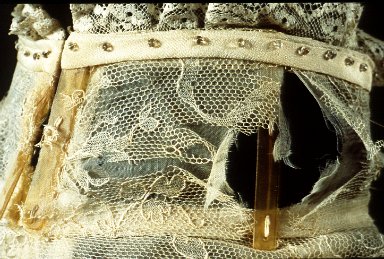
© Government of Canada, Canadian Conservation Institute. CCI 120210-0101
Figure 13. The collar fabric of this dress is attacked and destroyed by acidic and oxidizing volatile degradation products from CN collar stays (before treatment).
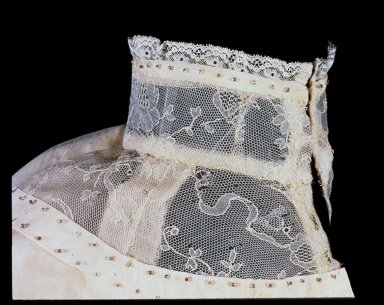
© Government of Canada, Canadian Conservation Institute. CCI 120210-0102
Figure 14. The CN stays were replaced by stays made from PET sheet (after treatment).
Solution:
The degraded CN collar stays were removed and saved in separate storage, appropriate for CN. Replica collar stays were made from inert PET sheets and substituted for the original CN stays.
Selecting the storage conditions to minimize degradation of least stable materials in composite objects
Degradation of CN and attack by degradation products
Problem:
CN is an inherently unstable plastic. It is the least stable plastic that may be encountered in a museum collection. As it degrades, CN produces acidic and oxidizing gases that attack other objects, causing degradation of organic material and corrosion of metals (Figure 15a and 15b).
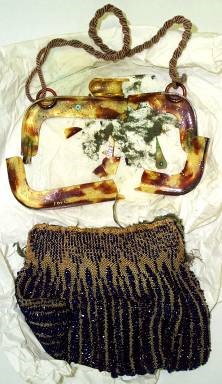
© Government of Canada, Canadian Conservation Institute. CCI 120210-0096

© Government of Canada, Canadian Conservation Institute. CCI 120210-0094
Figures 15a and 15b. Purse handle shows typical manifestations of CN degradation. A brass rivet is also corroded and the fabric lining is badly damaged from the gases.
Solution:
Degradation of CN is primarily by hydrolysis, the reaction of water with the CN plastic. Decrease the RH to slow the reaction. Acidic and oxidizing degradation products catalyze the hydrolysis reaction. Spaces containing CN objects, therefore, must be ventilated or have acid sorbers to remove the volatile degradation products and prevent catalysis of degradation. The rate of degradation of CN varies from object to object. Distribute and monitor indicator-saturated test strips, ribbons and papers close to CN objects to detect which particular objects are deteriorating, to give some indication of the rate of degradation and to alert staff if preservation measures are sufficient or objects should be removed to special storage.
Bibliography and further reading
Bibliography
-
Balcar, N., G. Barabant, C. Bollard, S. Kuperholc, B. Keneghan, A. Laganà, T. van Oosten, K. Segel and Y. Shashoua. "Studies in Cleaning Plastics." In B. Lavédrine, A. Fournier and G. Martin, eds., Preservation of Plastic Artefacts in Museum Collections. [N.p.]: Éditions du Comité des travaux historiques et scientfiques, 2012, pp. 225–268.
-
Barclay, R., A. Bergeron, and C. Dignard. Mount-making for Museum Objects, 2nd ed. Illustrated by C. Schlichting. Ottawa, ON: CCI, 1998.1
-
Bigelow, S. Cold Storage of Photographs at the City of Vancouver Archives (PDF format). [N.p.]: Canadian Council of Archives, 2004.
-
CCI. The Beilstein Test: Screening Organic and Polymeric Materials for the Presence of Chlorine, with Examples of Products Tested. CCI Notes 17/1. Ottawa, ON: Canadian Conservation Institute, 1993.
-
Coxon, H.C. "Practical Pitfalls in the Identification of Plastics." In D.W. Grattan, ed., Saving the Twentieth Century: The Conservation of Modern Materials: Proceedings of Symposium '91. Ottawa, ON: Canadian Conservation Institute, 1993, pp. 395–406.
-
Daniels, V., and S. Ward. "A Rapid Test for the Detection of Substances Which Will Tarnish Silver." Studies in Conservation 27 (1982), pp. 58–60.
-
DuPont Teijin Films. Product Information: Mylar Polyester Film (PDF format). Hopewell, VA: DuPont Teijin Films, 2003.
-
Michalski, S. Guidelines for Humidity and Temperature in Canadian Archives. Technical Bulletin 23. Ottawa, ON: Canadian Conservation Institute, 2000.
-
Padfield, T. "Condensation in Film Containers During Cooling and Warming." (PDF format) In Postprints of Preserve, Then Show. Copenhagen, Denmark: The Danish Film Institute, 2002.
-
Reilly, J. Instructions for Using the Wheel, Graphs, and Table: Basic Strategy for Film Preservation. IPI Storage Guide for Acetate Film. New York, NY: Image Permanence Institute, 1993.
-
Rémillard, F. Identification of Plastics and Elastomers – Miniaturized Tests (PDF format). Québec, QC: Centre du Conservation du Québec. 2007.
-
Roff, W.J., J.R. Scott and J. Pacitti. Handbook of Common Polymers. Cleveland, OH: CRC Press, 1971, p. 452.
-
Shashoua, Y.R. "Modern Plastics: Do They Suffer From Cold?" In A. Roy and P. Smith, eds., Modern Art, New Museums: International Institute for Conservation (IIC), Contributions to the Bilbao Congress, 13-17 September 2004. London, UK: IIC, 2004, pp. 91–95.
-
Vitale, T. History, Science, Preservation and Treatment of Cellulose Nitrate Still Film (PDF format). Emeryville, CA: Digital Imaging & Facsimiles Preservation Associates, 2009.
-
Williams, R.S. The Diphenylamine Spot Test for Cellulose Nitrate in Museum Objects. CCI Note 17/2, rev. ed. Ottawa, ON: Canadian Conservation Institute, 1994.
-
Williams, R.S., A.T. Brooks, S.L. Williams and R.L. Hinrichs. "Guide to the Identification of Common Clear Plastic Films." (PDF format) Society of the Preservation of Natural History Collections Leaflets 3 (Fall 1998).
Further reading
-
Albus, S., C. Bonten, K. Keßler, G. Rossi and T. Wessel. Plastic Art – A Precarious Success Story. Cologne, Germany: AXA Art Versicherung AG, 2006.
-
Grattan, D. W., ed. Saving the Twentieth Century: The Conservation of Modern Materials: Proceedings of Symposium '91. Ottawa, ON: Canadian Conservation Institute, 1993.
-
Heuman, J., ed. From Marble to Chocolate: The Conservation of Modern Sculpture. Postprints of Tate Gallery Conference, September 18–20, 1995. London, UK: Archetype Books, 1995.
-
Horie, V. Materials for Conservation: Organic Consolidants, Adhesives and Coatings. 2nd ed. Amsterdam, Netherlands: Butterworth-Heinemann, 2010.
-
Lavédrine, B., A. Fournier and G. Martin, eds. Preservation of Plastic Artefacts in Museum Collections. Paris, France: Comité des travaux historiques et scientifiques, 2012.
-
Loadman, J. Everything You Ever Wanted to Know about Rubber, n.d.
-
Plastics Historical Society. Plastics Historical Society Website, 2011.
-
Quye, A., and C. Williamson, eds. Plastics–Collecting and Conserving. Edinburgh, UK: NMS Publishing Ltd, 1999.
-
Shashoua, Y. Conservation of Plastics: Materials Science, Degradation and Preservation. Oxford, UK: Elsevier/Butterworth-Heinemann, 2008.
-
Shashoua, Y. Inhibiting the Deterioration of Plasticized Poly(vinyl chloride)–A Museum Perspective (PDF format). PhD thesis. Technical University of Denmark, 2001.
-
Tétreault, J. Airborne Pollutants in Museums, Galleries, and Archives: Risk Assessment, Control Strategies, and Preservation Management. Ottawa, ON: Canadian Conservation Institute, 2003.
-
van Oosten, T. PUR Facts: Conservation of Polyurethane Foam in Art and Design. Amsterdam, Netherlands: Amsterdam University Press, 2011.
-
van Oosten, T., Y. Shashoua and F. Waentig, eds. Plastics in Art: History, Technology, Preservation. Munich, Germany: Siegl, 2002.
-
Waentig, F. Plastics in Art: A Study from the Conservation Point of View. Translated by Michael Scuffil. Petersberg, Germany: Michael Imhof Verlag, 2008.
-
Williams, R.S. Display and Storage of Museum Objects Containing Cellulose Nitrate. CCI Notes 15/3. Ottawa, ON: Canadian Conservation Institute, 1994.
-
Williams, R.S. "Care of Plastics: Malignant Plastics." WAAC Newsletter 24,1 (January 2002), pp. 10–15.
-
Wright, M.M., and J.H. Townsend, eds. Resins–Ancient and Modern: Preprints of the Scottish Society for Conservation and Restoration (SSCR) 2nd Resins Conference, Aberdeen, September 13–14, 1995. Edinburgh, UK: SSCR, 1995.
© Government of Canada, Canadian Conservation Institute, 2018
Published by:
Canadian Conservation Institute
Department of Canadian Heritage
1030 Innes Road
Ottawa, ON K1B 4S7
Canada
Cat. No.: CH57-4/6-13 -2018E-PDF
ISBN 978-0-660-28019 -6
Page details
- Date modified: