Caring for textiles and costumes
Renée Dancause, Janet Wagner and Jan Vuori
Caring for textiles and costumes is part of CCI’s Preventive conservation guidelines for collections online resource. This section presents key aspects of managing the care of textiles and costumes in heritage collections based on the principles of preventive conservation and risk management.
Table of contents
- Understanding textiles and costumes and how they are damaged
- Causes of damage to textiles and costumes and key preventive conservation strategies
- Examples of preventive conservation practices
- Bibliography
List of abbreviations and symbols
Abbreviations
- CCI
- Canadian Conservation Institute
- HID
- high intensity discharge
- ISO
- International Organization for Standardization
- LED
- light-emitting diode
- RH
- relative humidity
- UV
- ultraviolet
Symbol
- µW/lm
- microwatt per lumen
Understanding textiles and costumes and how they are damaged
The long-term preservation of costume and textile collections is complicated by their diversity: textiles are made from any one or a combination of different natural and manufactured materials. A vast array of possible structures, both woven and non-woven, as well as a number of different dyes, finishes or decorations add to the range and complexity of textiles. In addition, textile objects come in a multitude of forms with varying functions, ranging from two-dimensional flags to three-dimensional costumes to oversized pieces of many shapes. This resource will assist in understanding and identifying the key characteristics of textiles.
General characteristics of textiles
Textiles have the following general characteristics:
- Organic (or inorganic) nature: Textiles are made from organic materials that are prone to natural processes of deterioration through exposure to ambient levels of light, temperature, humidity, dust and pollutants in the air, as well as through use and wear (Figure 1). Preventive conservation measures can slow down the rate of these deterioration processes but cannot halt them completely. Textiles can also be made from some inorganic materials or incorporate components such as glass, asbestos and metal.
- Fibrous structure: Fibres are long, fine, rod-like structures capable of being twisted together to form yarns. In a textile, a large surface area of fibres is exposed, making it susceptible to the effects of harmful substances in the environment.
- Flexibility: By their nature, textiles are very flexible and generally do not retain their shape without the aid of a support. They are prone to distortion, crumpling and creasing, which can become permanently set. If prolonged, creasing can form splits in the fabric, particularly in aged and weakened textiles. Unlike paintings, ceramics or other types of objects, textiles, especially costumes, may be stored flat, but they are usually displayed three-dimensionally and, as a result, have different needs in terms of volume, dimension and support.
- Absorbency: Most textiles are absorbent and porous, and they can readily become soiled or stained.
- Handling: Everyday textiles are often treated with a degree of familiarity not applied to works of art like paintings or sculpture. Museum textiles cannot be handled or cleaned in the same way as everyday clothing without the risk of damaging them.
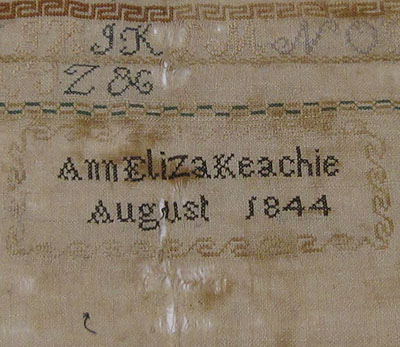
© Government of Canada, Canadian Conservation Institute. CCI 122559-0004
Figure 1. Detail of an embroidered sampler that shows discolouration of fibres, stains, breaks and losses at a fold line.
Most common textile fibres
The fibres that make up the majority of textiles in museum collections are classified as either natural fibres (plant or animal) or manufactured fibres (regenerated or synthetic). Other unusual or specialized fibres exist, but they are not discussed here.
Natural fibres
Natural fibres originate from plants or animals. Plant fibres may be classified as stem (bast), leaf or seed fibres, depending on which part of the plant provides the fibre. Because natural polymer cellulose is the major component in plant fibres, they are also known as cellulosic fibres. Cotton and linen textiles are the most common in Western museum collections; however, many varieties of cellulosic fibres have been used to create fabrics in various parts of the world including hemp, jute, ramie, sisal and coir.
Animal fibres, or protein fibres, are obtained from the coats of animals, such as sheep, or from the exudates of certain insects, such as the silk moth larva. The original function of natural fibres on a coat or exudate often has a bearing on the structure, properties and long-term preservation of the textiles created from them.
Consult CCI Note 13/18 The Identification of Natural Fibres to learn more about the characteristics of natural fibres.
Textiles and costumes predating the mid-20th century are most commonly made of one or more of the following natural fibre types:
- Cotton is a vegetable fibre obtained from the cotton plant (genus Gossypium). The original function of a cotton fibre is to accumulate moisture and provide it to the seed, which explains why cotton is so absorbent. Cotton fibres retain most of their original properties after processing and conversion into yarn. Though new cotton is stronger when wet, this may not be true for old cotton. Cotton fabrics wrinkle easily, are prone to shrinkage and may yellow over time. A detail of a cross-section and longitudinal view of a cotton fibre can be found in Figure 2.
- Flax is a long, soft fibre of the plant Linum usitatissimum. It requires several processing steps to produce the yarn and fabric called “linen.” The lustrous appearance of linen is due in part to the waxes it contains and to the long, smooth surface of the fibres. New linen is strong, absorbent, quick-drying and feels cool to the touch. These qualities make linen particularly useful for fabrics used next to the skin, such as undergarments and bed linens. Linen has a low resiliency and is prone to wrinkling. Over time, repeated folding of linen fabrics into sharp creases will cause the fibres and yarns in these areas to break. A detail of a cross-section and longitudinal view of a flax fibre can be found in Figure 3.
- Wool is an animal fibre composed mainly of keratin (a protein). Wool provides good insulation and very good moisture absorption, holding up to one-third of its own weight in water without feeling damp. Wool fibres, which are relatively weak, become weaker when wet. Wool is also very elastic due to its crimped molecular structure. The wool fibre has overlapping scales that cover its outer surface. With moisture, heat and mechanical action, these scales can become interlocked in a process known as felting. A detail of a cross-section and longitudinal view of a wool fibre can be found in Figure 4.
- Silk is obtained from the larva of the silk moth caterpillar, more commonly known as the silkworm. The silkworm secretes a viscous liquid that immediately solidifies and forms a continuous fibre or filament. The extruded filament is composed of a protein called “fibroin” that is coated with a gummy substance called “sericin.” In the processing of silk fibres, the filaments from several cocoons are gently unwound simultaneously and combined into a single yarn. Although the silk fibre is very fine, it is very strong, provides good insulation and is absorbent. The fibres become weaker when wet. In contrast to wool, silk is not very elastic. Silk is sensitive to light. A detail of a cross-section and longitudinal view of a silk fibre can be found in Figure 5.
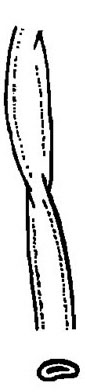
© Government of Canada, Canadian Conservation Institute. CCI 129981-0003
Figure 2. Detail of a cotton fibre.
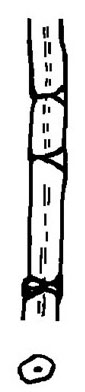
© Government of Canada, Canadian Conservation Institute. CCI 129981-0003
Figure 3. Detail of a flax fibre.
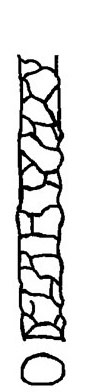
© Government of Canada, Canadian Conservation Institute. CCI 129981-0003
Figure 4. Detail of a wool fibre.
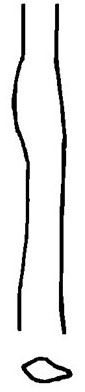
© Government of Canada, Canadian Conservation Institute. CCI 129981-0003
Figure 5. Detail of a silk fibre.
Manufactured fibres
Manufactured fibres are made by extruding a liquid polymer through small holes in a spinneret (a device much like a shower head). The extruded polymer emerges as long filaments, which can either be twisted loosely together to form filament yarns or cut into short lengths for spinning into staple yarn.
- Modified natural polymer fibres are made from polymers that exist in nature, such as the cellulose from plant materials. Naturally occurring polymer is chemically converted into liquid for extrusion and is then regenerated into a solid fibre. Due to the processing, the properties of fibres such as rayon (made from cellulose obtained from trees) are different from those of cotton (made from cellulose obtained already in fibre form from the seed boll of the cotton plant). Rayon is more absorbent but much weaker than cotton, particularly when wet.
- Synthetic fibres are created directly from chemicals rather than from naturally existing polymeric materials and have been in use since their creation in the 19th and 20th centuries (Table 1). Examples of synthetic fibres include nylon, polyester and acrylic. The properties of synthetic fibres vary depending on the raw materials and the processes used in their manufacture. For example, nylon has poor resistance to sunlight, whereas acrylic has good resistance.
Date | Manufactured fibre | Chemical composition | Place of origin |
---|---|---|---|
1884–89 |
Chardonnet silk |
regenerated cellulose |
France |
1899 |
cuprammonium rayon |
regenerated cellulose |
Germany |
1903 |
viscose rayon |
regenerated cellulose |
United Kingdom |
1924 |
cellulose acetate |
cellulose ester |
United Kingdom |
1940 |
nylon |
polyamide |
United States |
1950 |
acrylic |
acrylonitrile |
United States |
1951 |
polyester |
poly(ethylene terephthalate) |
United Kingdom |
Fabric structure
Woven textiles
Woven textiles are produced by interlacing two sets of yarn. One set of yarn, the warp, is put under tension and kept parallel. The second set, the weft, is worked in perpendicular, over and under the warp. A selvedge (from “self edge”) is a finished edge. It is formed where the weft doubles back over the outermost warp yarn. The presence of two selvedges indicates the width of the woven cloth. Warp yarns are usually stronger than those used for the weft because the warp must be kept under tension during weaving. When the fabric is folded on an angle, so that the warp and weft lie parallel, the true bias is indicated (Figure 6).
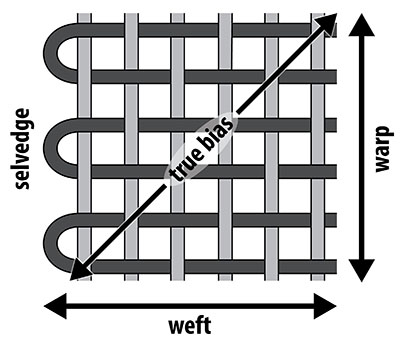
© Government of Canada, Canadian Conservation Institute. CCI 129981-0004
Figure 6. Detail of the selvedge of a textile, the perpendicular woven structure of the warp and weft sets of yarn, and the true bias.
There are three basic weave structures: plain (Figure 7), twill (Figure 8) and satin (Figure 9). With a few exceptions, all other weaves are variations or combinations of these.
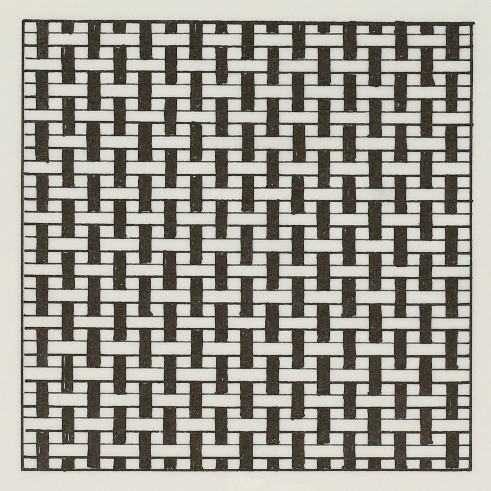
With the permission of the Royal Ontario Museum © ROM
Figure 7. Plain weave, also known as tabby weave, follows an over-under pattern.
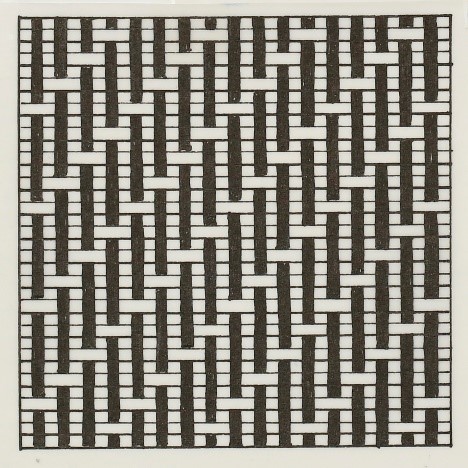
With the permission of the Royal Ontario Museum © ROM
Figure 8. Twill weave forms a diagonal ribbed pattern.
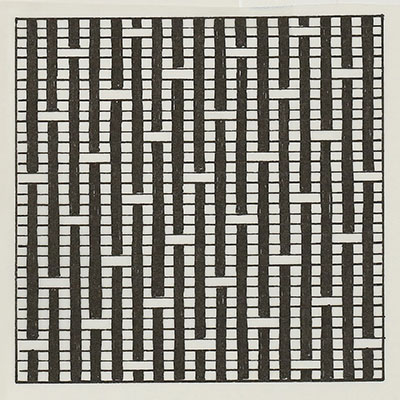
With the permission of the Royal Ontario Museum © ROM
Figure 9. Satin weave has long floating yarns which gives a smooth, lustrous appearance.
Certain aspects of fabric structure have implications for preservation. For example, the smooth lustrous appearance of satin weave is created by long floating yarns on the surface of the fabric. These yarns may easily be pulled out of alignment, changing the lustre and even the colour of the fabric, sometimes irreversibly. The raised pile of fabrics such as velvet is prone to crushing and distortion. Even minor disruptions in the pile are quite noticeable. Woven fabrics have the greatest stretch in the bias direction, so bias-cut garments will distort if not stored correctly.
Some fabrics are prone to shrinkage due to the type of fibre, yarn or weave. For example, crepe fabric made from overtwisted yarns, very popular as a dress fabric in the early to mid-20th century, is very prone to shrinkage. Similarly, loose weaves will shrink during washing and drying. Fabric shrinkage is irreversible.
Knitted textiles
Knits (Figures 10a and 10b) are made by interlooping yarns by hand or machine. Loops, formed by needles, are drawn through previously formed loops. The resulting structure makes knits quite wrinkle-resistant, form-fitting and stretchy. They are easily deformed and can stretch out of shape if they are hung vertically for display or storage. Often, this distortion becomes irreversible.
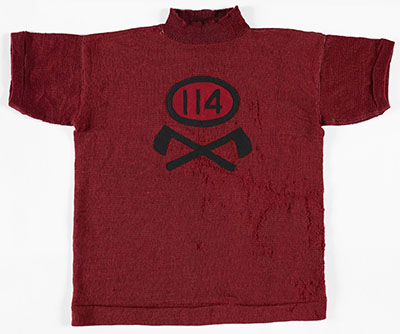
© Government of Canada, Canadian Conservation Institute. CCI 126197-0024
Figure 10a. Knit sports jersey.

© Government of Canada, Canadian Conservation Institute. CCI 126197-0037
Figure 10b. Detail of knitted textile.
Non-woven textiles
Some textiles, referred to as non-wovens, are made directly from fibres by bonding or interlocking manufactured fibres either mechanically, thermally, with adhesives or with a combination of these techniques. While non-woven textiles do not ravel if cut, they are inelastic and do not regain their original shape if stretched. Felt is an example of a non-woven textile. Historically, felts were made of wool. Modern-day felts can be made of blends of natural and/or manufactured fibres.
Other textile techniques
Textiles are made with a variety of other techniques, including crocheting, lacemaking, netting (Figure 11) and braiding. Netting (commonly found in veils) and lace (a form of netting, of which there are many kinds) are usually delicate fabrics with many open areas that can snag and tear easily.
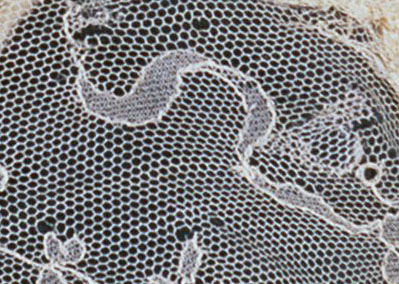
© Government of Canada, Canadian Conservation Institute. CCI 120210-0102
Figure 11. Detail of netting.
Dyes, finishes and embellishments
Since antiquity, textiles have been coloured by means of dyes. Until the commercial introduction of synthetic dyes in the latter half of the 19th century, all dyes were obtained from natural sources, such as plants and certain shellfish and insects. Dyes may be applied to fibres, yarns, fabrics or finished articles, usually by immersion in a dye bath. Dyes may also be mixed with mordants to fix the dye to the fibre and with thickening agents to form pastes that can be used to print patterns onto textiles. Paints, consisting of pigments in a binder, have also been used to embellish certain kinds of textile objects, such as flags and banners.
Textiles may also be decorated using stitching techniques, such as embroidery and appliqué. Surface ornamentation may include a host of other materials, such as beads, sequins, metal threads (Figure 12), feathers and paper.
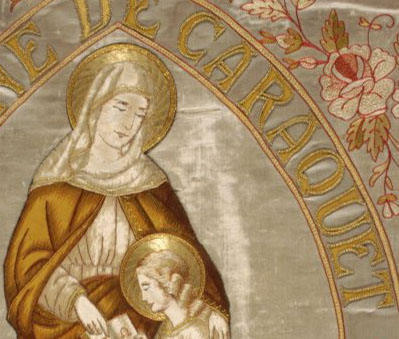
© Government of Canada, Canadian Conservation Institute. CCI 71565-0006
Figure 12. Banner embellished with metal threads as well as silk embroidery.
A great number of processes have been applied to fibres, yarns or fabrics from the 20th century onward to alter their properties. These processes can be chemical (e.g. weighting of silk) or mechanical (e.g. moiré silk, napped woollens) and either permanent or impermanent. Some are applied for aesthetic reasons, to alter texture, lustre or drape, and others for functional reasons, to improve ease of care, comfort and durability, or to provide protection (e.g. fire retardant). A variety of materials, including starches, waxes, glues and clays, have been applied to textiles as finishes (e.g. glazes on cotton).
Intrinsic vulnerabilities
Intrinsic vulnerabilities are those arising from how the textile was made, other materials that were used during manufacture and how the textile was used. The following processes are common ways in which textiles have intrinsic vulnerability.
Weighted silk
Some manufacturing and finishing processes have disastrous consequences for the preservation of textiles. A classic example is the weighting of silk with metallic salts that contain metals such as iron and tin. These agents were added to silk to improve drape and to restore the weight that it would lose as a result of degumming, a process whereby the natural protein sericin was removed from the fibre to improve lustre and increase dye uptake. Unfortunately, the metallic salts led to acidic deterioration of the fibres and greatly increased silk’s sensitivity to light damage. As a result, many weighted silks and the costumes made from them are extremely weak, brittle and fracturing—a condition known as “shattered silk” (Figure 13). During the 19th and 20th centuries, silk was often weighted with excessive amounts of metallic salts, even though their harmful effects were known.
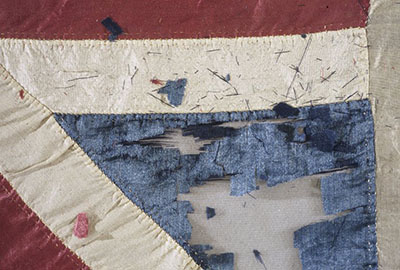
© Government of Canada, Canadian Conservation Institute. CCI 73924-0045
Figure 13. Detail of deteriorated weighted silk flag.
Metal mordants
Another example of a deleterious manufacturing process is the use of iron salts in dyeing. Dark, brittle textile fibres might have been dyed or printed using an iron mordant. Iron causes acid deterioration and catalyzes the photooxidation of the organic materials in textiles, resulting in significant or complete loss of strength over time. Other metal mordants (e.g. aluminum) have been used in the past to a more limited extent and can have similar damaging effects.
Bleaching
Most bleaches are harmful to textiles. Despite this, they were often used to whiten fabrics either during manufacture or use. For example, silk was bleached with sulfur to remove any original yellowness. White silk in very poor condition that is not weighted might have been bleached.
Causes of damage to textiles and costumes and key preventive conservation strategies
Textiles and costumes are some of the most sensitive items in museum collections. Textiles can be damaged by external agents of deterioration, such as elevated levels of light, ultraviolet (UV) radiation, inappropriate relative humidity (RH) and temperature, attack by insect pests and rodents, and poor handling, display and storage practices. Wearing historical costumes can cause damage and is not recommended. In some cases, intrinsic agents such as deleterious manufacturing processes or the presence of incompatible or actively degrading materials within a textile object can also contribute to its poor condition.
Physical forces
Holes, tears, distortions, losses and splits can have a number of causes. Sharp creases along fold lines have the potential to fracture because the fibres in those areas are under considerable stress.
Tearing due to stresses is also a common problem in textile objects (Figure 14).
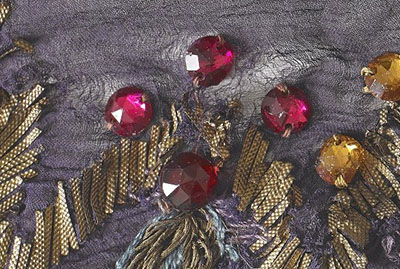
© Government of Canada, Canadian Conservation Institute. CCI 124901-0102
Figure 14. Delicate crepe fabric has become distorted and torn around red faceted cut glass faux jewels due to the weight of the ornamentation.
Handling increases the potential for damage to costumes and textiles. Historical textiles often appear deceptively strong and resistant, but they are vulnerable to damage not only due to their past history (age, wear, fragility) or composition (including combinations of heavy and lightweight materials), but also because they are familiar objects. As a result, historical textiles might have been handled more casually than other heritage objects. Threads holding decorative elements, such as beads and sequins, might have weakened through wear and use or through various deterioration mechanisms, thereby exposing the decorative elements to a high risk of loss.
Costumes on ill-fitting mannequins or heavy flat textiles on vertical display without adequate support may become distorted due to the effects of gravity.
Even with the most careful handling, mounting a costume on a mannequin can involve a great deal of manipulation; as such, this type of handling can result in undue stresses on certain parts of the garment.
In transit, direct physical forces, such as vibration or shocks, can result in abrasion over time.
Water
Accidental wetting from floods, roof leaks and other incidents poses a high risk of severe damage to textile collections. Types of water damage that can occur to a textile include shrinkage, loss of flexibility, stretching and tears (due to the inability of fibres to support the additional weight of water), formation of tide lines upon drying (Figure 15), soiling from dirty water, stains from running dyes, corrosion from contact with metal elements and contamination and stains from mould growth. If left to dry without treatment for an extended period of time, these damages become difficult or impossible to reverse.
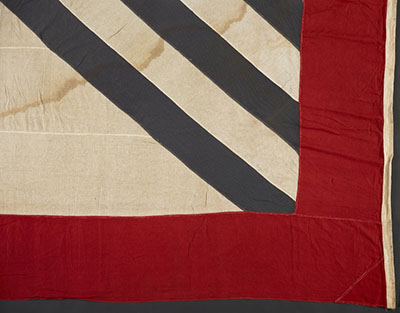
© Government of Canada, Canadian Conservation Institute. CCI 127438-0045
Figure 15. Tide lines have formed on this textile.
Excess water will penetrate natural and some manufactured fibres. When this happens, the fibres can swell, subjecting them to accelerated deterioration from chemicals in their surroundings or from biological agents, which can also cause physical damage.
Bacteria may be present on textiles due to contamination at the time of original use or from more recent contact with stagnant water or sewage present in flood waters. Bacteria require nearly 100% RH (i.e. wet or almost wet conditions) to grow.
Wool fibres are exceptional in that they are able to take up an enormous quantity of water; however, when wet, they are sensitive to mechanical damage.
Pests
Insects
Textile and costume collections are highly sensitive to the risk of insect attack because they not only offer a food source for some insects, but they may provide a habitat, since textiles and costumes are often housed in undisturbed, dark environments, which insects seek. Clothes moths and carpet beetle larvae are particularly damaging: they perforate and consume wool or other keratinous protein fibre, such as feathers and furs, but can also attack silk, cotton and synthetics if soils are present or if these fabrics block the way to their food source. Other insects, such as silverfish and cockroaches, will damage fabrics to get to a source of nourishment, such as the starch sizing of cotton or paper.
Holes in wool fabrics (Figure 16) often indicate insect attack, together with patchy areas from which the nap or pile is missing, a condition often referred to as “grazing” (Figure 17). Other signs of insect activity include observing the actual larvae, insect webs and casings (often containing fecal pellets that may be the same colour as the textile), larval skins that have been shed, eggs, frass and the presence of adult insects.
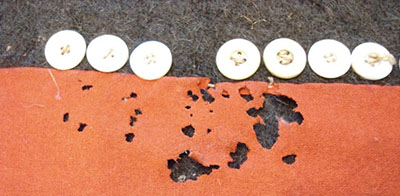
© Government of Canada, Canadian Conservation Institute. CCI 123268-0037
Figure 16. Holes in wool fabric caused by insect attack.
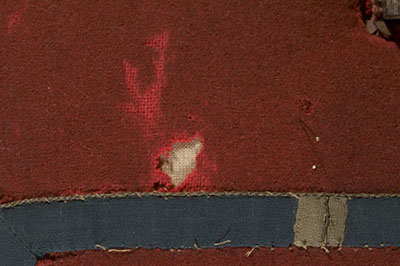
© Government of Canada, Canadian Conservation Institute. CCI 73062-0034
Figure 17. Insect hole and grazing mark on wool.
Vertebrate pests
Damage by rodents is indicated by chewed or shredded textiles and by the presence of animal droppings and other debris. Birds and animals soil textiles, producing stains that are very difficult, if not impossible, to remove and that are damaging to the fibres. These stains can, in turn, attract insects. Consult Agent of deterioration: pests for information on protecting heritage collections from pests.
Mould
Textiles can be attacked by mould; this is discussed further under Incorrect relative humidity.
Pollutants
Textiles provide many places for dust and particulates (solid contaminants) to lodge. Particles can be trapped in the spaces within and between yarns and on irregular fibre surfaces. The most common solid contaminants are combinations of soil, soot, sulfate and nitrate compounds, and dust and salt, either airborne or from handling. Particulates are often acidic due to adsorbed pollutant gases, which may lead to harmful chemical reactions to the fibre or dye under high humidity. Particles may also contain trace metals, which can catalyze the photodeterioration of fibres exposed to light. Sharp, gritty particles of silica, commonly found in dust, can cut through fibres. Some particulates are food sources for moulds and insects (e.g. dander, wool and silk carpet fibres).
Liquid contaminants that might harm textile objects include plasticizers migrating from certain plastics (e.g. poly[vinyl chloride]), oils deposited from improper handling, water and food stains, and stains from use. Water and oil (e.g. from perspiration during use or when handling with bare hands) can carry soils inside the fibre structure by capillary action. Over time, these stains oxidize and cause disfigurement, fibre-weakening and breakage (Figure 18). Stains become set over time, a process accelerated by heat and moisture.
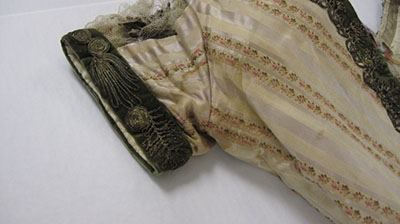
© Government of Canada, Canadian Conservation Institute. CCI 127501-0021
Figure 18. Soiling, such as underarm stains, may oxidize over time, becoming more visible and causing deterioration of the fabric.
Gaseous pollutants, such as sulfur dioxide, nitrogen dioxide, hydrogen sulfide and ozone gases, result from industrial, vehicle and other types of emissions. Once adsorbed onto the surfaces of fibres, they cause degradative chemical reactions, which affect fibre properties. For example, sulfur dioxide forms acid in the presence of moisture, making textiles acidic and ultimately weakening the material and affecting its dyes. Some natural and synthetic dyes may be sensitive to sulfur dioxide, nitrogen dioxide or ozone present in the ambient air, which may result in fading.
Certain dye-fibre combinations change colour in response to atmospheric pollutants, a process called “fume fading.” For example, acetate and nylon dyed blue (using disperse dyes) react with oxides of nitrogen and turn pink.
Gases emitted by materials within the museum include acids from wood, coatings, acidic tissue paper and storage materials or other objects. Ozone is an oxidizing agent and is given off by electronic air cleaners, photocopy machines and UV light sources. Acidity of fibres can also result from the deterioration of the fibre itself and from manufacturing and finishing processes.
Consult Agent of deterioration: pollutants for more details on pollutants and how they affect heritage collections.
Light and ultraviolet
Exposure to light, both visible and UV, can deteriorate textiles. Damage depends on the intensity of the light, the length of exposure and the proportion of UV radiation. Light damage is both cumulative and irreversible. All components of light are harmful.
UV radiation is more damaging to the structure of organic materials: it damages textile fibres, causing yellowing, weakening and disintegration. It also contributes to the fading of dyes and colourants. Daylight has a significant amount of UV radiation. It is also present in high quantities in high intensity discharge (HID) lamps (e.g. xenon and mercury lamps) and in medium quantities in fluorescent lights. There are low quantities of UV radiation in incandescent lights, and it is absent in most white light-emitting diodes (LEDs).
Visible light causes fading of most dyes and colours, including either the fading or darkening of the natural colours of (undyed) fibres. It can also contribute to fibre-weakening, especially its violet component.
Infrared radiation, in the form of heat, desiccates textiles and hastens their natural aging (as discussed under Incorrect temperature).
Fibre damage
Damage to fibres is caused mainly by UV radiation and occurs through the process of photooxidation, also known as phototendering, which results in the weakening and embrittlement of fibres (consult Table 2 for more details). Photochemical damage such as this occurs faster in the presence of moisture and metal ions (traditionally used as mordants), which act as catalysts to the chemical reactions.
Certain traditional dyes may exacerbate the problem. Weighted silks will undergo extreme photodeterioration due to the presence of the weighting agents and may virtually self-destruct within a short lapse of time (Figure 19). Of the natural fibres, flax is the most resistant to light damage (visible and UV), and silk is the most vulnerable. Acrylic is the most resistant manufactured fibre, while nylon and elastomeric materials, such as spandex, are the least resistant. The long-term instability of some of these modern materials will have a great impact on the preservation of collections from the latter half of the 20th century.
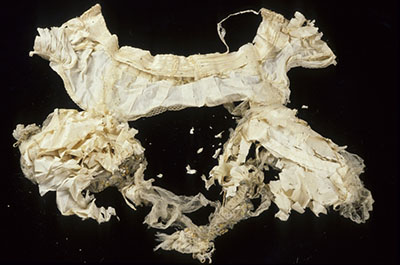
© Government of Canada, Canadian Conservation Institute. CCI 129981-0012
Figure 19. Shattered weighted silk costume.
In the case of painted textiles, UV radiation can also cause physical damage and disintegration of the paint media (chalking), which usually results in an overall fading of the paint colour even if the pigments may not be directly affected.
Lighting | UV contentTable 2 Footnote 2 | Visible lightTable 2 Footnote 2 | Medium sensitivity – Weakening and eventual fragmentation of the fibres | High sensitivity – Weakening and eventual fragmentation if photosensitizing dyes or components present |
---|---|---|---|---|
Daylight through window glass |
~400–500 μW/lm |
Full daylight: 30,000 lux |
~3 years or more |
~2 months or more |
50 lux |
~2000 years or more |
~100 years or more |
||
Daylight through window glass with good UV filter |
~75 μW/lm or less |
Full daylight: 30,000 lux |
~30 years or more |
~2 years or more |
50 lux |
~many millennia (thermal agingFootnote 3 likely in 100–1000 years at 20°C) |
~many millennia (thermal agingFootnote 3 likely in 100–1000 years at 20°C) |
||
Dark |
No UV |
none |
(thermal agingTable 2 Footnote 3 likely in 100–1000 years at 20°C) |
(thermal agingTable 2 Footnote 3 likely in 100–1000 years at 20°C) |
Note: Table 2 is based on Table 5 in CCI’s Agent of deterioration: light, ultraviolet and infrared.
Fading
The fading of colours is the most obvious form of light damage to textiles (Figure 20). It also is a photooxidation process and is due to reactions with both the visible and UV portions of light. Most natural dyes and a great many synthetic dyes, especially the early ones, are highly sensitive and easily faded or altered by light (consult Tables 3 and 4 for more details). As noted in Table 4, if the light levels are reduced, for example from 5000 lux to 50 lux, this will prolong the enjoyment of colours by a factor of 100; if, instead, only the UV is filtered out of the light (compare the third column “With UV” to the fourth column “No UV”), this will have a beneficial but much more limited effect. Note, however, that even if using the lowest light level (50 lux) without any UV, colours in the high sensitivity range may nevertheless fade within a few years if continuously displayed, and those in the medium sensitivity range, within decades; that is why limiting exposure times is also very important to preserve sensitive colours as long as possible. The rate of change for most colours is relatively quick at first and then tapers off over time. Thus, exercise caution and use strict controls if vividly coloured textiles are to be exhibited. Fading may not be noticed until it has developed to a considerable degree and, by then, irreversible damage has been done. The degree of fading is best seen by comparing exposed areas to those that have been protected from light, such as the front and back of an embroidery or the interior and the exterior of a garment.
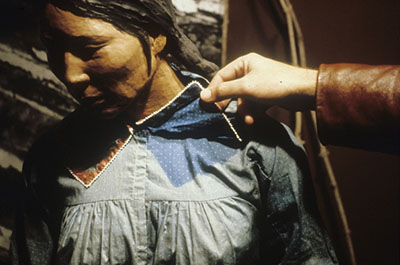
© Government of Canada, Canadian Conservation Institute. CCI 129981-0013
Figure 20. Fading of a blue-dyed fabric due to exposure to light while on display.
Sensitivity | Types of coloured material at risk |
---|---|
High sensitivity |
|
Medium sensitivity |
|
Low sensitivity |
|
Note: Table 3 is based on Table 3 in CCI’s Agent of deterioration: light, ultraviolet and infrared.
SensitivityFootnote * | Visible light level | TimeTable 4 Footnote 1 for just noticeable fadeTable 4 Footnote 2 | |
---|---|---|---|
With UVTable 4 Footnote 3 | No UVTable 4 Footnote 4 | ||
High sensitivity |
30,000 lux |
0.8 to 7 days |
1 to 14 days |
5000 lux (light from a window or study lamp) |
4 days to 1 month |
5 days to 2 months |
|
500 lux |
5 weeks to 1 year |
7 weeks to 2 years |
|
150 lux |
20 weeks to 3.5 years |
6 months to 7 years |
|
50 lux |
1 to 10 years |
1.5 to 20 years |
|
Medium sensitivity |
30,000 lux |
5 days to 10 weeks |
2 weeks to 1 year |
5000 lux (light from a window or study lamp) |
3 weeks to 17 months |
2 months to 7 years |
|
500 lux |
8 months to 14 years |
2 to 70 years |
|
150 lux |
2 to 40 years |
7 to 200 years |
|
50 lux |
7 to 140 years |
20 to 700 years |
|
Low sensitivity |
30,000 lux |
1 to 14 months |
6 months to 10 years |
5000 lux (light from a window or study lamp) |
0.5 to 8 years |
3 to 70 years |
|
500 lux |
5 to 84 years |
30 to 700 years |
|
150 lux |
17 to 240 years |
100 to 2000 years |
|
50 lux |
50 to 840 years |
300 to 7000 years |
Note: Table 4 is based on Tables 3 and 4 in CCI’s Agent of deterioration: light, ultraviolet and infrared.
Change of colour
Some colours change hue as the more fugitive-coloured components fade away. A prime example would be the bluish-green foliage on most 16th- and 17th-century tapestries (Figure 21). Originally, the foliage would have appeared green, but over time, the more fugitive yellow dye (weld) has faded away, leaving the more lightfast blue dye (indigo).
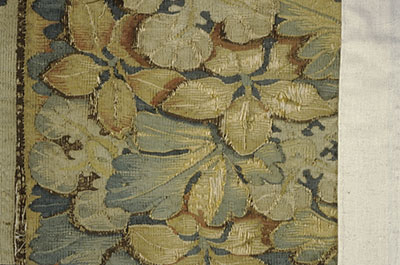
© Government of Canada, Canadian Conservation Institute. CCI 2005175-0001
Figure 21. Green foliage that has now changed to blue.
Yellowing
Yellowing is an indication that fibres have undergone photooxidation through exposure to light, particularly UV radiation (Figure 22). These reactions are accelerated in the presence of heat and moisture. Yellowing will often be noticeable along the lines of folds where the fibres are more exposed to the environment. Many types of fibres yellow upon exposure to UV, including wool, silk, cotton, linen, jute, rayon and nylon.
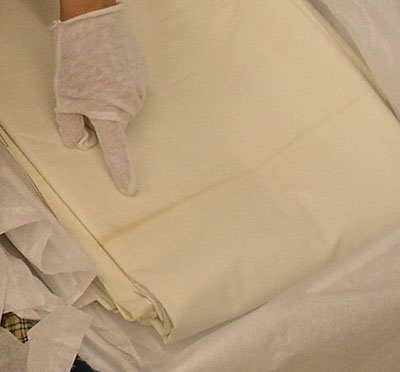
© Government of Canada, Canadian Conservation Institute. CCI 129981-0014
Figure 22. Yellowing at the fold line of a cellulosic textile, probably due to photooxidation.
To learn more about how to prevent damage to heritage collections from light, UV and infrared, consult Agent of deterioration: light, ultraviolet and infrared.
Incorrect temperature
High temperatures increase the rate of deterioration of all organic materials, which becomes of practical significance for textiles that are chemically unstable, such as weighted silk. Acidic and unwashed cellulosic textiles (cotton, linen) that have been exposed to pollution are also vulnerable, as are early synthetic textiles that can develop acidity internally.
Low temperatures (5°C and lower) have many benefits for textiles. Besides reducing chemical decay, they greatly decrease pest frequency. There is no known danger to textiles when treating them at -30°C for insect infestation. However, painted textiles should not be frozen.
Low temperature becomes a problem only when it causes high RH and damp. This can occur when textiles are stored in a poorly ventilated space and either the space experiences a sudden temperature drop or the storage cabinets where they are kept are pushed against a cold exterior wall (consult Table 6).
Table 5 provides the relationship between temperature and expected lifespans of textiles undergoing chemical deterioration. As it demonstrates, keeping the room temperature at moderate to cool levels is beneficial for textiles in the long-term.
Temperature | Materials of low sensitivityTable 5 Footnote 1 | Materials of medium sensitivityTable 5 Footnote 2 | Materials of high sensitivityTable 5 Footnote 3 |
---|---|---|---|
~30°C |
~250 years or more |
~75 years |
~25 years |
~25°C |
~500 years or more |
~150 years |
~50 years |
~20°C |
~1000 years or more |
~300 years |
~100 years |
~15°C |
~2500 years |
~700 years |
~250 years |
~10°C |
~5000 years or more |
~1500 years |
~500 years |
~0°C |
20,000 years or more |
~6000 years or more |
~2000 years or more |
Note: Table 5 is based on Tables 1a and 1b in CCI’s Agent of deterioration: incorrect temperature.
Incorrect relative humidity
Textiles are hygroscopic, meaning that they absorb and release water vapour from the air as the RH fluctuates. At very high RH levels, fibres swell, adhesives may fail, dyes may transfer, mould may grow (as noted under Mould) and metal trim may corrode and stain adjoining fabric. High RH also accelerates the fading of many dyes by light.
Textiles can tolerate a wide range of RH levels. It is only the extremes that threaten textile collections. At high RH, fibres swell as they absorb water vapour; at low RH, fibres shrink as they release it. This swelling and shrinking occurs primarily in the diameter of the textile fibres. The resultant behaviour of a woven textile is counterintuitive—the textile shrinks when the fibres swell at high RH, especially in the warp direction, since the crimp is greater.
While woven organic materials without edge restraints (e.g. blankets, flags) and simple costumes can withstand or accommodate moderate RH fluctuations, woven organic textiles with hard twist yarns or those with edge restraints (e.g. needlepoint fixed to a stretcher or upholstered seat cover) may tear during fluctuation from moderate to high RH.
Mould spores are ubiquitously present in ambient air. High RH allows mould to grow on textiles. Both cellulosic and proteinaceous textiles are at risk, serving as nutrients. At 70% RH, it takes three months or more for mould to develop. At 90%, however, mould grows in only a few days. The presence of soils, stains or finishes, such as starch, also provide food for microorganisms, making almost any fibre vulnerable. Consult Agent of deterioration: incorrect relative humidity, which provides a chart indicating the rate of mould growth by humidity level.
The growth of microorganisms causes staining, which is often impossible to remove, while also weakening textile fibres, sometimes to the point of disintegration. Table 6 provides data on mould risks for textiles in an enclosure (e.g. a bag, frame or cabinet) when a small part of the enclosure is much colder than the rest of it. Even without a sealed enclosure, high risks arise if a thermal gradient occurs where air is trapped in a stagnant pocket, as can occur behind a textile on display on a cold exterior wall, especially if the museum is humidified.
Temperature gradient | Initial relative humidity | ||||
---|---|---|---|---|---|
50% | 60% | 70% | 80% | 90% | |
No gradient, both sides at 25ºC |
No mould growth |
Visible mould growth unlikely |
Risk of mould in ~100 days Growth increases in vigour above 75% |
Risk of mould in ~10 days Mould growth is strongly active above 85% |
Risk of mould in ~2–3 days |
Warm side 25°C |
RHcool side= 55% |
RHcool side= 67% |
RHcool side= ~78% |
RHcool side= 88% |
RHcool side = 97% Risk of mould in ~1 day |
Warm side 25°C |
RHcool side= 68% Risk of mould in ~200 days |
RHcool side= 78% |
RHcool side= ~90% |
RHcool side= 97% |
RHcool side = 100% Risk of mould in hours |
Warm side 25°C |
RHcool side= 75% Risk of mould in ~30 days |
RHcool side= 85% Risk of mould in ~7 days |
RHcool side= 95% Risk of mould in ~1 day |
RHcool side= 100% Risk of mould in hours |
RHcool side= 100% Risk of mould in hours |
Mould often appears as a white or coloured velvety growth (Figure 23) and is sometimes accompanied by a musty odour. Isolated and disfiguring spots are signs of the early stages of mould growth. Powdery dirt, dust and fibrous deposits are sometimes mistaken for mould. The hyphae of surface mould will often appear to radiate from a central spot where the spore has germinated, whereas powdery deposits will be randomly distributed. The difference between the two may be seen under magnification.
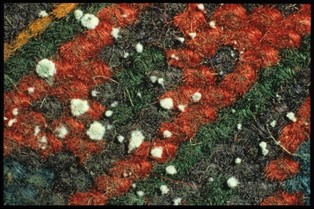
© Government of Canada, Canadian Conservation Institute. CCI 129981-0011
Figure 23. Velvety growth of mould on a textile.
Consult CCI Note 13/15 Mould Growth on Textiles for more information on detecting and preventing mould on textiles.
During the winter, heating without humidification leads to low RH. Between 40% and 5% RH, textiles become increasingly brittle and much more fragile to handle. On the other hand, low RH has significant benefits for textiles. Light fading is slower, its rate dropping by almost half between 60% and 10% RH for some dyes. Insect attack is less frequent below 40% RH.
The only way to be certain of the environmental conditions in a display or storage area is to use instruments to measure them. A hygrothermograph or data-logger is recommended for continuous recording of RH and temperature fluctuations throughout seasonal cycles. Equipment for monitoring light, temperature and RH can be borrowed from the Canadian Conservation Institute (consult Environmental monitoring equipment loans program for more information).
More information on RH and how it affects heritage collections can be found under Agent of deterioration: incorrect relative humidity.
Key preventive conservation strategies for textiles and costumes
The effects of the agents of deterioration listed above can be minimized by paying attention to handling techniques and storage and display materials, methods and conditions. Often, the use of a single recommended practice can reduce the effects of several agents of deterioration. For example, storing a textile flat in a labelled box protects the object from light, dust and pollutants and also provides physical support and minimizes handling.
Key preservation strategies for handling, storing and displaying textiles are provided below.
Handling
- Do not wear historical costumes. Use historically accurate reproductions for interpretive purposes.
- Identify textiles and accessories that are damaged or weakened and that require special handling and supports.
- Use pencils for documentation rather than ink.
- Wash hands before working with textiles, or wear clean gloves during handling to avoid soiling by the hands.
- Handle textiles only when necessary, making gentle, planned movements, thus minimizing the risk of physical damage to objects that may be weaker than they appear to be.
- Provide flat supports or custom mounts large enough to adequately support the entire textile before moving it (Figure 24).
- Pack textiles with adequate cushioning to prevent abrasion due to vibration in transit.
- Handle the flat support, hanger or mount, rather than the textile itself (Figures 24 and 25).
- Provide custom supports for handling oversized textiles. Supports may need to be specially fabricated because textiles such as rugs and hangings are often larger than standard sizes. Plan any move beforehand, and prepare the storage area or display in advance of moving a large textile into it. Rolls or tubes used for storage also make useful tools for turning over large flat textiles and for handling and transit.
- Prepare a large enough space to accommodate objects before moving them.
- Oversized textiles often require custom supports and two or more people to transport them or install them for display or onto storage supports.
- Consult Handling heritage objects for more guidance on handling.
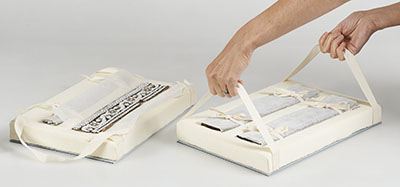
© Government of Canada, Canadian Conservation Institute. CCI 79408-0020
Figure 24. Beaded fabric bands are provided with a padded support that facilitates their safe storage and handling. Handles at either end of the support facilitate handling without having to touch the objects.
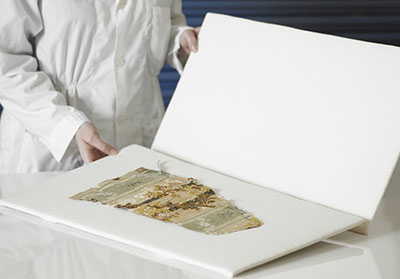
© Government of Canada, Canadian Conservation Institute. CCI 125773-0017
Figure 25. A textile is stored in a large flat support to facilitate safe storage and handling.
Storage
- Prewash all fabrics for packing, cushioning or mounting textiles before use (e.g. dust covers, linings).
- Store small flat textiles and costumes with as few folds as possible in boxes or drawers.
- To prevent tight folds, pad them out with crumpled acid-free tissue, lightweight cotton sheeting, soft nylon tulle or cotton knit tubing stuffed with polyester fibrefill (Figures 26a and 26b).
- Line boxes with cushioning material, with the objects interleaved if they must be stacked. If possible, limit the stacking of textiles.
- Store larger textiles, such as quilts and rugs, rolled, as outlined under Rolled Storage for Textiles.
- Hang costumes on padded hangers or store them flat if they are very fragile, heavy, beaded or cut on the bias.
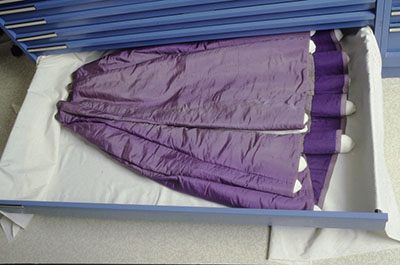
© Government of Canada, Canadian Conservation Institute. CCI 129981-0015
Figure 26a. Skirt folds padded with stuffed knit tubing.
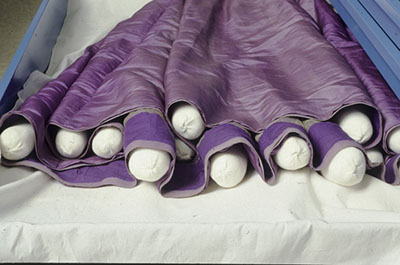
© Government of Canada, Canadian Conservation Institute. CCI 129981-0016
Figure 26b. Detail of stuffed knit tubing ends.
Display
- Display costumes on custom mannequins (Figure 27), flat textiles on padded mounts and oversized textiles on a hanging system such as Velcro (as described in CCI Note 13/4 Velcro Support System for Textiles). Alternatively, a casing and properly sealed dowel for vertical display will prevent textiles from becoming distorted due to gravity.
- Display textiles for limited time periods (e.g. a three-month maximum). Keep some representative objects out of the rotation so that they remain pristine indefinitely, for future research and to make reproductions.
- Use physical barriers or display cases when possible. Display cases are preferable to open display, as they protect against dust, reduce pollutant exposure and provide a barrier against contact by the public.
- Provide custom supports for displaying oversized textiles. Supports may need to be specially fabricated because textiles such as rugs and hangings are often larger than standard sizes.
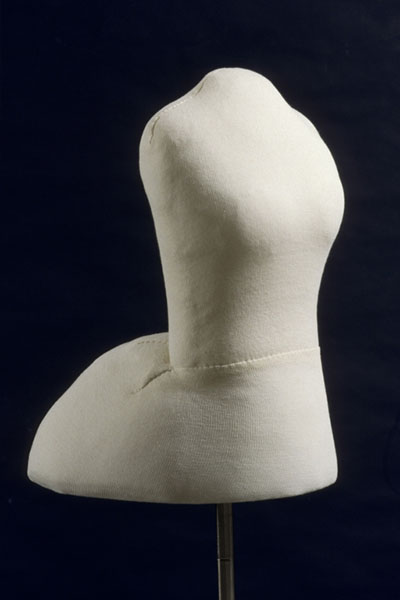
© Government of Canada, Canadian Conservation Institute. CCI 120171-0013
Figure 27. A custom-made mannequin with bustle support to accommodate a period costume.
The environment
The following environmental recommendations will assist in preserving textiles for the long term.
- Use stable materials such as acid-free card, archival foam board and fluted plastic sheet to support flat textiles and costume accessories. Take measures to seal (e.g. with Marvelseal) any acidic or emissive materials (e.g. wood or acidic tubes) to be used for storage and display in order to make them safe and thus avoid harming the objects.
- Make mannequins from stable materials such as extruded polyethylene foam plank.
- Protect textiles from dust with acid-free tissue or cotton sheeting covered with plastic sheeting (e.g. Mylar) or with polyethylene non-woven (Tyvek) or polyethylene sheeting. The plastic sheeting will also protect from water leaks.
- Establish deterioration rates due to visible light (e.g. fading, colour change, yellowing, fibre damage) for various objects and establish illumination levels as well as exposure times and schedules. Ensure all UV is eliminated from light sources (to 75 mW/lm or less). Use window coverings to eliminate natural light.
- Avoid heat. Consider keeping storage cool to cold, especially for high vulnerability objects. Consult the section Incorrect temperature.
- Prevent high RH that can cause mould. Avoid temperature gradients (“cold spots”) within the museum that could result in a higher RH and the risk of mould growth. Provide adequate insulation to all exterior walls. Consult Agent of deterioration: incorrect relative humidity for details.
- Implement an integrated pest management plan. Ensure woollens and other keratinous objects in the collection are regularly inspected for the presence of insect pests (in particular clothes moths and carpet beetles). Have staff report any signs of insect activity. Quarantine any incoming textiles to ensure that pests are not inadvertently introduced into the collection.
- Consult CCI Note 13/1 Textiles and the Environment for further environmental guidelines for preserving textiles and costumes.
Examples of preventive conservation practices
This section provides practical examples in the care of textiles and costumes.
Storage of flat textiles
Small, flat textiles, such as samplers, should be wrapped in acid-free tissue paper. A sheet of acid-free tissue can be pre-folded in half or in quarters to a size larger than the object, so that, once inserted, the textile is protected front and back. They can be stored in acid-free card boxes or inert plastic boxes that have been lined with acid-free tissue or prewashed cotton sheeting. To facilitate handling, the textile in its tissue support can be placed on a piece of fluted plastic sheet or a 4-ply acid-free card, or inserted in a single-ply acid-free card folder (Figure 28). Consult CCI Notes 13/2 Flat Storage for Textiles and 13/6 Mounting Small, Light, Flat Textiles for advice on storing and mounting flat textiles.
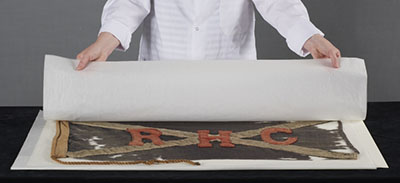
© Government of Canada, Canadian Conservation Institute. CCI 129430-0019
Figure 28. Flat textile in tissue on acid-free card support.
Storage of shoes and hats
The shape of three-dimensional items like shoes and hats can be retained in storage by lightly stuffing them with crumpled acid-free tissue. Shapes that correspond to the bottoms of shoes can be cut from stable plastic foam plank and attached to a fluted plastic sheet or 4-ply acid-free card support. If plastic trays or boxes are used, the shapes can be adhered directly to them. Provide for adequate space on the mount so that the shoes are not touching each other. Cotton tapes can be used to secure the shoes to their supports (Figure 29).
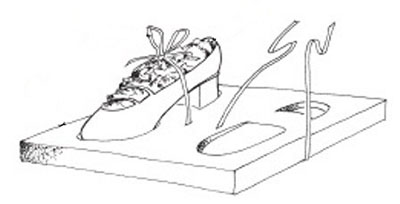
© Government of Canada, Canadian Conservation Institute. CCI 129981-0006
Figure 29. Support for shoes.
Hats are best stored on mounts that elevate the brim off the storage shelf while fully supporting both the brim itself and the crown. A variety of methods and materials can be used to make hat mounts. If the mounts are neatly made and covered with a display fabric, they can be used for both storage and display (Figures 30a and 30b).
To further protect hats, bonnets, shoes and boots, store in boxes to provide a safe means of handling them and to shelter them from dust. Consult CCI Note 13/12 Storage for Costume Accessories for more information on storing these types of items.

© Government of Canada, Canadian Conservation Institute. CCI 99201-0021
Figure 30a. Hat mount consisting of two padded foam elements covered with knit fabric.
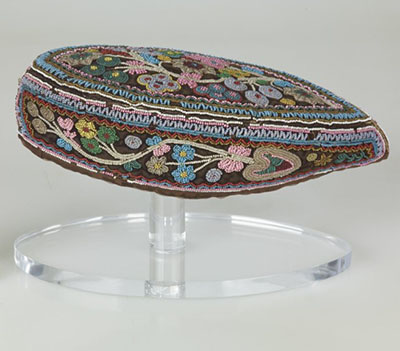
© Government of Canada, Canadian Conservation Institute. CCI 99201-0019
Figure 30b. Beaded cap on storage and display mount shown in Figure 30a.
Rolled storage
To make efficient use of space and to facilitate handling, textiles such as carpets are stored rolled on an acid-free cardboard tube that is several inches longer than the width of the rolled textile. If a regular cardboard tube is used, before rolling, it is first covered with plastic sheeting (Mylar) or Marvelseal and then with acid-free tissue, prewashed cotton sheeting or cotton stockinette. Carpets are rolled with the pile on the outside, interleaving with acid-free tissue, following the direction of the pile so that it does not become crushed. If a solid metal rod is inserted through the tube, the rolled carpet can be supported by chains or brackets (Figures 31a and 31b). If not stored in a cupboard, a prewashed cotton or polyethylene non-woven (Tyvek) cover can be used to protect the rolled textile from dust and light. Auxiliary labels and/or colour photos of the textile can be attached to the tube to facilitate identification. Consult CCI Note 13/3 Rolled Storage for Textiles for more details on rolled storage.
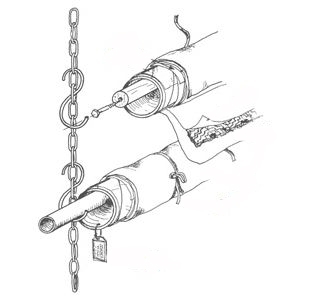
© Government of Canada, Canadian Conservation Institute. CCI 129981-0007
Figure 31a. Examples of a suspension storage system for rolled carpets.
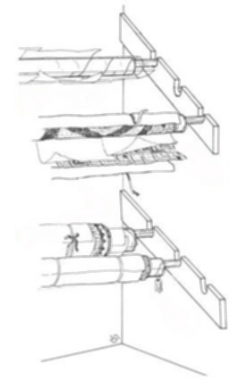
© Government of Canada, Canadian Conservation Institute. CCI 129981-0008
Figure 31b. Examples of a bracket storage system for rolled carpets.
Display and flat storage of a cotton christening gown
The bodice of this christening gown has a more or less square-cut construction (i.e. the sleeves extend out in a straight line perpendicular to the torso). This enables it to be displayed suspended from a dowel inserted through both sleeves (Figures 32a and 32b). Plexiglas rod is ideal as a dowel since it is inert and unobtrusive. If a wooden dowel is used, it must be isolated from the textile by sealing it with acrylic latex paint or by wrapping it in a barrier material, like Marvelseal. Another option is to display the gown on a mannequin or on a support made of chemically inert, stable materials.
The gown can be stored in a lined drawer or box that is large enough to eliminate the need for much folding. The fewer folds the better. The sleeves and bodice can be slightly padded out with crumpled acid-free tissue to reduce creasing. Similarly, any folds should be lightly padded out with acid-free tissue or soft nylon tulle to prevent hard creases from forming.
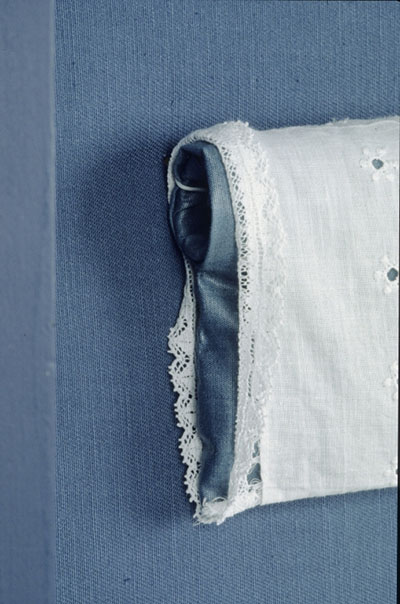
© Government of Canada, Canadian Conservation Institute. CCI 129981-0017
Figure 32a. Detail of one of the sleeves of a christening gown suspended on a dowel.
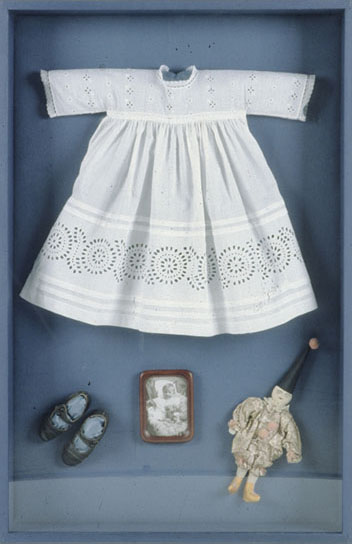
© Government of Canada, Canadian Conservation Institute. CCI 129981-0018
Figure 32b. Christening gown in a display case.
Display and hanging storage for a military tunic
A military tunic in good condition is well suited for display on a mannequin (Figure 33). An existing mannequin adapted for conservation purposes (e.g. using a barrier between the mannequin and the object) can be used to display the tunic, providing it is of the appropriate size. If a suitable mannequin cannot be found, one can be custom-made using a variety of methods (e.g. paper tape, foam discs, intersecting silhouette technique) and materials (e.g. gummed paper tape, polyethylene foam, buckram, Fosshape).
Hanging storage is a suitable option for this military tunic as it is in good condition and structurally sound. The tunic can be stored on a padded hanger with additional interior support (e.g. crumpled acid-free tissue paper in the sleeves). Ideally, each costume should be protected from dust and light and from contact with other garments with a dust cover.
Consult CCI Note 13/5 Hanging Storage for Costumes for further details on hanging storage.
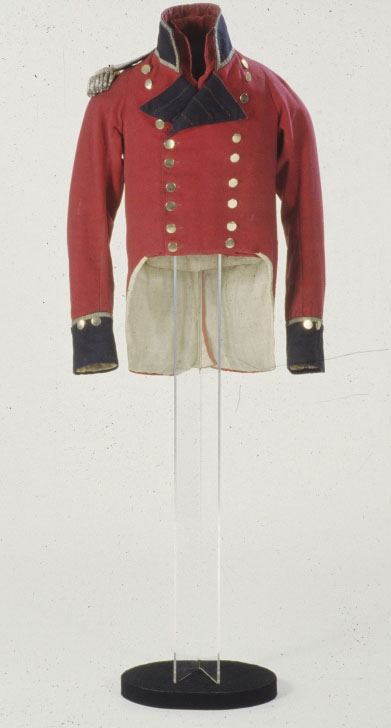
© Government of Canada, Canadian Conservation Institute. CCI 2005178-0001
Figure 33. A military tunic displayed on a custom mannequin and stand.
Displaying quilts
There are several options for displaying quilts. Those that are structurally sound and can support their own weight can be suspended for temporary display. It is important to provide adequate support evenly along the edge from which the quilt will be suspended. A strip of Velcro can be sewn to the back to provide uniform support along the entire width of the quilt (Figure 34). Consult CCI Note 13/4 Velcro Support System for Textiles for instructions on creating a Velcro support system.
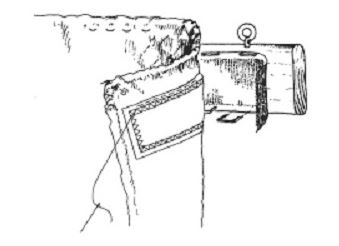
© Government of Canada, Canadian Conservation Institute. CCI 129981-0009
Figure 34. A quilt can be mounted for display by using a Velcro support system.
Alternatively, a fabric sleeve may be hand-stitched to the reverse of the quilt along the top edge. A sealed dowel is inserted through the sleeve and supported by brackets, chains or rope at each end. The lower portion of the quilt can also be draped over a padded dowel or tube to reduce the amount of space that it takes up vertically. Another approach is to roll the top portion of the quilt onto a tube, leaving the bottom portion exposed for display. To prevent it from unrolling, the top edge of the quilt can be stitched to a piece of fabric, which is attached to the tube. If a bed is part of the exhibit, a quilt can be displayed as a bed covering either fully opened out or folded at the foot of the bed. The folds should be padded with acid-free tissue.
Bibliography
Brunn, M., and J. White, eds. Museum Mannequins: A Guide for Creating the Perfect Fit. Edmonton, AB: Alberta Regional Group of Conservators, 2002.
Burnham, D.K. Warp and Weft: A Textile Terminology. Toronto, ON: Royal Ontario Museum, 1980.
Canadian Conservation Institute. Environmental Monitoring Kit. CCI Notes 2/4 (retired). Ottawa, ON: Canadian Conservation Institute, 1983.
Canadian Conservation Institute. Textiles and the Environment, revised. CCI Notes 13/1. Ottawa, ON: Canadian Conservation Institute, 2013.
Canadian Conservation Institute. Flat Storage for Textiles, revised. CCI Notes 13/2. Ottawa, ON: Canadian Conservation Institute, 2008.
Canadian Conservation Institute. Rolled Storage for Textiles, revised. CCI Notes 13/3. Ottawa, ON: Canadian Conservation Institute, 2008.
Canadian Conservation Institute. Velcro Support System for Textiles, revised. CCI Notes 13/4. Ottawa, ON: Canadian Conservation Institute, 2008.
Canadian Conservation Institute. Hanging Storage for Costumes, revised. CCI Notes 13/5. Ottawa, ON: Canadian Conservation Institute, 2009.
Canadian Conservation Institute. Mounting Small, Light, Flat Textiles, revised. CCI Notes 13/6. Ottawa, ON: Canadian Conservation Institute, 2009.
Canadian Conservation Institute. Washing Non-coloured Textiles, revised. CCI Notes 13/7. Ottawa, ON: Canadian Conservation Institute, 2009.
Canadian Conservation Institute. Applying Accession Numbers to Textiles, revised. CCI Notes 13/8. Ottawa, ON: Canadian Conservation Institute, 2008.
Canadian Conservation Institute. Anionic Detergent, revised. CCI Notes 13/9. Ottawa, ON: Canadian Conservation Institute, 2008.
Canadian Conservation Institute. Stitches Used in Textile Conservation, revised. CCI Notes 13/10. Ottawa, ON: Canadian Conservation Institute, 2008.
Canadian Conservation Institute. Natural Fibres, revised. CCI Notes 13/11. Ottawa, ON: Canadian Conservation Institute, 2008.
Canadian Conservation Institute. Storage for Costume Accessories, revised. CCI Notes 13/12. Ottawa, ON: Canadian Conservation Institute, 2009.
Canadian Conservation Institute. Commercial Dry Cleaning of Museum Textiles, revised. CCI Notes 13/13. Ottawa, ON: Canadian Conservation Institute, 2008.
Canadian Conservation Institute. Testing for Colourfastness, revised. CCI Notes 13/14. Ottawa, ON: Canadian Conservation Institute, 2008.
Canadian Conservation Institute. Mould Growth on Textiles, revised. CCI Notes 13/15. Ottawa, ON: Canadian Conservation Institute, 2008.
Canadian Conservation Institute. Mechanical Surface Cleaning of Textiles. CCI Notes 13/16. Ottawa, ON: Canadian Conservation Institute, 2010.
Canadian Conservation Institute. Conservation Framing of Embroideries and Other Flat Textiles. CCI Notes 13/17. Ottawa, ON: Canadian Conservation Institute, 2010.
Canadian Conservation Institute. The Identification of Natural Fibres. CCI Notes 13/18. Ottawa, ON: Canadian Conservation Institute, 2010.
Hudson, P.B., A.C. Clapp, D. Kness and M.L. Joseph. Joseph’s Introductory Textile Science. 6th ed. NY: Harcourt Brace College Publishers, 1993.
Korenberg, C. “The Effect of Ultraviolet-filtered Light on the Mechanical Strength of Fabrics.” In The British Museum Technical Research Bulletin, vol. 1, 2007, p. 23–27.
Mailand, H.F., and D.S. Alig. Preserving Textiles: A Guide for the Nonspecialist. Indianapolis, IN: Indianapolis Museum of Art, 1999.
Museums and Galleries Commission. Standards in the Museum Care of Costume and Textile Collections. London, UK: Museums and Galleries Commission, 1998.
Robinson, J., and T. Pardoe. An Illustrated Guide to the Care of Costume and Textile Collections. London, UK: Museums and Galleries Commission, 2000.
Seiler-Baldinger, A. Textiles: A Classification of Techniques. Washington, D.C.: Smithsonian, 1994.
Strang, T. “The Effect of Thermal Methods of Pest Control on Museum Collections.” In Proceedings of the 3rd International Conference on Biodeterioration of Cultural Property, Bangkok, Thailand 4–7 July, 1995: Preprints. Bangkok, Thailand: Organizing Committee of ICBCP-3, 1995, pp. 199–212.
Strang, T. Preventing Infestations: Control Strategies and Detection Methods. CCI Notes 3/1. Ottawa, ON: CCI, 1996.
Strang, T. Controlling Insect Pests With Low Temperature. CCI Notes 3/3. Ottawa, ON: Canadian Conservation Institute, 1997.
Tétreault, J. Airborne Pollutants in Museums, Galleries and Archives: Risk Assessment, Control Strategies, and Preservation Management. Ottawa, ON: CCI, 2003.
Tímár-Balázsy, A., and D. Eastop. Chemical Principles of Textile Conservation. Oxford, UK: Butterworth-Heinemann, 1998.
© Government of Canada, Canadian Conservation Institute, 2024
Published by:
Canadian Conservation Institute
Department of Canadian Heritage
1030 Innes Road
Ottawa, ON K1B 4S7
Canada
Revised in 2024
Originally published in 2018
Cat. No.: CH57-4/6-15-2018E-PDF
ISBN 978-0-660-28033-2
Page details
- Date modified: